
3 minute read
ROLE OF LOW VISCOSITY OILS IN FUEL ECONOMY
Today, the automotive industry and OEMs are increasingly looking to fuel economy to reduce carbon emissions
Why? Because CO2 is emitted with every liter of fuel burned, so the less fuel a vehicle uses, the less CO2 it emits. The growing demand for improved fuel economy has, in turn, driven the adoption of lowviscosity engine oils.
The fact that the viscosity of a lubricant can contribute to an engine’s fuel economy is well known within the industry. But it has taken nearly a decade for many OEMs to transition from heavier viscosity oils to thinner ones due to apprehension about performance and protection, and sometimes the cost.
In general, lower-viscosity oils reduce the amount of energy required to keep engine components in motion, which lowers fuel consumption.
Developing and testing new engine oils requires a careful balance: fuel economy must be balanced with product durability; and the precision of laboratory testing must be balanced with evaluating the oil’s performance in real-world conditions.
Consumers want to know that any performance benefits were tested and achieved under conditions that closely match their real operational conditions for the oil. However, evaluation in the field can be difficult because many factors influence real-world fuel economy, mainly driver behavior and driving conditions.
To isolate the effect of a lubricant, oil formulators conduct large-scale experiments that minimise the number of variables to be controlled and standardise those variables that cannot be controlled. This approach eliminates bias and enables accurate evaluations of an oil’s impact on fuel economy.
“We are already seeing APAC markets move to lower-viscosity engine oils, for example adopting SAE 0W-20 lubricants, amid growing interest in even lower viscosities,” Viva Energy Shell Lubricants Help Desk Technical Adviser, Silvana Farrugia, said.
To support this growing trend, Shell says it is driving the development of effective low-viscosity motor oils.
In 2011, Shell invested in and built the Pearl GTL plant, which it explains is the world’s largest gas-toliquids plant. Located along the coast from Doha, Qatar, it was the culmination of hundreds of millions of hours work.
Ten years later, and the decision to put that time and effort towards producing low-viscosity engine oils made from natural gas is paying off, says Shell.
“There are also many benefits of using lowviscosity oils made with GTL technology. Free of the contaminants inherent to conventional oils, they can generally provide better wear protection and longevity,” Silvana said.
“However, the main reason for the trend towards lower viscosity is the desire among drivers to achieve better fuel efficiency.”
Shell says this is supported by the fact that simply switching to a premium low-viscosity oil can help to increase fuel efficiency by up to three percent1 And, with longer life, Shell’s passenger car lubricants reduce the oil consumption as well. Shell says this all helps drivers to cut the cost of every journey they make while also reducing their CO2 footprint.
So, says Shell, a million hours to create the plans for the world’s largest GTL plant might sound like a lot, but that is how long it takes when you are designing the future of passenger car travel. For more information, visit www.shell.com.au
1 Based on ACEA M111 fuel economy results compared with the industry reference oil
WHY FLUSHING THE A/C SYSTEM IS SO IMPORTANT
In this article, MAHLE discusses this important topic
If you have a vehicle with a compressor failure on stage, then you must be careful, because just replacing the defective compressor is usually not enough, warns MAHLE.
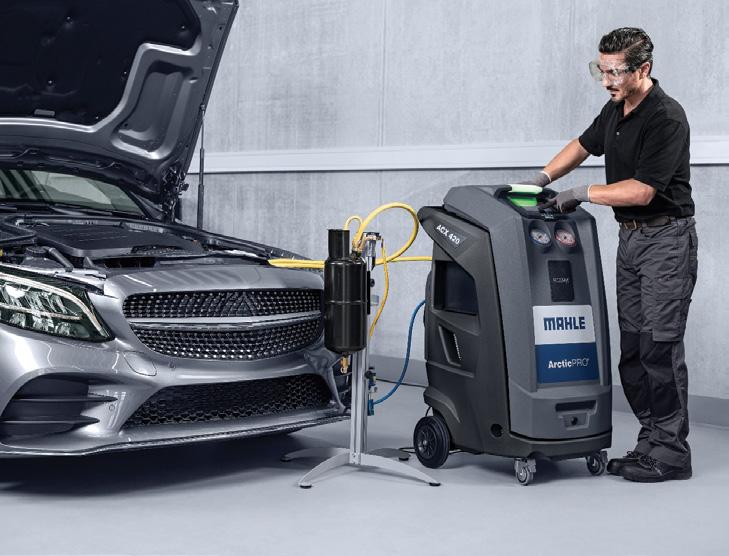
MAHLE says only those who flush the refrigerant circuit can save themselves annoying consequential damage, so it advises that you grab your A/C service unit and flush the dirt out.
Why is flushing required?
Flushing the air conditioning system is one of the most important process steps during repair work or when an air conditioning compressor is damaged. Flushing removes contamination and harmful substances (such as metal abrasion and chips) from the air conditioning circuit. This is necessary to carry out repairs properly and avoid expensive follow-up work; however, air conditioning compressors, filter-driers (accumulators), and expansion or throttle valves cannot be flushed. Depending on the design (parallel flow), the air conditioning condenser must not be flushed either.
Flushing can rid the system of the following possible contaminations:
• Carbonized oil particles, for example, if oil is exposed to high operating temperatures
• Elastomer/rubber particles, for example, due to aggressive acids
• Moisture, for example., due to leakage, improper vacuum, poor-quality additives
• Metal swarf, for example, due to a seized air conditioning compressor or wear on parts
• Aggressive acids, for example, due to the chemical reaction of moisture, coolant, and oil
• Various particles, for example., due to sludge or a poor-quality contrast agent or oil blend
How is flushing performed?
MAHLE Aftermarket says its team and also most vehicle manufacturers recommend the following:
• Flushing with refrigerant and service unit
• Using an air conditioning service unit – such as a MAHLE (ACX) product – and an additional flushing device with filters and adapters to flush the system components against the direction of the refrigerant flow (accessories available separately)
MAHLE says that by using the MAHLE A/C service unit and an additional flushing device with filters and adapters, the system components are flushed against the direction of flow of the refrigerant (both available separately). It says advantages include:
• No costs for a separate flushing medium, as the existing refrigerant is used as the flushing medium
• No disposal costs for the flushing medium
• Removes loose dirt particles and oil
• Method is approved by different vehicle manufacturers
For more information, email mapl.sales@mahle.com or visit www.mahle-aftermarket.com