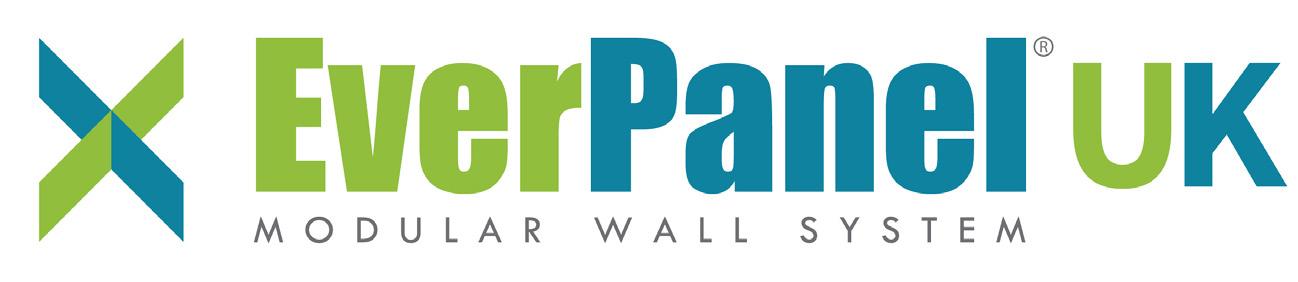
23 minute read
EverPanel Launch Smoothes the Path for Sustainable Public Sector Response to COVID-19 Distancing
Health & Safety
EverPanel Launch Smoothes the Path for Sustainable Public Sector Response to COVID-19 Distancing
A new modular walling system from the creative brand behind the bestselling EverBlock® universal building blocks has launched to smooth the path to sustainability for public sector organisations in a post COVID-19 environment.
EverPanel is a highly configurable, naturally hygienic modular wall system which has infinite applications and can be reused endlessly in all kinds of spaces. The interlocking walls can be quickly constructed to form physical barriers, portion off space for private offices or consultation and treatment rooms, segment offices into socially distanced cubicles and used to delineate traffic flow in public spaces by creating immediate temporary corridors.
A flexible, affordable and above all sustainable solution, EverPanel affords public sector facilities management teams with the wherewithal to make buildings safe for use.
Joe Plosky, Everblock® UK Director said, “EverPanel fibreglass modular panels can be installed in minutes thanks to a proprietary interlocking lug and connector system. They can be used as partitions or deployed to create rooms with doors, sleeping pods, offices, nursing stations, storage areas and divide spaces as required to enable social distancing in a wide range of settings. They are the ideal public sector
solution thanks to their immense flexibility and very quick installation and demounting.”
