
3 minute read
INNOVATION FOCUSED CLUTCH SOLUTIONS
Clutch Industries has seen plenty in its seven decades of business
Clutch Industries says it is proud of its 70-plus year history as a major Australian clutch manufacturer, supplying original equipment for Toyota, Nissan, Ford, GM and Mitsubishi.
With the decline in vehicle manufacturing, Clutch Industries has now pivoted its business to supplying the aftermarket, however, it has retained its OEM test lab and most of its manufacturing equipment in Melbourne, Australia.
Research and development is a high priority for the company and Clutch Industries has a dedicated R&D division, known as Mantic Engineering.
Mantic Engineering holds 10 current patents on clutch technology and employs several mechanical engineers in its Melbourne facility. In recent years, the company says it has invested one million dollars in modernising and increasing its manufacturing capabilities, with part of this investment including state of the art automation equipment and robotics to increase efficiencies in its Australian manufacturing processes. Further, Clutch Industries says another focus of its company is undertaking initiatives to increase efficiencies for workshops.
One such initiative launched in 2021 was Clutch Industries’ OEM replacement flywheel program. Traditionally when a clutch kit is replaced, the flywheel must be ground to ensure the surface finish is correct.
Clutch Industries reports it surveyed workshops and found that on average, 4.5 hours of hoist time is wasted due to this process and the trade price for a grind is on average $70 plus the delivery cost: a massive cost for workshops when the cost of the grind, delivery time/cost and lost hoist time is considered.
Clutch Industries says there is a multitude of reasons why you would replace a flywheel instead of grinding one, such as:
• Faster installation time and less hoist time wasted.
• In most cases the price is comparable to a grind.
• Eliminate issues related to a poor grind like shudder, noise and slipping.
• Restore correct stack height, reducing the chance of disengagement issues after installation.
• Stick out from the competition, by offering your customer new instead of old.
Clutch Industries says currently its range covers around 50 percent of the common clutch kits sold (where the OE flywheel is single mass), with the range being expanded regularly. The range is available through our distributors, meaning that you are able to buy everything you need to get the clutch job done in one place.
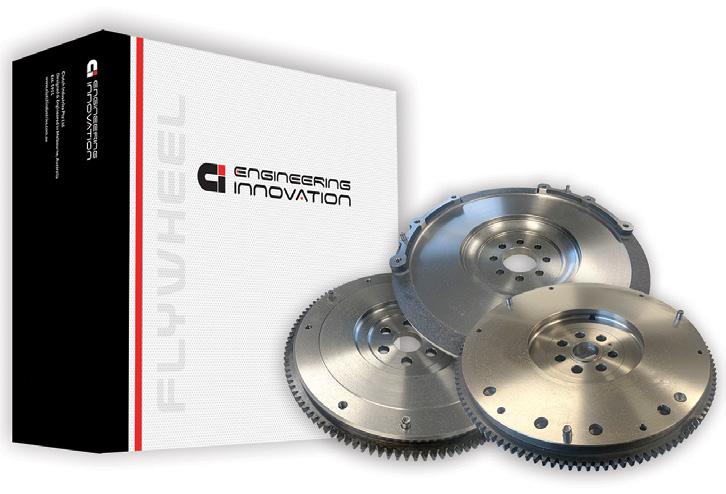
Looking to the future, Clutch Industries says the rise of Electric Vehicles (EVs) will decrease demand for a lot of common vehicle parts, outside of a handful of categories. It states while the effect of this has not been felt in the market yet, with major manufacturers phasing out production of Internal Combustion Engine (ICE) vehicles in 2030, it is only a matter of time before the effect is seen in the industry. Clutch Industries explains that its Mantic Engineering division has a future thinking philosophy and therefore has been proactively approaching the challenge of how to ensure workshops have immediate access to the parts they need in a complex and significant category (clutch) when demand will be declining with increased adoption of EVs.
In 2018 a dedicated engineering team at Mantic embarked on a project to decrease clutch SKU complexity (ie. increase carparc coverage with less parts) and reduce installation time for mechanics whilst also looking to enhance performance and quality compared with typical OEM clutches.
What they created is a clutch system that replaces thousands of different clutch kits with 20 products, called UniClutch.
UniClutch works by taking the fitment complexity out of the clutch and consolidating the mechanical interfaces into a fitment kit, which contains its patented multi fit flywheel mount and patented interchangeable splines.
This system allows the sealed pre-assembled clutch to be adapted to various makes and models where traditionally a different clutch would be required for each vehicle.
Another key piece of patented technology, new to UniClutch, is Mantic’s Radial Dampening Centre (RDC) found in the UniClutch disc. Clutch Industries says this technology is the pinnacle of noise and harmonics reduction inside a clutch disc and performs comparable to that of a dual mass flywheel.
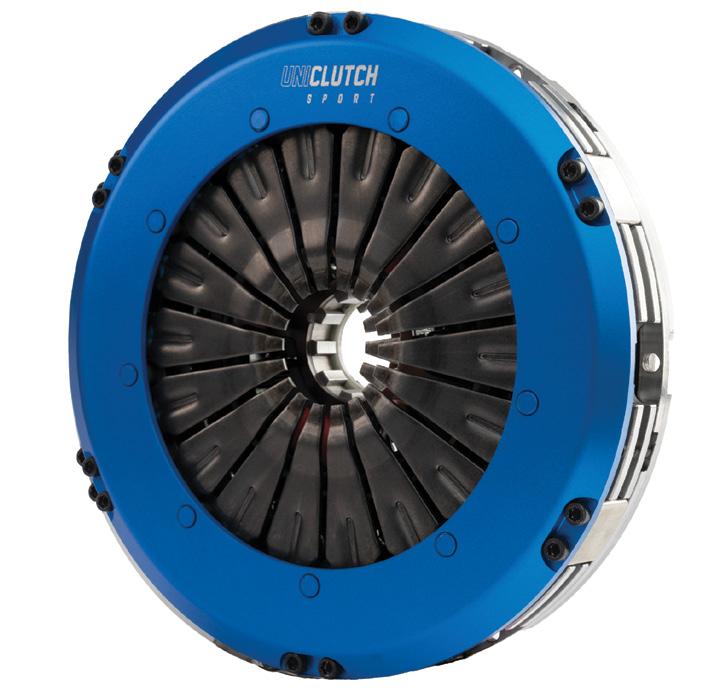
Lastly, UniClutch is designed to handle prodigious torque in a compact modular package which fits into the bellhousing of most vehicles from a Toyota Corolla to a Nissan Patrol. This is achieved by leveraging Mantic Engineering’s 70 years of experience manufacturing multi-disc clutch systems in Australia.
With the development stage of the project now complete, Mantic Engineering has been running a pilot program having hundreds of installations completed in Australia, New Zealand and around the world. The UniClutch will be officially launched in 2023 and will be available through select automotive parts distributors.
For more information, visit www.uniclutch.com or call 1300 369 787.