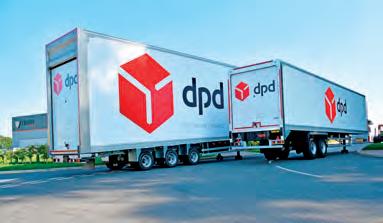
15 minute read
Ken Davis, CILT
from ExF Nov-Dec
by 4SMNI
The Chartered Institute of Logistics and Transport
Ken Davis
M Sc FCILT, CILT Northern Ireland
DRIVER SHORTAGES: WHAT IS THE REAL SITUATION?
If you are reading this edition of Export & Freight, then some deliveries are still getting through, despite the alleged shortage of 100,000 drivers. As a happily retired ex-operator, I know those of you reading this article, while still struggling to man your delivery schedule, may be tempted to throw it away, but please read on…
If I haven’t got your attention yet: how about this? There’s no such thing as a shortage of HGV drivers in the UK. Now you’re paying attention. What’s my evidence for this outlandish statement? Well, the UK Minister for Roads, Baroness Vere has sent a letter, countersigned by the heads of Logistics UK and the RHA, to all UK HGV licence holders, thanking those within the industry for their contribution, and asking those with a licence but not active, to “consider returning” to the industry. According to the government, this letter is being sent to a million licence holders. That’s right, one million vocational licence holders. So, how many of these are inactive? Well, according to the governments own Office for National Statistics (ONS) there were 268,000 people working as HGV drivers in June 2021. In other words, officially, there are about three quarters of a million people in the UK, today, who can drive a lorry but chose not to. I told you there wasn’t a driver shortage. But there is definitely a crisis in getting enough drivers to get the deliveries made. Clearly, the million licence holders is a headline grabbing number, and includes all sorts of double counting, such as retired drivers, fitters, dual licence holders, even magazine test drivers, etc, but even taking the difference between the RHA’s assessment of HGV licence holders - 516,000 - and the pre-Covid ONS number of active HGV drivers - 321,000 (June 2017) - we are still looking at about 200,000 people who could drive, but choose not to.
Potential Solutions
So, as I see things, there are two potential solutions to the current shortage of active drivers: 1. Leave it to the government to help; or 2. Ask why so many licence holders aren’t driving, and decide what the industry can do to fix its own problems. Let’s start with number 1. So far the Government has sent a letter, temporarily extended driving hours, mobilised the army to driver fuel, promised a “boot camp” to deliver 5000 drivers, reluctantly agreed to allow some limited short-term immigration and watered down the driving test to separately assess the couple/ uncouple and reversing manoeuvre. I, for one, question whether we as a profession should really be supporting the lowering of hard won, empirically backed, safety standards? We can’t just blame the government. Look at it from their position. Our industry has told them there is a shortage of 100,000 drivers. The actual figure is a questionable amalgam of an RHA survey showing a shortage of 60,000 drivers, plus a net Brexit outflow of 10,000, plus 30,000 driving tests cancelled due to Covid. Even if we accept it as true, what the UK Government hears is that there are potentially 100,000 (relatively) well paid, skilled jobs available for the UK workforce, partly as a result of Brexit. Little wonder that this Government doesn’t want to fill the gap by immigration!
Longer Term
Of course, longer term the Government has a key role to play, not least in providing funding to help address the age, gender and ethnic balance in the HGV driving population. They could start by delivering on Chancellor Sunak’s promise in the budget to deliver a network of better roadside facilities, ASAP. No, I think we need to look at ourselves and ask why so many drivers can drive, but don’t. We can blame an unfortunate combination of circumstances, including Covid-19, Brexit, changes to tax rules for self-employed drivers, but in truth this availability crisis has been creeping up on us for years. Look at it from the driver’s perspective. After an early start, a long hard shift, chasing the clock, battling congestion on ever busier roads, waiting to tip in an RDC where you can’t even sit in your cab because you can’t be trusted with the keys, you return to the office to be told by someone who might not even be able to drive, that the telemetry in your vehicle says you have been guilty of harsh braking. Of course, throwing money at the problem might help individual employers in the short-term, but are we now seeing the results of a race to the bottom and treating drivers as a commodity?
