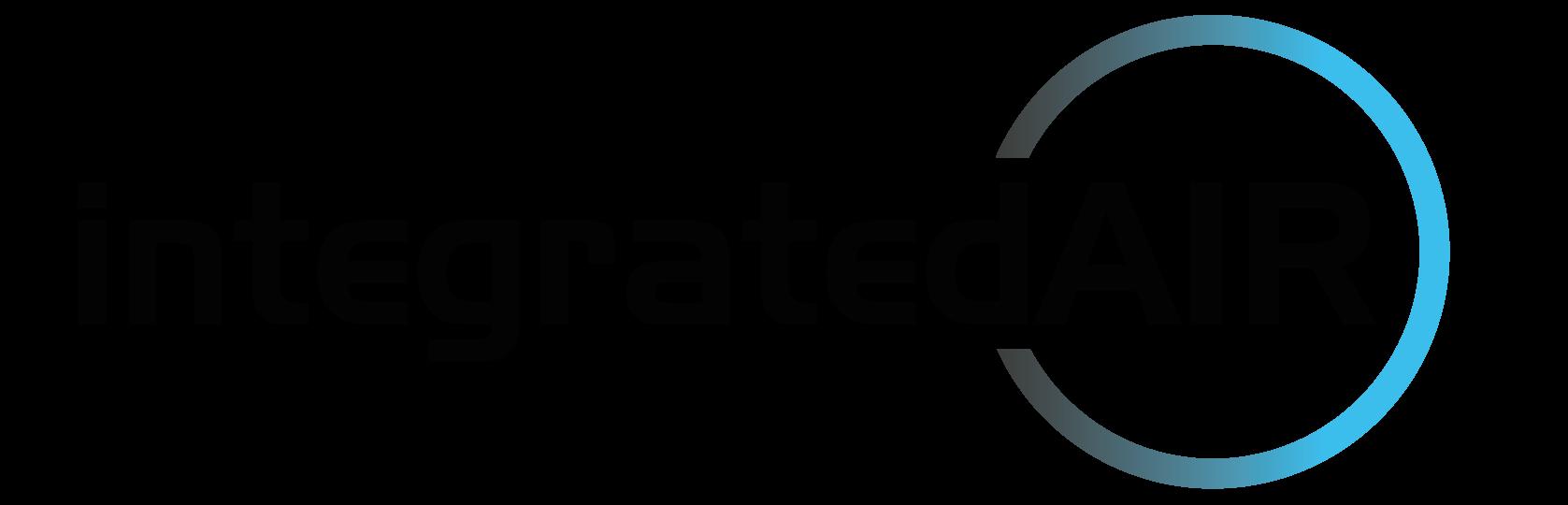
8 minute read
DUST CONTROL
WHY YOU NEED DUST CONTROL IN BULK SOLID HANDLING
Whether to prevent product loss or avoid health risks for operatives working in your production facility, managing and controlling air-born dust particulate is vital whenever bulk solids are handled. It is essential to control respirable dust to prevent health hazards for your operatives and should be regarded as a priority. Correctly designed dust control or LEV (Local Exhaust Ventilation) will protect your employees and ensure your production and processing facilities comply with legislation.
WHY DUST CONTROL IS CRUCIAL
Apart from preventing the issues of workers being exposed to hazardous dusts and product loss, uncontrolled airborne contaminants can: • Produce cross contamination issues to a production process • Increase worker absenteeism • Reduce equipment reliability leading to an increased level of breakdowns • Increase the combustion risk within a production facility • Increase the plant cleaning requirement • Create additional slip hazards • Increase the risk of costly litigation both in the short and long term
These issues can all be addressed with correctly designed LEV, helping to provide a safer environment in which to work, protecting both businesses and employees.
When applying dust control within the United Kingdom, legislation such as CoSHH (Control of Substances Hazardous to Health) and EH40 (which details the numerous dust levels acceptable within a production facility) must be considered. LEV systems should be designed following HSG258 guidelines giving advice on the effective design, commissioning and testing of LEV systems.
WHAT ARE YOUR SPECIFIC DUST CONTROL NEEDS?
