
17 minute read
Rapid Celebrates 50 Years of Mixing Technology Expertise
RAPID INTERNATIONAL: CELEBRATES 50 YEARS OF MIXING TECHNOLOGY EXPERTISE
Rapid International Ltd recently celebrated its 50th anniversary; established in County Armagh in 1969, the company is one of the world’s leading manufacturers of mixing technology for the concrete, construction, environmental, nuclear, mining and tunnelling industries.
In 1969, at a period in Northern Ireland’s history when political and sectarian violence were commonplace, Rapid’s founders, Robert (Bertie) Pickering and Jim Lappin intended to bring about advancement, progress and hope for the local economy. Founded on 1 September 1969, Craigavon Engineering, originally manufactured agricultural equipment in a humble 7m x 4m domestic garage. From the outset, Bertie and Jim were renowned for their exacting quality standards and customer focus. Demand subsequently grew and in the 1970’s the business relocated to a larger custom built facility, diversifying into manufacturing ready mixed and precast concrete plant. Today, each machine is produced in Rapid’s 50,000 square foot purpose built factory, which underwent a recent extension to include a new £1 million state of-the-art Hodge Clemco shotblasting facility and Dalby paint booth. In 1982, Rapid launched the first in a range of concrete mixers, the Rapid Pan. The very first of these was sold to J Graham and Sons Ltd in County Down and is still operational today, 37 years later. The product range later expanded in 1992 to include the novel Rapid Reclaimer, a reclaiming unit for the recovery of unused concrete. The ground-breaking invention was met with industry acclaim and featured on BBC’s Tomorrow’s World. Rapidmix, Rapid’s flagship product, was first launched in 1997 and later adapted to include full weighing capabilities in 2012. Rapidmix is a totally mobile and self-contained, high volume continuous mixing plant ideal for
Managing Director Mark Lappin (left) with John Pickering, Operations Executive.
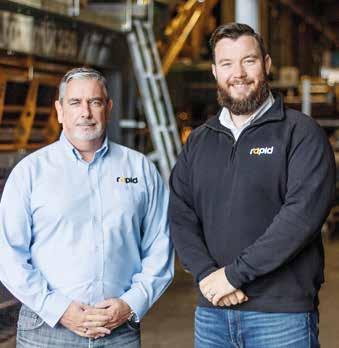
a wide range of concrete, construction, civils and environmental applications.
Applications expertise
New product development remains a strong focus for Rapid and the product range has expanded considerably since 2009. Rapidbatch, Rapid’s first fully mobile concrete batching plant, was launched in 2009, as was the Rapid twin-shaft concrete mixer. Transbatch, a compact, single load version of the Rapidbatch plant, was launched in 2011, followed by Trakmix, an innovative track-mounted mobile continuous mixing plant in 2015. In recent years, Rapid has witnessed a demand shift towards specialist applications such as contaminated land treatment, mine back fill, tunnel finings, marine
dredging, bentonite and many more. Rapid’s in-house team of highly qualified and experienced design engineers, sales team and skilled operatives work in total collaboration with the customer to achieve a completely bespoke solution.
Begins exporting
After the success of the Reclaimer launch the company set its sights on penetrating international markets and in preparation for this, changed its name to Rapid International Ltd. Rapid officially commenced exporting in 1995, initially to the USA and later in 1996 to the Middle East. Today, Rapid has a presence in over 20 countries via a wide reaching international dealer network. Sadly, in 2007, Robert (Bertie) Pickering, co-founder and Managing Director, passed away after a short illness, later followed by fellow co-founder Jim Lappin in 2018. Mark Lappin, son of co-founder Jim Lappin, was subsequently appointed Managing Director and continues to lead the company to the present day. While Rapid’s operations have expanded, the families underlying principles of hard work, trust, feedback, care, collaboration and relentless dedication to quality have remained constant to the present day.