I propose the following steps:
In the short-term (0-3 months): Every employer to contact every driver who has retired in the last 5 years, and see what is needed to get them back to work part-time, to cover peaks. This could include paying for their medical, glasses, CPC training, not giving them nights out etc, but does mean accepting that not every driver wants to, or needs to, work 60 hours a week. In the medium-term (6 months to 1 year): All our industry body leaders need to get together with 3PL’s and Retailers and other operators of RDC’s, to agree a plan on how to tackle the 2 unacceptable wastes of waiting time at RDC’s, and empty running. The solutions aren’t simple, but surely we can work together to treat inbound drivers the same as outbound drivers, and not maintain a national empty running figure of 30% which, according to the national transport statistics, is a figure which has hardly changed for over 30 years. When I operated a network of distribution centres on behalf of one major retailer, in-bound driver waiting times was not one of my KPI’s; in fact if I put more labour into tipping Goods In, I delayed Goods Out which paid my bonus. These industry KPI’s need to change, but this can only be done by us, not the Government. In the longer-term (1 year plus): As an industry, we need to work with the Government to secure funding to recruit, train and retain drivers as part of a national solution to the ageing driver population. It might even mean a freight levy to fund this, including better facilities, but will certainly mean employers taking driver development and training and the CPC seriously, as an opportunity to invest in the driving workforce, not as another box to be ticked.
Summary
In summary, as a profession, we can either use the driver availability crisis as an opportunity to professionalise our approach to drivers, or we can just offer a recruitment bonus to make it someone else’s problem. As ever, these thoughts are my own, and do not represent official CILT policy.
DPD’s fleet grows with an additional 250 trailers from Tiger
Express parcel delivery specialist, DPD, is introducing 250 Tiger trailers to its UK logistics fleet during 2021, with the orders from the Cheshire manufacturer split into two product types,one of which has impressive green credentials.
Delivered in several batches respectively, Tiger Trailers is amidst manufacturing 100 tandem axle single deck box van trailers, alongside 150 moving deck double deck trailers which have been designed to deliver enhanced durability and environmental efficiency. Darren Wilson, Associate Director - Linehaul & Transport, DPD UK commented: “DPD’s sustainability strategy is based on examining every aspect of our operation to make it more efficient and better for the environment. “We thrive on innovation and that’s exactly what Tiger is doing in the trailer space. We’ve ordered over 250 trailers from them to support our growth, all of which will be manufactured in the UK using the latest technology and greenest components. In fact, the material being used on the double-deck trailer panels is constructed in such a way as to be totally recyclable. We love working with suppliers who share the same values and goals and Tiger is certainly one such supplier.” DPD’s Tiger-built double deck ‘wedge’ trailers incorporate a Hatcher Aero at the front and feature sidewalls made from Tata Steel’s thin, lightweight yet strong 10mm Coretinium composite sheet material solution, which is efficient at all stages of its product life cycle, from minimising raw materials in its creation, to saving weight and maximising payload space to help reduce fuel and CO2 emissions. “Up to 85% of the material, produced at our Shotton Works in Flintshire, can be recycled without separating the skins from the core,” explains Edwin Richards, Technical Sales Manager Coretinium Tata Steel, who adds: “The honeycomb product enables us to create material-efficient solutions. Having teamed up with Tiger Trailers on double decks in 2019, it’s great to now be involved in the supply to a company like DPD who place such strong value on the whole life impact of their trailers.” A number of Tiger’s moving deck double deck trailers for DPD incorporate the manufacturer’s latest digital touchpad control panel that replaces a traditional wanderlead setup, and the deck is operated by the OEM’s proven 4-ram hydraulic system that maximises the space available inside the vehicle, whilst also requiring reduced maintenance over the life of the trailer. The double deck trailers also feature galvanised chassis and stainless steel rear frames. Meanwhile, the single deck box van trailers have been equipped with various high-impact protection features and nose guarding to mitigate potential damage during coupling. The vehicles’ Goodyear KMAX D Fuel Grip tyres are specifically designed to provide robustness in regional and urban environments, backed by slow wear and ensuing high mileage capability, while the non-slip phenolic coated plywood floor is made from environmentally friendly material sourced from sustainable and 100% traceable forests in Finland. Stephen Pollock, Tiger Trailers’ Business Development Director, comments: “We’re proud to be working closely with DPD in manufacturing these two different products for their fleet. Online retail and delivery have proliferated even more quickly in recent months, so we are very pleased to be able to support DPD in getting parcels delivered safely and on time as the company strives to offer its customers increasingly wider choice. We echo DPD’s sentiments over sharing passions for innovation, technology and environmental sustainability, and look forward to supporting DPD and its green trailers.”
