
22 minute read
Bureau Veritas Launches New Swab Testing Service as COVID-19 Found to Survive 28 Days on Surfaces
Cleaning & Hygiene
Bureau Veritas Launches New Swab Testing Service as COVID-19 Found to Survive 28 Days on Surfaces
Responding to latest research showing Covid-19 can remain infectious on surfaces for up to 28 days, leading health and safety authority Bureau Veritas has developed a new swab sampling service.
Giving employers the peace of mind of knowing their workplaces are COVID free, the new offering involves Bureau Veritas’ highly-qualified occupational hygienists swab testing various surfaces on business sites in line with MDHS 97 – Methods for Sampling Surface Contamination.
Recognising the many challenges businesses face in remaining open and operational when dealing with a potential coronavirus outbreak, the swab sampling service includes a speedy 24hr turnaround time for all samples. Following this, a sample analysis report is issued to businesses within seven working days from the final visit to a site.
Crucially, if traces of the virus are detected, Bureau Veritas can pin-point exactly where and provide accurate recommendations on adapting and improving cleaning practices to help eradicate COVID-19 from the workplace.
The launch of the new swab sampling service comes as latest research shows the virus that causes COVID-19 can survive for up to 28 days on surfaces such as the glass on mobile phones, stainless steel, vinyl and paper banknotes1.
Joe Marais, Occupational Hygiene Team Leader at Bureau Veritas comments: “Amid the ongoing coronavirus pandemic and new research showing the COVID-19 virus can survive almost a month on certain surfaces, employers face an ever-escalating pressure to prove their premises are clean and COVID free.
“To support businesses in demonstrating that reassurance, we’ve developed our new tried and tested swab sampling
service, which as restrictions continue to tighten, will be essential to keeping many sites open, operational and safe enough for employees, visitors and customers to use. We’d encourage all businesses, whatever the sector, to make use of this critical new service.”
According to Bureau Veritas, one of the main areas to consider when managing coronavirus risks in the workplace includes heating and the movement of indoor air.
Joe adds: “Reducing the amount of fresh air in workplaces and using Air Handling Units to manage internal climates brings an increased risk of retaining COVID-19 within the environment. Therefore, it’s really important that duty holders assess and identify the risk this presents for work surfaces.
“For many sectors, this is still new territory where following best practice via a third party consultancy such as Bureau Veritas provides confidence to employers, their staff and customers during what remains a challenging time for us all.”
As part of its commitment to helping employers navigate the coronavirus pandemic, Bureau Veritas is hosting a free webinar on developing appropriate controls in the workplace. The webinar will be hosted by Joe Marais, covering current issues with Air Handling Units, the risks of air recirculation as well as a panel discussion with Suhail Bakawala from independent laboratory Eurofins.
To register for Swab sampling: Control measures and indoor air quality in the COVID-19 era webinar, please visit: https://bureauveritas.zoom.us/ webinar/register/8516020712759/ WN_CdZJ7dA0Sy-nyv7P1JfuGA
Cleaning & Hygiene
EverPanel Launch Smoothes the Path for Sustainable Public Sector Response to COVID-19 Distancing
A new modular walling system from the creative brand behind the bestselling EverBlock® universal building blocks has launched to smooth the path to sustainability for public sector organisations in a post COVID-19 environment.
EverPanel is a highly configurable, naturally hygienic modular wall system which has infinite applications and can be reused endlessly in all kinds of spaces. The interlocking walls can be quickly constructed to form physical barriers, portion off space for private offices or consultation and treatment rooms, segment offices into socially distanced cubicles and used to delineate traffic flow in public spaces by creating immediate temporary corridors.
A flexible, affordable and above all sustainable solution, EverPanel affords public sector facilities management teams with the wherewithal to make buildings safe for use.
Joe Plosky, Everblock® UK Director said, “EverPanel fibreglass modular panels can be installed in minutes thanks to a proprietary interlocking lug and connector system. They can be used as partitions or deployed to create rooms with doors, sleeping pods, offices, nursing stations, storage areas and divide spaces as required to enable social distancing in a wide range of settings. They are the ideal public sector solution thanks to their immense flexibility and very quick installation and demounting.”
EverPanel modular walls don’t require drilling or other intrusive installation, meaning the building can continue to be used without disrupting users as controlled areas and social distancing spaces are created. The panels can be moved as needed, reconfigured and deployed in other areas as temporary or permanent solutions on demand, making them incredibly sustainable. The panels can be disinfected and wiped clean after use to maintain good standards of hygiene.