Entrepreneurial spirit
Commenting on the milestone, Mark Lappin remarked, “As we reflect on the last 50 years, it’s clear we owe our continued success to the entrepreneurial spirit of our founding partners, which the company is still driven by today. We continue to push boundaries, seek out new product innovations and enter new global markets on an annual basis. As was the case in 1969, total quality,
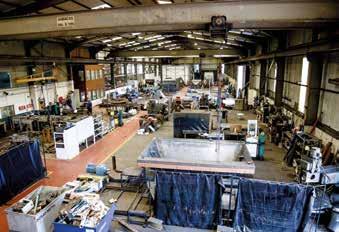
On the shopfloor.
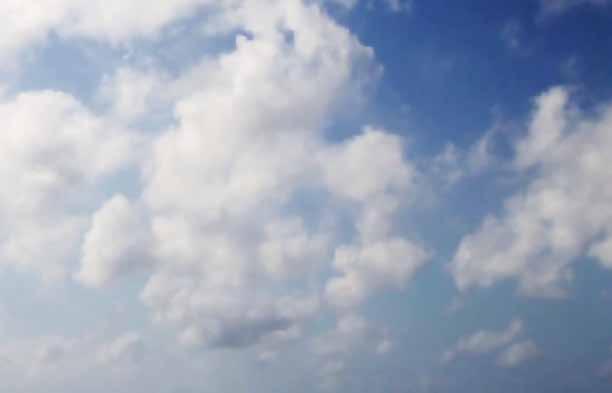
technological advancement and customer focus still remain at the core of Rapid.” Mark continued, “It’s been my privilege to lead Rapid for the last 13 years and personally witness Rapid’s success for 30 of its 50 years. We wish to sincerely thank our customers, dealer partners and suppliers for the loyalty and trust they have placed in us over the last 50 years. We look forward to continuing these partnerships in the years that lie ahead.”
Rapid expansion
In an effort to streamline its supply chain, Rapid recently welcomed Rapid Power Generation, formerly A1 Power Systems, into the Rapid family. Rapid Power Generation, a Volvo Penta preferred partner, is a leading manufacturer of bespoke diesel powered generating sets from 10Kva – 2500Kva.
Charity gala
Rapid will be hosting a 50th anniversary charity gala dinner and raising funds for Marie Curie and Macmillan Cancer Support in memory of Rapid’s co-founders. The company hopes to raise a generous sum to support these two very worthy causes. If you wish to offer a charitable donation, please visit: www.justgiving. com/crowdfunding/rapid-international
The new Rapid façade.
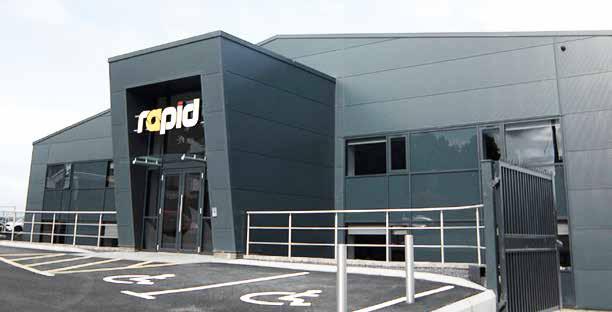
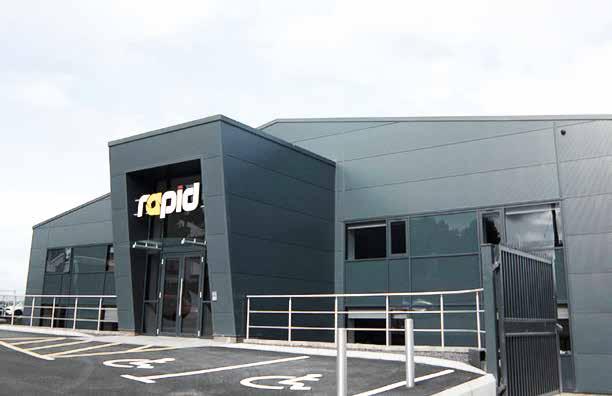
news
SITECH Brings Trimble’s Latest Visualisation Technology to UK & Ireland
The market for project modelling and visualisation is set to see a new addition this Autumn, as SITECH UK & Ireland brings Trimble’s latest technology solution, Trimble SiteVision, to the UK & Ireland.