EverPanel modular walls don’t require drilling or other intrusive installation, meaning the building can continue to be used without disrupting users as controlled areas and social distancing spaces are created. The panels can be moved as needed, reconfigured and deployed in other areas as temporary or permanent solutions on demand, making them incredibly sustainable. The panels can be disinfected and wiped clean after use to maintain good standards of hygiene.
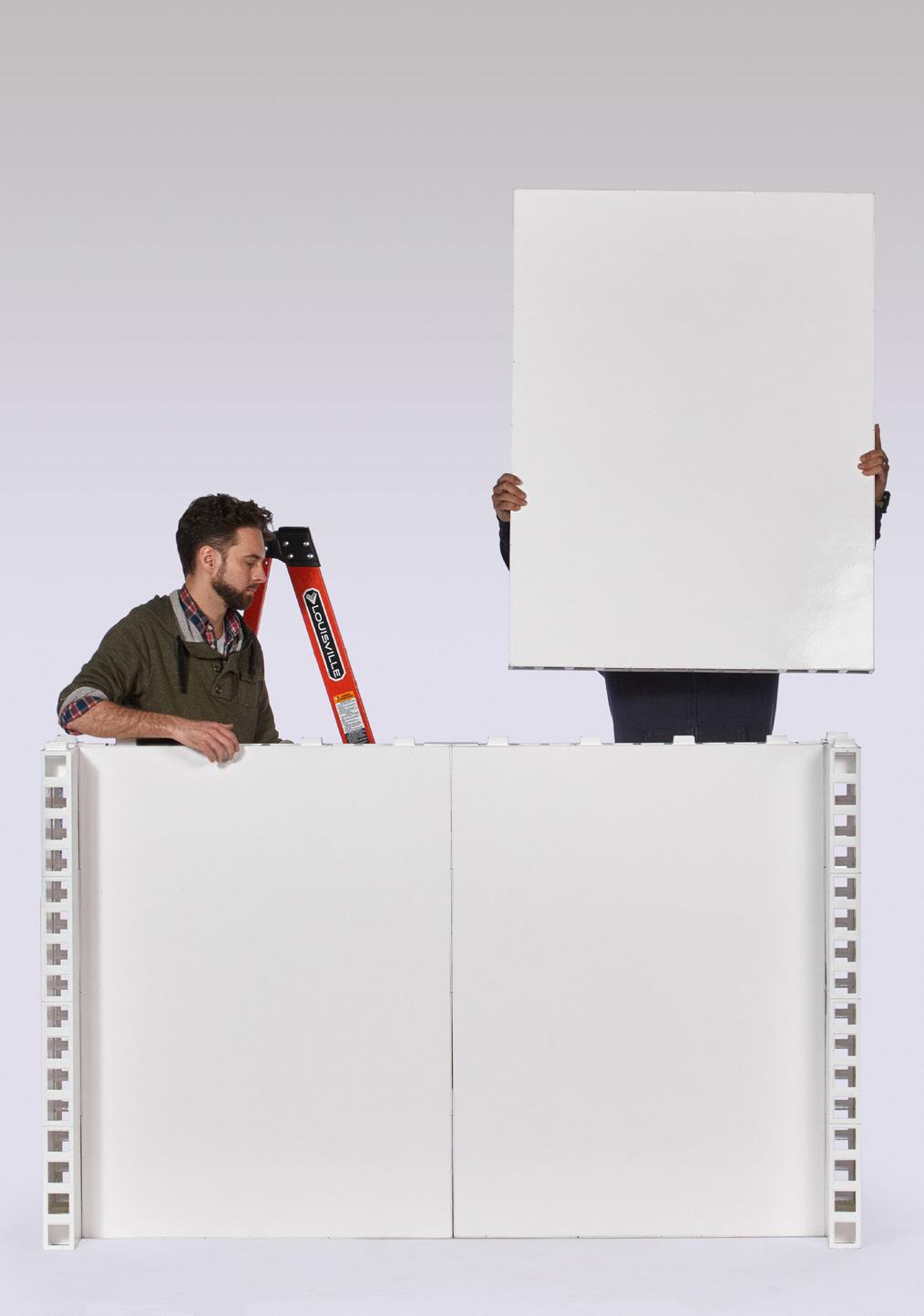
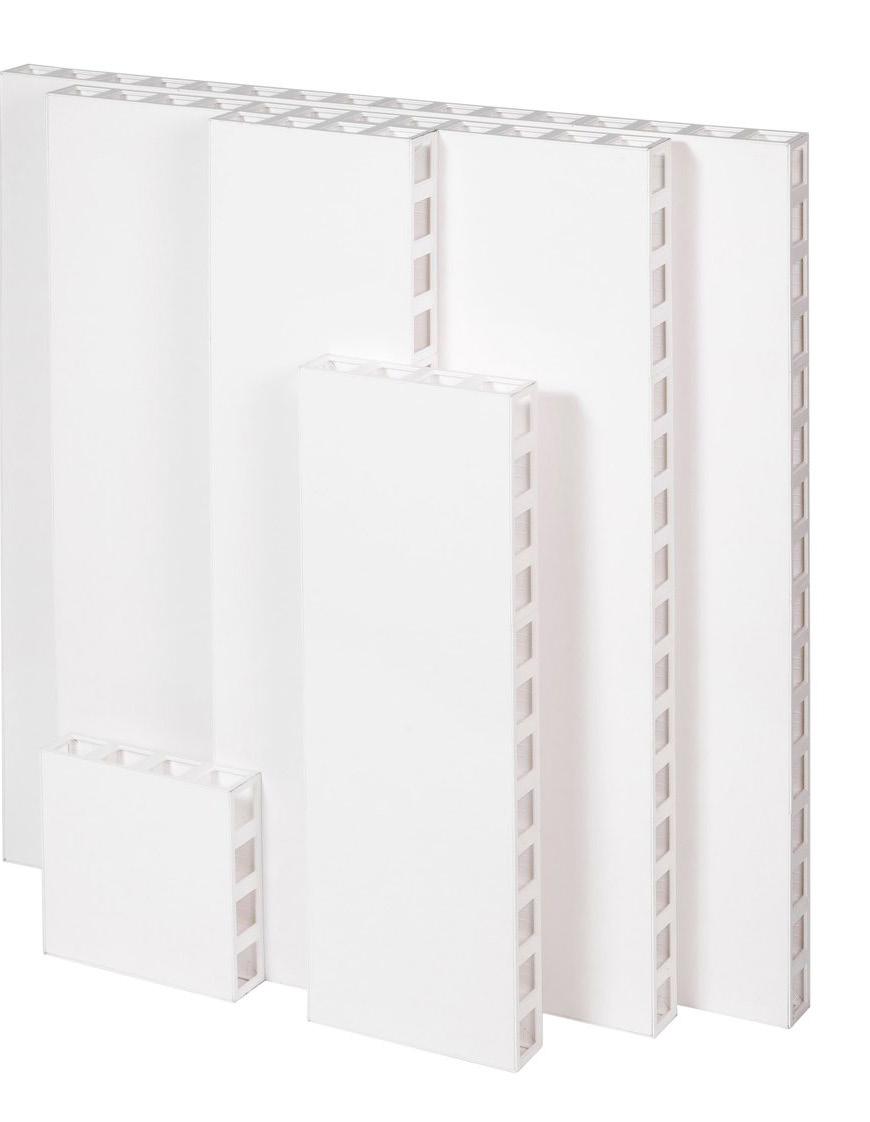
To find out more about EverPanel, visit www.Everpanels.co.uk
Health & Safety
New Beaverswood Flexi-Delineators Keep Warehouse and Logistics Traffic on the Safe and Narrow
A new range of Visusafe flexi-delineators from visual communications specialist Beaverswood, provide improved vehicle routing and pedestrian safety for warehouse, logistics and storage handling applications.
The range provides end-users with a high visibility crush and bend resistant self-righting post system, which can be used effectively to indicate and protect specific zones and areas around an industrial building or complex.
Quickly fixed and secured on either tarmac or concrete industrial floors, the lightweight one metre high flexi-delineators offer improved demarcation and segregation of traffic routes while also minimising impact and costly damage to property, forklift trucks and pallet stackers.
Manufactured from tough 100% recyclable polyurethane for greater flex capabilities and available in a variety of eye-catching colour options with reflectors for heightened visibility in low-light levels and night-time conditions.
Individual posts can be linked together via a strong yet lightweight polymer chain to form a highly visible, impact resistant safety rope-style system. This can be used to guide people quickly through a facility, or prevent them from straying into hazardous traffic routes, providing additional levels of safety and improved pedestrian control.