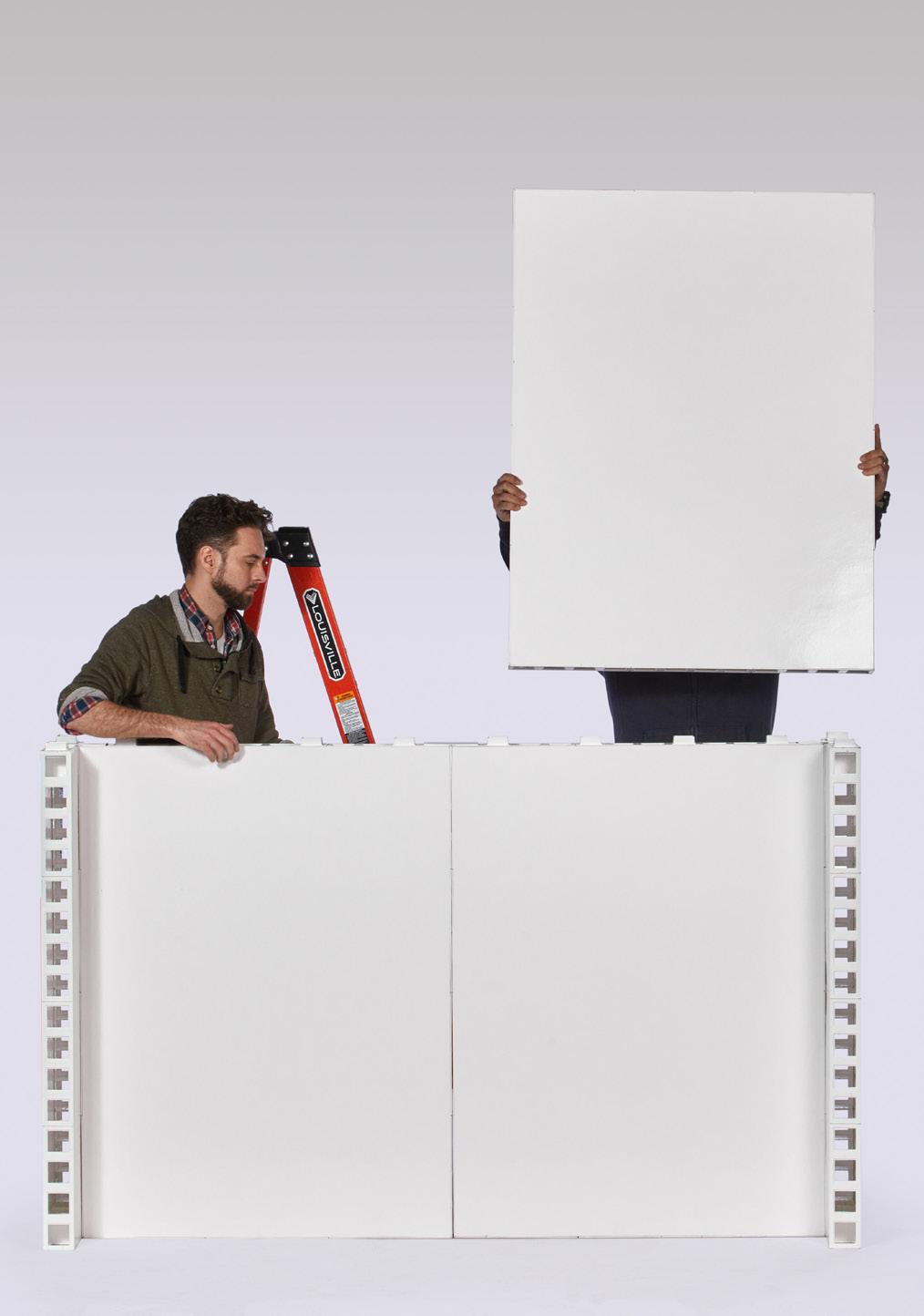
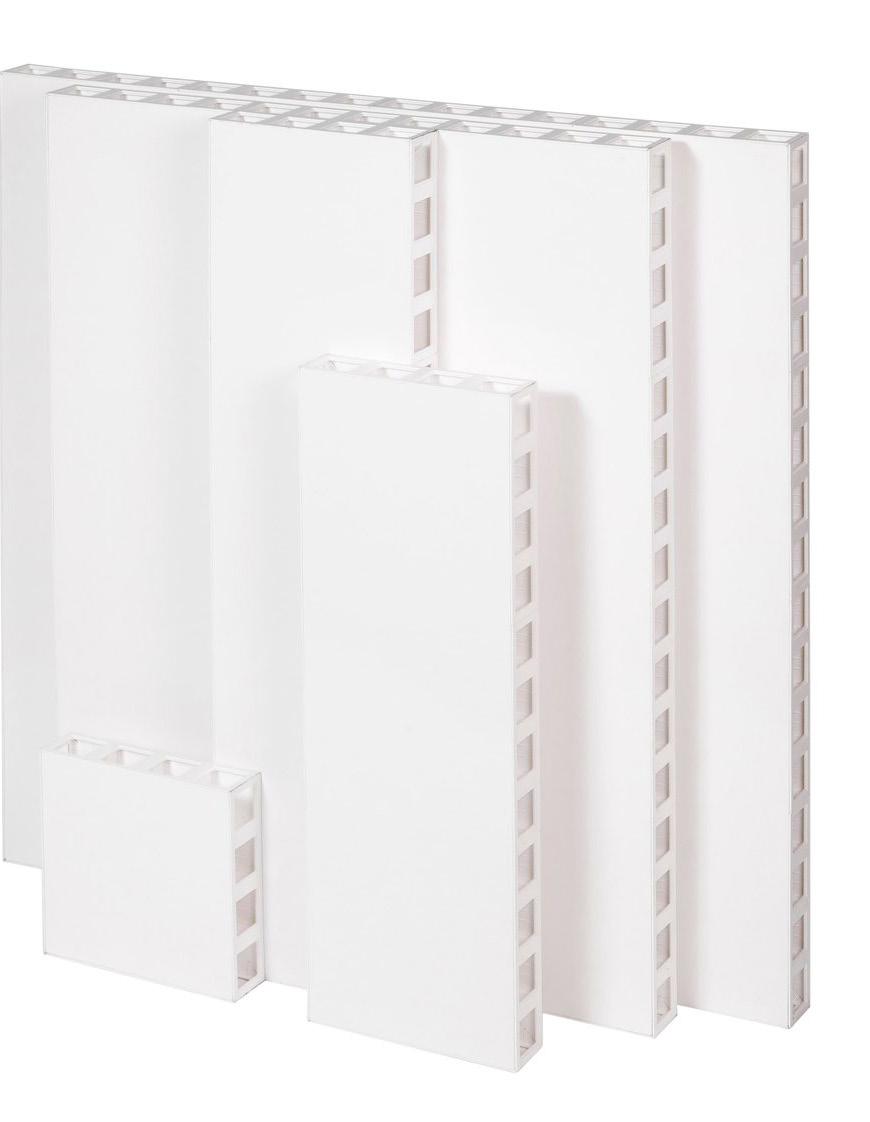
To find out more about EverPanel, visit www.Everpanels.co.uk

Cleaning & Hygiene
Breaking the chain of infection through innovation
As a direct result of the Coronavirus pandemic, health, hygiene and above all safety is at the top of everyone’s agenda – and in premises, people need to feel as safe as possible.
