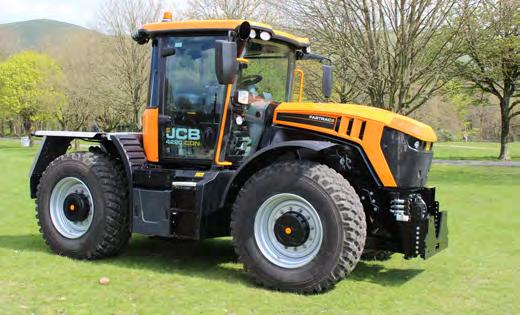
10 minute read
Bobcat Mini Tracked Loaders
Bobcat Launches New MT100 Mini Track Loader
Bobcat has launched the new MT100 mini track loader, removing the need for manual labour, and replacing the use of wheelbarrows, shovels and hand tools in many applications in construction, demolition, rental, landscaping, agriculture and other industries.
With a standard width of just 904 mm (increasing to 1045 mm with the Wide Track Option providing increased stability and lower ground pressure), the reduced dimensions of the new MT100 provide easy passage through narrow gates and doorways and facilitate work in confined spaces. The integrated ride-on platform of the MT100 gives the user a wider view to the sides of the machine as well as the bucket cutting edge or attachment. Combined with the track system, the ride-on platform on the MT100 provides a smooth ride for enhanced operator comfort and confidence. The ISO joystick controls on the MT100 are ergonomically designed and provide finely tuned precision – so controlling the machine is safe, easy and comfortable. John Chattaway, Loaders Product Manager at Bobcat, commented: “With the MT100 mini track loader, users can travel and work in the tightest spaces where other machines cannot. The MT100 should not be underestimated - it does serious work: from cleaning up under conveyors at quarries and waste sites to digging, trenching, tilling and moving materials and more on construction and demolition sites. The MT100 also offers the attachment versatility of larger Bobcat compact loaders.”
Outstanding Specifications
Despite its compact size, the MT100 mini track loader still delivers a rated operating capacity of 460 kg, a tipping load of 1314 kg, a powerful breakout force and a lift height of 2057 mm. The moveable counterweights (CWs) system adds even more capability and allows the user to tailor the lift capacity or ground engagement depending on the application. As standard, the counterweights sit in the front undercarriage to provide optimal ground engagement. Moving them to the rear uprights increases lift capacity to 485 kg and the tipping load to 1387 kg when needed. The Stage V, 25 HP engine on the MT100 works efficiently to drive the work equipment. The track drive and powerful 41 l/min auxiliary hydraulics ensure the MT100 can be used for multi-function work, carried out using the many different attachments available. In fact, whether constructing, demolishing or landscaping, the MT100 shares many of the same attachments found on the company’s smaller loaders using the same standard Bob-Tach attachment system. There is also a common industry interface available for hooking up to other equipment that customers may have in their fleets.
Tracks Help
The tracks on the MT100 allow travel over established surfaces, with less worry about repairs and costs associated with surface damage. With a ground pressure of 36 kPa (5.25 psi), the standard 180 mm narrow tracks provide good protection for most turf and finished surfaces. The optional 250 mm wide tracks further reduce the ground pressure to 30 kPa (3.97 psi). The MT100 also has a class-leading ground clearance of 205 mm, that makes working over and around obstacles safer and easier for demolition and landscaping tasks.
New JCB Fastrac iCON ‘Utility’ Has Even Greater Capabilities
JCB has launched a new ‘utility’ version of the Fastrac 4000 series highspeed tractor with all-new electronics that deliver higher levels of performance and convenience while giving operators unprecedented choice in the way they set-up and control their machine.
All Fastrac tractors are unique in being equipped with powerful external disc brakes and selflevelling axle suspension at front and rear. The 175hp to 235hp 4000 Series models, which are available to ‘utility’ specification for highways, airport and other applications, also feature multimode four-wheel steering. The new iCON models have more advanced control software for the stepless transmission, making it easier than ever to operate the tractors in work and when travelling at up to 60kph on the road, while the fully-integrated ISOBUS implement control option adds new capabilities. Inside the cab, the iCON armrest console and touch-screen display provide outstanding flexibility in control allocation and operator information, while further improving the operator’s all-round view from the two-seat Command Plus cab, which has improved heating and ventilation. The ‘utility’ version can be equipped for winter and summer maintenance tasks, operating rear-mounted, front-mounted and deck-mounted equipment – individually or in combination – for applications such as snow clearance, salt spreading and roadside vegetation control. Features include a DIN-standard mounting frame for highway snow ploughs, snow blowers and powered sweepers; a stability control system to keep the tractor level when operating heavy long-reach vegetation mowers; and a purpose-built rear deck frame for quick mounting and demounting of specialist spraying equipment and salt spreaders. The rear deck is fabricated with a steel frame and aluminium chequer plate covering, with built-in mud guards formed from stainless steel; operators can quickly remove a sprayer or spreader by lowering the tractor’s suspension after deploying support legs and disconnecting quick-release mounts and electrical and hydraulic couplings. As standard, the tractors are finished in high-visibility orange rather than traditional JCB yellow, and are available with block pattern tyres for routine use on tarmac, concrete and other hard surfaces, as well as the familiar agricultural pattern for maximum off-road traction. At the heart of the Fastrac iCON models is a new electronics infrastructure that enables a host of modern technology features to be fully integrated as standard or optional equipment. The seat-mounted armrest console carries a 12in colour touch-screen display providing comprehensive vehicle information and the facility to set-up systems such as front and rear equipment hitches and the tractor’s hydraulics, as well as ISOBUS-compatible equipment. Flexible allocation of hydraulic functions to the new main joystick and its five buttons, proportional spool valve fingertip levers, and an optional auxiliary joystick means controls can be set-up (and saved for recall) according to the type of equipment being operated and individual operator preferences. The 12in touch-screen display, meanwhile, provides access for drag-and-drop spool valve and tractor control allocation, vehicle information, remote camera view (connectors are at the front, rear and side of the tractor), and ISOBUS applications. Using the Fastrac’s stepless transmission has been made easier with Smart Transmission Control, which allows the operator to set a ground speed and leave the tractor to decide the best combination of engine speed and transmission ratio for changing loads both on- and off-road.
news
Rokbak & one of the world’s fittest women join forces again!
