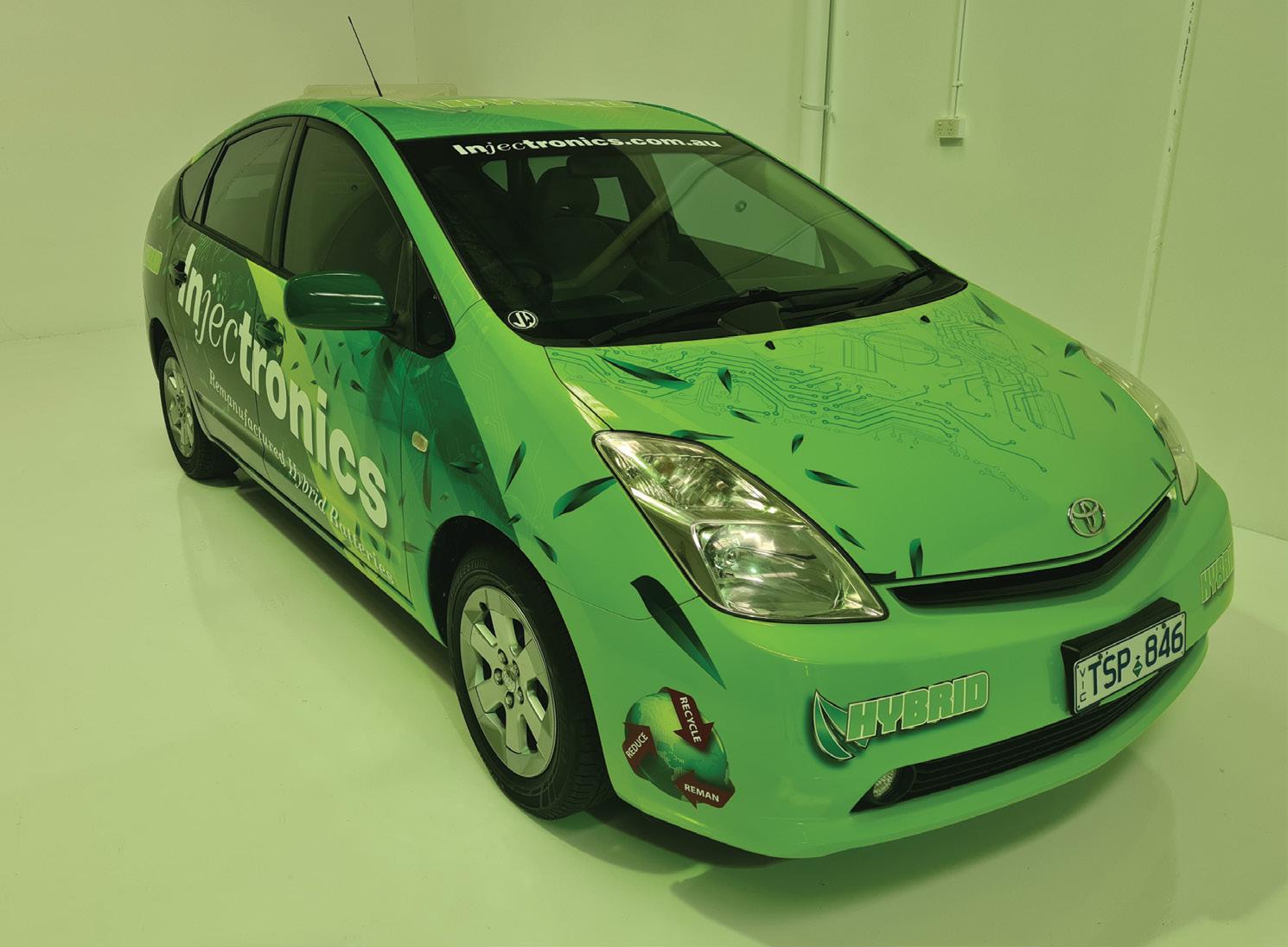
27 minute read
EV & Alternative Fuels: Powering into the future
POWERING INTO THE FUTURE
IM Group General Manager of of Circular Hybrid and Electric Vehicle Power Solutions, Dickson Leow, takes a look at the current EV landscape
A recent article about the cessation of the Prius model from the Australian market signifies some maturity of the electrification of models in Australia, although Australia still lacks behind many regions around the world in the adoption of EVs. The Prius nameplate was synonymous with technology and electrification, and after 15 years, each Toyota model line has a hybrid drivetrain and more electrification of the powertrain from the likes of Tesla, Honda, Kia, Hyundai, and many new technology-turn car makers are on this electrification journey. It is, however, more than just a transition to a new battery-derived drive train and more about how we transition towards sustainable electrification, where our next generations have a sustainable future. A better tomorrow
Although the uptake of EVs and derivatives such as plug-in hybrid electric vehicles (PHEV) and HEV has been slow in Australia, their numbers are increasing rapidly each year. With such an increase and expansion in the uptake of these alternative fueled vehicles, state and local governments must consider the ways these vehicles will impact road operations and the potential opportunity of harnessed energy it creates – especially with the growing availability of models and because of the potential for reduced operating costs, oil displacement and some environmental benefits. The primary value of EVs (and their derivatives) is the reduced fuel costs by substituting some petrol with electricity, but this benefit is offset by higher purchase costs (in comparison to the ICE variant, largely due to the cost of batteries). According to the Australian Bureau of Statistics (ABS), as of 2019, there were 19.5 million registered vehicles on Australian roads, with an average age of 10.2 years. According to VFACTS, an average of about one million vehicles are sold, of which Zero Emission Vehicles (ZEVs) – account for less than one per cent. There are many reasons attributed to the low uptake rate in Australia including vehicle price, model availability, access to charging infrastructure, charging time, incentives, service support and education. However, as mentioned sales are encouraging over the past three years. Many manufacturers are waking up to the trend and allocating an alternative fueled vehicle to the mix in their model line-up. You can now purchase an EV across many car brands, including Hyundai, MG and Mercedes Benz. In a March 2020 article by Infrastructure Magazine, the Chief Technology Leader and National Leader, Future Transport Systems at NTRO, said, “By supporting the transition to EVs and ZEVs, road operators can help shape how charging infrastructure is modelled – as opposed to random third party install – what incentives could be considered to generate greater uptake, and how road design, planning, maintenance, build and implementation could be influenced.” This article also stated the benefits of supporting the transition, including: • Life-saving technology and contribution to
‘Towards Zero’ • Fewer GHG emissions than fossil fuel-powered vehicles • Reduced energy consumption by returning energy to the grid • Reduced dependence on the importation of fossil fuels • Possible creation of tens of thousands of jobs

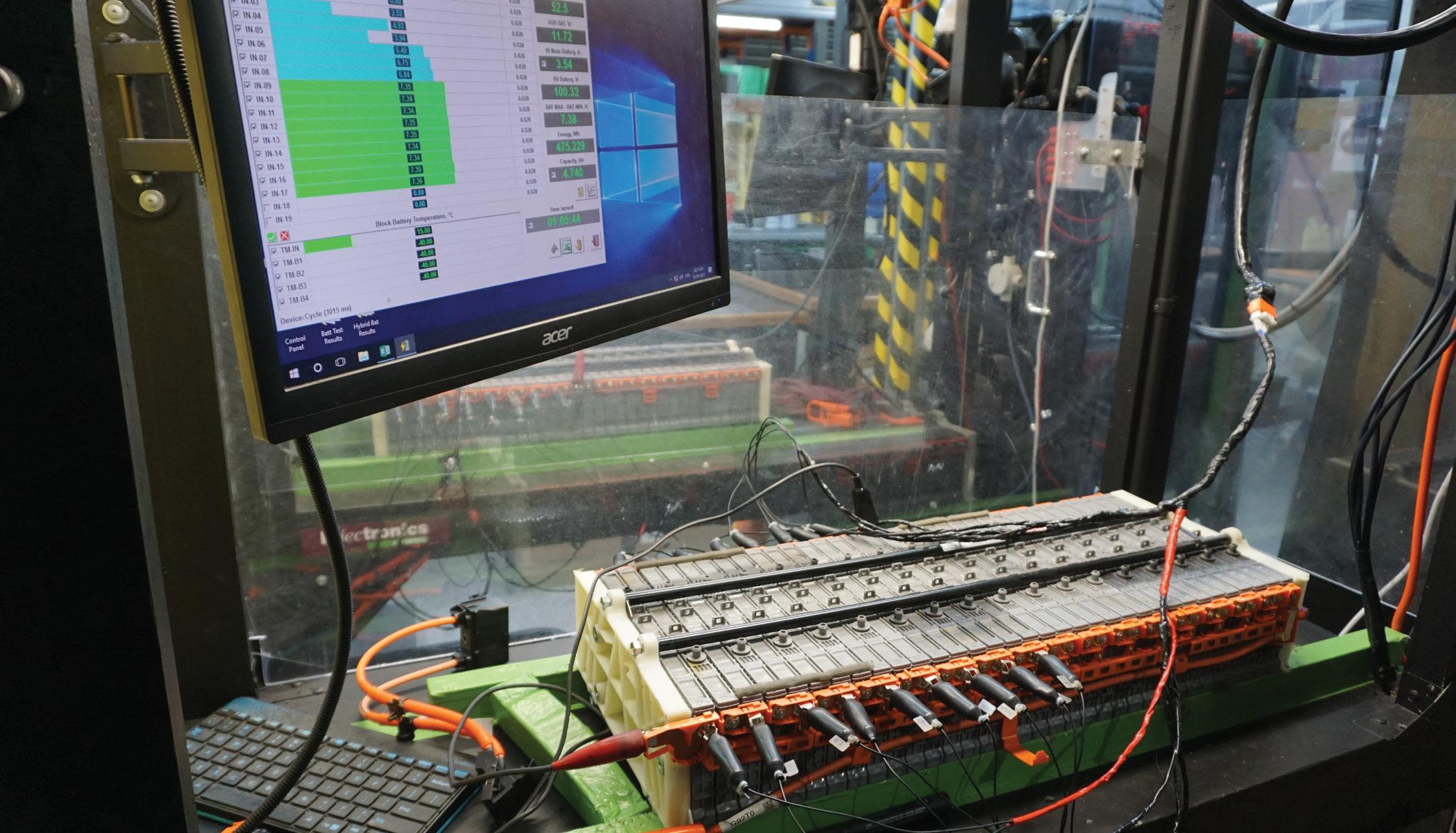
Another benefit of battery-powered vehicles is the potential of data sharing with insights to many sensors monitoring the road surfaces or vehicle movements. Also, the information on origin and destination information could be collected to better plan road network loading and peak periods of charging. This is due to the charging of EVs and PHEVs, where there is an indirect impact on the operational requirements of the energy utility company as the load may trip a blackout over-loading scenario. The information will allow for better optimisation of energy required and production. The new labour force