“We are working closely with facilities managers to recommend that they take the right steps to ensure the safety of their staff and visitors, and to restore confidence”, said P-Wave® Sales and Marketing Manager Mark Wintle.
One of the biggest challenges in any building is keeping regularly touched surfaces, or ‘hotspots’ clean and free from bacteria and viruses. Door furniture is among the ‘most-touched’ of all hotspots in business premises, and is one of the fastest ways for infections and viruses to spread. The typical handle in a public toilet is home to up to 40,000 germs per square inch, and standard handles are without doubt the largest carrier of healthcare associated infections.
Keeping surfaces clean can only ever be a temporary measure as each person who touches a door handle transfers new bacteria, which multiplies and spreads to other users. Traditional stainless steel or painted handles increase the spread of infections by providing an area for transmission to occur, creating more carriers.
“What if the door furniture was antimicrobial and antibacterial, creating a permanent solution, which is effective against bacteria and viruses and continues to protect in between your standard cleaning intervals?”, asks Mark Wintle. “P-Wave® is delighted to introduce the perfect solution, which is not only affordable, but also features an additive which lasts for the entire lifecycle of the product.” Antimicrobial to the core
P-Wave’s Steri-Core antimicrobial silver ion technology door furniture helps reduce the spread of bacteria and viruses. Tested and proven effective against MRSA, E-Coli, Salmonella and Norovirus, the products feature a high concentration of antimicrobial which is blended with the polymer during the manufacturing process and forms part of the molecular structure of the product. This ensures that the silver Ion technology is active all the way through to the core of the handles. So unlike coated products or films, even if they become scratched or damaged, Steri-Core handles

will continue to kill pathogens effectively for the life of the product, and each handle has a 10 year manufacturer guarantee.
To withstand heavy usage, the handles are one-piece injectionmoulded from strong polymer material with rounded edges and no joints or joins, 100% recyclable and scratch and water resistant, the unique material will not rust, unlike standard metal handles. Available in two widths (75mm or 100mm), in blue, black or grey/silver, the handles are fire rated and UV and fade resistant, making them perfect for indoor and outdoor use.
The non-porous polypropylene material stops dirt embedding and staining the surface, making the removal of dirt and bacteria easier compared with traditional materials. The material used in the SteriCore products enables quick effective all over cleaning using detergents, steam cleaning, and chlorine disinfectants (BS EN 12720:2009). European standard specifies a method for the assessment of the resistance to cold liquids of all rigid furniture surfaces regardless of materials.
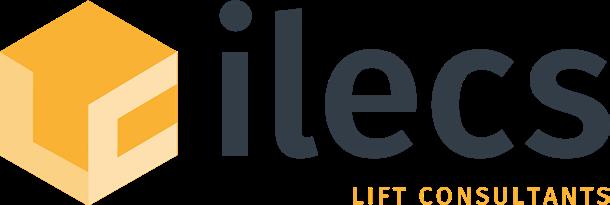
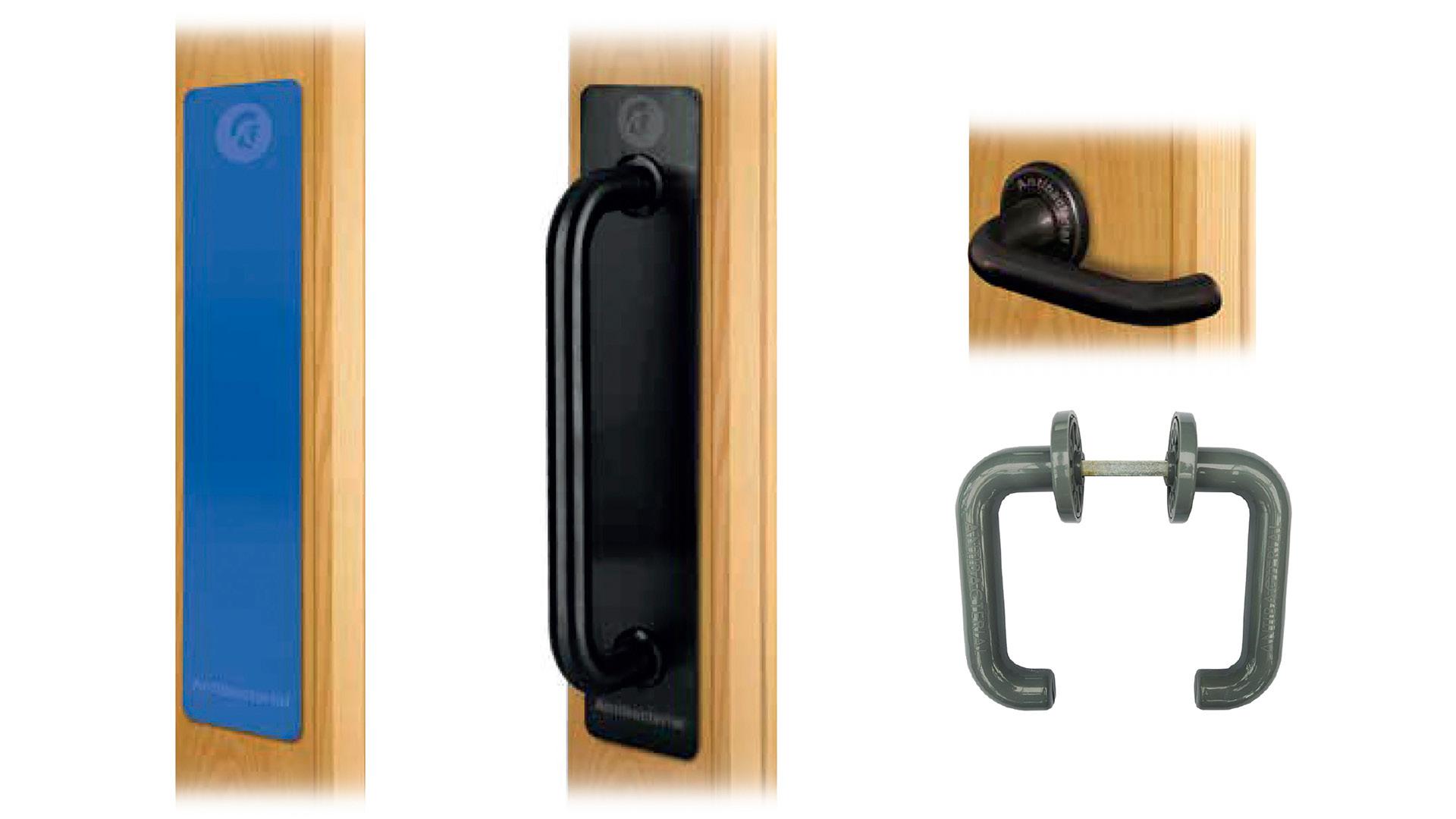
Patents have been granted for the range and independent tests prove that P-Wave’s SteriCore products are made from the world’s only material clinically proven to kill the non-enveloped EPA FCA Strain F9 of Human Norovirus (ISO 22196:2011). P-Wave® is currently awaiting results of tests to prove that its Steri-Core products are also effective against Coronavirus, which – according to the American Chemistry Council – is an enveloped virus and easier to kill than non-enveloped viruses.
