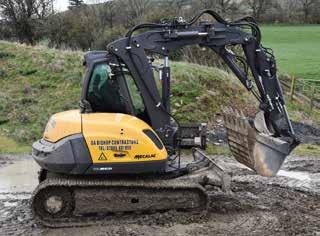
7 minute read
Versatile Mecalac 10MCR Impresses D A Bishop Contractors`
view from the cab VERSATILE MECALAC 10MCR IMPRESSES D A BISHOP CONTRACTORS
If there’s a single word to describe the Mecalac MCR crawler excavator it has to be ‘versatile.’ Lifting, laying, moving, unloading, storing... whatever you need to accomplish, whatever the challenge, the MCR sets the pace and makes execution easy.
Well, that’s what the manufacturer claims, adding, it’s capable of working side-by-side with trucks, or carrying a pallet loaded with material and laying it to rest on the other side of a wall, or even next to the machine itself, whatever you need. But is that really the case? Plant & Civil Engineer’s David Stokes recently caught up with Matt Bishop who acquired a new Mecalac 10MCR a few months ago for the family business base at Welshpool in Wales to find out what his ‘view from the cab’ is. Matt didn’t have many reservations when it came to adding the 10MCR to the company’s growing fleet of mixed machinery; it already operates an 8MCR, and has done so since November 2017. “The 8MCR hasn’t disappointed, and neither has the new 10 tonne addition,” says Matt. “It really is a fantastic machine. Very flexible, very versatile.” The company, established by Matt’s father in 1974, is heavily involved in general contracting, land drainage, excavation and agricultural projects, so versatility, durability and reliability of equipment are essential ingredients in its continuing success and growth. “The Mecalac is essentially two machines in one; nothing else comes close to its flexibility, in my opinion. You can’t really compare it to other excavators; it’s just on a different level when it comes to versatility.” Thanks to a simple selector-switch, you can turn this compact excavator into a compact loader and then back again, using the same commands. Familiarisation is instant in the single mode of operation thanks to grouped functions and the transformation into loader mode using the control level. Loading efficiency is maximised, thanks to the skid bucket being supported on the blade which increases the machine’s efficiency as the force of the thrust is transmitted directly from the chassis to the bucket. The operation is performed more accurately using the control lever; the patented Mecalac cylinder coupling function allows you to synchronise the boom cylinders for perfect movement coordination and precision. It makes driving and handling easy, regardless of whether the operator is a novice or more experienced. The Mecalac “CONNECT” hydraulic quick coupler system means that attachments can be changed in just a few seconds, without having to get down from the cab. Designed to work in both directions, the loss of an attachment is virtually impossible, during the locking or when working in excavator mode or in loader mode. It’s been described as the safest and best performing quick coupler system on the market.
Compact Cab
The 10MCR features a compact cab offering excellent comfort and allround visibility, essential when working on busy or challenging projects. The rear hood lines of the machine have obviously been carefully studied by
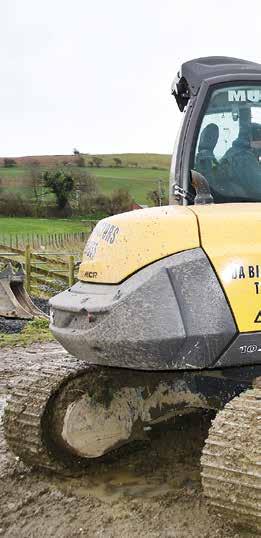
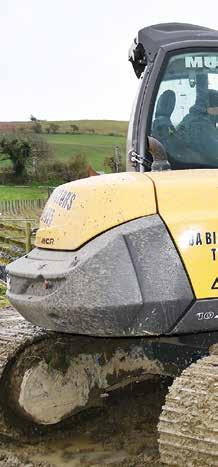
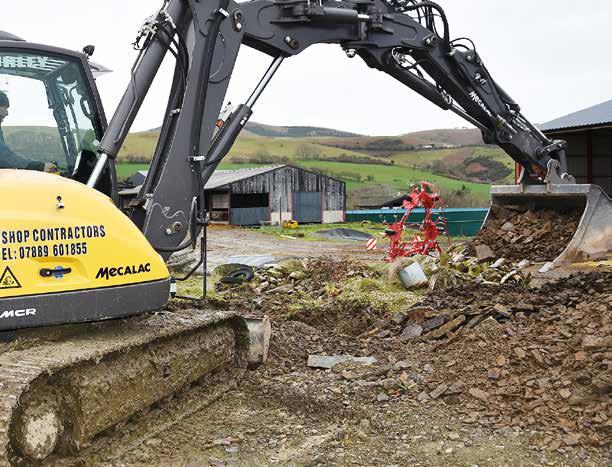
the designers. The windshield is fully removable, allowing the driver the option to remain in constant contact with the outside world. A TFT colour screen makes the control panel very easy to use. Regardless of brightness, the operator can easily view all useful information: mode currently being used, speed, engine speed, number of hours, cylinder selected, safety features activated. “It does take time to master the various controls, to become comfortable in doing so, but once you do, it comes second nature,” says Matt, who initially honed his operating skills on the Mecalac 8MCR before progressing to the new excavator. That said, the functions on the control levers are reckoned to be easier to use than those on standard equipment.