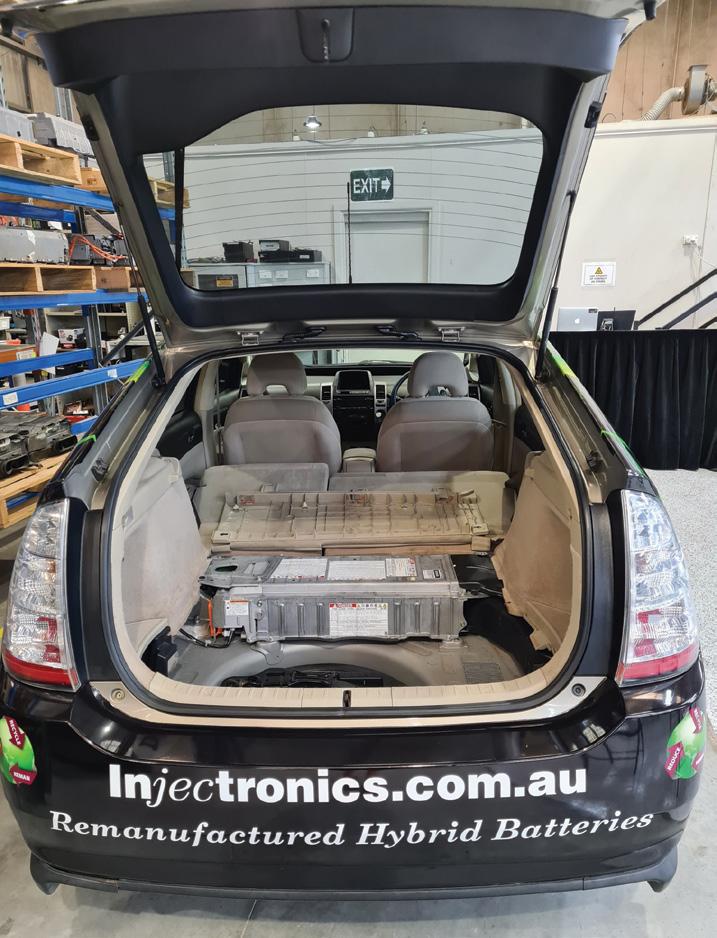
Over the next decade, the required knowledge and skill sets of existing manufacturers and suppliers will need to shift dramatically due to several variables and factors driving this. As vehicles get “smarter” and communicate with each other and infrastructure, the software and connected sensors become critical, and the needs of these digital talents are essential. Research suggests there are shortages of employees across the industry supply chain as we transition from mechanical components to electronic and electrical circuitries. However, wireless “over-the-air” updates to diagnose faults could be the norm rather than having to book your vehicle in for a mechanic to check your faults. As the chemistry of the vehicle changes, the automotive workforce will also follow suit. A new kind of “mechanics” and “technicians” are needed to complement the future vehicle labour force – essentially transitioning how an auto mechanic trains to become a data analyst to determine why a vehicle is discharging energy abnormally or investigating how the cooling system is ineffective and triggering the battery management system to display a fault code. There are, however, many similarities between EVs and ICE vehicles. The service process and moving parts, although they can be different, are still necessary, such as suspension, brakes, electronics and interior components, lighting and wiring, steering, and transmission servicing to name a few. EV is a small part of the smart mobility movement
A smart mobility society focuses on total solutions for sustainable mobility without impact on the environment and this includes the various powertrains such as EVs, PHEVs, Hybrids and even Hydrogen Fuel Cell vehicles. The EV aftermarket offers a stepping-stone into the broader world of smart mobility. Of interest is the use of the EV batteries once they are no longer suitable for powering vehicles, but adequately amped for stationary energy use, like as a Battery Energy Storage System (BESS). It has been suggested that stationery and transportation energy storage combined markets are estimated to grow between 2.5 to 4 terawatthours (TWh) annually, approximately three to five times the current 800-gigawatt-hour (GWh) market. This rapid transition toward transport electrification and decreasing battery storage costs triggered an increase in research and market deployments of BESS to ensure the readiness of the sector for electrification. IM Group at its Hallam facility is conducting such a pilot of BESS to store and manage energy in collaboration with Sustainability Victoria and its technology partner. The findings will be released later this year and IM Group says the results will be of interest to the automotive industry. For more from IM Group, visit www.im-group.com.au
A WIDE RANGE OF EV SPARE PARTS
ZF offers a broad spare parts portfolio for electric vehicles
Public perception of electric vehicles can often focus on the electric drivetrain, which is considered quite reliable, requiring little maintenance. The brakes and chassis systems of these cars, however, can be more susceptible to damage and wear than conventional vehicles due to the stresses exerted by the extra weight of the battery. ZF Aftermarket supports automotive workshops working on electric vehicles with an extensive range of spare parts under its Lemförder, Sachs and TRW brands. Chassis and brake noises are more annoying in e-cars