SiteVision utilises the latest in augmentedreality technology, paired with highly accurate GNSS survey data, to provide a detailed 3D visualisation of existing infrastructure, design plans and future structures, all in the palm of the user’s hand. By interpreting site data and building an ultra-realistic 3D model, the new system can help to spot and solve issues early in the planning phase, as well as providing unparalleled client engagement opportunities. In addition, SiteVision can even utilise data from Trimble’s range of machine control systems to show accurate cutand-fill information, as well as delivering accurate and visual site progress updates. The system is designed as a combined hardware and software offering that leverages Trimble’s powerful technology packages. These include Trimble Catalyst to ensure accuracy to within centimetres, the cloud-based storage system Trimble Connect and Google’s ARCore, the leading AR-experience building platform. Trimble has developed the new system to synergise with their other technology services, allowing SiteVision to be available at an extremely competitive entry price point. The system uses a subscription-based service model that delivers real value for customers, providing everything that site managers or surveyors could need in a single package. SITECH UK & Ireland will be launching SiteVision to the UK & Ireland market in Autumn 2019 and have already opened registrations for technical demonstrations of the system that are set to begin this month. Danielle Barker, Regional Sales Manager for SITECH UK & Ireland, commented: “SiteVision is the latest in a long line of groundbreaking site technology advancements that Trimble has developed. The power of the device is amazing, especially as it contains everything within a handheld package. “It’s going to add a new dimension for planning and site management activities. SiteVision’s versatility means that it can be used for everything from initial works assessments right through to client engagement, providing a powerful tool that is useful at any stage of the construction process. “SiteVision is just the first in a huge range of new and exciting technology offerings