Every production facility has its own unique LEV requirement. When enquiring about the purchase of a dust filter unit/LEV system, it is helpful to know; • The type of dust that your industrial process generates. This includes the products themselves and the particulate size (e.g. is the product in the form of lumps, granules, pellets, powder, etc.) • Understanding how much dust is created. This includes determining the plant operation (e.g. is production 8hr per weekday or 24 hr production 7 days per week, etc.) The type of dust generation is also an important factor to consider (e.g. intermittent sack tipping through to a continuous production process, etc.) Estimating the type and level of dust generated affects the type of filter unit, the filter unit size and the dust collection/discharge arrangement. • Determining the air volume that is required to provide effective dust control. This affects both the filter and fan sizes. • Establishing whether or not your dust is potentially explosive. If your dust is potentially explosive, your dust extraction filter unit must comply with DSEAR (Dangerous Substances and Explosive Atmosphere Regulations) and the ATEX Directive. The Kst value (the rate at which a given dust will explode, measured in Bar.m/s) must be determined to size the explosion protection system correctly.
Knowing these elements will help ensure that your LEV system will be designed to meet your unique requirements and help you make a more informed decision in choosing the right dust collector for your needs. integratedAIR Filtration can help you choose the most efficient filter from their BlueClean® range. They have years of experience in the industry, so rest assured that you are in good hands. Whether you are looking for a customised dust extraction filter unit or a full turnkey system, integratedAIR Filtration can help to provide your LEV solution.
MODU-KLEEN® DOWNDRAFT SERIES DUST COLLECTOR
The Modu-Kleen® downdraft dust collector represents the latest dust collector technology developed by Dynamic Air to contain fugitive dust. With the new Modu-Kleen downdraft dust collector, the air enters at the top of the dust collector housing and flows downward to the cartridge filters, improving the filtering process and the material-to-air ratio. Air velocities are much lower than those with a conventional dust collector, reducing the load on each filter cartridge and extending filter life. Cartridge filters are positioned horizontally, requiring less floor space and making filter removal easier.
Personnel never have to enter the filter housing for general maintenance or for cartridge filter removal. This provides a much safer and quicker method of filter removal. For fast and easy inspections, a large, quick-opening door allows maintenance personnel to closely inspect each cartridge when required. In addition, any single cartridge can be removed without disturbing adjacent cartridges. Also, each cartridge filter has a unique built-in quarter turn bayonet mount, so no tools of any kind are required for cartridge removal.