“P-Wave’s P-Hold Steri-Core, P-Plate Steri-Core and P-Lever Steri-Core not only provide a high level of protection against virus transmission, but also save money over many alternatives,” said Mark Wintle. “This solution avoids the regular and costly replacement of antibacterial covers or films as well as their ongoing maintenance. We are delighted to be making a positive, and affordable, contribution to keeping people safe.” www.p-wave.co.uk
We manage your lifts, so you don’t have to...
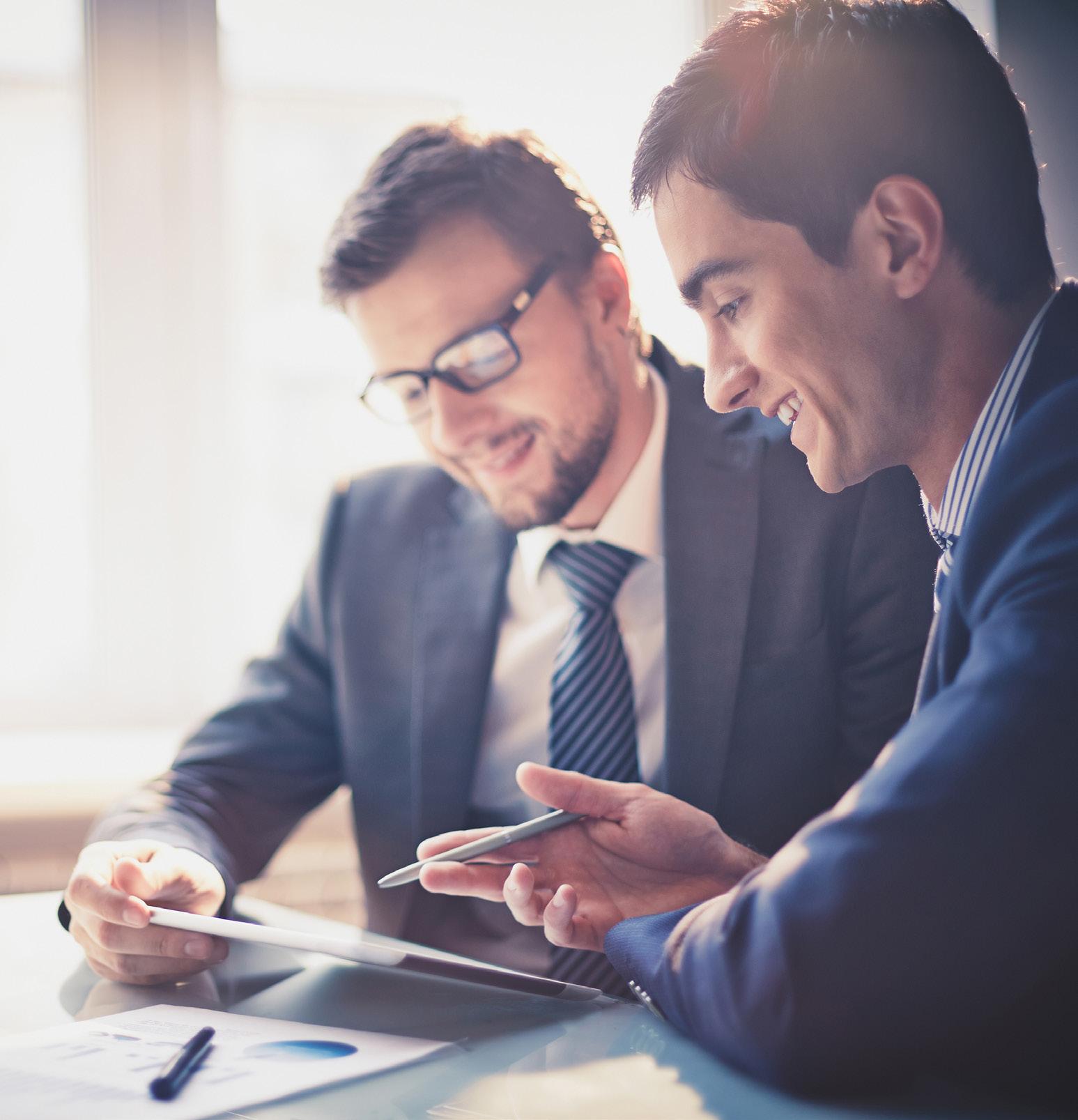
From lift design and engineering, to administration support and lift management, it’s our job to provide expert advice and build impartial solutions designed to keep you moving.