A common question to workshops around electric vehicles is how great is the need for maintenance and repair? After all, the energy storage and drive technology of practically all e-cars have so far proven to be extremely durable and lowmaintenance. ZF explains that due to the high mass of the traction battery being 300 to 500 kilograms heavier than conventional vehicles of comparable size, significantly more strain can be put on springs, dampers and support joints. The high torque of the electric motors also puts greater stress on the chassis parts and increases tyre wear. Workshops should therefore take a close look at the chassis of these vehicles. And the brakes? Here, too little load is more likely to cause problems. Because these vehicles decelerate electrically in many driving situations, the service brakes are hardly used which can result in the brake discs corroding and the pads glazing over. As electric cars are very quiet, owners quickly notice any rattling suspensions or grinding brakes which can limit driving comfort much more than with petrol or diesel cars, because the engine typically drowns out these noises. Low-noise brake pads for electric cars
With an extensive range of spare parts from its Lemförder (steering and suspension components), Sachs (shock absorbers) and TRW (brakes) brands, ZF Aftermarket says it supports automotive operations in many chassis repair cases. The range extends from the Nissan Leaf to the Tesla S and X models. A special brake disc for the Tesla Model S is available under the TRW brand and the low-noise brake pad branded TRW Electric Blue is suitable for practically all electric cars in the local market. ZF Aftermarket is set to expand its portfolio for electric cars even further with suspension and steering components for the VW ID.4, ID.3 and Skoda Enyaq models, which are projected to be released in 2022. ZF is also an original equipment supplier for the Volkswagen electric models. For further information on ZF in Oceania, please visit www.zf.com/au or call 1800 ZF SALES (1800 93 72537).
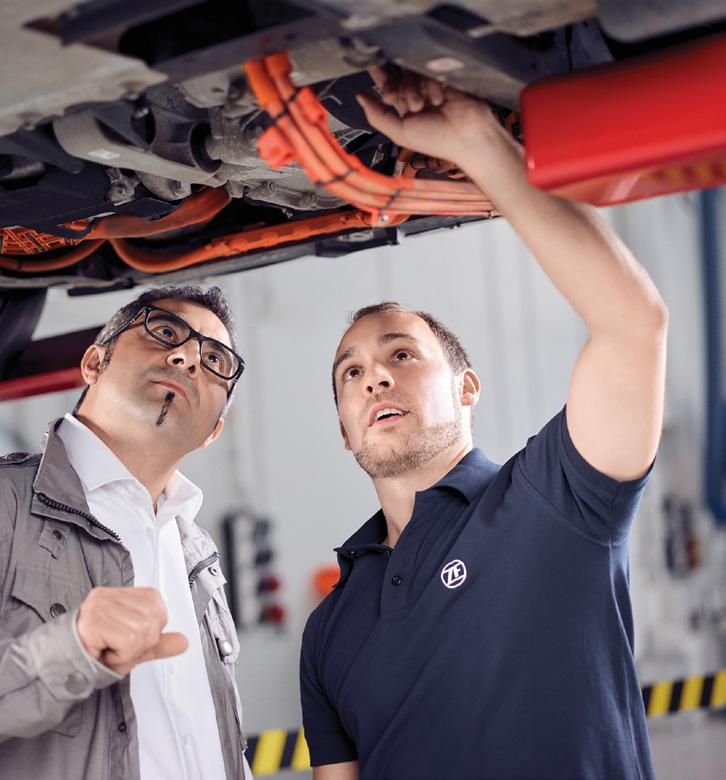
HYBRID AND ELECTRIC VEHICLE REPAIR TRAINING
The MTA Institute says it is leading the way in this important training area
The MTA Institute (RTO.31529) says it is proud of the leading role it continues to play in delivering crucial knowledge and upskilling opportunities in the evolving area of hybrid and electric vehicle repairs, servicing, and maintenance to the Australian automotive industry. MTA Institute states it is the leading independent provider of automotive training and apprenticeships in Queensland. It commenced delivering dedicated hybrid electric vehicle (HEV) and battery electric vehicle (BEV) technology training in 2018 through the accredited AURSS00035 – Battery Electric Vehicle Inspection and Servicing Skill Set (now superseded and equivalent to the AURSS00064 – Battery Electric Vehicle Inspection and Servicing Skill Set) and AURSS00037 – Hybrid Electric Vehicle Inspection and Servicing Skill Set course. The innovative MTA Institute was one of the first Registered Training Organisations in the country to offer accredited training in the area and has trained hundreds of technicians over the last four years, attracting mechanics from across the country and the world. As HEVs and BEVs continue to increase in popularity among local car buyers, training that delivers the required skills and knowledge to correctly service and repair the vehicles has never been more sought after. It is now imperative that all workshops ensure their workforce is upskilled and prepared for the influx of vehicles expected to come in for repairs and maintenance in the coming years. A key component of the three-day course offered by the MTA Institute is the completion of AURETH101 – Depower and reinitalise battery electric vehicles. This unit of competency has been identified as a prerequisite for automotive technicians to access safety information under the new Motor Vehicle Service and Repair Information Sharing Scheme which commenced on the 1st of July, 2022. “We take great pride in delivering industry leading training that directly improves the skills of technicians in the automotive sector,” MTA Institute General Manager, Paul Kulpa, said. “Our training delivers critical knowledge at a time where electric vehicle technology is increasing on the workshop floor. “Understanding this technology is complicated and dangerous, it is not something you can learn solely on the job, so it is vital for automotive professionals to complete the accredited training prior to attempting to inspect or service a hybrid or electric vehicle. “And now with the introduction of legal requirements to access safety service and repair information in Australia, workshops must upskill their employees now to ensure they can access hybrid and electric vehicle data and work on those vehicles.” The AURSS00064 – Battery Electric Vehicle Inspection and Servicing Skill Set and AURSS00037 – Hybrid Electric Vehicle Inspection and Servicing Skill Set course is regularly scheduled throughout the year, with places in hot demand. For more information, visit www.mtai.edu.au