https://www.dynamicair.com/products/ dustcollector681.html
Dynamic Air Ltd. Milton Keynes, United Kingdom +44 1908-622344 E-mail: sales@dynamicair.co.uk www.dynamicair.com
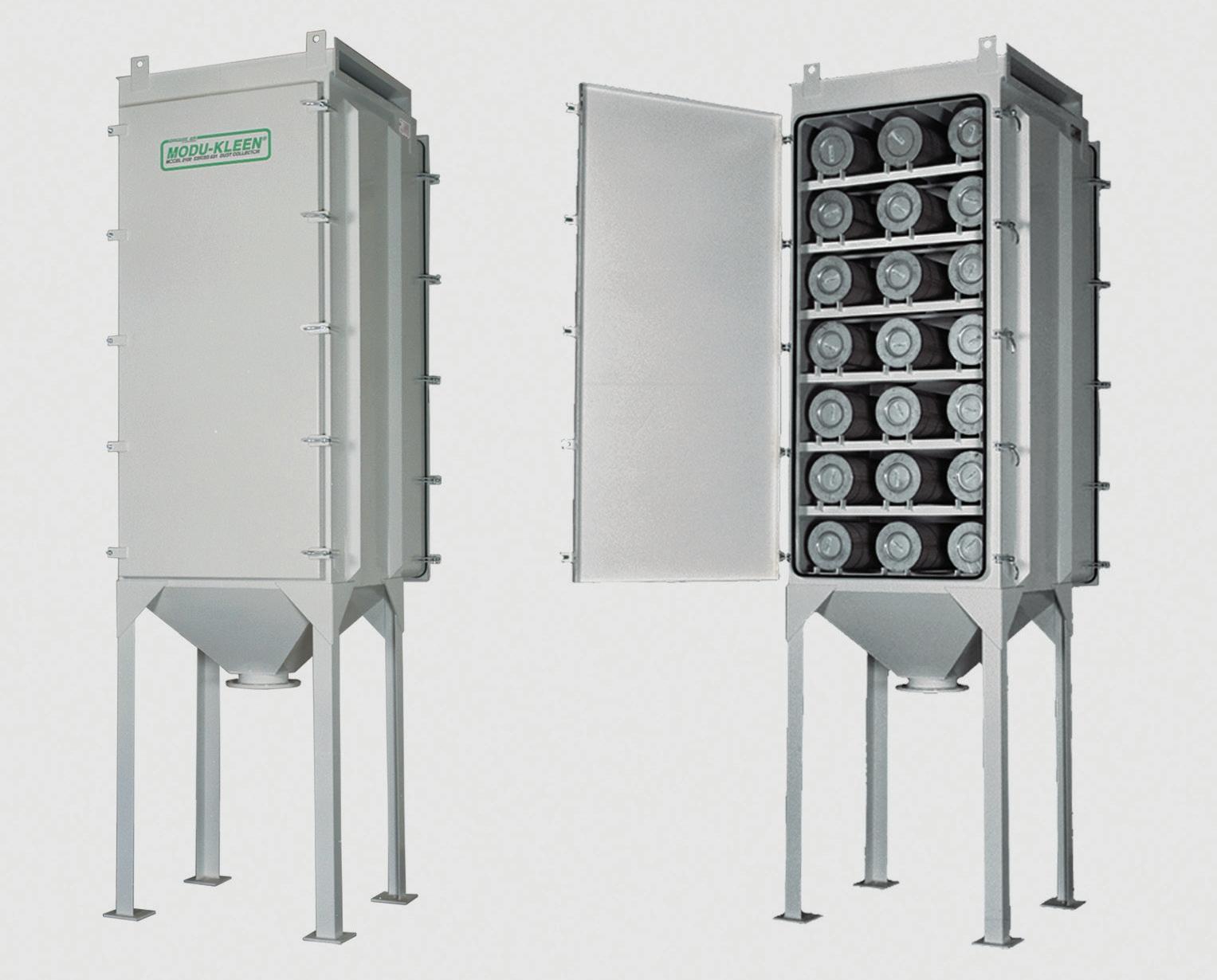
FOOD PROCESSORS GRAVITATE TOWARDS GRAVITY
The popularity of Fortress Technology’s Gravity Stealth metal detectors continues unabated. A critical part of most food production processes, inspecting and removing metal contaminants in upstream free-falling dry applications, Fortress draws attention to several recent enhancements designed to advance productivity, enhance safety and maintain HACCP compliance in the busiest of food factories.
With productivity being such a critical measurement of output per hour, machine uptime on any fast moving gravity inspection line is critical. Custom manufactured to accommodate different food factory layouts, including mezzanine floors, ceiling mounts, between product chutes and hoppers, and even integrated alongside a checkweigher, the Fortress Stealth Gravity metal detector is packed full of useful labour and time saving features. Including digital automatic testing to eliminate production downtime, plus accurate, high speed reject capabilities.
Offering best-in-class detection of magnetic and non-magnetic metals, Fortress Gravity Metal Detectors are increasingly an everyday sight on flour, rice, cereal, sugar, powder and grain production lines.
“There is always value to be gained from adding upstream detection systems to most processes,” explains Fortress Commercial Manager Jodie Curry. “Machines upstream often makes it easier to detect contaminants, trace to their source and potentially alert staff to equipment failures before they become catastrophic and potentially trigger huge recalls.”
Scanning raw materials as ingredients come into the factory is prudent for many reasons. Although in most instances these ingredients would be inspected by the supplier, a reinspection will help to doubly ensure that suppliers are complying and hold them accountable for ingredient quality, reaffirms Jodie “Of course, the most notable benefit is preventing metal from entering the production process in the first instance. Rejecting at the end of the line is typically the most expensive phase.”
For hazardous locations, such as flour factories or chemical plants where the application presents a combustible explosion risk, Fortress supplies clear ratings to meet the defined danger standards. Always mindful of real factory conditions, the robust Gravity Metal Detector is built to be sturdy and stable enough to withstand vibrations and temperature changes without compromising performance.
Available in a selection of food-grade anti-static aperture in-feed pipe sizes, including 75mm, 150mm and 200mm, Fortress Gravity Metal Detectors apply powerful Digital Signal Processing technology to identify the smallest of metal fragments. Operatives are instantly alerted to any detection by an audible and visual alarm. A reject confirmation alert verifies that the reject device has operated correctly during every reject.