Independent Lift & Escalator Consultants. Get in touch to discuss your requirements: w: www.liftconsultants.co.uk t: 01206 399555 e: info@liftconsultants.co.uk
Join the PSSA - Launching the Public Sector Sustainability Association
The Public Sector Sustainability Association (PSSA) provides a professional association and network for all those working in the Public Sector who have a common interest in sustainability. The aim of the association is to bring together a wide group of people working across all areas of the Public Sector – to help educate, train, support and connect as we work towards a more sustainable future.
Never has there been a more pressing need and indeed, requirement for individuals and organisations to turn their attention to sustainability and take stock of their environmental impact on our world.
An increasing number of UK local authorities have declared a climate emergency. But having made this important step, what happens next? Well for many sustainability professionals working within these authorities, they simply do not know. Logically, the first step that can be taken is to develop a strategy to address
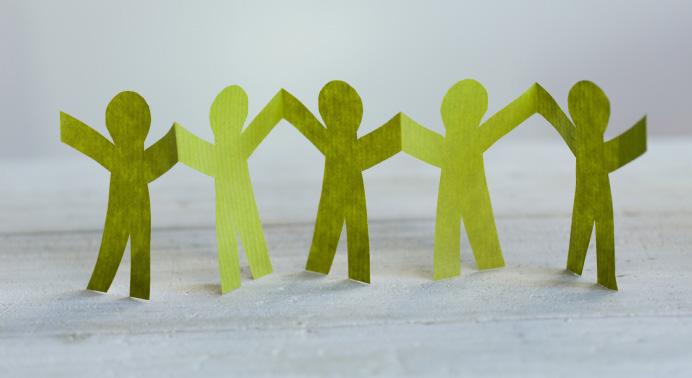
the challenge of the emergency they have declared. However there are a number of pitfalls and issues which can arise when doing so and there is a need for the individuals tasked with creating such a plan to be given the knowledge and support they need to do so.
Similar issues are faced by professionals working in the NHS (the health and care system in England is responsible for an estimated 4-5% of the country’s carbon footprint), Universities, Schools and of course central Government.
Through the PSSA we hope to
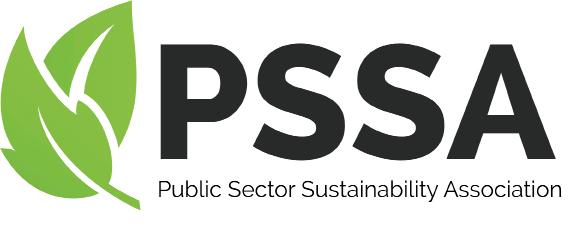
provide these individuals with the support, guidance and knowledge that will assist them and by extension, the entire country in tackling the climate emergency and recuding their organisations carbon footprint. The assocation will provide the latest news and developments, best practice, case studies, white papers, reports and guides to this aim.
There is no charge for membership to those working within the Public Sector and we are now open to new members. If you are interested in joining, please visit our website where you will find more detailed information about the association and also a membership form to join.
www.pssa.info
PSSAWARDS
Public Sector Sustainability Awards
Highlight your commitment to sustainability - become an environmental leader.
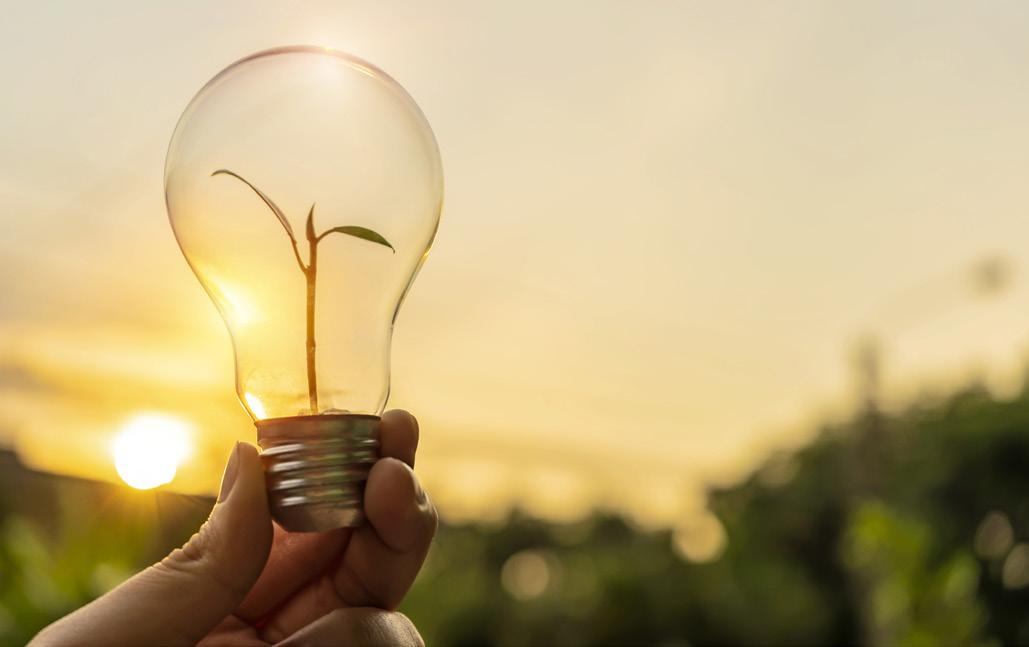
The purpose of the Public Sector Sustainability Awards is simple - to promote environmental leadership, to innovate and to inspire all those working in the Public Sector committed to reducing the carbon footprint of their organisation.