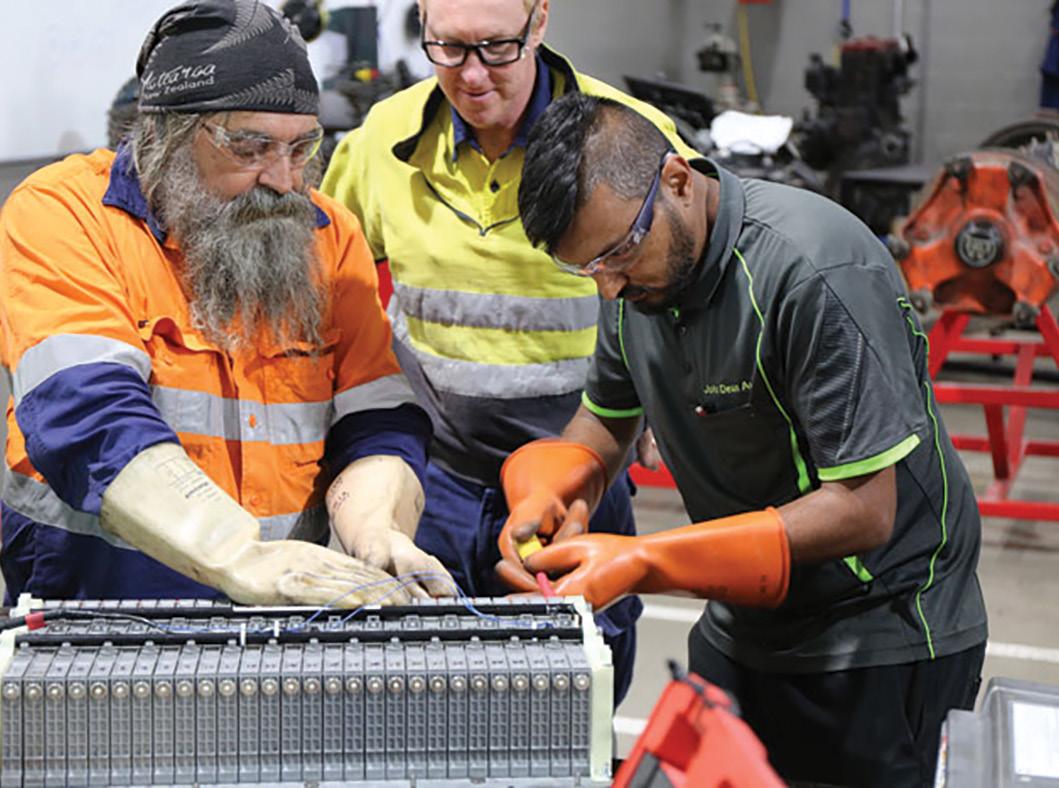
ANSWERING THE CALL FOR TESLA PARTS
ASV Euro Car Parts is working hard to meet demand
The market for electric vehicles is ever-growing and evolving. On the back of the recent news that the ACT government is set to ban sales of petrol and diesel cars by 2035, and rising fuel costs, market demand is only set to increase. With this increase of EVs and in particular Teslas on the roads, so too does the demand for quality aftermarket options, especially for commonly replaced parts such as steering and suspension. In 2020, ASV Euro Car Parts’ executive team made a decision to diversify the company’s current offering and expanded from being a one stop shop for European cars to introduce the Tesla brand to the suite of vehicles they source and supply quality parts for. ASV explains that it has long term, established relationships with most of the mechanics and smash repairers who are now Tesla approved and trained, stating they knew the customer demand was increasing. But ultimately, ASV says it decided to start dismantling and working with Tesla because they first and foremost represent the same qualities as European cars. “It is undeniable that the world is moving towards electric vehicles. Volvo, Volkswagen, Mercedes, Porsche are all heading in this direction,” ASV Euro Car Parts Chief Executive Officer, Vic Soghomonian, said. “Tesla just happens to be leading the way and as we are industry leaders too, we want to be on the front foot of the EV revolution and have the stock and solutions for our customers. “Genuine Tesla parts are hard to come by. ASV is currently dismantling and selling pre-used parts from a number of ELV Tesla’s each month, however, there is demand for new parts as well which is why we have sourced aftermarket Tesla parts to offer cost effective options and alternative solutions to the dealership network. “With our expert product and purchasing team and quality assurance processes, we have secured quality aftermarket brands to supply Tesla parts including Brembo, ASV Airbags and OSSCA.” Testament to this quality, ASV says it is offering a two year guarantee on these brands and parts. ASV currently has in stock a large range of new control and suspension arms from OSSCA which all come with a two-year guarantee, as well as brakes from Brembo Brakes. It also has shock absorbers with a two-year or 60,000km warranty from its own ASV Airbags brand which are suitable for Tesla. As the largest seller of new and used European parts, ASV says it has the delivery network and stock available to provide customers with competitively priced, quality Tesla aftermarket parts with an express delivery service Australia-wide. For more information, visit www.asv.com.au
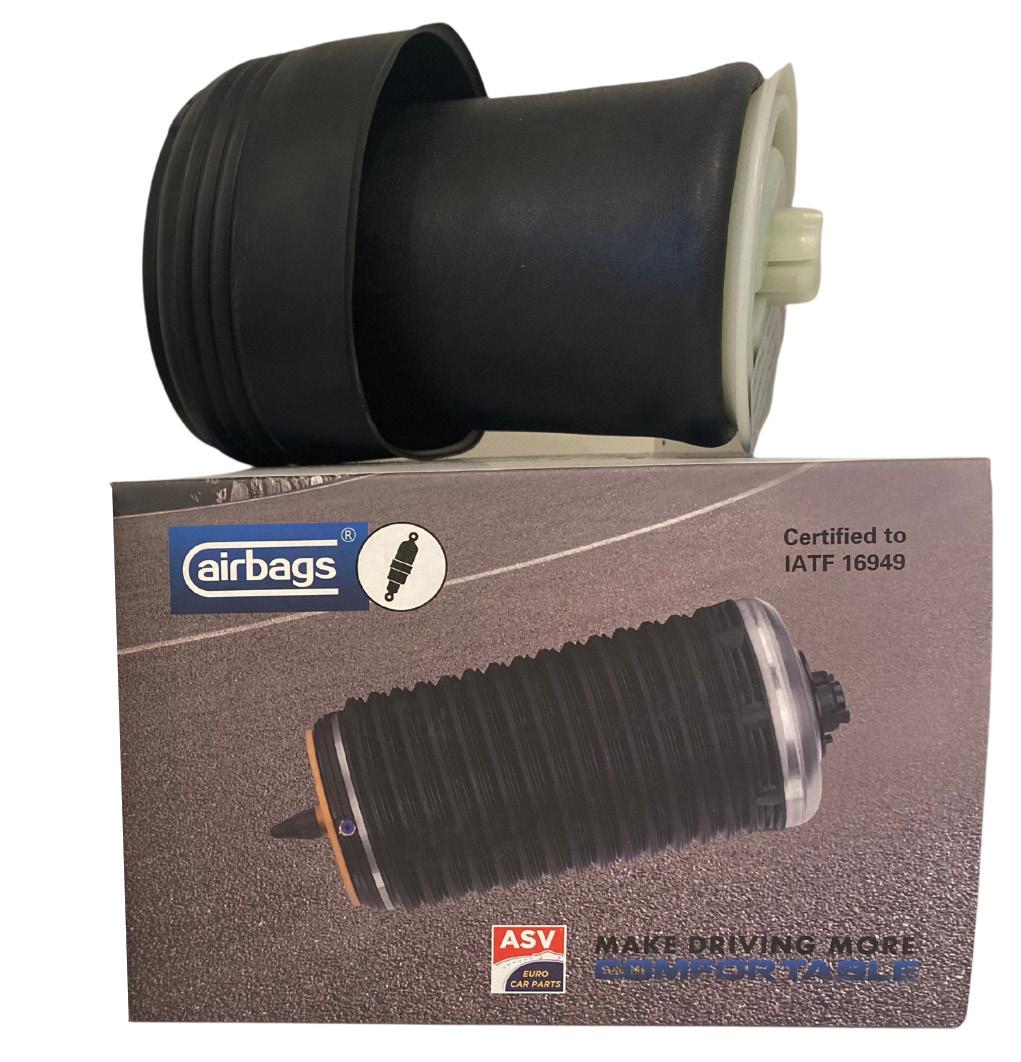
A LOOK AT THE CURRENT EV CHARGING LANDSCAPE
With a recent report, Savvy looked into the current state of EV charging infrastructure and what is planned for the future
With EV sales making up a small 1.6 percent of all new vehicle registrations in 2021, one of the most cited reasons that people are reluctant to take up electric vehicles is a lack of charging infrastructure. A research report by online broker Savvy utilising March 2022 data from the Electric Vehicle Council of Australia sought to answer questions such as, how many public charging stations are there in Australia? How many are planned for the future? Where are they now, and where will they be located? How many public charging stations are there in Australia?