AN EASIER CLEAN
To remove metal contaminants from good product flow, most Fortress customers now specify the
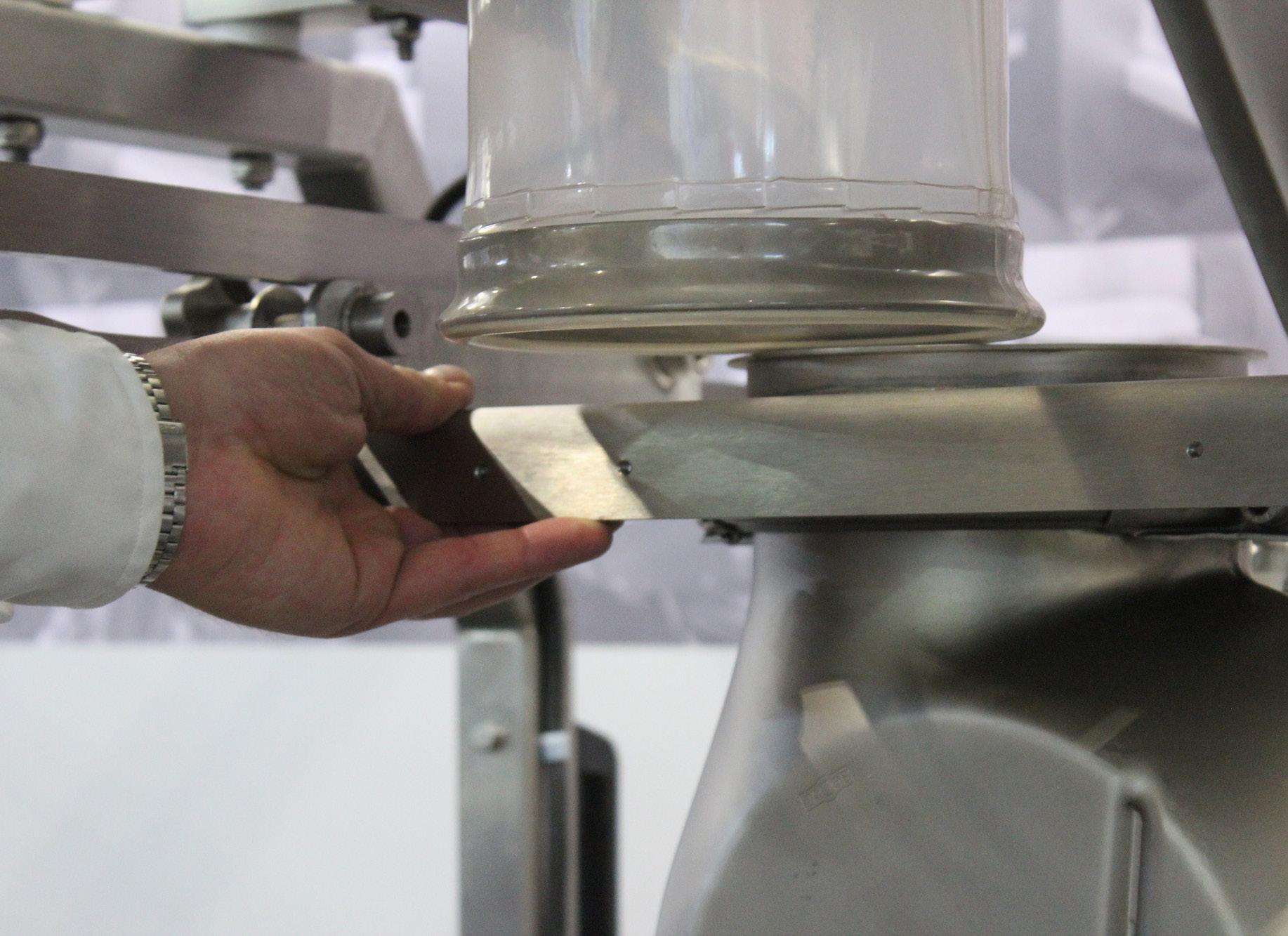
company’s new retractable easy clean diverter valve reject system. IP69Krated, rather than tubular supports or struts, the new Fortress Gravity design features open supports and fewer welds. Making it easier to identify potential areas where product material can accumulate, and much faster to sanitise. Overcoming another longstanding challenge with Gravity systems - gaining access to the enclosed flap-style reject mechanism and removing from service for deep cleans and maintenance – Fortress has engineered a retractable reject unit. By placing on a carriage, processing operatives can quickly disconnect, gain access to working parts, clean and slot back into place, with minimal business disruption.
