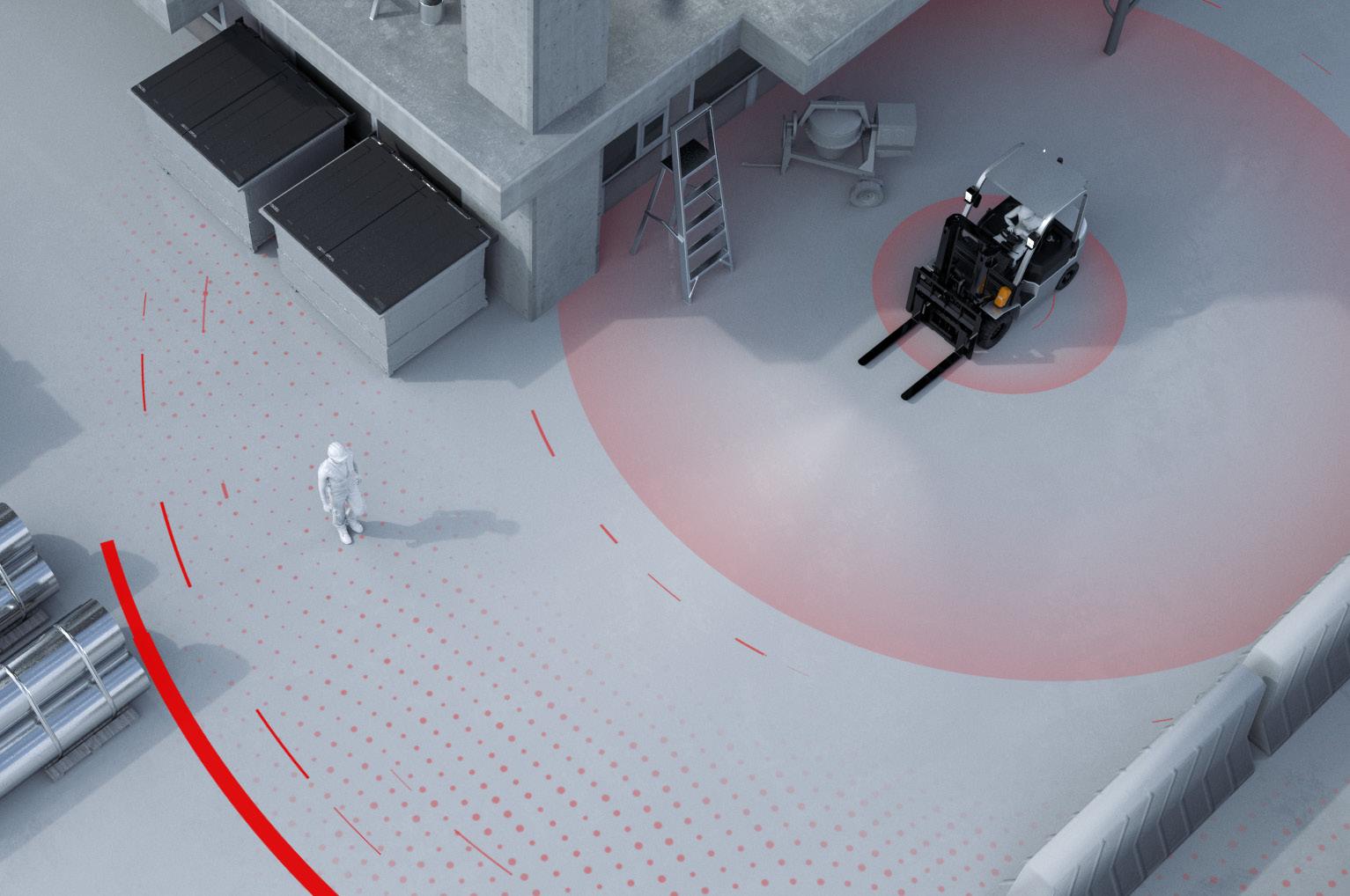
9 minute read
Seamus Leheny, Logistics UK Policy Manager-NI
Seamus Leheny
Policy Manager - Northern Ireland. Logistics UK
THE HGV DRIVER SHORTAGE HITS CRISIS POINT
The HGV driver shortage is still making headlines across the UK, with supply chains under extreme pressure of a UK-wide short fall of 90,000 of these critical workers. With HGV drivers at the heart of Northern Ireland’s supply chains – their work helps to ensure the nation and its supermarkets, schools and hospitals are stocked with all the necessary essentials – it is vital that this issue is resolved quickly. In this month’s column, I will provide an overview of the causes, the proposed solutions as well as an update on Logistics UK’s campaign work to guide government towards a resolution.