HOW TO ENTER:
There is no qualifying criteria that needs to be satisfied in order to enter the awards. All we ask is that entrants send us up to 2000 words detailing the activities undertaken by them to reduce, by any means, the impact of their organisation on our environment. Please feel free to attach any images, graphs, charts etc to support your entry.
You can focus your entry on just one project or multiple schemes. You can enter as an individual or on behalf of your organisation, or both, as there are awards for both categories.
There is no charge for entry.
If you wish to enter, please complete the registration form at www.pssa.info/pssawards or download the form from the website, complete it and email it back to us. Your completed entry needs to be submitted by the 31st January 2020 and should include images and/or logos.
Please send your entries through to submissions@pssa.info.
If that is not possible, you can mail them to:
PSS Awards, 42 Wymington Park, Rushden NN10 9JP
Whether it is on a stand at an exhibition or through our website contact page, one of the most common questions we are asked is:
Similar questions can also include: “Why do we need you when we can ask the lift contractor?” or even “My contractor is also a lift consultant so why should we appoint you?”
There are several differences between a lift contractor and a lift consultant, but perhaps the most important is that of independence. As an independent lift consultant, we do not sell lifts, lift parts, or lift maintenance. Therefore, when it comes to providing advice, whether that be technical or administrative, we have no ulterior motive, no hidden agenda and no conflict of interest. What we sell is technical expertise. Our experience and technical knowledge allow us to provide advice on all aspects of the industry without bias or prejudice therefore affords our clients peace of mind when it comes to making the right decisions in relation to their lift project or maintenance portfolio.
As a lift consultant, we act on behalf of the client. Whether they are looking to install a new lift, modernise an existing lift or simply manage the day to day operation of a lift portfolio, we provide assistance and advice on issues from planning and design to maintenance and legal responsibilities.
It is often the case that a lift contractor will set out to deliberately mislead. Nonetheless, contractors are not always best placed to determine the needs of the client. Ultimately contractors need to sell a product or maintenance service in order to continue in business. There is always therefore a risk that advice given by the contractor, will be based around what they can offer or sell and not what is most appropriate for the client. With no product to sell, a consultant can analyse a client’s individual requirements and offer an independent viewpoint on the most appropriate solution. This may not always be the cheapest option, but it will most likely be the most effective.
Employing a consultant can save a client money. Whether it be evaluating contractor quotations for repair work on a
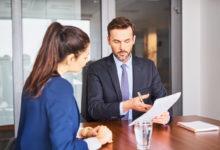
managed portfolio, or tendering for major lift installation projects, the savings gained by employing a consultant can often make them at the very least, a cost neutral addition to any lift project. However, it is the piece of mind that they can bring, providing the information and guidance that allows the client to make the right decisions when it comes to selecting maintenance, design and equipment that can make a real difference both in the short term and for the remaining life of the lift.
If you would like independent advice regarding your lift portfolio, or just have a question for us, please contact one of our specialists for a FREE telephone consultation on 01206 399555 or get in touch via our website.
For more information on advertising within BFM Magazine, please visit our website or get in touch using the details below:
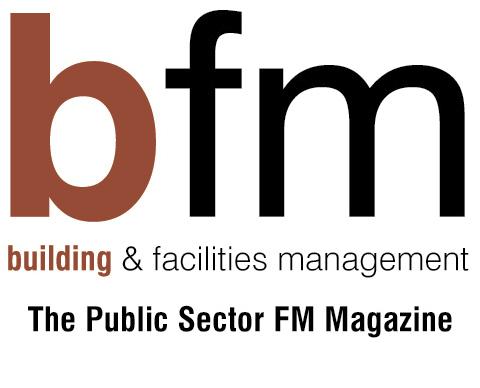
Health & Safety
What you need to know about working in leading edge applications
Despite steady progress, falls from height remain a common cause of injury and death across Europe. This is why regulations surrounding fall protection equipment exist and are regularly updated – to help ensure manufacturers meet certain standards. These regulations, and the associated standards that manufacturers of fall protection equipment must meet, are important when working in leading edge applications.
In this article, Tim Bissett, Technical Manager for Fall Protection at MSA Safety looks at the relevant standards relating to leading edge work; what to look out for in the equipment you use; and what processes you need to have in place, including the vital importance of a rescue plan.
Tim has been Technical Manager for the Latchways® Engineered Systems range for 18 years. Part of his role is to contribute to the development of product standards for PPE. This involves looking at product testing methods and systems and evolving standards to meet changing industry needs. He is a member of the BSI Technical Committee PH/5, from which he convenes two working groups for CEN/TC 160.
What is leading edge work?
“Leading edge” work or “edge working” is defined as working at any unprotected edge of a platform, floor, or other construction point where there’s a risk that the lifeline a worker is using may come in contact with an exposed edge, or edge of the working surface. In many scenarios, leading edge applications occur when a worker is connected to an anchor point below their back D-ring, although it’s also possible when anchor points are above this position.
Work in leading edge applications presents its own unique challenges and safety hazards; one of which is the greater risk of lifelines being frayed, cut, or severed on impact with the edge in the event of a fall. This is complicated further should the worker swing after falling, creating a pendulum-like motion. The friction this causes can increase the likelihood of the lifeline being cut or severed.