that we’re working with Trimble to deliver over the next few years. It’s vital for us that our customers are at the cutting-edge of site and productivity technology and as such we’re thrilled to be able to bring SiteVision to the UK & Ireland. We know that our customers will immediately see the immense benefits that the new system can provide and we can’t wait to see their reaction.”
Are you optimising your R&D Tax Credits?
Momentum specialise in R&D claims for the manufacturing, quarry, construction and plant machinery sectors Over £130m R&D tax relief claimed Over 850 claims 100% success rate Free Consultation Free ‘Second Opinion’ Review Unlock your true R&D potential
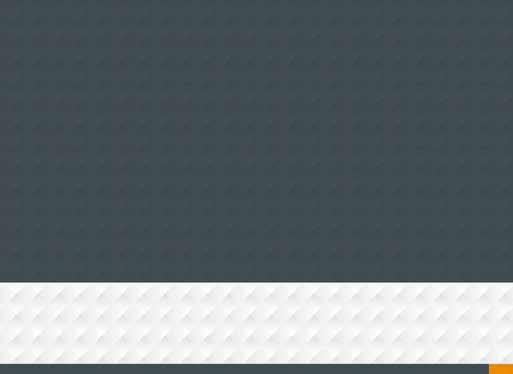
T: +44 (0) 28 9140 4030 W: momentumgroupni.com
open day TEREX FINLAY ‘CRUSH’ RAISBY QUARRY, WITH SPECTACULAR TWO DAY CUSTOMER EVENT
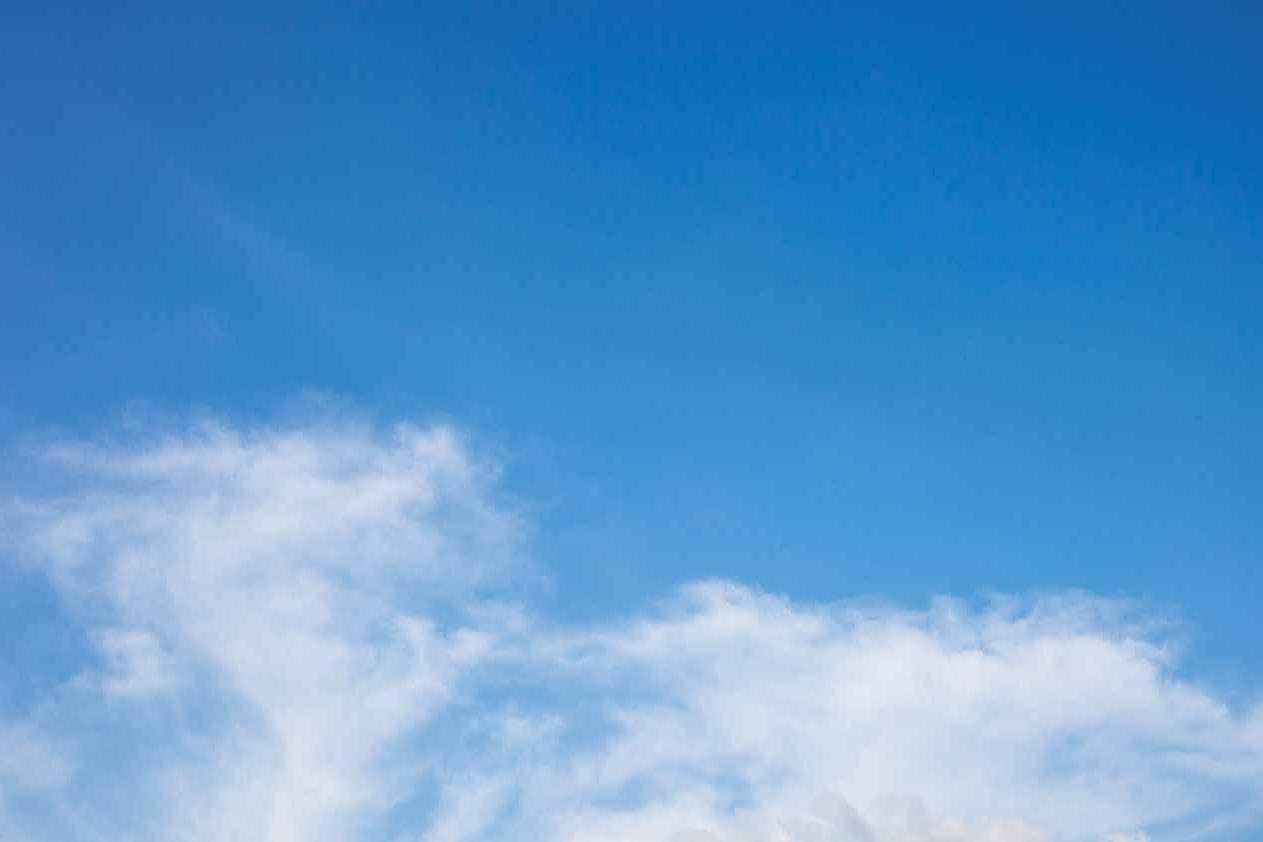
Terex Finlay, in conjunction with Finlay Molson and Finlay Scotland, recently hosted two open days event at Breedon Aggregates (Northern Ltd)’s Raisby Quarry in County Durham in the north of England where an incredible 19 machines were on display.
At the event Terex Finlay previewed two versions of their new 694+ inclined screens in advance of their production launch in Q4, 2019. The recently launched TC-100 and TR-75 conveyors where also showcased for the first time at a customer event. Visitors were also treated to live demonstrations of the innovative new ‘OMNI by Terex’ system that was fitted on the main working train of machines. OMNI gives a previously inaccessible level of control to multiple crushing and screening solutions. Nigel Irvine, Sales Director, commented on the event: “It was a huge pleasure to welcome so many customers to yet another successful Terex Finlay open day. Innovation is at the heart of Terex Finlay mission and vision. Not just in terms of the machines that we produce but also in the features that we are incorporating into our machines. “Our T-Link telematics and OMNI system are industry leading. OMNI is pioneering technology unique and exclusive to our business and visitors were impressed with the safety benefits that the system can bring to their operations.