While there was a shortage of HGV drivers prior to the COVID-19 pandemic and Brexit, these two events have exacerbated the situation, leading to the crisis we see today. The pandemic halted driver training and testing for more than 12 months, leading to a backlog of more than 26,000 positive tests, while an estimated 14,000 EU drivers returned home during the pandemic and following the end of the transition period. Longer-term contributory factors include the poor facilities available to drivers while on the road, including a lack of sufficient overnight parking spaces, which continues to be a huge impediment to attracting more people to join the industry. The logistics industry is committed to employing domestic drivers to overcome the current shortage. But while these drivers are trained and qualify into the workforce, which can take up to nine months, and DVSA works through its backlog of outstanding HGV driver tests – which we estimate could take until early 2022 – temporary visas made available for European workers would help to overcome the current supply chain problems experienced across the UK. The industry needs drivers now, and we are urging the government to replicate its temporary visa scheme, introduced for agricultural workers and already in place for seven industries, for logistics to keep trucks and vans moving in the short term. While the government has rejected this call, we will continue to press upon the authorities that this is the only solution available to deal with the immediate, short-term crisis, while new domestic HGV drivers enter the workforce train and qualify, a process which can take up to nine months.
Funded Training
Logistics UK is also urging the government to review longer-term measures, such as implementing funded training to open the industry up to as many people as possible and counteracting the long-term recruitment issues which logistics has faced for many years, such as poor welfare facilities. Three years ago, the government pledged to increase the availability of secure, safe parking spaces for lorry drivers, but has not delivered on its promise. Rest facilities across the UK’s road network lag far behind those available on the continent, and it is imperative that the welfare of drivers is prioritised to encourage new recruits to enter the industry. Logistics UK would also like to see more government support, in the form of interest-free loans or grants to aid those looking to retrain into this vital role, similar to the university loans scheme.
More Incentives
Businesses within the logistics industry are already playing their part to attract workers, with many increasing pay rates, offering bonuses, and implementing internal training schemes. Logistics UK itself is working closely with The Department for Work and Pensions (DWP) Job Centre Plus network to link individuals to roles in logistics, and also supports Think Logistics’ campaign to attract young people into the profession. The business group is coordinating a weekend of activity nationwide, called “Discover Logistics Careers,” from 28 November to 1 December, during which member businesses are being encouraged to open up their premises to potential employees to educate them about the work of the sector, provide work experience opportunities and advertise current job vacancies. To find out more about how to get involved, please visit logistics.org.uk/discover-logistics-careers
Local Efforts
Locally here in Northern Ireland, Logistics UK is working with local government on a proposed new all age apprenticeship that could potentially be fully funded and available to those wishing to become HGV drivers. If successful, this new apprenticeship could be ready for delivery by the end of 2021. The logistics industry is committed to protecting Northern Ireland’s supply chains, but it needs the right government support to do so. Logistics UK will continue to press government for decisive action on the HGV driver shortage to tackle both the long- and short-term causes that have led to the crisis we see today.
Brigade Electronics launches ZoneSafe proximity warning system
Brigade Electronics has added ZoneSafe, a Radio Frequency Identification (RFID) proximity warning system, to its range of vehicle safety systems.
ZoneSafe works by using RFID technology to create detection zones around vehicles, reducing the risk of injury or damage from collisions and near miss occurrences to people and property. Designed for use in challenging environments, such as warehouses, construction sites, manufacturing sites, waste sites, airports and distribution centres, ZoneSafe uses vehicle-mounted antennas that communicate with detection tags, which can be worn by workers, set up in restricted areas or placed on objects or property. When a tag enters a detection zone, the vehicle operator will automatically receive a visual and audible alert via the in-cab control unit, which will enable them to take the necessary action. Tags worn by workers on foot will also vibrate to warn of an approaching vehicle. Due to the RFID technology, which does not require line-of-sight, tags will be detected regardless of obstructions, blind spots, adverse weather conditions or poor visibility. Each tag can be uniquely identified and linked to individual people. Emily Hardy, from Brigade Electronics, said: “Approximately 70% of incidents on sites happen during initial machine startup and low speed movement because of poor visibility. This makes ZoneSafe ideal for vehicles and mobile plant that frequently operate within close proximity to workers and other machines, particularly in difficult conditions. It provides fast, reliable and accurate data exchange without any limitation on the number of tags or antennas in operation.”