Like the haulers she appeared alongside a year ago to highlight their power, strength and reliability, Ali Crawford only gets better. Fresh from being crowned the world’s fittest woman over 45, she recently returned to Motherwell to put an RA40 through its paces and help celebrate the brand’s first anniversary.
In the latest video – which is live on Facebook, Instagram, Twitter and LinkedIn – she talks about her experience filming the brand video and how she has more in common with Rokbak and its machines than you might think! Initially chosen to reflect the tough, powerful characteristics and values she shares with the Rokbak brand, Ali has gone on to enjoy even greater success over the past year, officially becoming the World Number One in her age category after an exceptional performance at the CrossFit Games in Madison, Wisconsin, USA. “Even though I’m in my forties now, I feel like I’m getting stronger and fitter every year, rather than older,” says Ali. “So, I can definitely relate to another Scottish champion that is in better shape than ever after 80 years of continual improvement and hard work! These impressive machines and what they stand for, how robust and reliable they are, really align with me as a person – I feel like the human version of an RA40!” Despite living relatively close to the Rokbak factory, Ali had no previous experience with articulated haulers, so found the first video shoot an extremely enjoyable and eye-opening experience. “I hadn’t known what to expect but it turned out to be so much fun,” she grins. “I had a brilliant time, doing various fitness exercises around the machines to help illustrate their qualities was amazing.
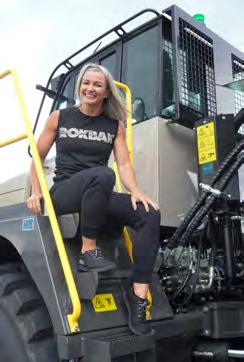
Ali Crawford.
Women in Construction Suffer ‘Praise Penalty’
As over two-thirds of female employees feel they deserve more recognition, how can construction companies do more to meet female employees’ recognition needs?
According to a recent study, female employees are suffering from a ‘praise penalty’ at work. Female employees are 34% more likely than their male counterparts to experience mental health issues, such as stress or burnout, due to not having their efforts at work sufficiently acknowledged. Some 71% of female workers feel underappreciated. The Employee Recognition Survey – conducted by virtual team building and virtual escape room specialists Wildgoose – surveyed employees from 133 different UK companies. It asked them whether they receive enough praise and appreciation in the workplace, how they would react to a lack of recognition and how companies could better meet their ‘recognition needs’. Around 13% of UK construction employees are female according to the ONS. Despite this imbalance, societal pushes to address it are gradually taking effect – Randstad research found there was a 9% increase in the number of women entering construction management roles between 2018 and 2021. Plus, this year construction firms and major-project clients like HS2 have pledged to work with non-profit advocacy group Women in Construction to accelerate an improved gender balance in the sector. However, employers must focus on retention as much as recruitment, with almost half (47%) of construction workers citing the male-dominated culture as a reason why so many women leave the industry. For the female employees already in the construction sector and with a new wave of female talent entering, it’s vital for companies to ensure their approach to employee recognition includes all members of the workforce. As well as affecting employee mental wellbeing, failing to recognise and value employees can also negatively impact the company itself. Over the last year, 42% of underappreciated female employees said their productivity has dropped, while 38% said they’ve lost faith in the management team and the company’s core goals.
Respect & Feedback
What form of recognition do female employees want?
Data from the Employee Recognition Survey emphasises the importance of regular meetings and one-to-one time for female employees: 57% want private recognition through regular, in-person meetings with their managers. 54% would like respect from colleagues, alongside regular feedback. Female employees value these things more than receiving a higher salary than the industry standard – which was cited by 43% of female respondents. Public recognition from above also counts for a lot: around a third (32%) of women have a preference for regular public appreciation or shoutouts from management. Commenting on the findings, Wildgoose managing director Jonny Edser said: “Everyone wants to feel valued and appreciated for the work they do, so recognition really is a basic need at work. And with more employees now working away from the office, companies have to take a step back and make sure remote employees feel equally recognised. “It’s clear that many UK companies aren’t providing their employees with enough recognition – and firms should realise that can affect their bottom lines. When organisations fulfil the ‘recognition needs’ of their workforce, the result is motivated, engaged employees, who are less likely to be off through poor mental health. “Here at Wildgoose, we offer a mix of in-person, hybrid and virtual events to help boost team morale and encourage relationships between colleagues and managers. Time and again, clients tell us that it really works.” Kasia Richter, founder at the Wellbeing Strategist, said: “Praise is a form of recognition and acknowledgement, which is a basic human need. We all want to be seen, heard and witnessed. Some of us are more sensitive and have a greater need to be praised than others. If a person strongly identifies himself/ herself with the job, it becomes even more important to acknowledge them, their efforts and their achievements. “Recognition of employees is one of the most powerful ways to motivate them and improve the quality of their work, as well as making them loyal. And allowing employees to be heard and feel supported can go a long way to showing employees they’re valued. “It can be achieved by creating a culture of open communication, transparency and fairness. Communicating requirements, providing support when necessary, encouraging self-discipline and self-mastery: all this will strengthen your workforce and keep employees feeling valued.”