
7 minute read
Ballast Water Management
Optimarin - water quality can create logistical difficulties and delays
Ballasting operations in different parts of the world can be challenging due to wide variations in water quality. And this could make it difficult to achieve compliance with IMO’s so-called D2 standard for ballast water discharges - even with a BWM system installed.
Advertisement
The D2 standard, which will be mandatory for all ships from September 2024 under IMO’s BWMC, specifies the maximum amount of viable marine organisms allowed to be released in ballast water discharges. But poor water quality at certain ports, such as those with a high level of sediment load, may impede effective ballasting operations needed for compliance and thus prevent ships calling at these ports. And this could result in lost contracts and revenue for shipowners if they are not able to sail to challenging ports, according to Norway’s BWM specialist Optimarin.
Optimarin’s Chief executive Leiv Kallestad points out that challenges in ensuring ballast water quality meets local standards can create logistical difficulties and delays for fleet operations. “The main issues are transparency and predictability - being aware of the water quality at different ports to plan voyage itineraries in an optimal manner. But how can that be achieved on a global basis with multiple ports on numerous trade routes? The answer is digital technology.”
Optimarin has developed the pioneering OptiLink cloud-based digital solution that is able to stream data on water quality at ports around the world. Its head of technology Kim Stian Haugland, who developed OptiLink with his team, says analysis of big data means a ship operator can assess water quality in specific ports through ‘heat-mapping’ to determine the duration of ballasting operations, which makes for better fleet planning.
The advanced digital tool provides real-time monitoring of Optimarin’s BWM systems, along with automated data generation and remote connectivity for ship-to-shore data-sharing in this critical area of ship operations.
It also gives the vessel crew instantaneous online access to key performance indicators for the system - including water quality and system functionality - through a user-friendly visual interface featuring data transmitted from the ballast water control system. OptiLink means BWM can be integrated in the ship’s digitalised functions, while also giving a fleet-wide overview of ballast water KPIs for each vessel.
Online connectivity enables continuous condition monitoring of the BWM systems for proactive maintenance, as well as interactive remote support with over-the-air software updates to keep the system working efficiently.
These features make for improved efficiency of ballast water operations and enhanced voyage planning to support reduced fuel consumption and lessen vessel downtime. In addition, OptiLink allows compliance data on ballast water quality to be transmitted to regulatory authorities for certification, effectively negating the need for lab testing and on-board inspections, to facilitate faster port turnarounds.
“Data visibility is vital to the predictability of ballast water operations,” Kallestad explains. “This also has significant economic spin-offs in fuel cost savings, optimised ship routing and reduced port turnaround times to boost the overall cost-efficiency of fleet operations.”
Cruiseship contract for BIO-UV
French UV-C water treatment specialist BIOUV Group has received an order to supply a low-flow BIO-SEA L-Series BWM system for
OptiLink enables improved efficiency of ballast water operations and enhanced voyage planning to support reduced fuel consumption and lessen vessel downtime
retrofit installation to the 1,268 gt expedition vessel Quest .
The 49 m long, 60-passenger capacity vessel is the fifth passenger ship operating under Cruise Management International (CMI) to have specified a BWM system from BIO-SEA by BIO-UV Group partner TECO2030.
Maxime Dedeurwaerder, Business Unit Director, BIO-UV Group’s maritime division, said, “This new order underscores the success of the partnership agreement we signed with TECO2030 in 2019. The BIO-SEA system fits perfectly with TECO2030’s ethos to supply environmentally sustainable, energy efficient technologies to the global shipping fleet. The environmental and energy efficiency of our UV-based treatment technology provides the optimum solution for expedition cruise ships operating in ecologically sensitive environments.”
Incorporating BIO-UV Group’s next generation UV-reactor, the ‘L’ range is based around a completely new type-approved UV lamp arrangement. The system is sized to guarantee full IMO and USCG compliance, treating flow rates of between 20 m3/hr and 120 m3/hr from one of the most compact, low energy consuming BWM systems on the market.