Average clean times now take operatives a matter of minutes. Jodie confirms: “With open areas and smoother surfaces, operatives can now access and clean their Gravity Metal Detectors much faster. Not only does this reduce machine downtime, it also speeds up the changeover process from one application to another.”
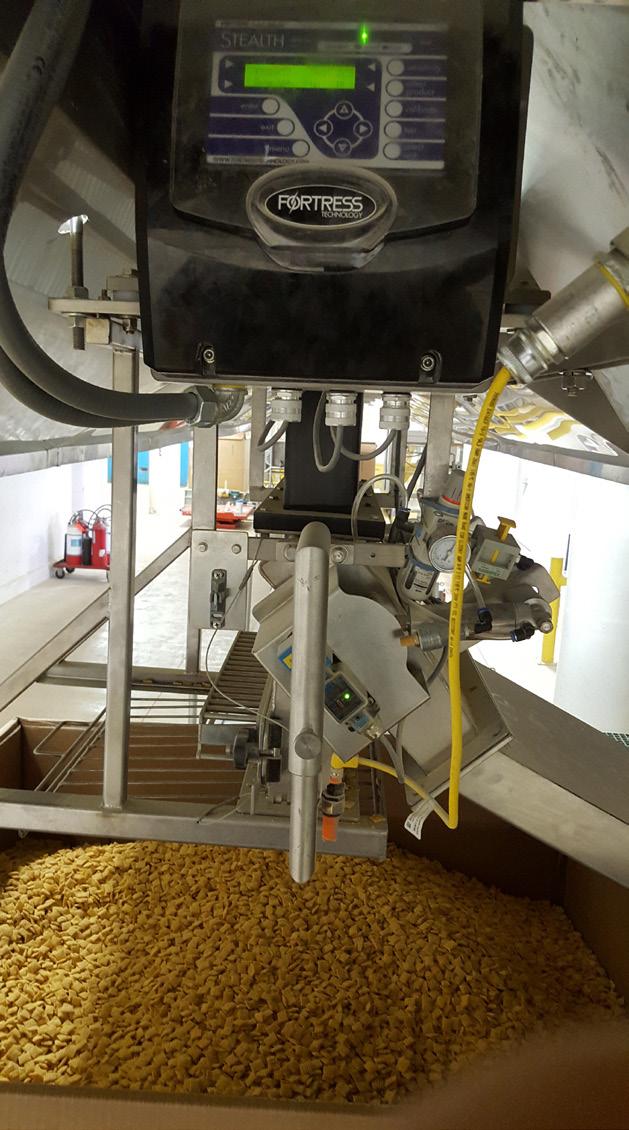
SAFETY AT HEIGHTS
To successfully comply with application-specific production standards, food processors also need an appropriate and effective testing system. Defined by the audit process of industrial metal detectors and the criteria set out by each retailer Code of Practice (COP), tests are typically scheduled throughout the day at hourly intervals to confirm the inspection system is repeatedly identifying all potential metal contaminants.
Manually performing these regular tests on Gravity Metal Detectors can be especially time consuming. The degree of accuracy could also be considered questionable. Mainly due to challenges of accessing machinery positioned at height. “It is virtually impossible to time and again replicate a metal contaminant passing through the exact centre of the product flow within the aperture in free flowing applications,” notes Jodie.
“One of the biggest pitfalls of manual testing in Gravity applications is dropping the test sample from a height, through the centre of the product flow where the signal is the least sensitive,” she highlights. With many Gravity metal detectors located near product silos above production lines, climbing up to perform this task manually is usually a two person job and brings with it some significant safety risks.
To solve this dilemma, Fortress created Halo Automatic Testing. An alternative to manual performance testing, without interrupting production, Halo mimics the signal disturbance in the centre of the aperture, without having to physically pass a metal contaminant through the metal detector or flush out a sample. In addition to reducing operational costs, Halo testing is proven to reduce waste and product rework.