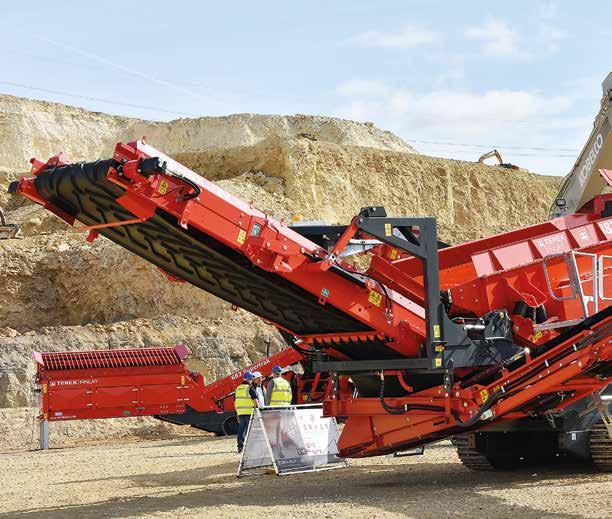
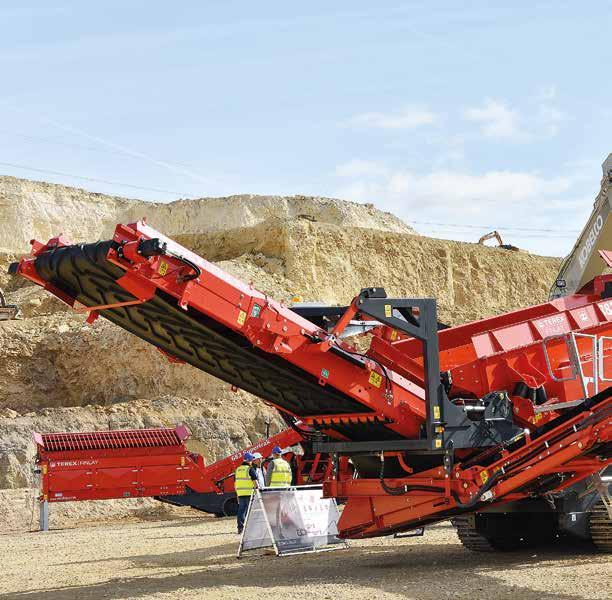
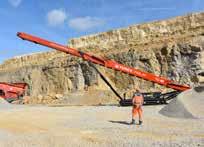
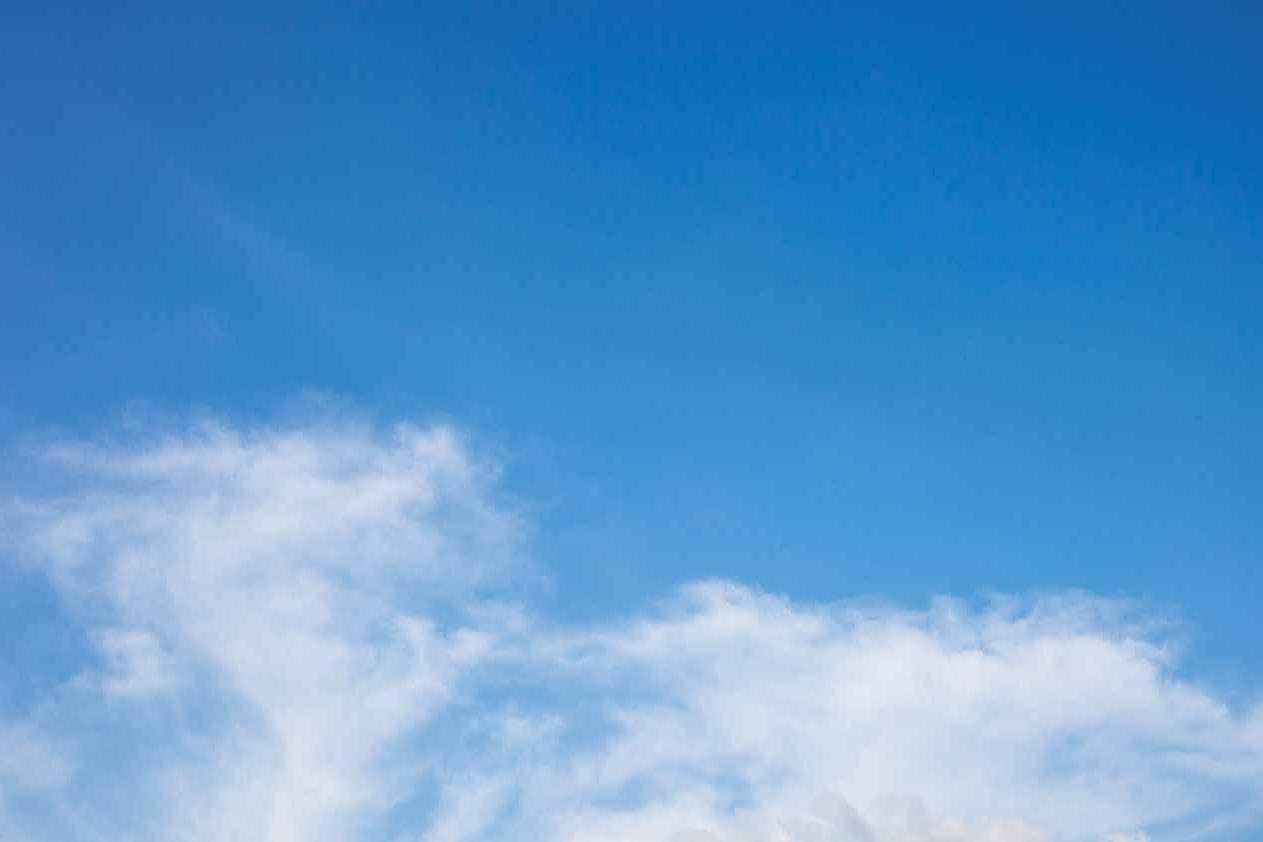
“To our hosts, Breedon Aggregates (Northern), ‘thank you’ for welcoming us and giving us access to such an amazing site and really making our open days a great event. Its success was in large part due to the site and your team members on the Raisby Quarry!” Alan Mackenzie, managing director of Breedon Northern, said: “We were delighted to host Molson Finlay and Finlay Scotland in conjunction with Terex Finlay at our Raisby quarry. We have built a long-standing relationship with the team at Finlay Scotland, as they have been an excellent supplier for us over the years. They have always provided us with a highquality range of products and been there to back them up when needed. “The Terex