Wrightbus prevents one million kgs of CO2 entering the atmosphere
Wrightbus has prevented an incredible one million kilograms (1,000 tonnes) of harmful carbon dioxide (CO2) emissions entering the atmosphere since the launch of its world-first hydrogen double decker buses - just two years after the company was bought out of administration.
The reduction in emissions, from 600,000 miles covered by Wrightbus’s fleet of hydrogenpowered buses, is the equivalent of taking more than 230 cars off the roads for a whole year. Wrightbus launched its first zeroemission bus - the Streetdeck Hydroliner - last year in Aberdeen, with the fleet entering passenger service in January 2021. The Hydroliner bus emits only water from its tailpipe, with no harmful emissions. In addition to the Aberdeen fleet, the company’s zero emission hydrogen buses are currently in operation in London, Dublin and Belfast. A further 20 buses have been delivered to Birmingham, with several other local authorities looking to introduce them to their town and city streets to improve local air quality. Wrightbus also recently unveiled the Streetdeck Electroliner - its first double-decker EV bus, and the fastest charging double deck EV on the market at just two hours 45 minutes. In the run-up to the COP26 climate conference in Glasgow, the first ever Streetdeck Hydroliner model undertook a nationwide tour from London to Scotland, The UK Hydrogen Roadshow - a partnership between bus manufacturer Wrightbus, RYZE Hydrogen and hydrogen production company INEOS - saw the bus travel a 600-mile route, taking in businesses along the way to highlight the potential that lowcarbon hydrogen fuel has to play in various industries, including aviation, construction, heating and transport. Its journey ended at Jordanhill School, in Glasgow, where pupils learned all about hydrogen and its potential to help prevent climate change. When green entrepreneur Jo Bamford took over Wrightbus in October 2019, only 56 staff remained in the business. Just two years on, and largely thanks to its new zero emission products, Wrigtbus is now on track to have more than 900 staff over the next few months once its latest recruitment drive is complete. “Hitting such a landmark on the eve of COP26 is incredibly emotive,” said Wrightbus Executive Chairman Jo Bamford. “When we set out on this journey our aim was to offer multiple zero-emission solutions, but to see this number on paper - one million kgs of CO2 saved - really puts our efforts into context. “At Wrightbus we have been relentless in our commitment to zero emissions transport but even though these figures are impressive we cannot let up. As we showcase the Wrightbus Hydroliner, the world’s first hydrogen doubledecker bus, to world leaders at COP26, we will continue to press the case for more support for zero emissions transport.”
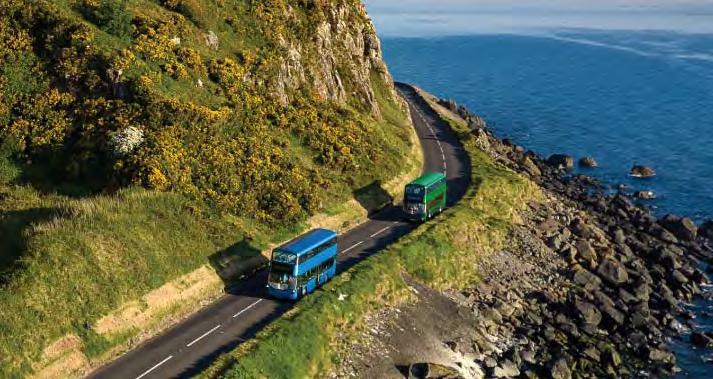
Michelin Names Andrew French as B2B Sales Director UK & Ireland
Michelin has appointed Andrew French as B2B Sales Director for the UK and Ireland, with responsibility for truck and bus, van, agriculture, construction, mining and the Services and Solutions business lines.
