
4 minute read
CDE and Skipway open day
CDE & SKIPWAY OPEN DAY SHOWCASES LATEST TROMMEL FINES SOLUTION
Skipway’s Dunmurry plant recently opened its doors to its latest trommel fines wash plant to demonstrate how CDE wet processing technology is supporting the waste management firm to divert over 95% of its trommel fines from landfill.
The event, which started with a guided tour of CDE’s world-class manufacturing facility in Monkstown, enabled guests to see the 300,000 sq. ft. facility in operation, where CDE’s advanced wet processing solutions are commissioned for customers around the world, from Creagh Concrete in Toome, Northern Ireland to Posillico Materials LLC on Long Island, New York, from Repurpose It in Melbourne, Australia to Feiring Bruk, Norway. As part of a long-term investment strategy in its manufacturing capabilities, CDE recently commissioned two new Bystronic high-speed sheet metal laser cutting systems. The systems integrate with a new 400-tonne steel storage and management system incorporating fully automated loading and offloading of the laser cutters. Following the tour of CDE’s facility, guests were invited to tour its latest trommel fines solution, designed and engineered for Skipway. The new 50 tonnes per hour (tph) trommel fines plant, the first of its kind in Northern Ireland, has been commissioned at the waste management firm’s processing site in Dunmurry, one of three recycling facilities it operates in Belfast, Lisburn and Portadown. It diverts trommel fines from landfill and converts the material into a resource by producing recycled products with the same specification and quality as quarry grade sand, therefore making it suitable for concrete and building products while also improving the quality of other recycled aggregates such as pipe bedding and recycled hardcore. CIRCULAR ECONOMY BENEFITS
Skipway director Trevor Heatrick said: “By putting trommel fines through a wet processing plant the clean sand and aggregates recovered can be resold and reused in the secondary aggregates market. This minimises disposal costs, as well as closing the loop on challenging waste streams to create a more circular economy and generating additional revenue for our business.” CDE business development manager Fergal Campbell added: “It was good to guide our industry colleagues through the entire CDE process as part of the open day event. From fabrication through to the commissioning of a plant, this event highlighted the engineering excellence for which CDE has become renowned over its 30-year history.” Skipway was acquired by the R. Heatrick Group in 2012. The company had many years of experience in the recycling of demolition wastes and acquired Skipway to further diversify into the recycling industry by providing skip hire and investing in the materials recovery facility. Following this acquisition R. Heatrick Ltd continued to grow under the Skipway trading name and became a major force in the recycling industry through investment, innovation and providing a fast and reliable service that’s unparalleled to their competitors. The plant incorporates AggMax modular logwasher, EvoWash sand wash plant with Counter Flow Classification Unit (CFCU), AquaCycle thickener and static screens. Through the washing process, the plant removes the lightweight and organic material
THROUGH THE WASHING PROCESS, THE PLANT REMOVES THE LIGHTWEIGHT AND ORGANIC MATERIAL DIRECTLY LINKED TO LOSS ON IGNITION (LOI) AND TRANSFORMS THE LARGEST PROPORTION OF THE TROMMEL FINES WASTE STREAM INTO SELLABLE PRODUCTS FOR THE CONSTRUCTION MARKET.
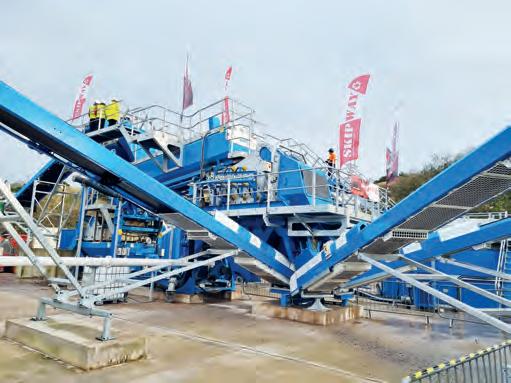


Trevor Heatrick, Director, Skipway and Tracy O’Kane, Technical Innovation Lead, CDE.
directly linked to Loss on Ignition (LOI) and transforms the largest proportion of the trommel fines waste stream into sellable products for the construction market. Added Fergal Campbell: “At CDE we’re passionate about contributing to a circular economy and enabling our customers with our innovative technologies so they can play their part. Skipway’s local landfill is reaching capacity so it’s encouraging to see them so passionate about landfill diversion and extracting the value that we can get from waste streams like trommel fines and reusing outputs, such as sand for concrete. INDUSTRY’S FUTURE
“Plants like this are the future of the industry in their ability to minimise waste and maximise value. It’s been a pleasure to work with Skipway and we really look forward to seeing how this partnership can contribute to Northern Ireland’s circular economy.” And said Trevor Heatrick at Skipway: “We had numerous other options in front of us, however CDE displayed their knowledge and expertise from the sales stage through to the delivery of the project. Every aspect of the material processing that they highlighted as being required, we can see the benefit of now. One of our biggest issues was that our material contains a lot of polystyrene which can be hard to remove, and we found that CDE had the best and most robust solution in ensuring that this material could be removed. “CDE were able to create a product tailored to us which is helping us achieve the goals that we presented them with. Close collaboration meant that we were able to have input on the design of the plant so that it addressed our needs and did the job we wanted it to do. Working with CDE was an easy process and we’re delighted to be able to push the boundaries in sustainable innovation.”