The 80mm diameter posts are available in a choice of three eye-catching colour patterns for maximum visual impact: yellow with silver reflectors, black with yellow reflectors, and white with red reflectors. Three floor anchors for rapid and secure installation to most industrial floor types, including block substrates, are also provided with every post. More at www.beaverswood.co.uk
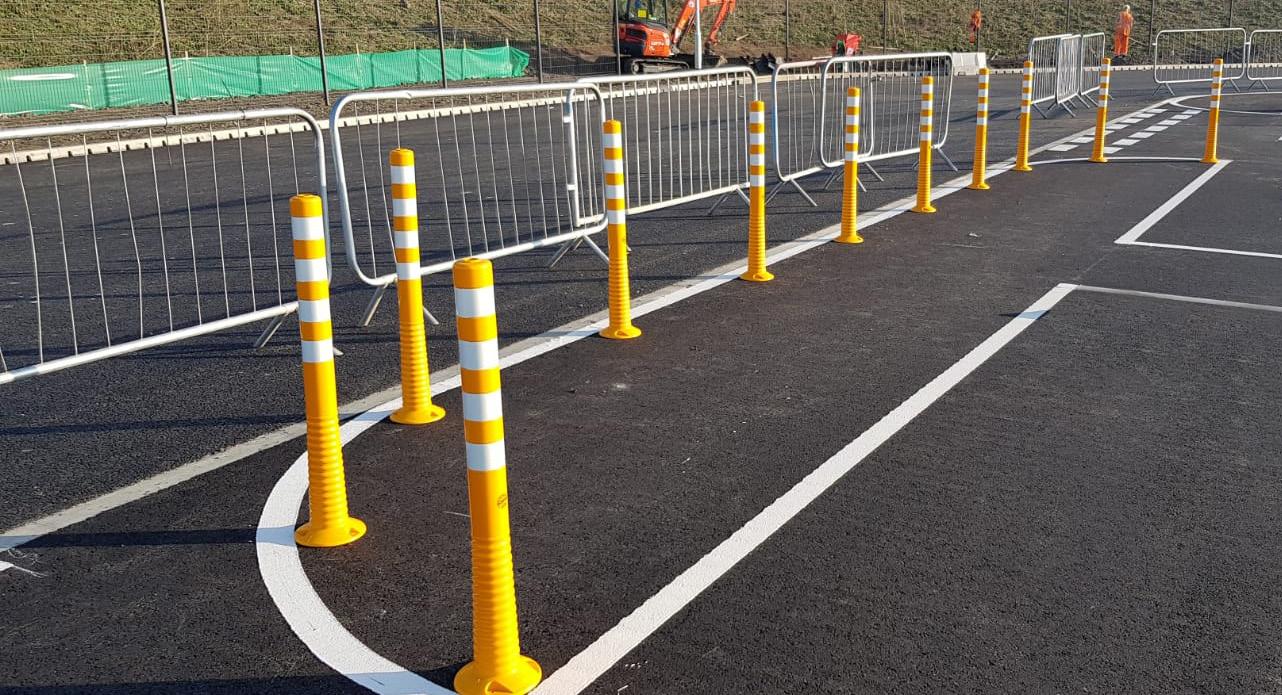

Health & Safety
Extinguishing Fire Safety Myths with Allegion UK
Fire Safety has and always will be a well-documented subject, with various experts and regulatory bodies sharing key insights that save lives. Despite this, practical knowledge can sometimes be overshadowed by false information and myth. Karen Trigg of Allegion UK investigates some common fire safety myths and uncovers the correct way to handle fire safety.
Safety as a wider area has always been one that has courted myth and rumour. Most will be aware of the more amusing health and safety myths, such as the HSE example of children being banned from playing conkers unless they wore safety goggles.
Some of the more classic myths may seem light-hearted and relatively harmless but they are indicative of a much more serious issue that exists, whereby real and practical safety knowledge is replaced with unreliable information. This information is passed from person to person and may not actually be grounded in fact at all. And in a more serious context, such as fire safety, that presents a danger.
Fire safety itself has more than its share of myths and misconceptions too, all proving to be more dangerous than safety goggles and conkers. Treating fire safety knowledge as something that can be shared nonchalantly between one unreliable source to another, rather than learned from credible sources, could put facility managers, businesses and building occupants alike at risk in the event of a fire.
No Smoke Without Fire
With the stakes naturally being so high, fire safety is often shrouded in controversy. Official guidelines and resources are sometimes sidelined and not followed as they should be. But with us all living in a time where information is so easy to obtain, why are those responsible for fire safety decisions still getting it wrong?
Simply put, misinformation is a prominent issue. In fact, the spread of inconsistent and incorrect information mimics fire itself. Commonly, fiction has always surrounded that of fire safety equipment to some extent, and it only takes one to pass that material on for it to result in an unfortunate fire emergency. Some of the more common fire safety myths include: • Once fire safety equipment (such as fire alarms, smoke detectors and even door hardware) is fitted, it no longer requires maintenance. • In the event of a fire, flames cause more casualties than smoke. • The older a building is, the more prone to fire it is. • The gap between the fire door and its surrounding frame isn’t important.