Flexible & Efficient
The fact that the 10MCR can almost be whatever you want it to be on site means fewer machine deployments and that can result in lower fuel consumption, less damage and ground compaction, less annoyance for local residents, fewer dangers for site workers, and fewer working breaks. Think about it! As the MCRs are the only compact loaders with total rotation on the market, in addition to the exceptional speed until 10 km/h (6.2 mph), they are perfectly independent, powerful, and fast when travelling as well as in work cycles. The MCR, incidentally, is also equipped with the famous patented Mecalac boom. With the in-build offset, the boom folds in to 130° to offer maximum stability associated with exceptional lifting and handling performances. Indeed, as we discovered, the equipment’s lifting capabilities and versatility mean that it can virtually have a thousand different uses; no wonder it is a firm favourite with contractors like D A Bishop.
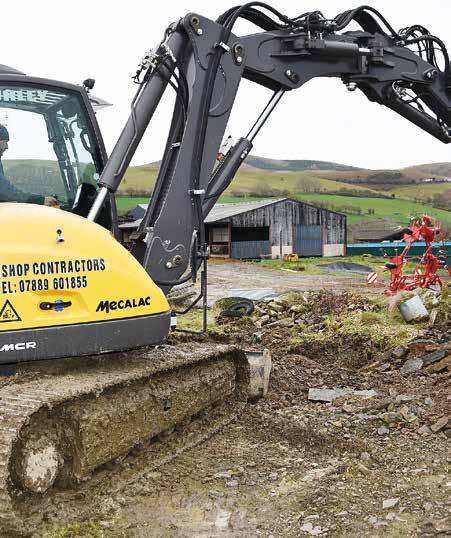
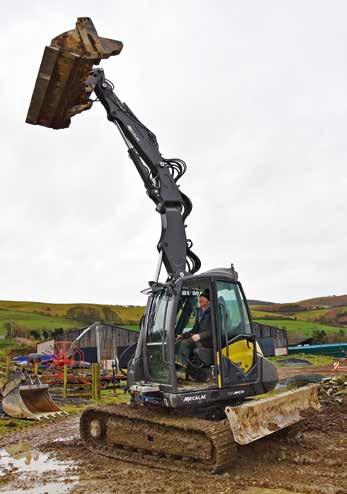
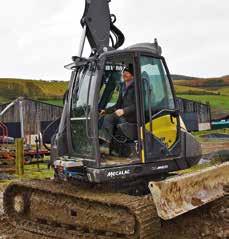
news
Construction Industry helpline provides £1.25m of charitable support to the industry
2018 was a difficult year for the construction industry and the human impact of the stress and strains of working in such an environment is clearly being seen by the Lighthouse Construction Industry Charity.
Last year, 1662 construction families in crisis called the helpline. 662 of these cases were seeking emergency financial support, an increase of over 40% on 2018. The amount of charitable giving provided in 2018 was £1.25m, rocketing a staggering 75% on the previous year. Of the 1662 cases presented to the helpline, 1033 of these were given advice and support on issues ranging from mental wellbeing issues through to legal, debt management and taxation advice. The charity has also seen a huge increase for requests of their helpline packs and now have over 350,000 helpline cards in circulation within the construction workforce. Bill Hill, CEO of the Lighthouse Construction Industry Charity said, “On the positive side the 2018 figures show that we are reaching out to more construction workers and their families, but it also means that too many of them find themselves in desperate situations. The significant escalation in families needing our support has taken us by surprise and has put pressure on our finances. With two construction workers taking their own life every single working day, and stress, depression, and anxiety accounting for a fifth of all work related illness, it’s vital that we continue to provide our helpline services and put additional funding into the construction industry’s dedicated and volunteer led, Building Mental Health programme. But the only way that we can plan ahead is with predictable income. That’s why we launched our Company Supporters initiative and our ‘Save a Life’ campaign. We’re urging companies to pledge a regular annual donation to ensure the long term sustainability of our valuable charitable services. If you’re reading this and wondering how your company can make a difference, then here’s how to get involved.” https://www.lighthouseclub.org/ lighthouse-company-supporter/ With the support of construction software firm ‘COINS’, the charity has also recently launched their helpline app. The app helps people find out more information about how they can help themselves or take the next step in seeking professional help. It is a preventative tool and provides support at the early stages of a situation so that the problem does not reach a life critical stage. It provides vital information, advice and guidance on many wellbeing topics including stress, anxiety, depression, anger and suicidal thoughts. For more information visit https://www. constructionindustryhelpline. com/our-app.html To access the helpline’s team of experts, call the Construction Industry Helpline on 0345 605 1956 or visit www. constructionindustryhelpline. com
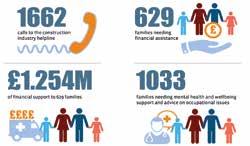
Lagan Airport Maintenance Upgrading Runway at London Southend Airport
Lagan Airport Maintenance (LAM) has been appointed by Stobart Rail & Civils to carry out an essential maintenance project to upgrade the durability and performance of the runway at London Southend Airport.
Works commenced on site in January 2019 and are expected to last three months. The project team will carry out works during strict night-time possessions from 23.30pm – 05.30am. It will involve removal of 50mm of the existing surface course and installation of 200mm overlay of grooved Marshall asphalt utilising an in-house batching plant. Other works will include friction testing, Airfield Ground Lighting and white lining. Kieran McIlhatton, Lagan Airport Maintenance Director, commented: “The team at Lagan Airport Maintenance are thrilled to have secured this project at London Southend Airport. We look forward to working collaboratively with the airport team whilst delivering the project to the highest safety and quality standards.”
PLANT & CIVIL
Find us on


