3 minute read
Borg & Beck: Challenging misconceptions
Is Borg & Beck the same today as it was in the past? Rob Marshall heads to First Line's Oxfordshire HQ to find out
Wrong impressions can be extremely harmful. Take Borg & Beck as a typical example. For decades, the UK clutch company established itself as an OE fitment for the sprawling British Motor Industry, from the 'Saintly' Volvo P1800 (made initially in West Bromwich) to the multiple UK-built BMC, British Leyland, Rootes and Ford of Britain products that littered our shores in huge numbers.
Surprisingly, Borg & Beck is not British. Mr Marshall Beck and Mr Charles W. Borg (the same Borg of BorgWarner but that is another story) established the company in Moline, Illinois, USA, where it pioneered the single plate clutch that became the automotive application blueprint.
It was AP Lockhead of Leamington Spa that took the brand global, by negotiating the rights to distribute Borg & Beck clutches not just in the UK but also to all British colonies. At its peak, the company supplied 85% of all new cars, a move that exposed the company to the British Motor Industry's decline. By the late 1980s, Delphi (a division of the North American General Motors company that, ironically, was subsumed into BorgWarner) acquired the brand. In 2006, the family firm, First Line Limited, took over.
Extending the reach
Today, Borg & Beck cannot be considered a sole clutch brand any longer. After First Line's considerable investment, steering, suspension, filtration, cables, braking, turbo hoses, wheel bearings, cooling, wiper blades, sumps, wiper motors, CV joints and driveshafts have been added to its portfolio. Borg & Beck's long-established international repute is so strong that it has become the company's primary overseas brand.
This development might make you imagine that Borg & Beck has waned from being a clutch pioneer to a label, applied to a generic clutch box cynically to capitalise on past glories. Again, the perception is untrue. While Borg & Beck clutches are not fitted in car factories anymore, First Line is adamant that its aftermarket offerings are developed to OE specifications, or better – but how can they prove it?
Having retained the range, intellectual property, technical documentation and expertise from AP Lockheed, First Line has ensured the availability of high-quality clutches for classic and historic cars. Yet, time moves on and, where some materials cannot be used anymore (asbestos included), Borg & Beck clutches utilise alternatives that deliver equivalent characteristics to those delivered by the original part. Continual product evaluation has led to the redesign and reformulation of certain parts that can tolerate modern driving conditions. For instance, the carbon clutch release bearing wears considerably, if the clutch is depressed for long periods. Unfortunately, this mechanically-unsympathetic driving habit has become de-rigour and so the release bearing has needed upgrading accordingly.
Viewing Borg & Beck as a classic-only brand is also inaccurate. While the company does not supply clutch kits to the OEMs, it possesses the formal clutch specification data, from which it can design and produce replacements that meet the original requirements. Improvements can also be identified and integrated. A range of over 65 single mass flywheel conversions for vehicles that experience exceptional driving conditions, such as taxis, or those deployed for emergency responses, is evidence of this stance.
21st-century quality
While First Line works with multiple overseas manufacturing partners, and ensures that they carry out frequent quality control checks, the company has established a dedicated UK test centre at its HQ in Banbury, Oxfordshire, visible to all travellers passing Junction 4 of the M40.
Naturally, there are many ways in which clutches are tested for quality. AT was granted access to the company's test centre, to witness its trio of test rigs in action...
1. The test centre's primary function is quality control testing, carried out not just on final stage prototype parts but also on warranty returns and as part of routine checks of current clutch stock, to maintain the Borg & Beck repute and provide an efficient resolution for distributors.
2. Borg & Beck retains a considerable library of technical literature, not just for classic and historic vehicles but also those that make the current UK car parc.
(CSC) tests require this bespoke machine to run continually for 24 hours. It operates the CSC 100,000 times, replicating 80,000 miles of normal motoring.
5. The system also monitors the hydraulic pressure required to operate the CSC, which influences the clutch pedal pressure and, therefore, is an important driver comfort consideration.
6. This rig evaluates the clutch plate cushioning and dimensional specifications, provided not just by the damper springs but also the laminated plate layers. Along with correctly-specified friction materials, the desired result is a smooth take-up of drive, with no sudden grab, optimising driver comfort.
11. The cover can also be reoriented on the machine, so its clamp load is assessed and, as with the release load, the results are compared against the formal specification. Pictured, is one of the three clutch straps, all of which must be parallel with each other. Should one of them become bent, pressure cannot be released evenly, and judder can result.
10. The pressures applied are plotted accurately on a so the operator can note the result in real-time and deduce whether the clutch pedal would be excessively heavy.
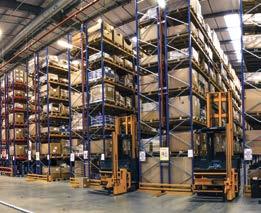
P38 ACtronics: Automated ABS unit remanufacturing