All of these statements are in fact false and dangerous, yet are believed by pockets of
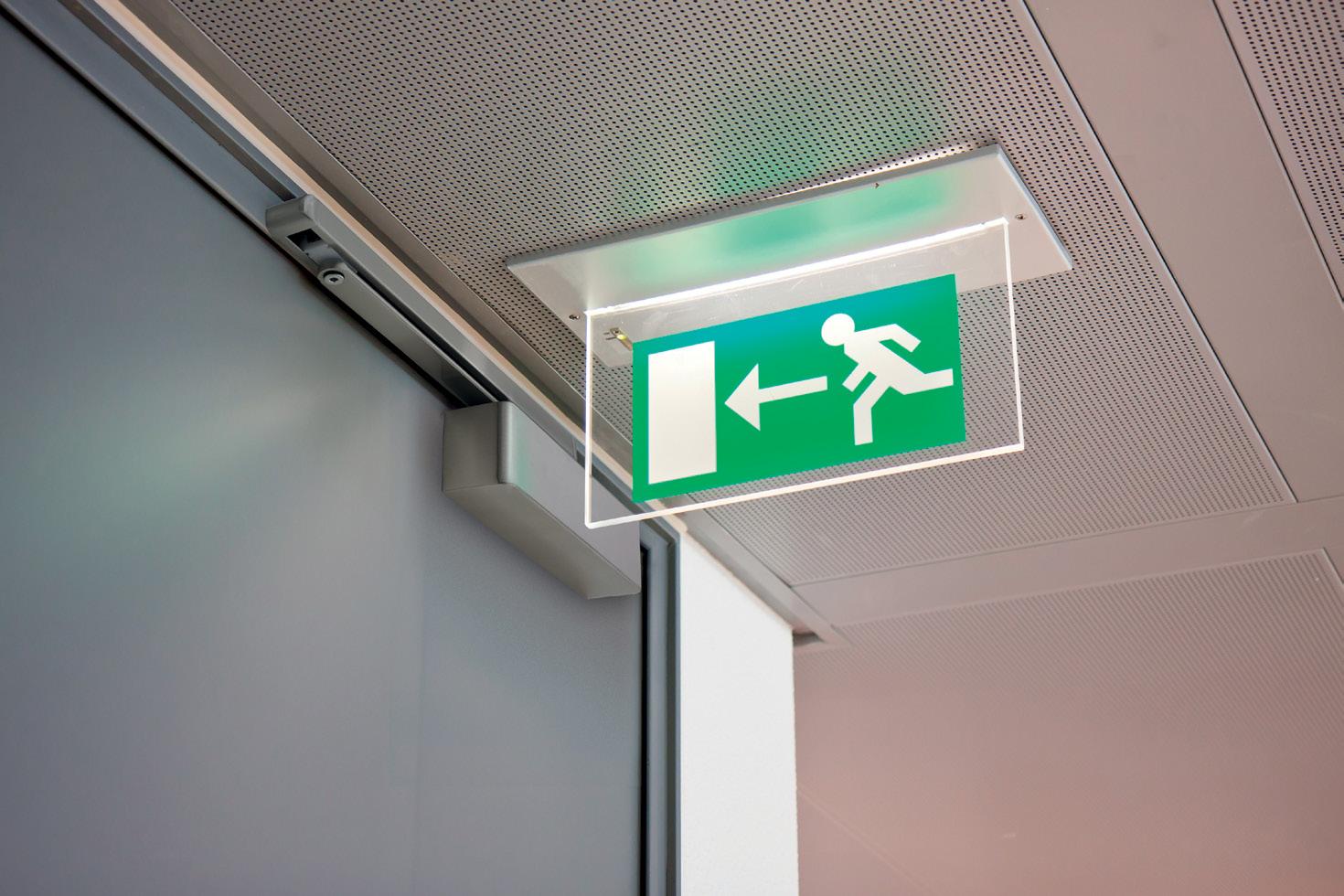
individuals that are subsequently putting their buildings and people’s lives at risk.
One of the more prevalent (and most perilous) fire safety innaccuracies surrounds the use of fire doors and their operation. Under UK law, fire doors can’t be propped or wedged open. Yet, we’ve all seen instances of fire doors being used incorrectly. In the event of a fire, a propped open fire door is useless and will fail to compartmentalise the fire and toxic smoke filling the building, instead facilitating the spread of it.
Some fire safety myths are born purely from convenience, with responsible parties often trying to bend the rules to something that suits the operation of their building. For example, it may be that fire doors slow the movement of people through a building or act as an additional obstacle when items are moved throughout the premises and as a result, they’re illegally left open. Despite the dangers and risk of fines, penalties and prison, a large proportion of people who do so fail to see the safety of occupants as a priority until disaster strikes.
Home Truths
Perhaps this is where a lack of education plays a part in the spread of misinformation. Today, decision makers and installers have a variety of options when it comes to fire door hardware, with tailored options able to adapt to a building’s specific needs.
Electromagnetic door control solutions for example, can be linked to a building’s alarm system with fire doors kept in an open position until the alarm is sounded, fixing potential convenience issues in a safe and sustainable way. By correctly specifying products that suit the use of a building more closely, not only can we educate decision makers further, but there’s an opportunity to significantly increase fire safety standards, too.
For gaps in practical knowledge, such as the process of fire door and equipment checks, industry standard guidelines are readily available from legitimate experts and regulatory bodies. Helpful guidelines and checklists on everything from door hardware to fire safety compliance are also accessible. However, this information must now be used more regularly, replacing the gossip and conjecture that is unfortunately being followed by too many.
With the legal regulations and ramifications at stake, it’s imperative to educate ourselves on a subject that can rapidly turn into a life-or-death matter.
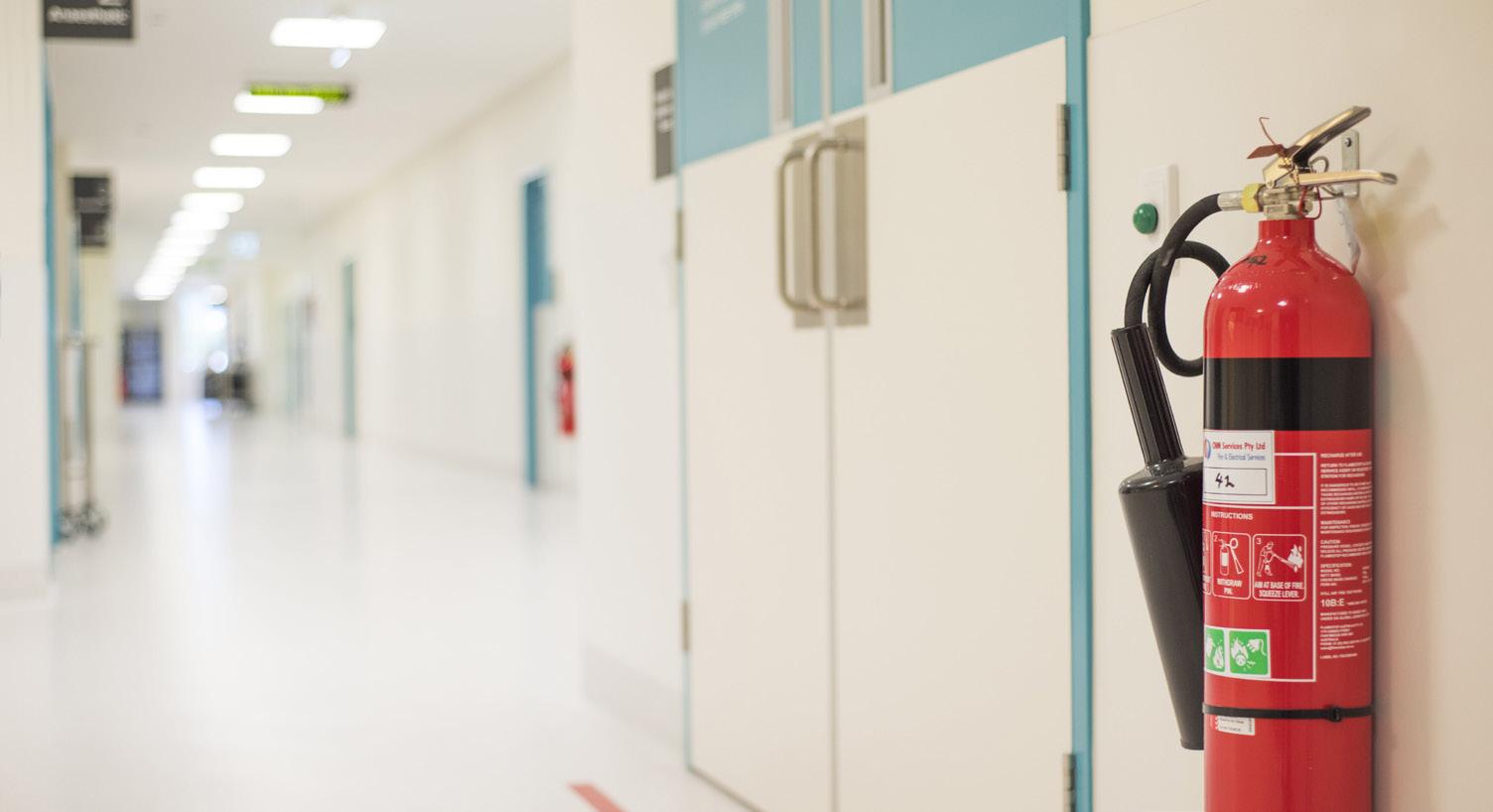
The Key to Fire Safety
Most fires are preventable. By adopting accurate procedures and fire safety practices, decision makers can prepare themselves and their buildings for the worst, creating a safer environment and sharing authentic knowledge on the subject.