BPW wins the coveted ETM Award for the 15th time in a row
Barely any other trailer component has as much impact on the added value per kilometre as the running gear, which is why BPW Bergische Achsen KG has now won the ETM Award for the 15th year in a row.
The award is one of the most sought after in the industry and gives transport professionals from the vehicle and logistics industry the chance to have their say. Claiming the top spot has become an annual tradition for the company, as no other provider offers more-advanced technology. “In the transport and logistics industry, everything revolves around the question of which technology can be used to generate more added value per kilometre. Choosing the right axle and running gear systems is crucial here,” comments Ralf Merkelbach, Head of Key Account Management Large Fleets Europe at BPW, “which is why at BPW we invest in innovative technologies more than any other provider and work closely with hauliers in our development work. The result is the most advanced running gear technology on the market, which gives vehicle operators a decisive advantage.” BPW actually uses more than steel and aluminium when constructing axles and running gear – it also uses data. The global player and family-owned company based in Wiehl, North Rhine-Westphalia, has fitted selected trailers with specially developed data collection devices (Mini Black Box) that accurately record every movement. Whether a trailer is speeding over the potholes of the Silk Road in China, climbing the road to a mountain pass in Eastern Anatolia, driving through the monsoon in India or being subjected to hard braking at a motorway junction in Germany, every physical detail is registered and used to fine-tune the running gear components for maximum sturdiness and efficiency. The result is a modular component kit where every individual part is based on a ‘digital twin’ and can even be put together online to create running gear that is precisely tailored to the intended use. The artificial intelligence in the configurator helps the vehicle engineer to choose precisely the right combination. This year, BPW completely rebuilt the successful Airlight II running gear, which is among the top-selling trailer running gear in Europe. This achieved a weight saving of 60 kg for the vehicle operator – and gives the vehicle manufacturer even more flexibility in the design. Ralf Merkelbach says: “The new version of Airlight II proves that we do not rest on our laurels at BPW. By digitising our running gear kit, we have replaced the conventional development cycles with a continuous renewal process. This means that every BPW running gear is always the most up to date and efficient on the market.”
FORS breaks its personal best with record Gold and Silver members
It’s not just Team GB that has been racking up the golds and silvers this summer. FORS has reported that it has reached record numbers of FORS Gold and FORS Silver-accredited members.
As of 19 August 2021, the total number of Gold-accredited members reached a new high of 321, while the number of Silver members stands at a record 1,650. FORS Silver and Gold are the highest levels of accreditation available to members, requiring operators to meet more exacting standards and hold themselves to a higher level of accountability than at Bronze level. The recent increase in the number of operators opting to progress to higher levels of FORS accreditation is testament to the value of FORS Silver and Gold and the benefits that operators of all shapes and sizes can enjoy, particularly in relation to efficiency, cost reduction and winning new contracts. Data from the FORS 2019 Performance Survey revealed that, for Bronze operators, on average 26% of contracts require FORS. For Silver and Gold operators, however, the percentages rise to 38% and 51% respectively. Overall, 38% of FORS members reported winning work over competitors as a direct benefit of FORS. When it comes to cost and efficiency savings, the case for FORS membership is just as compelling. 24% of FORS members reported saving on their insurance premium, at an average saving of 8.2%, while the average yearon-year change in MPG for Gold members equates to a whopping 12%. Gold members also demonstrated improved fleet safety, reducing the number of annual incidents by 31% on average. John Hix, FORS Director, said, “We are delighted to see our membership levels continuing to rise at Silver and Gold level. Our data and member feedback consistently demonstrate the benefits of FORS and its growing importance in the tendering process. We are always evaluating our offering to ensure that members get the very most out of FORS, no matter the size or make-up of their fleet”. FORS members work through the progressive levels of the scheme and adhere to the FORS Standard, which sets out the requirements operators must meet if they wish to become FORS accredited. The document is updated every two years to ensure it keeps abreast of industry trends and upcoming legislative changes. The latest iteration of the FORS Standard, version 6, is due to be published in October 2021 and implemented in July 2022, having being postponed by one year to minimise disruption to FORS members in light of the COVID-19 pandemic.