The system retrofitted to Questis modular to fit in the limited space available and has two lamps to treat a ballast water flow rate of 55 m3/hr. “One lamp can treat ballast water flows of up to 30 m3/hr. A further one or two lamps can be added to the BWM system skid to deal with higher flow rates. This means reduced maintenance for the crew, fewer spare parts have to be kept on-board and as the automated UV sensors adapt to the quality of the water, energy consumption is better regulated, reducing energy consumption and preserving lamp life,” Dedeurwaerder added.
BIO-UV Group’s partner TECO2030 provides its customers with full turnkey environmental solutions, offering everything from front end engineering and design, through to installation, commissioning. VI GRATULERER
SKIPSREVYEN The expedition ship Quest
MED JUBILEET! Optimarin har levert ballastrensesystemer til nasjonal og internasjonal skipsfart siden 2009.

Ecochlor’s container unit suitable for offshore units
US-based Ecochlor has launched a containerised version of the EcoOne filterless BWM system. The EcoOne Container Unit is well suited for semi-submersible rigs, jack-up rigs, drillships, FPSOs, FSRUs and other vessels with infrequent ballasting operations at medium to high flow rates.
“The EcoOne Container Unit offers incredible benefits to Mobile Offshore Drilling Units (MODU),” said Andrew Marshall, Ecochlor CEO. “One system can simultaneously serve up to four separate sea chests or quadrants, in the case of the semisubmersible rigs. It also allows for gravity ballasting on uptake and discharge and has
OPTIMARIN AD 1/2 PAGE
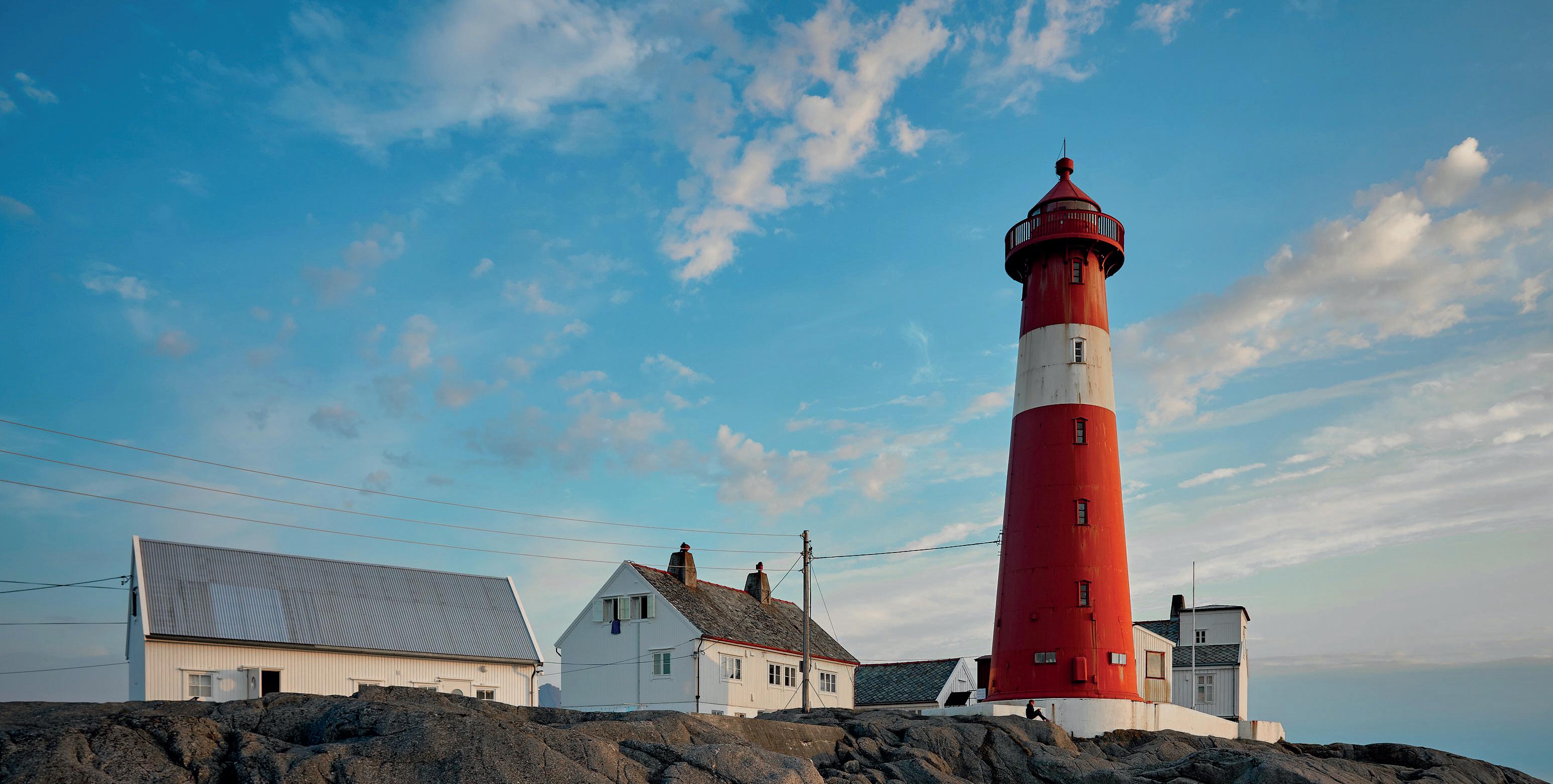
www.optimarin.com ENVIRONMENTALLY FRIENDLY BALLAST WATER TREATMENT
The EcoOne Container Unit is well suited for semi-submersible rigs and other offshore vessels
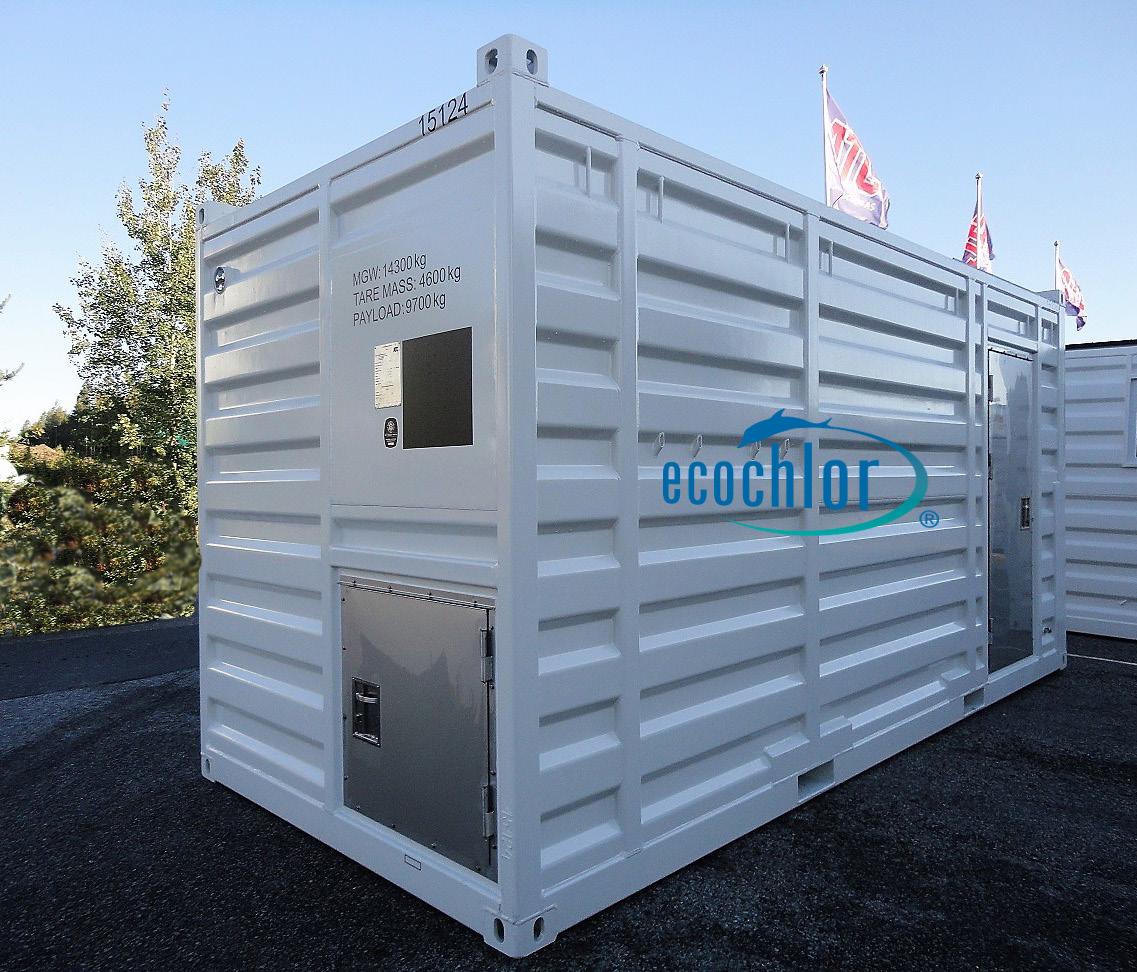
very low power requirements. Plus, a single unit can be easily shared between multiple rigs and/ or vessels. This is a great break-through for the offshore market as they have faced difficulty complying with the BWMC due to a lack of systems that work reliably and cost-effectively for their unique needs.”
The unit has a small footprint and does not require filters. Installation requirements below deck and in the pontoons are minimal with only one-way, 1”/DN25 piping. Additionally, the container can be removed while the MODU is stationary, saving valuable deck space.
DESMI – the importance of service
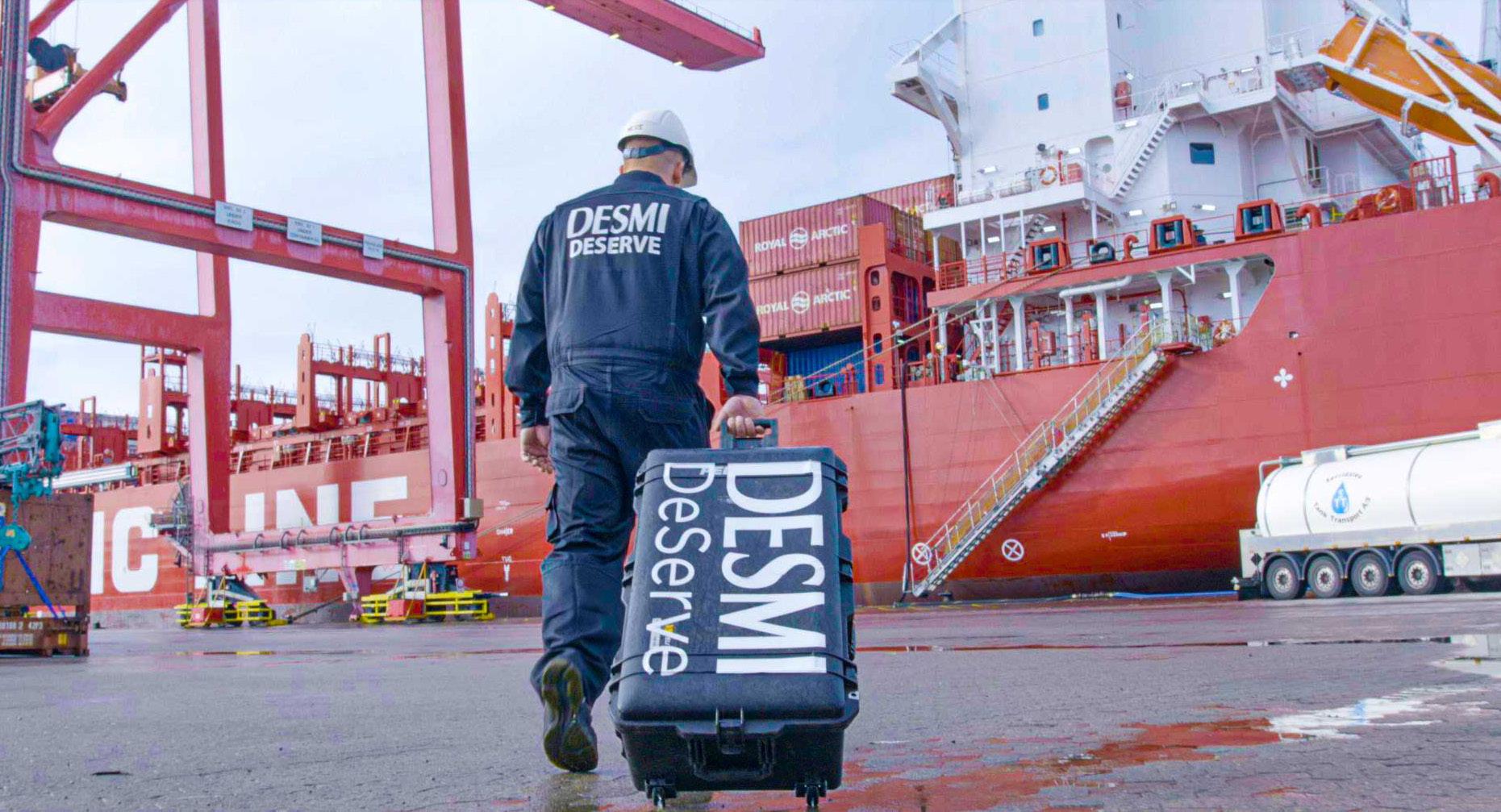