Only when we eliminate the ‘corner cutting’ and reduce the potency of fire safety myths can we truly achieve a fire safe future.
For more information on advertising within BFM Magazine, please visit our website or get in touch using the details below:
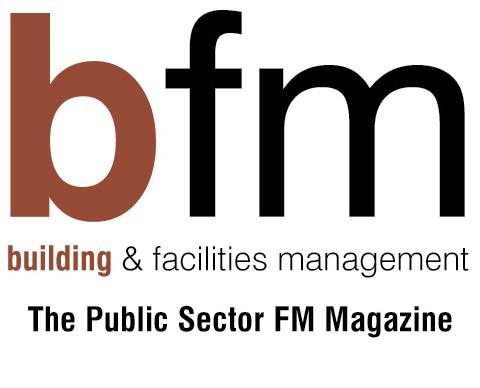
Join the PSSA - Launching the Public Sector Sustainability Association
The Public Sector Sustainability Association (PSSA) provides a professional association and network for all those working in the Public Sector who have a common interest in sustainability. The aim of the association is to bring together a wide group of people working across all areas of the Public Sector – to help educate, train, support and connect as we work towards a more sustainable future.
Never has there been a more pressing need and indeed, requirement for individuals and organisations to turn their attention to sustainability and take stock of their environmental impact on our world.
An increasing number of UK local authorities have declared a climate emergency. But having made this important step, what happens next? Well for many sustainability professionals working within these authorities, they simply do not know. Logically, the first step that can be taken is to develop a strategy to address
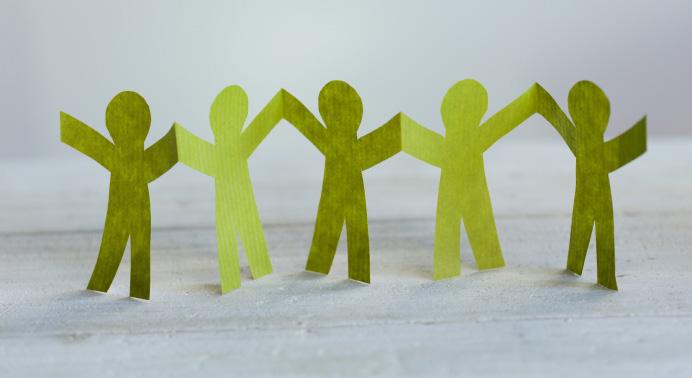
the challenge of the emergency they have declared. However there are a number of pitfalls and issues which can arise when doing so and there is a need for the individuals tasked with creating such a plan to be given the knowledge and support they need to do so.
Similar issues are faced by professionals working in the NHS (the health and care system in England is responsible for an estimated 4-5% of the country’s carbon footprint), Universities, Schools and of course central Government.
Through the PSSA we hope to
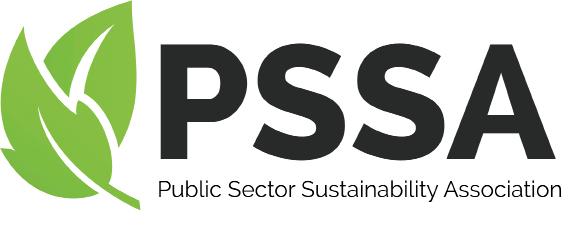
provide these individuals with the support, guidance and knowledge that will assist them and by extension, the entire country in tackling the climate emergency and recuding their organisations carbon footprint. The assocation will provide the latest news and developments, best practice, case studies, white papers, reports and guides to this aim.
There is no charge for membership to those working within the Public Sector and we are now open to new members. If you are interested in joining, please visit our website where you will find more detailed information about the association and also a membership form to join.
www.pssa.info
PSSAWARDS
Public Sector Sustainability Awards
Highlight your commitment to sustainability - become an environmental leader.
The purpose of the Public Sector Sustainability Awards is simple - to promote environmental leadership, to innovate and to inspire all those working in the Public Sector committed to reducing the carbon footprint of their organisation.