Finlay products have always served us very well offering great all-round performance. We have a team on the ground that has bought into the brand, thanks to the service and support provided over the years, not only by Finlay Scotland, but the guys at the Terex Finlay factory, too.” OUR T-LINK TELEMATICS AND OMNI SYSTEM ARE INDUSTRY LEADING. OMNI IS PIONEERING TECHNOLOGY UNIQUE AND EXCLUSIVE TO OUR BUSINESS AND VISITORS WERE IMPRESSED WITH THE SAFETY BENEFITS THAT THE SYSTEM CAN BRING TO THEIR OPERATIONS.
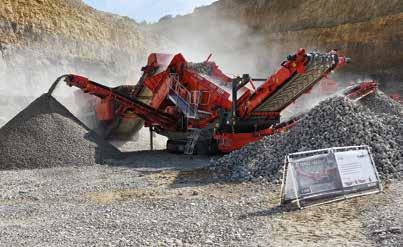
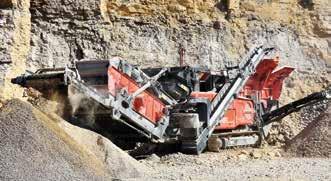
HS2 REVEAL NEW DIGITAL EARTHWORKS SOLUTION
BY PETER HADDOCK
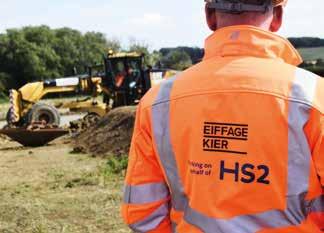
At the beginning of September, I was invited to visit the offices of Eiffage Kier JV in Birmingham, for an exclusive HS2 reveal event, in partnership Finning UK & Ireland.