Note that the number of public charging locations does not reflect the number of individual charging points. There may be many points at one location. • Fast charging – as of January 2022, there are 293 fast charging locations around Australia.
This represents an increase of 85 percent since August 2020 (157). Unsurprisingly, the distribution of these stations matches the population density of each respective state. • Regular charging – as of January 2022, there are 1,580 regular charging stations in
Australia. This represents an increase of 29 percent since August 2020 (1219) This also matches population density, though WA with 202 is an outlier. Finding charging stations

The EV community has pitched in to help fellow drivers by providing a free cross-platform app called PlugShare. PlugShare allows users to find charging stations in Australia and worldwide, map new ones and share their EV activity with other enthusiasts. Google has already rolled out an EV charging station finder in the United Kingdom and United States, with countries such as Australia and New Zealand to follow. The future of charging
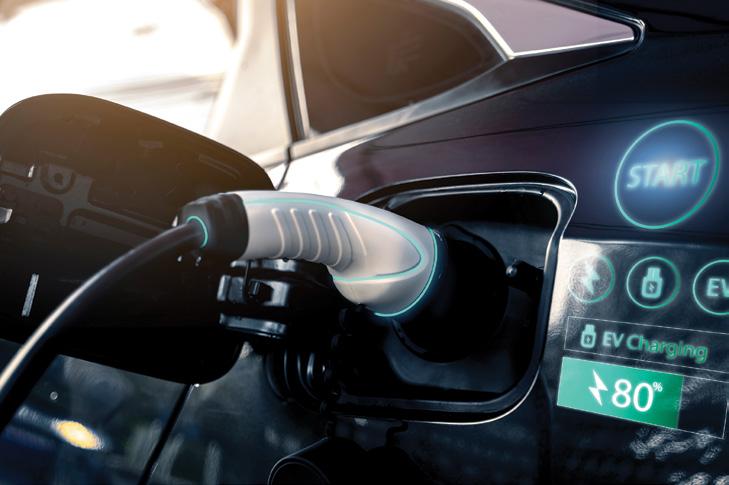
State and federal governments are supporting the rollout of additional fast charging stations around Australia. The Electric Vehicle Council, based on estimates of funding from state and federal governments, says that 700 new fast charging locations will be added across Australia over the next five years. Each location will have multiple charging points to accommodate many vehicles. Other state government programs will increase the density of fast charging equipment currently in use, so more cars can take advantage of charging at the same time. To learn more by viewing the full survey report, visit www.savvy.com.au
BENDIX EV-HYBRID DISC BRAKE PADS
Sustainability is at the heart of these brake pads, says Bendix
As well as being locally designed at Bendix’s Ballarat R&D facility to suit the needs of EV and hybrid electric braking systems, Bendix says it has applied broader sustainability goals around its entire EV-Hybrid Disc Brake program. The disc brake pads feature copper-free, organic brake friction material that sees them certified to the Automotive Aftermarket Suppliers Association (AASA) ‘N’ rating. This measure confirms the pads contain less than 0.5 of copper by weight, allowing Bendix to use the AASA LeafMark ‘N’ icon. The organic friction material used in the EV-Hybrid disc brake pads comprise of a range of ingredients including synthetic glass fibres, aramid fibres and natural organic fibres as the main reinforcing elements. Added to these are organic modifiers and binding resins. Together Bendix says they deliver strong stopping power, and low noise and dust emissions while providing a low environmental impact. Users of Bendix EV-Hybrid Disc Brake pads will also notice that the packaging is different – the brake pads are not shrink-wrapped – there’s no sign of plastic whatsoever. Instead, the pads are cocooned in a material called Hexcel Wrap. While protecting and cushioning the brake pads in a similar way to plastic shrink wrap and bubble wrap, Hexcel Wrap is a paper product that is 100 percent recyclable. Complementing the Hexcel Wrap is exterior packaging which is FSC Certified – this means that 70 percent of the packaging comes from FSC certified or recycled materials, while 30 percent is made from controlled wood. Once the Bendix EV-Hybrid Disc Brake Pads are fitted, all packaging can be disposed of in kerbside recycling. When the brake pads themselves ultimately need replacing, they can be recycled in the workshop’s metal recycling bin, making Bendix EV-Hybrid Disc Brake Pads a completely recyclable product. Bendix says its EV-Hybrid disc brake pads are the smarter environmentally sensitive choice, and are available for popular EV and Hybrid brands including Toyota, Lexus, Honda and Mitsubishi, with additional coverage coming soon. For more information free call the Bendix Brake Advice Centre on 1800 819 666 or +61 3 5327 0211 from overseas (8am-5pm Monday to Friday EST), e-mail brakeadvicecentre@bendix.com.au or visit www.bendix.com.au
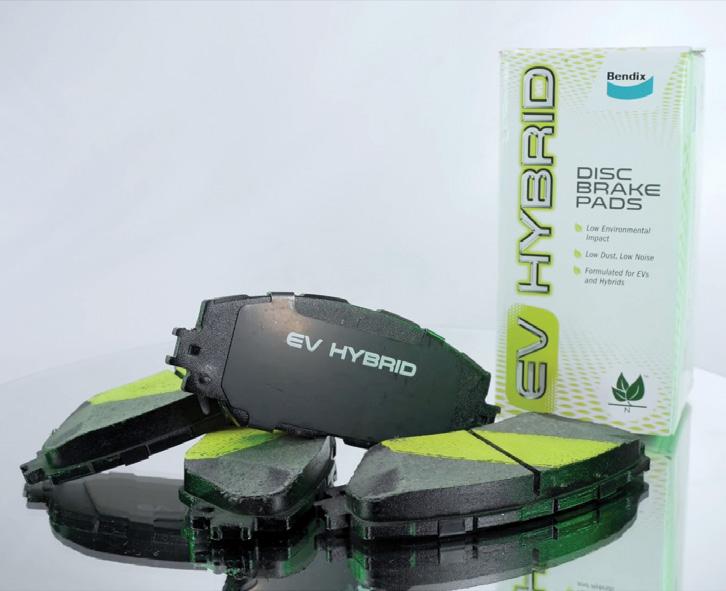
PROFESSIONAL DIAGNOSTICS FOR ELECTRIC VEHICLES
Bosch has the answer for diagnostics and ups the ante on training
FSA 050