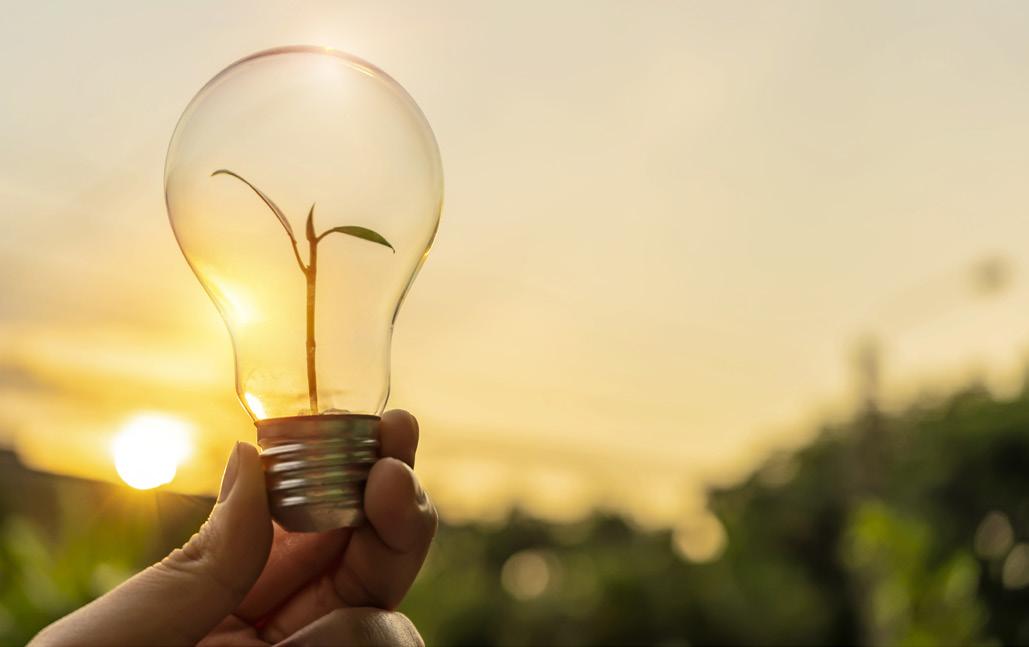
HOW TO ENTER:
There is no qualifying criteria that needs to be satisfied in order to enter the awards. All we ask is that entrants send us up to 2000 words detailing the activities undertaken by them to reduce, by any means, the impact of their organisation on our environment. Please feel free to attach any images, graphs, charts etc to support your entry.
You can focus your entry on just one project or multiple schemes. You can enter as an individual or on behalf of your organisation, or both, as there are awards for both categories.
There is no charge for entry.
If you wish to enter, please complete the registration form at www.pssa.info/pssawards or download the form from the website, complete it and email it back to us. Your completed entry needs to be submitted by the 31st January 2020 and should include images and/or logos.
Please send your entries through to submissions@pssa.info.
If that is not possible, you can mail them to:
PSS Awards, 42 Wymington Park, Rushden NN10 9JP
Health & Safety
When is it time to replace your lift?
Nothing lasts forever. Whether it is our phone, laptop, washing machine or car, there will come a time when it needs to be replaced. In some cases, that may be if a new model, style or feature becomes more desirable. In others, such as a car, it may be before the level of depreciation becomes too great. Irrespective of the reasons, at some point every piece of electrical or mechanical equipment will reach the end of its serviceable life and a decision will need to be taken as to what to do next.
Lifts are no different. It is easy to take one for granted, most users will never see anything other than the interior decoration, pushes and displays. Yet throughout its life, mechanical and electrical components within the lift system will make hundreds of thousands, in some cases millions, of operations. Like any other machine, those components will eventually age, wear and expire. The major difference between your lift and your phone of course, is the price of replacement.
So how do you know when a lift has reached the end of its useful service life? After all, a lift may look perfect from within the car. But unlike a car, it’s not possible to simply look under the bonnet. Whilst there isn’t a simple answer, there are some guidelines that will help you to determine the remaining life of your lift.
There isn’t an absolute maximum or minimum lifespan for a lift. The Chartered Institution of Building Services Engineers (CIBSE) suggests within their Guide D to Transportation systems in buildings, that the typical life of a lift can be between 20 and 25 years for an electric traction lift, and approximately 15 years for a hydraulic lift. However, it also warns that light duty cheaper equipment can last as little as 10 years. This is important to remember, as a large number of residential buildings, even those marketed at the upper end of the price range, will often feature the most lightweight and basic of equipment. Unfortunately, the average user will see little difference between a high end and value engineered package so it will be difficult to determine, simply from looking at your lift, whether you have a reasonable product installed. Although, the original duty type or manufacturing quality of your lift will not be the sole factor when determining its expected service life. Other factors such as the quality of installation and subsequent maintenance and level of use (and sometimes more importantly, misuse) can all play a part. It is, therefore, important to look at all aspects of your lift installation before coming to a decision on its future.
So where to begin? Well, as suggested above, it is not unreasonable to expect to get at least 10 years from even the most lightweight of lifts. If you are experiencing problems before this time, it is likely that there could be an issue at play that is not simply related to age. After 10 years we would suggest that at least some consideration be given to the long term future of your lift. That is not to say that immediate replacement is necessary. But the financial cost of lift replacement, or even full modernisation, can be high - often in excess of £100,000. So, it is worth starting to plan for the replacement at an earlier stage, and not be caught when the inevitable happens.
Whilst there often isn’t a single sign that your lift is in need of replacement, there are clues that, when added together, could give some indication that attention is needed. Age is certainly one of those. Any lift that is over 15 years is certainly reaching the later years of serviceable life. It is possible that some work may have already been required by this time to ensure the continued operation of the lift, and this could have already resulted in a significant outlay. Certainly, by 15 years, there is a real chance that some components on the lift may no longer be supported, and this can include key equipment such as the control system, which can cost from £25,000 to replace.
Reliability is another good indicator. A lift that develops multiple or regular faults, especially if it has historically been reliable, could be suffering from worn or ageing components that require replacement. While this could simply be down to maintenance, it should be viewed in conjunction with other indicators as a possible sign of a lift reaching the end of its useful service life. When a part does fail, the availability of spares and replacement parts can also be a useful guide. Equipment that is no longer supported will often require replacement of an entire unit, rather than simply the broken part, due to it no longer being supported by the original manufacturer. This can result in higher costs to the client, as well as extended downtime while the new equipment is sourced and fitted. While the new component may result in an improvement in reliability, it rarely improves longevity of the lift as a whole.