Effiage Kier is one of the joint venture organisations responsible for the delivery of different sections of the HS2 project. On entering their offices, the first surprise that greeted me was what could only be described as a mini Hillhead Expo. On display were simulators, screens showing 3D models and lots of different solutions, all brought together by Finning. They included demonstrations of the Caterpillar fatigue technology and remote dozer operation, Trimble drone, surveying and 3D machine control solutions and TrellisWorks systems that deliver wireless high-speed connectivity. The HS2 Expo was running for a number of days to introduce both Eiffage Kier staff and the wider supply chain to a brand-new digital earthworks solution, developed not just for HS2, but for the future of the industry. It was an approach that Eiffage Kier had been working on even before it was awarded the contract to build an 80km stretch of the project in June 2017. At the event, David Lowery, Executive Director of Eiffage Kier explained that it has invested in a 23 hectare ‘Heave Monitoring Site’ on the HS2 route, to gain a better understanding of how the ground would move when excavation occurs and how its new DIGital Graphical Earthworks Reporting (DIGGER) strategy would work. Commented David: “‘DIGGER’ is all about taking a step back and looking at every little bit of data that is created and captured for the project. It takes into account the ability to capture and process data now and the flexibility to adapt to new data inputs, as future innovations are created, turning data into useful realtime information. On the site itself, we have drilled 34 boreholes and installed sensors to monitor the movement of the ground. We have also brought in a fleet of Caterpillar equipment to perform the key earthworks operations required.” To bring its DIGGER strategy to life, Eiffage Kier has working in collaboration with HS2, Finning UK & Ireland and its earthworks supplier Blackwell bringing together a connected site and fleet, using the latest Caterpillar and Trimble technologies. The data collected from these technologies and other solutions provided by Finning, like fluid sampling, have all been made available in real-time. This has been achieved through the development of a ‘Single pane of glass’ dashboard reporting technology, by experts at Finning. Called ‘My.Finning.com’, the new solution delivers on the DIGGER principles of being able to track the mass haul activity onsite in real-time, with the ability to monitor and optimise the performance of the load and haul fleet, through excavation, grading and compaction operations. With real-time also comes the opportunity to automate the generation of alerts when operational parameters fall outside of acceptable norms, like under or overloading of trucks for example. In addition, Finning has included information that supports the monitoring of machine health for preventative maintenance.
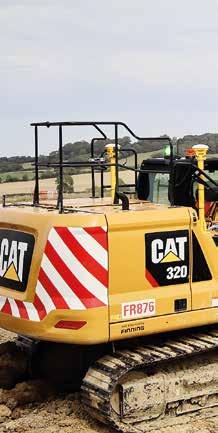
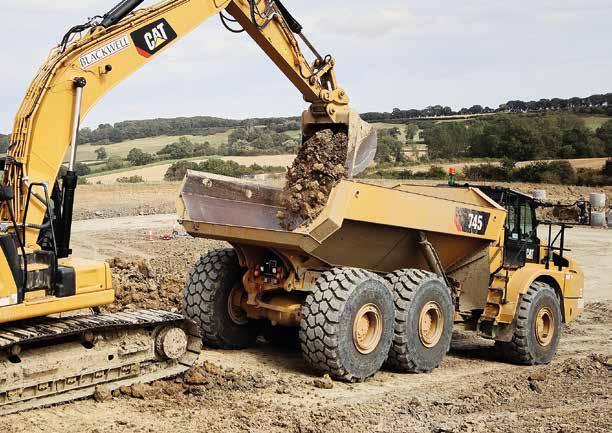
Commenting on the development of My.Finning.com, Ian Stewart, general manager of performance solutions at Finning, said: “With earthworks volumes of up to 32 million cubic metres of cut and fill for its 80km section of HS2, we knew we had to develop something that put this level of control into the hands of the Eiffage Kier and the Blackwell team. To achieve this, we developed a solution that creates powerful insights and analytics data. By putting this solution together with our performance solutions services, we can deliver a new level of operational performance across an earthworks operation. “Sitting in ‘the cloud’ it’s simple to use and easy to access from lots of connected devices. This helps the team and individuals use real-time data to make adjustments and improvements to both operation and plan quickly.” The ‘Heave Monitoring Site’ fleet used on the project includes eight ADTs made up of six Cat 745s and two Volvo A45Gs, fitted with GPS and payload monitoring technology. The technologies ensure payload compliance and allow for cycle time measurement. The ADT’s are loaded by two Cat 352F LME mass excavation spec excavators, with 3.6 cube buckets, fitted with the latest GPS enabled 3D Trimble Earthworks grade control platform. This solution comes with an in-cab colour touch screen monitor, fitted alongside
a Trimble LOADRITE payload management solution. LOADRITE allows the operators to tag each load, so it can be tracked to the exact location on the stockpile. The load and haul fleet are supported by two Cat D6T LGP dozers, fitted with the latest GPS enabled 3D Trimble Earthworks solution, delivering millimetre grade accuracy against the design target grade for the creation of the HS2 line sections and batters. The remainder of the fleet includes a Cat CS76B Compactor with Trimble compaction control system, a Cat 16M motor grader for haul road maintenance and Cat 320s with Trimble Earthworks, used for final trimming works and digging drainage ditches around stockpiles and the main cutting. In addition to the plant, a 4x4 site vehicle has also been fitted with a Trimble Earthworks solution, enabling 3D site monitoring from the vehicle as is drives the site. To support the information transmitted from the fleet, weekly drone flights using the Trimble Stratus solution are being made, helping to obtain ‘as dug’ data for comparison between the information received from the machine control. With the my.finning.com solution created in-house as a modular piece of software, it will not only change how earthworks projects can be delivered now it will also shape the way new technologies can be integrated for the future.