These potential risks place a sharp focus on testing criteria
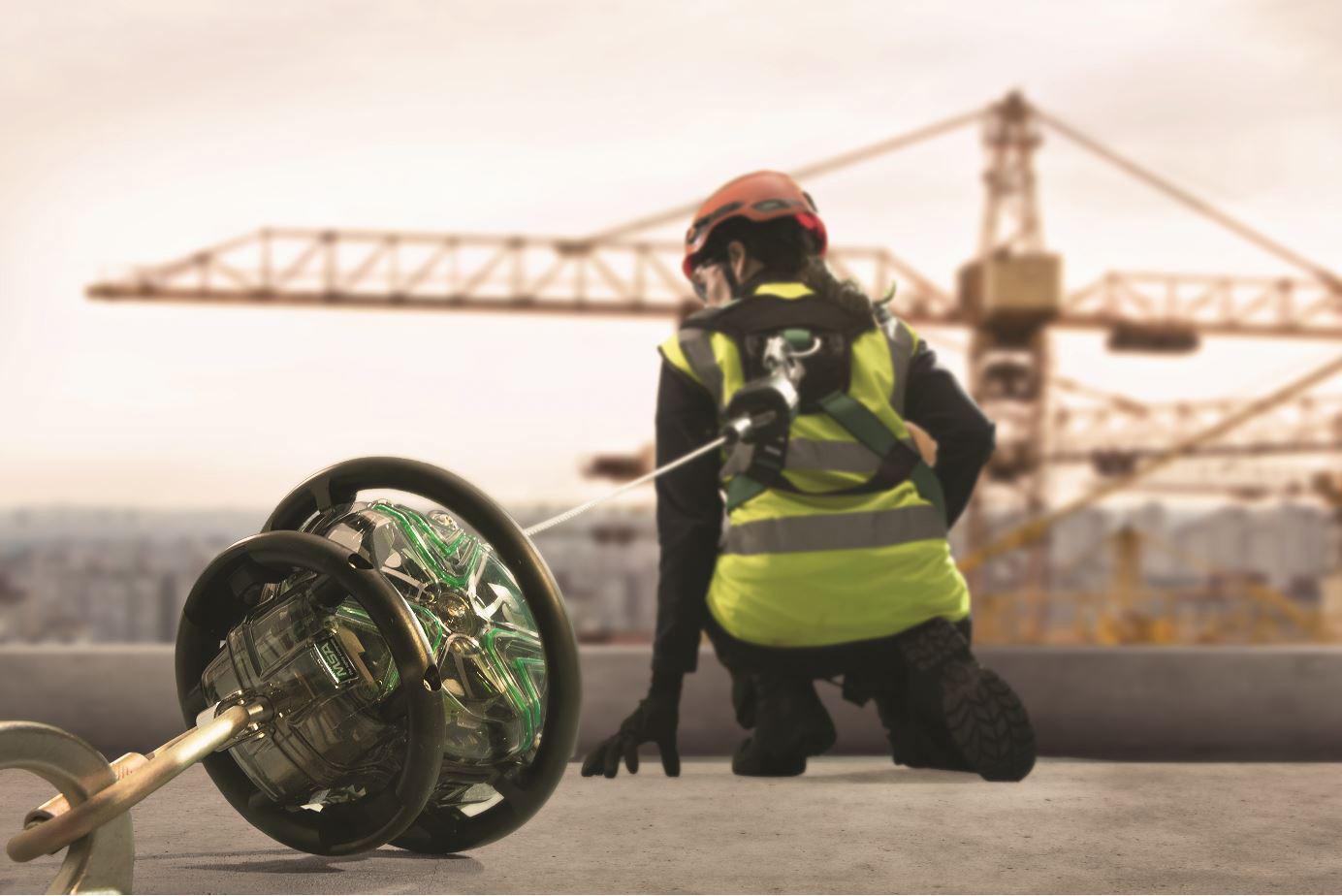
within relevant standards, following best practice and choosing the right equipment for the job. Let’s start by looking at the standards you need to be aware of.
Standards relating to leading edge work
First things first, before any leading edge work takes place, check that the equipment you’re using adheres to the relevant standards. We appreciate that these standards can seem complex, so we’ve broken them down below.
PPE Regulation (EU) 2016/425
These regulations, which were first introduced in 2018, imposed additional requirements on manufacturers of PPE, including an assessment of the risks against which the PPE is intended to protect and changes in requirements for product marking. It’s vital that purchasers of PPE take steps to ensure that their suppliers meet these new regulatory requirements. You can do so by looking out for the CE marking affixed to PPE. This provides evidence of compliance with the applicable EU legislation.
EN 360 and CNB/P/11.060
This standard (EN 360:2002), relating to retractable fall arrest devices, is currently under revision and is expected to be out for review shortly prior to publication. It is likely, given their increasing popularity, that an updated standard will encompass twin-legged, as well as singleunit retractable devices. Be mindful that overhead or traditional SRLs meeting the requirements of EN 360:2002 are not necessarily designed or rated to arrest a fall over an edge. Necessary steps should always be taken to select the absolute right equipment for the job at hand.
CNB/P/11.060 is a coordination document associated with EN 360:2002. It outlines the testing criteria for the use of SRLs in leading edge applications, specifically how SRLs must carry evidence of dynamic performance, dynamic strength, and static strength within a leading edge application with the retractable lifeline stressed over an edge. Adherence to this coordination document and the testing criteria within it are central to mitigating the potential risk of lines fraying or being cut in the event of a fall.
First port of call: hierarchy of fall protection
Typically, fall protection is associated with saving a worker’s life in the event of a fall. And while this isn’t strictly wrong, it’s not the ideal scenario either. The hierarchy of fall protection helps to prevent a worker ever getting into a situation where they could fall by prioritising various applications from “most preferred” to “least preferred”. Leading edge applications will inevitably mean working in fall arrest – the “least preferred” option. It’s not something to take lightly and should always be a last resort, taken only once the first three options outlined below have been explored. 1. Hazard elimination. This means the removal of the hazard by designing it out wherever possible. It’s the “most preferred”, safest option. If there’s no hazard, there’s no fall. 2. Collective (or passive) fall prevention. This defines products that prevent access to a fall hazard. A guardrail, for instance, acts as a physical barrier between the worker and the hazard. 3. Fall restraint. If working in fall restraint then there is no barrier between the user and the fall hazard. Instead, they’re using fall protection equipment – harness, lanyard, and anchor point – that will not allow them to reach the hazard. For example, a worker who is working in fall restraint may use a six metre lanyard to connect to an anchor point at least seven metres away from the fall hazard. 4. Fall arrest. This defines equipment designed to catch (or “arrest”) the worker in the event of a fall. This is the “least preferred” option because arresting a fall exposes the worker to significant forces, putting them at risk of physical harm. Rescuing a fallen worker (which we’ll come onto a little later) can also be a challenging and potentially dangerous process.
