
1 minute read
Operational downtime is a significant risk for businesses that ignore their drains, according to new research
from BFM June 2023
Many businesses are prioritizing office refurbishments over drainage maintenance, putting themselves at risk of operational downtime, which is identified as their top challenge.
A recent survey conducted by Metro Rod, in partnership with FMJ, revealed that operational downtime is a major concern for respondents, ranking closely behind material shortages. Staff skill shortages, energy prices, and rising costs are also pressing issues. Surprisingly, in the past year, a significant number of businesses focused on non- drainage-related activities such as lighting upgrades, office improvements, and accessibility enhancements, while less than a quarter invested in drainage or asset mapping. Despite this, nearly one-third experienced drain blockages and incurred drain maintenance expenses. The survey also highlighted the benefits of having a drainage plan. Respondents recognised the advantages of planned maintenance, including minimal operational downtime, improved environmental impact, and the absence of foul smells. However, only 38% had a pre- planned maintenance (PPM) plan, leaving many businesses unaware of the condition of their underground drainage system. Furthermore, a concerning number of businesses only engage with drainage maintenance companies during emergencies or when issues arise, which could lead to forced closures.
How to Avoid Operational Downtime
To avoid operational downtime and its negative consequences, businesses are encouraged to invest in PPM.
This proactive service plan includes routine drainage and pump maintenance scheduled at regular intervals throughout the year. By addressing problems like scale or grease build-up in pipework, PPM can help prevent overflows, blockages, emergency closures, and costly engineer call-outs.
PPM typically covers drain and pipework cleaning, high-pressure water jetting, gully and gutter clearance, urinal descaling, grease trap emptying, interceptor maintenance, shower trap and hand basin trap cleaning, sewage and fresh water pump servicing, and CCTV drain surveys for problem identification.
We recommend a visit from a drainage engineer every six to twelve months depending on the facility usage and site condition.
As Metro Rod operates 24/7, PPM can be scheduled at a convenient time for the customer, reducing disruption to the working day. With engineers available nationwide from over 45 depots within a one-hour drive of 85% of UK commercial properties, Metro Rod’s engineers are never far away.

Businesses face numerous challenges, but operational downtime caused by drainage issues should not be one of them. By proactively investing in an asset map and drain maintenance, businesses can minimise operational downtime and protect their bottom line.
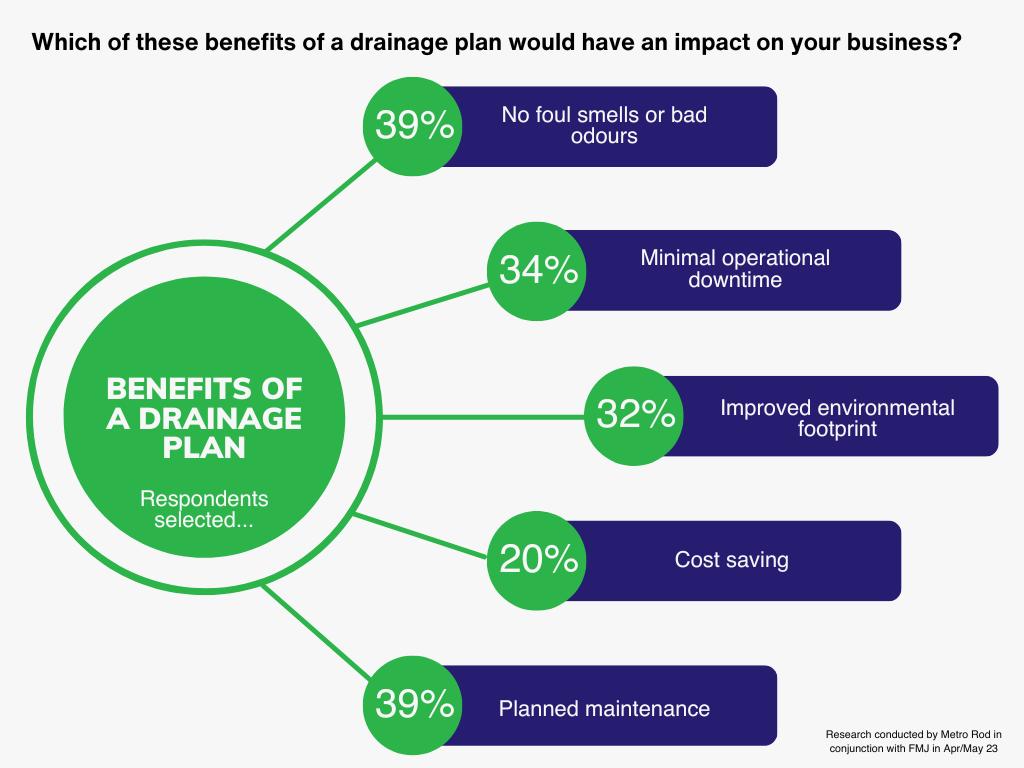
For more information on Pre-Planned Maintenance or how to reduce the impact of operational downtime through drainage solutions, please visit www.metrorod.co.uk