Workshop customers have high standards. So, if a vehicle has a problem, diagnosing the fault needs to be quick, thorough and affordable. With vehicle systems and components becoming ever more complex and diverse, Bosch says workshops are best equipped to conduct quick and efficient repair and maintenance on customer vehicles with its products. Bosch says reliable analysis and diagnostics save unnecessary work on a vehicle, which can save both time and money; and workshops can make a lasting impression on new and existing customers while demonstrating their expertise using its modular diagnostics systems. It states the FSA 050 is an important and simple diagnostic module for testing vehicles with electric and hybrid drive. With the ability to work wirelessly, it is capable of performing multimeter functions such as voltage, resistance, capacitance, insulation and continuity tests, with measurements on the high voltage side up to 600 V (CAT IV1) as well as testing insulation resistance up to 200 GOhm at test voltages of 50 to 1,000 V. The FSA 050 can be used in a variety of different ways, either as a device on its own for diagnostics of electric and hybrid vehicles, or as a special accessory for existing PC systems. Thanks to its compact dimensions of 220 x 110 x 65 millimetres (H x W x D) and its weight of just under 600 grams, Bosch says the FSA 050 is suitable for every workshop. Automotive Technical Training
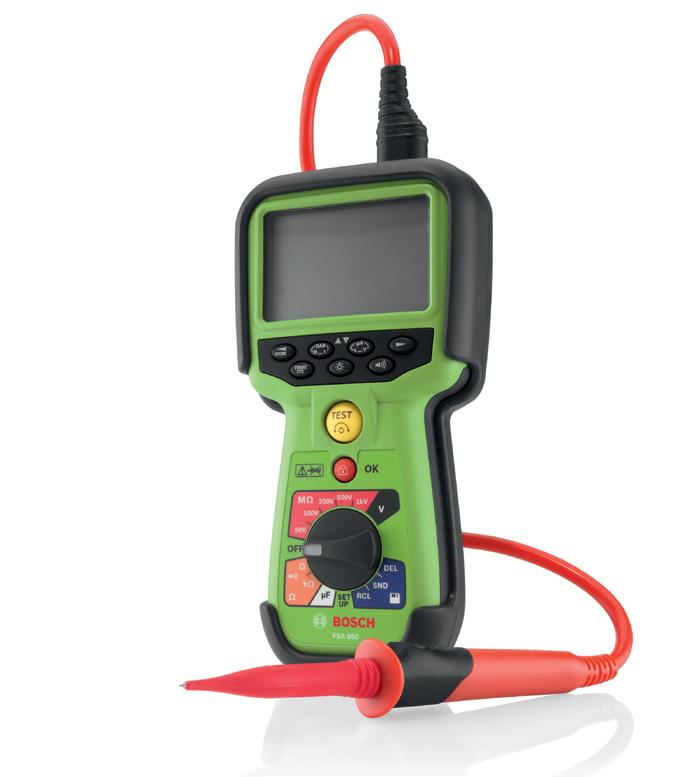
With increasing numbers of hybrid and electric vehicles on our roads, all workshops need to have some understanding of the key components and vehicle architecture and as with any high voltage system, safe servicing procedures are also essential. Bosch says an investment in training adds a competitive edge to any workshop focused on customer satisfaction, productivity and profitability. It states its courses are delivered by highly skilled and experienced educators, who have the knowledge to provide professional training on the latest system innovations, diagnostic procedures and test equipment. Further, having the appropriate training can give you access to the information of vehicle manufacturers’, allowing you to work safety and diagnose efficiently. The new ‘Right to Repair’ legislation which became active on 1 July allows access to the manufacturers’ information, however Hybrid and Electric Vehicle information is excluded to those who have not completed recognised training, such as the ‘Bosch HEV101 – Hybrid and Electric Vehicle Systems’ training. For more information and to enrol, please email automotive.training@au.bosch.com To learn more about Bosch FSA 050, please visit www.boschaftermarket.com.au

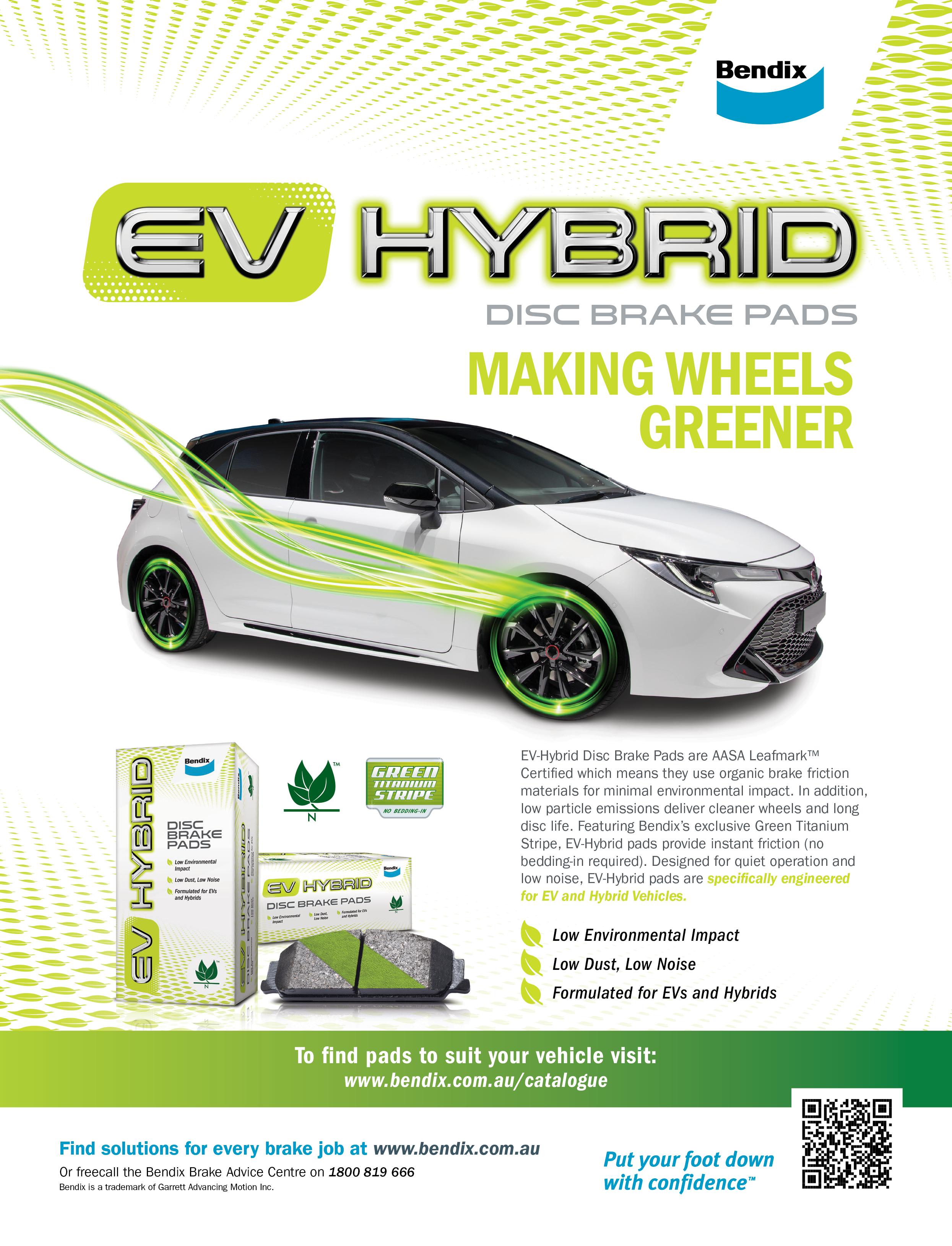
MYCAR READYING FOR EV
mycar Managing Director, Adam Pay, says his business is working around the clock to ready for the coming car parc evolution. “mycar is a people first business, and in order to remain our customer’s preferred servicing partner, we need to anticipate their future needs. That’s why we’ve been pursuing a leadership position in the EV servicing space,” Adam said. “We’re investing heavily in rolling out support services for EV customers across Australia, initially with a select number of stores, and with a goal to scale the service across our network. “From August 2022, we’ll have 30 EV ready stores around Australia. Not only are we shifting the mindset of our business so we can better support early EV adopters, we’re altering our store fit-outs and adding in-store EV chargers, providing personal protective equipment and tools for our technicians, and ensuring new safety requirements and standards are in place to protect both mycar team members and customers. “Through the Kangan Institute’s Automotive Centre of Excellence, we’ve trained a dedicated team of technicians to serve in these locations. The program has been designed to ensure these technicians are ready to service any EV vehicle, no matter the make or model.” mycar EV servicing will be complemented by all 276 mycar stores who are already able to assist EV owners with general requirements such as tyres and general inspections for vehicles, along with brakes, suspension, wipers and globes etc. “The uptake of EVs is an evolution, not a revolution,” Adam said. “There’s going to be petrol and diesel cars on Australian roads for many years to come. Our strategy is about ensuring we deliver the best service to all customers, whatever vehicle they own. “Fixing cars and doing right by our customers is the lifeblood of our business, whether your vehicle is petrol, diesel, hybrid or electric. “As a leader in automotive car care and supporting auto customers, we’ve a big role to play in growing Australia’s EV market and ensuring our