Denmark’s DESMI’s global service department adds value for global and local customers through optimal equipment performance and 24-hour accessibility anywhere in the world. In all industries, equipment must be kept in top condition to deliver safe, energy-efficient, and reliable performance throughout the lifetime of the assets and ensure maximum return on investment. Buying the hardware is just the start - after that, professional service and maintenance are required – especially for equipment used for mission-critical operations in tough environments where sudden breakdowns are not an option.
DESMI DeServe is DESMI’s dedicated global service and aftermarket department and fulfils the need for professional service through a complete range of offerings for all DESMI products. According to DeServe Managing Director Johan Schwerin, the objective is very simple. “Our target is to make it as easy as possible to own a DESMI product. When our hardware offerings are complemented by our service offerings, the result is a complete, valueadded solution that keeps running efficiently for years. We contribute to efficient and problemfree performance for all DESMI products throughout their lifetime.”
With a 24-hour phone hotline, contacting DESMI DeServe is very simple and provides quick access to a world of service options. DeServe offers spare part kits, on-site repair and service, product replacement, installation, commissioning, and user training, and digital offerings that provide an overview of connected assets and enable preventive maintenance.
“Our department is staffed by service specialists around the globe,” explains Johan Schwerin. “They have extensive product and application knowledge and react quickly to service requests. We also cooperate with authorised partners so our customers can expect rapid support anywhere. At DESMI DeServe, we are always close to our customers and their assets.”
DESMI DeServe’s global presence gives the department the capabilities to support international customers looking to streamline and optimise their service strategies. At the same time, DeServe draws on its extensive local market experience to adapt to all requirements and support customers of all sizes.
“We don’t assume that one size fits all,” adds Johan Schwerin. “We have global customers that require high-level global support such as service contracts or spare part framework agreements – and we have smaller, local customers who mainly require fast parts delivery and a contact person they trust. We can accommodate DESMI customers of all sizes.”
A DESMI service technician joins a ship