He takes on the role with immediate effect, just weeks after celebrating his 25th anniversary with the company – having joined Michelin as an apprentice in August 1996. After a number of roles in accounting and finance, he qualified as a Chartered Management Accountant in 2009, before being appointed Company Accountant for a small group of UK-based Michelin companies. In 2011, he joined the UK commercial management team, holding roles from Business Partner Controller to Key Account Manager, responsible for the company’s multi product-line relationship with a major distributor. Since 2018 he has held the role of Director - Services and Solutions for the UK, Ireland and Nordics, heading a team looking after some of Michelin’s largest European customers and collectively responsible for growing the business and managing the tyres on more than 98,000 vehicles. Comments Andrew French: “I am hugely excited to land a role which will enable me to work across so many parts of the Michelin business. These are all sectors where we can provide sustainable and connected mobility solutions which will help to drive fleet safety, compliance and efficiency to new levels, all in a sustainable manner. “My focus is going to be on ensuring we deliver the highest standards of customer satisfaction and growth. There are a lot of companies evaluating new ways of working as the country starts to build back stronger, smarter and greener from the pandemic, and we are confident this will bring new opportunities for Michelin – both with tyres, and around tyres.” He takes over the responsibilities of B2B Sales Director from Chris Smith, who previously held the role as part of his wider remit as Managing Director. Smith is moving to Michelin’s international headquarters in Clermont-Ferrand, France, and will take over the role of Global Marketing Director long distance transportation, from 1 November. Smith joined Michelin in 2007 and has extensive experience across the business – including nearly three years as Head of Truck Marketing for the UK and Ireland, followed by a year as Truck and Bus Marketing Director for North Europe.

Andrew French
Irish haulage companies set to save up to
€4,000 per fleet vehicle annually
The Irish Minister of State for Skills and Further Education, Niall Collins has formally launched a new innovative Eco Driving course for the haulage sector in Ireland.
The three-day SMART Driving programme, targeted at existing professional HGVs drivers, will help participants to develop behaviours and techniques that will improve fuel efficiency and road safety, reduce emissions, and will create cost savings for businesses & employers in the haulage sector. According research conducted during programme development, haulage companies who participate in the course are set to save up to €4,000 annually in fuel and maintenance costs per fleet vehicle. Speaking at the launch, Minister Collins said: “The Programme for Government 2020 outlines our commitment to reduce Ireland’s greenhouse gas emissions by 51% over this decade and to achieving climate neutrality by 2050. I am delighted to be launching this programme as it provides a great example of how industry and Government can work collaboratively as we all work towards the achievement of these goals. “This programme will not only assist haulage companies to reduce their carbon emissions, it will also provide upskilling opportunities for those working in the sector which has seen huge technological advances in recent years.” The programme has been developed by Mayo, Sligo and Leitrim Education and Training Board (MSLETB) in collaboration with Waterford and Wexford Education and Training Board (WWETB) in partnership with the Irish Road Haulage Association (IRHA). The programme is funded by SOLAS through the “Skills to Advance” policy initiative under a competitive “Innovation through Collaboration” call for proposals. Designed to meet specific upskilling needs in the HGV sector, the programme aims to support employers in the haulage sector which is experiencing significant change in work practices due to emerging opportunities in new technologies such as advanced tachographics, AI predictive systems for fuel efficiency, and digitisation in everyday driver activity. Coupled with this, the sector is also experiencing increasing economic vulnerabilities and significant challenges due to environmental pressures, Brexit, Covid-19, and changing markets. The programme is designed to help mitigate against these challenges by upskilling professional drivers in eco-driving behaviour (creating fuel savings & lowering emissions), digital technology (in-cab and hand-held devices, for example), safe driving and driver health and well-being. Also speaking at the launch was Paul Jackman, Vice President of the IRHA: “The nature of work for HGV drivers, with the equipment being utilised, digitalisation, market demands, regulatory compliance and changing work practices, has evolved in the road haulage sector almost beyond recognition in the last fifteen to twenty years. “These changes coupled with the high average age in the sector very much suggests the need for an upskilling course for this current crop of drivers. Upskilling opportunities will help drivers deal with this new world while best availing of new technologies and practices. This will help drivers get a better understanding of their modern work environment and equipment thus helping drivers to drive and work in a safe and compliant manner, while using less fuel to do so.”