Tom Verner Group Managing Director, The Momentum Group
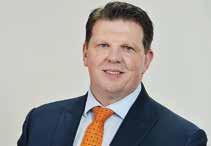
TIGHTENING RULES MEAN R&D TAX CREDIT SPECIALISTS ARE INVALUABLE
R&D Tax Credits are a hugely valuable asset for companies, helping fund innovation and give Northern Ireland a world-class edge in manufacturing and many other industries.
Proof of that statement’s worth comes from HMRC’s own research which found that for every £1 of tax forgone, between £1.53 and £2.35 of research and development is stimulated. That’s quite a return in anyone’s book and is the main reason why the government is putting considerable effort into raising awareness of R&D Tax Credits. The payable tax credit in the SME scheme provides valuable support to loss-making companies. It allows companies to claim a tax credit worth up to 33% of the R&D element of their losses and receive an immediate cash-flow benefit. Because of that, more and more companies realise that much of the dayto-day work which they are carrying out is eligible under the scheme. Somewhat inevitably, such a lucrative scheme has become a target for abuse in some quarters. To date, HMRC has identified and prevented fraud attempts on the SME scheme worth £300 million in total. In these cases, companies were set up to claim the cash available through the payable credit in cash even though they had no legitimate R&D activity. As a direct result, then Chancellor Philip Hammond unveiled new measures to help prevent the misuse of the R&D SME tax relief initiative in 2018 Autumn Budget. As part of the Finance Bill for 20192020, the amount that a loss-making company can receive in R&D Tax Credits will now be capped at three times its total Pay As You Earn (PAYE) and National Insurance contributions (NICs) liability.
On the back of HMRC issuing an apology for delays in R&D Tax Credits not being received as quickly as businesses would like, we believe this shows increased scrutiny in an increasingly specialised field.
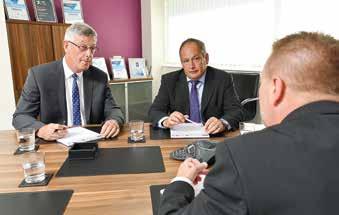
This will come into effect for the accounting periods beginning on or after 1st April 2020. Any loss that a company cannot surrender for a payable credit can be carried forward and used against future profits. This is just one example of how complex the process of claiming R&D Tax Credits can be. Indeed, given the penalties for incorrect claims can be harsh, in some cases as much as 100% of the tax lost, it can sometimes seem like a gauntlet. To remove such risk, an R&D Tax Credit advisor with technical expertise in a vast range of sectors to truly understand the detailed processes is vital. A reputable R&D Tax Credit advisory firm should be able to evidence of expert knowledge of the legislation, technical expertise across a wide range of sectors, proven methodologies and robust processes, comprehensive systems that ensure the security of your data and links to HMRC and insight into legislative changes. They should have a 100% success rate in claims submitted, ethical standards and credibility, previous clients as references and, lastly, should be completely transparent in their fee structure. At Momentum we welcome a higher level of scrutiny as our approach has always been to apply the highest professional standards to every claim we prepare, resulting in a 100% success rate across more ethan 800 claims with over £125m R&D tax relief approved. When it comes to navigating the complexities of the R&D Tax Credit scheme, there are none better.