Let’s take a look at some key things to consider if – after following this hierarchy – edge working remains the only option available.
Choosing the right harness for the job
First things first, all harnesses on the market should be compliant in accordance with EN 361:2002. That’s a given. But a good harness – one that’s comfortable, doesn’t restrict workers’ movement, and mitigates impact on the user’s body in the event of a fall – goes beyond mere compliance.
Fit is fundamental to achieving this. Leg and shoulder straps should be easily adjustable for a comfortable, snug fit. The user’s finished position in a fall scenario should be heads up and slightly forward-leaning. This is important for correct distribution of load through the leg straps and load through the body, such that the spine and pelvis are being properly supported and protected. In a fall event, a good quality, well-fitted harness can help limit the effects of suspension trauma/ syncope (more on that later).
While incredibly important, fit is just one aspect. Fall protection harnesses are highly engineered pieces of kit and many design features dictate performance, such as appropriate materials for improved fit and speed of donning, or how dirt may affect the webbing (to name just a few). If in doubt about which harness is most appropriate for you and/ or the job at hand then consult with a reputable manufacturer.
Do nothing without training
Making sure your workers have completed a comprehensive training programme is absolutely essential. Not only do employers have a responsibility to provide suitable information, instruction and training for their employees, but training gives those working at height the confidence, knowledge and skills required to carry out their work safely and efficiently. It will also teach operatives how to properly use, care and maintain their equipment.
If you must, be prepared
For many, having followed the hierarchy of fall protection, edge working remains an unavoidable reality. If that’s the case then the steps you take before any work takes place are vital. So, stop, think and ask yourself these three questions: 1. Training, training, training. Have my workers received the very best training for the specific job at hand? Are they as prepared as they can be to work safely and confidently? 2. Am I up to speed with and implementing the very latest legislation and best practice processes? 3. Is the equipment I’m using not only compliant with the relevant legislation, but designed specifically for work in leading edge applications?
Finally, remember, you don’t have to tackle all of this alone. Any reputable fall protection provider – like MSA Safety – is readily available for consultation on any of the above. They will be willing to help guide you on implementing the very best and safest work at height solutions. And at no other time is that more important than when working in leading edge applications.
Visit www.MSAsafety.com to view MSA’s full fall protection range, including training courses.
PSSA Public Sector Sustainability Association
BECOME A CORPORATE MEMBER
The Public Sector Sustainability Association (PSSA) provides a professional association and network for all those working in the Public Sector who have a common interest in sustainability. The aim of the association is to bring together a wide group of people working across all areas of the Public Sector – to help educate, train, support and connect as we work towards a more sustainable future.
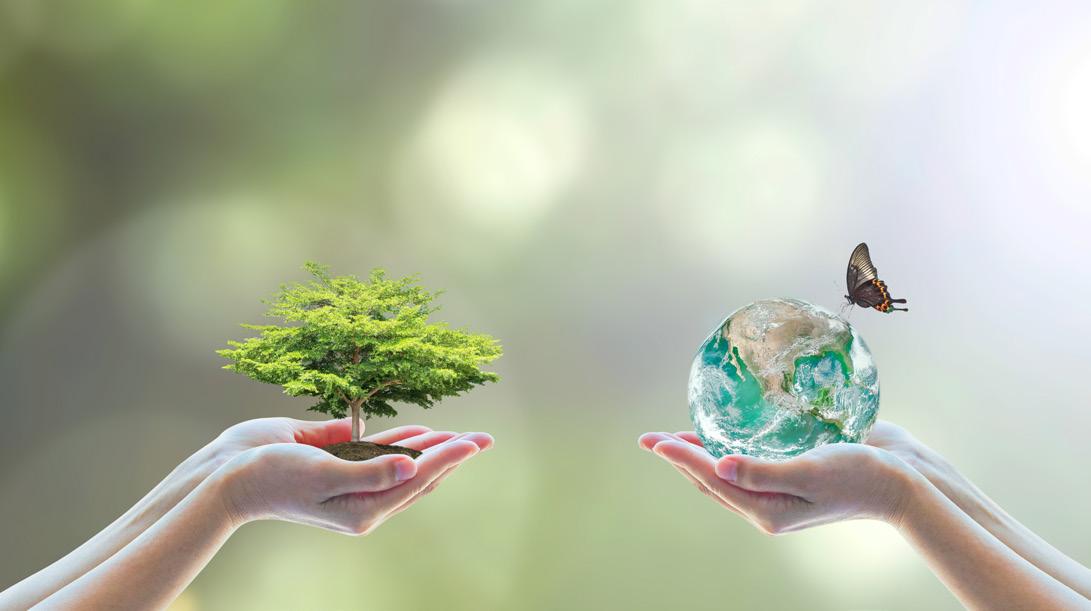
Corporate membership of the Public Sector Sustainability Association is available to any private sector organisation wishing to reach committed and influencial sustainability professionals in Government, Local Authorities, NHS, Education and Housing Associations.
MEMBERSHIP BENEFITS
Comprehensive listing in Suppliers Directory Unlimited opportunity to supply press releases, articles & news to feature on PSSA website One release for inclusion in monthly Newsletter. Logo on PSSA homepage Introductory email sent to our members as the latest Corporate Member to join the PSSA Logo - ‘Member of the PSSA’ to use on your own websites/materials 25% off Website/Newsletter banner advertising 25% off Newsletter sponsorship
WHAT DOES IT COST
The annual membership fee is £495+VAT.
Interested in becoming a Corporate Member of the PSSA? Get in touch today - call us on 01933 316931 or email us at info@pssa.info