customers have a trusted auto expert ready to deliver quality service, regardless of the vehicle they own.” Contrary to popular belief, EVs still have many of the basic serving needs that petrol and dieselpowered vehicles do – such as tyres, brakes, suspension, wipers and so on. “mycar is investing in solutions that enable us to better understand our customers’ needs and the demands of the wider market, EVs are a big part of this shift,” Adam said. “What’s important to an EV owner can be somewhat different to that of a petrol or diesel car owner, but what’s crucial is to understand what your customer wants, regardless of technological disruption. “Knowledge about EVs is the first step to incorporating an effective EV service and repair solution into our existing mycar stores. “It’s crucial to implement tools and programs, train existing and new team members and provide industry information sessions alongside respected industry bodies like the AAAA to build industry understanding of EVs.” For more from mycar, visit www.mycar.com.au
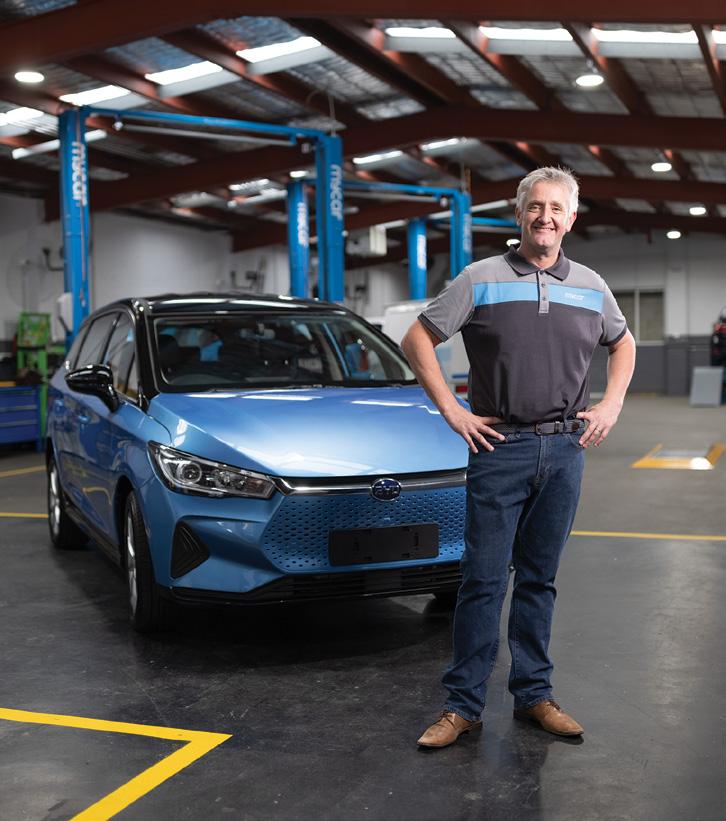
BOSCH IS JOINING THE PUSH FOR A HYDROGEN ECONOMY
Bosch is taking its experience and expertise and making it available to partners and customers
Bosch says it is playing a prominent role in the establishment of a hydrogen economy and actively supporting the move to alternative energy. “On the path to a climate-neutral future, we have to make it possible for energy-intensive industries to shift to renewables. Hydrogen will be a key element in security of supply,” says Rolf Najork, the Bosch management board member responsible for industrial technology and the company’s Manufacturing Technology Chief. Bosch says it can offer the technology needed for hydrogen use in various sectors. The company is developing fuel cells for mobile and stationary applications, equipping hydrogen filling stations with compressors, and producing hydrogen in its own plants. In addition, Bosch plans to enter the electrolyzer components business. “We are getting hydrogen-based technologies out of the laboratory and into industrial practice – onto the roads and into factories,” Rolf said. Through a newly established project unit, Bosch is making its hydrogen expertise available for other companies and recently presented its hydrogen activities at Hannover Messe from May 30 to June 2. In its Industry 4.0 lead plant in Homburg, Germany, Bosch is demonstrating what a hydrogen cycle may look like in the factory of the future. Using renewable energy, an electrolyzer produces green hydrogen. This hydrogen will then be used for manufacturing operations and mobility, with fuel-cell vehicles refueling with the hydrogen that Bosch technology has already compressed. By the end of the decade, Bosch aims to invest up to 500 million euros into the volume production and marketing of the core component of hydrogen electrolysis: the stack. Bosch hopes to launch its smart modules in 2025. For industrial processes, a stationary fuel cell developed by Bosch converts hydrogen into heat and electricity. Energy flows in the plant are controlled in line with demand, using Bosch Industry 4.0 software. The Energy Platform is already being used in more than 120 of the company’s plants. Manufacturing operations account for some 90 percent of Bosch’s global energy consumption. A solution developed by Bosch Rexroth and Maximator Hydrogen for compressing hydrogen for filling stations, storage tanks, and pipelines is also to be trailed at the Homburg plant. For more information, visit www.bosch.com.au
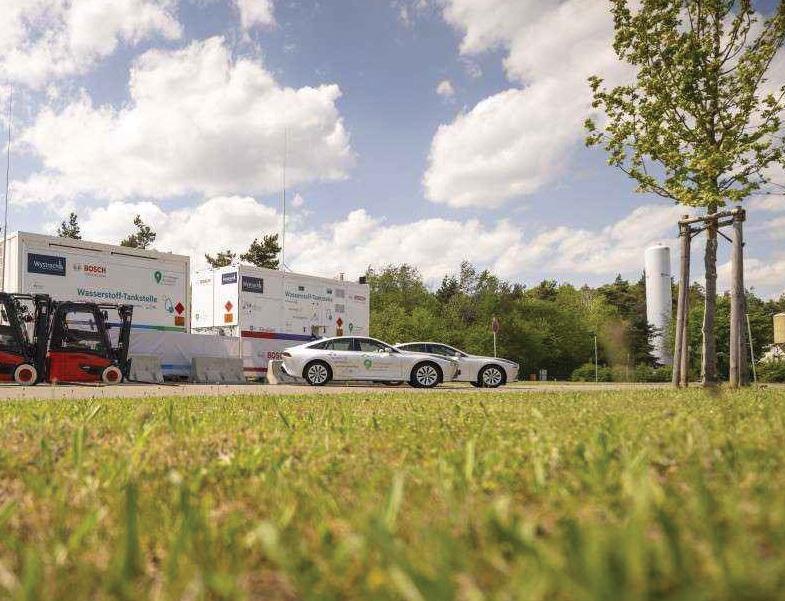
FLEET INSIGHTS AND THE SHIFT TO EV
In this article, ACA Research takes a look at fleet electric vehicle uptake and what it means for Australian workshops
We’ve talked in previous articles about the coming electrification of the Australian car parc, and the impact that will have on servicing and repair businesses. To quickly recap the story so far: 1. We know that the number of electric vehicles will increase substantially over the next decade. 2. If we assume that up to half of the vehicles sold in 2030 could be electric, that means around one million electric vehicles operating in Australia. 