Through the incorporation of all these innovative features, Fortress asserts that its popular processcentric inline Gravity applications are now internationally regarded among the safest to operate and maintain.
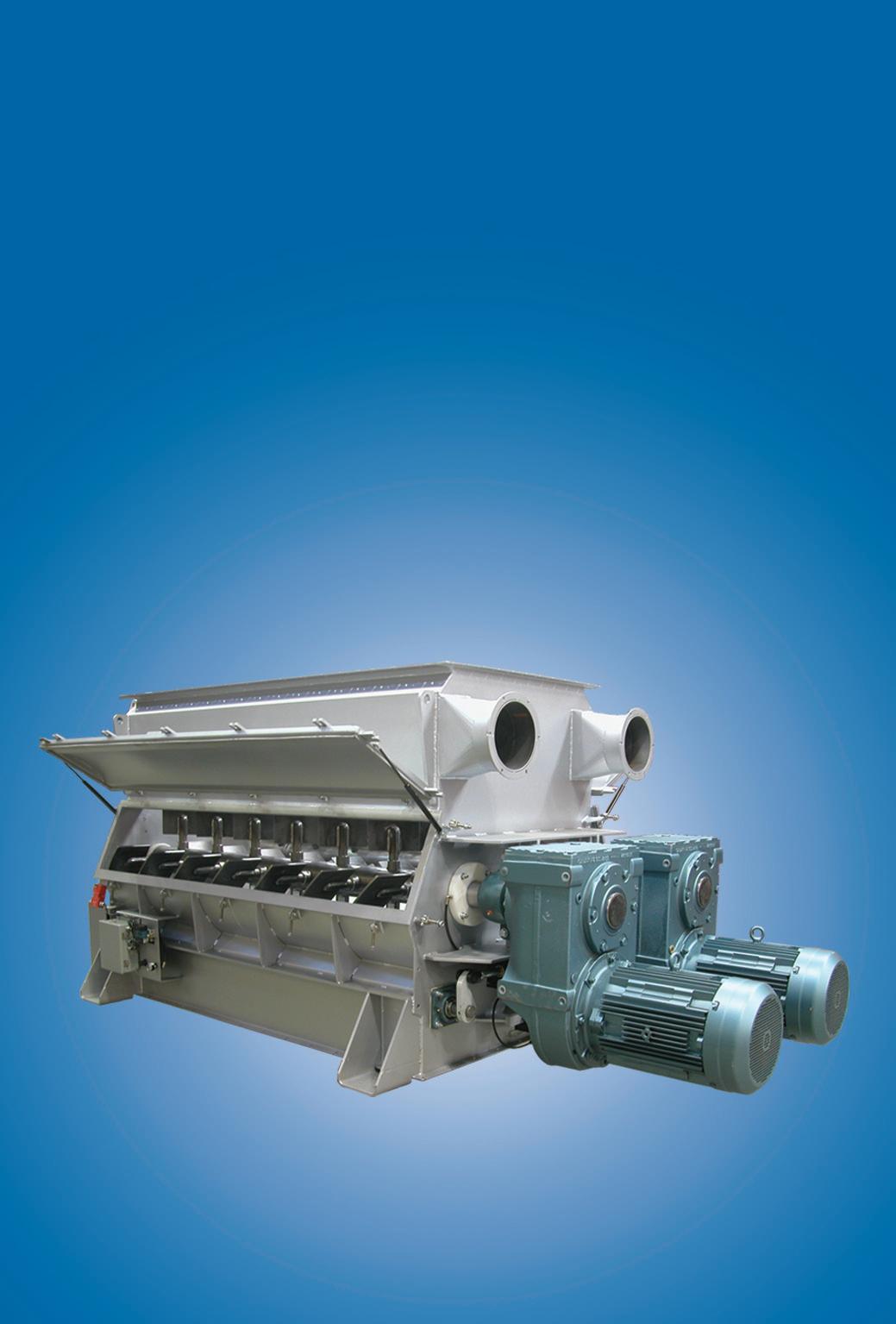
www.fortresstechnology.co.uk
High Efficiency Drying or Cooling of Bulk Solids
The Bella dryer/cooler offers thermal efficiencies to 80 percent or better because air flows around material while it is suspended in the weightless zone. The result is a more consistent material.