As a consequence of the above, the cost of maintenance can often increase with older lifts, with the lift contractor increasing the premium to match the risk associated with a less reliable lift. This is particularly applicable to comprehensive contracts, where the maintenance provider will bear some of the risk when replacing parts. It may be that the maintenance provider will want to exclude some parts due to their age, level of wear, or obsolete design.
A final warning signal can often be provided by the number of unsolicited quotations received from your maintenance contractor, or the number of items found on the latest LOLER inspection report. These can often be health and safety related and can indicate revisions of health and safety legislation or standards. While they may not always require mandatory improvements to your lift, they can be an indication that your lift is beginning to fall behind on current design and health and safety standards.
None of these signals will, in isolation, point to your lift requiring immediate attention. However, a pattern of some, or all of the discussed issues could mean that it is time to consider improvements to or replacement of your lift, before the cost of maintaining it becomes excessive. If you are unsure as to whether your lift is reaching the end of its serviceable life, ILECS offer a full range of inspections and surveys to help evaluate the condition, health and safety and quality of maintenance on your lift. Speak to one of our consultants today on: 01206 399555 or email us at: info@liftconsultants.com
Health & Safety
What you need to know about working in leading edge applications
Despite steady progress, falls from height remain a common cause of injury and death across Europe. This is why regulations surrounding fall protection equipment exist and are regularly updated – to help ensure manufacturers meet certain standards. These regulations, and the associated standards that manufacturers of fall protection equipment must meet, are important when working in leading edge applications.
In this article, Tim Bissett, Technical Manager for Fall Protection at MSA Safety looks at the relevant standards relating to leading edge work; what to look out for in the equipment you use; and what processes you need to have in place, including the vital importance of a rescue plan.
Tim has been Technical Manager for the Latchways® Engineered Systems range for 18 years. Part of his role is to contribute to the development of product standards for PPE. This involves looking at product testing methods and systems and evolving standards to meet changing industry needs. He is a member of the BSI Technical Committee PH/5, from which he convenes two working groups for CEN/TC 160.
What is leading edge work?
“Leading edge” work or “edge working” is defined as working at any unprotected edge of a platform, floor, or other construction point where there’s a risk that the lifeline a worker is using may come in contact with an exposed edge, or edge of the working surface. In many scenarios, leading edge applications occur when a worker is connected to an anchor point below their back D-ring, although it’s also possible when anchor points are above this position.
Work in leading edge applications presents its own unique challenges and safety hazards; one of which is the greater risk of lifelines being frayed, cut, or severed on impact with the edge in the event of a fall. This is complicated further should the worker swing after falling, creating a pendulum-like motion. The friction this causes can increase the likelihood of the lifeline being cut or severed.
These potential risks place a sharp focus on testing criteria
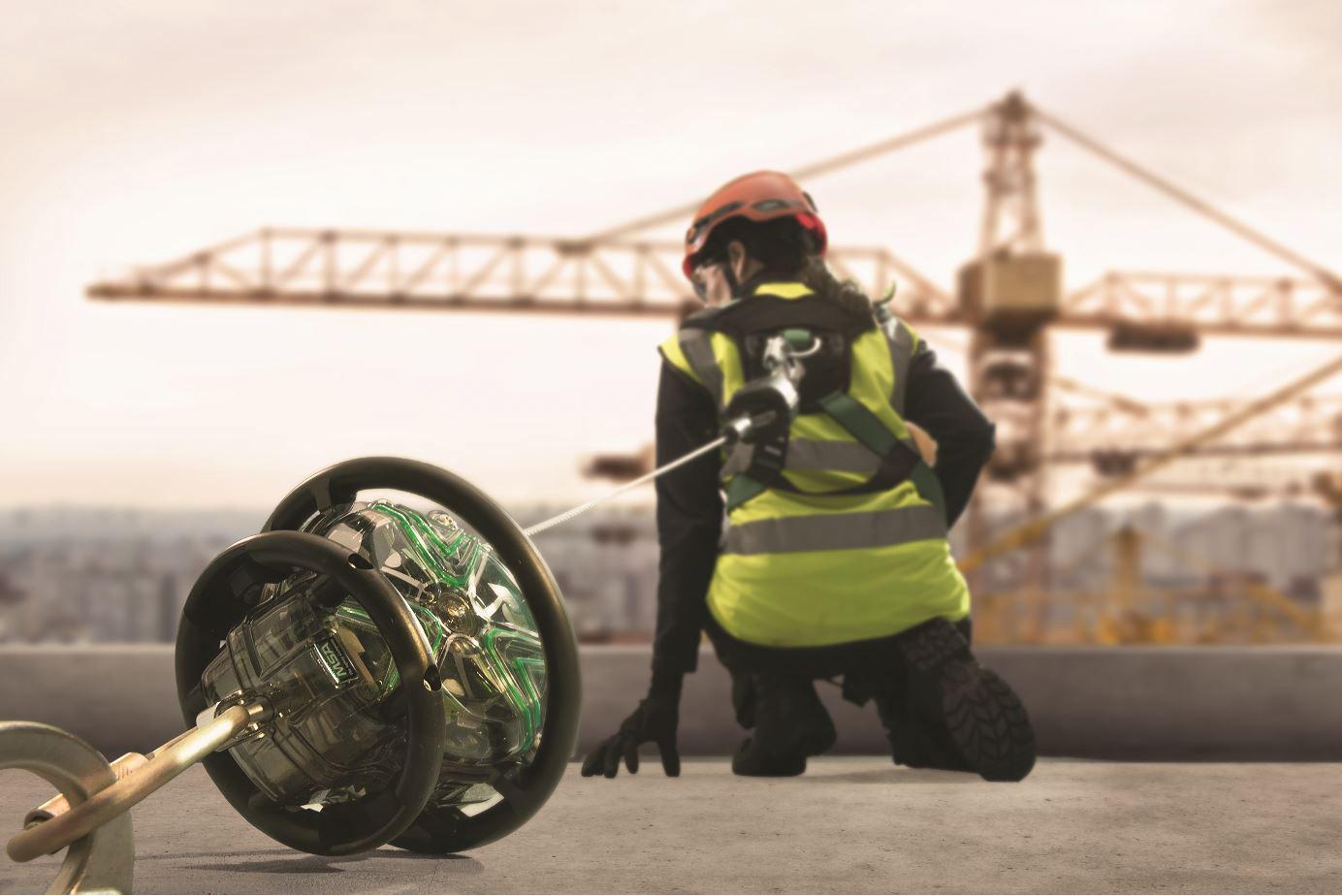
within relevant standards, following best practice and choosing the right equipment for the job. Let’s start by looking at the standards you need to be aware of.