3. From a workshop perspective, there are decisions to be made around whether that warrants investment in the certifications, training and equipment needed to service these vehicles, or if it is better to focus on the (much) larger ICE parc instead. When we think about the uptake of electric vehicles in Australia though, it is also important to consider who will be driving that change. In the initial stages, fleets will play a significant role in this journey, also feeding ex-fleet vehicles into the second-hand market. In fact, even when we consider fleets at the smaller end (for example, less than 20 vehicles) some are already trialling EVs, testing how they perform in day-to-day operations. These will however be limited in terms of both numbers and usage, with hybrids playing a much more significant role at this point in time. In fact, from a servicing and maintenance perspective today, it is more important to be equipped to service hybrid vehicles (such as the hybrid Toyota Rav4) than it is to service electric ones.
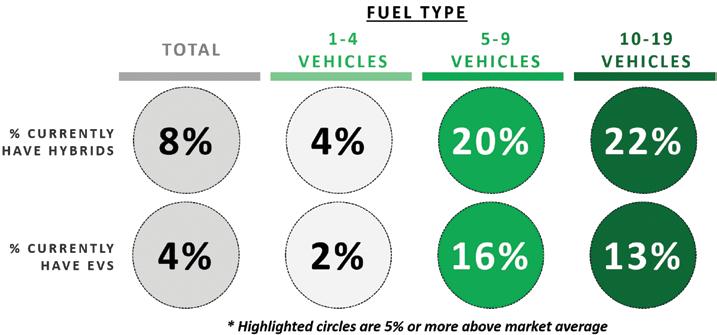
Looking to the future though, this is going to change, with Small Fleets consistently expecting electric vehicles to become a genuine alternative to ICE over the coming decade. While vehicle availability (in terms of total volumes and fit for purpose options) will delay this in the short term, these issues will be overcome with time. Looking at EV servicing requirements, there will be a higher proportion of dealership servicing in the initial phase, but that naturally shifts to the aftermarket as the pool of vehicles increases, and more of them start moving beyond new vehicle warranty periods.
EV BATTERY COOLING
Penrite manufactures a range of OEM approved coolants suitable for electric vehicles
With increased development of batteries in electric and hybrid vehicles, the Automotive OEMs are facing the increased challenges of keeping the batteries cool enough to function at peak performance and charge quickly and safely throughout the vehicle’s life cycle. In the early days of EV and Hybrid vehicles, batteries were air cooled but as the technology advanced and safety standards increased, liquid cooling has become the preferred option for these types of vehicles. In a vehicle with an internal combustion engine, the engine generates heat from the movement of the pistons up and down the cylinders and the actual combustion process itself. This heat is largely wasted energy and dispersed via the vehicle’s exhaust system. The engine oil accounts for a good percentage of cooling and the cooling system maintains the engine at its peak operating temperature. In an electric vehicle the battery can lose efficiency very quicky if it is overheated. This results in range reduction, longer charge times and reduced life cycle of the battery. An overheated battery can also cause damage to sensitive electrical components that can be very expensive to repair – no different to an overheated internal combustion engine. To offset the performance losses of batteries, OEMs incorporated liquid cooling into the battery system by employing cooling channels throughout the battery to maintain operating temperatures at peak performance levels. This is generally between 20 to 40 degrees Celsius. The preferred coolant for EV vehicles and batteries is a mixture of Glycol and water, the same as used in internal combustion engines. Penrite manufactures a range of OEM approved coolants including Penrite Green OEM Coolant which is suitable for electric vehicles and OEM approved by Tesla for use on the vehicles. Penrite says its Green OEM coolant has excellent stability at high temperatures and excellent Fleet business is important for many independent and chain workshops, and so in the same way that fleets are currently making decisions about when they should be investing in EVs, workshops that are catering to these businesses should be considering what preparations they need to make to ensure they can continue meeting the needs of their customers through the coming transition. This column was prepared for AAAA Magazine by ACA Research, the AAAA’s partners in the AAAA Aftermarket Dashboard which is delivered to AAAA members each quarter. For more information, visit www.acaresearch.com.au or contact Ben Selwyn on bselwyn@acaresearch.com.au

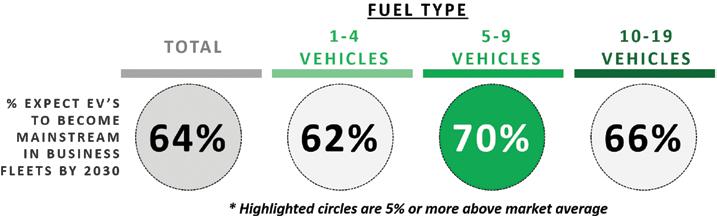

corrosion protection in a broad temperature window. This coolant also offers low electrical conductivity for improved safety performance. Penrite Red, Blue and Purple OEM Coolants are also suitable for electrified vehicles to keep their batteries at ideal operating temperature to enable optimum driving range and performance. Penrite Oil is a 100 percent Australian family owned and operated business and has been producing world class products for over 95 years. For more information, visit www.penriteoil.com.au