Standards relating to leading edge work
First things first, before any leading edge work takes place, check that the equipment you’re using adheres to the relevant standards. We appreciate that these standards can seem complex, so we’ve broken them down below.
PPE Regulation (EU) 2016/425
These regulations, which were first introduced in 2018, imposed additional requirements on manufacturers of PPE, including an assessment of the risks against which the PPE is intended to protect and changes in requirements for product marking. It’s vital that purchasers of PPE take steps to ensure that their suppliers meet these new regulatory requirements. You can do so by looking out for the CE marking affixed to PPE. This provides evidence of compliance with the applicable EU legislation.
EN 360 and CNB/P/11.060
This standard (EN 360:2002), relating to retractable fall arrest devices, is currently under revision and is expected to be out for review shortly prior to publication. It is likely, given their increasing popularity, that an updated standard will encompass twin-legged, as well as singleunit retractable devices. Be mindful that overhead or traditional SRLs meeting the requirements of EN 360:2002 are not necessarily designed or rated to arrest a fall over an edge. Necessary steps should always be taken to select the absolute right equipment for the job at hand.
CNB/P/11.060 is a coordination document associated with EN 360:2002. It outlines the testing criteria for the use of SRLs in leading edge applications, specifically how SRLs must carry evidence of dynamic performance, dynamic strength, and static strength within a leading edge application with the retractable lifeline stressed over an edge. Adherence to this coordination document and the testing criteria within it are central to mitigating the potential risk of lines fraying or being cut in the event of a fall.
First port of call: hierarchy of fall protection
Typically, fall protection is associated with saving a worker’s life in the event of a fall. And while this isn’t strictly wrong, it’s not the ideal scenario either. The hierarchy of fall protection helps to prevent a worker ever getting into a situation where they could fall by prioritising various applications from “most preferred” to “least preferred”. Leading edge applications will inevitably mean working in fall arrest – the “least preferred” option. It’s not something to take lightly and should always be a last resort, taken only once the first three options outlined below have been explored. 1. Hazard elimination. This means the removal of the hazard by designing it out wherever possible. It’s the “most preferred”, safest option. If there’s no hazard, there’s no fall. 2. Collective (or passive) fall prevention. This defines products that prevent access to a fall hazard. A guardrail, for instance, acts as a physical barrier between the worker and the hazard. 3. Fall restraint. If working in fall restraint then there is no barrier between the user and the fall hazard. Instead, they’re using fall protection equipment – harness, lanyard, and anchor point – that will not allow them to reach the hazard. For example, a worker who is working in fall restraint may use a six metre lanyard to connect to an anchor point at least seven metres away from the fall hazard. 4. Fall arrest. This defines equipment designed to catch (or “arrest”) the worker in the event of a fall. This is the “least preferred” option because arresting a fall exposes the worker to significant forces, putting them at risk of physical harm. Rescuing a fallen worker (which we’ll come onto a little later) can also be a challenging and potentially dangerous process.
Let’s take a look at some key things to consider if – after following this hierarchy – edge working remains the only option available.
Choosing the right harness for the job
First things first, all harnesses on the market should be compliant in accordance with EN 361:2002. That’s a given. But a good harness – one that’s comfortable, doesn’t restrict workers’ movement, and mitigates impact on the user’s body in the event of a fall – goes beyond mere compliance.
Fit is fundamental to achieving this. Leg and shoulder straps should be easily adjustable for a comfortable, snug fit. The user’s finished position in a fall scenario should be heads up and slightly forward-leaning. This is important for correct distribution of load through the leg straps and load through the body, such that the spine and pelvis are being properly supported and protected. In a fall event, a good quality, well-fitted harness can help limit the effects of suspension trauma/ syncope (more on that later).
While incredibly important, fit is just one aspect. Fall protection harnesses are highly engineered pieces of kit and many design features dictate performance, such as appropriate materials for improved fit and speed of donning, or how dirt may affect the webbing (to name just a few). If in doubt about which harness is most appropriate for you and/ or the job at hand then consult with a reputable manufacturer.
Do nothing without training
Making sure your workers have completed a comprehensive training programme is absolutely essential. Not only do employers have a responsibility to provide suitable information, instruction and training for their employees, but training gives those working at height the confidence, knowledge and skills required to carry out their work safely and efficiently. It will also teach operatives how to properly use, care and maintain their equipment.
If you must, be prepared
For many, having followed the hierarchy of fall protection, edge working remains an unavoidable reality. If that’s the case then the steps you take before any work takes place are vital. So, stop, think and ask yourself these three questions: 1. Training, training, training. Have my workers received the very best training for the specific job at hand? Are they as prepared as they can be to work safely and confidently? 2. Am I up to speed with and implementing the very latest legislation and best practice processes? 3. Is the equipment I’m using not only compliant with the relevant legislation, but designed specifically for work in leading edge applications?
Finally, remember, you don’t have to tackle all of this alone. Any reputable fall protection provider – like MSA Safety – is readily available for consultation on any of the above. They will be willing to help guide you on implementing the very best and safest work at height solutions. And at no other time is that more important than when working in leading edge applications.
Visit www.MSAsafety.com to view MSA’s full fall protection range, including training courses.