
7 minute read
CONVEYING
LUXME’S ONE-STEP COOLER/ CONVEYOR CUTS FOOD PRODUCERS’ FLOORSPACE AND COSTS WHILE INCREASING PRODUCTIVITY
In response to food industry demands for an enclosed system that can safely transfer and cool hot food powders and mixes in one single step, Luxme International has launched the THERMOLuxme. A tubular chain conveyor with the addition of jacketed pipes containing cooling fluid, it conveys and cools material from 260°C to 43°C and can save food producers up to £300,000 by eliminating the cost and floorspace required for a separate cooling stage.
In food processing, hot materials such as powders and mixes must be cooled to ambient temperatures after baking, frying, boiling and broiling for safe handling in the next stage of the process; for example, bagging, packaging, moving, storing or loading. Cooling also delays the fermentation process, which can cause material waste due to mildew and mould growth.
Replacing a separate cooling station with the THERMOLuxme Tubular Chain Conveying and Cooling System can result in capital cost savings of more than £300,000, since no separate coolers and/or chillers are required. Further savings include a reduction in plant floorspace; lower operational costs; decreased maintenance charges; and reduced material losses from product spoilage due to mildew. Future operational cost savings can also be made due to eliminated annual rises in electrical energy fees.
As products are cooled while they are conveyed, food producers can also enjoy increased productivity thanks to shorter processing times. Plus, treated and untreated municipal water sources, or water from elsewhere within the plant, can be used as the cooling fluid, removing additional cooling energy costs.
As with all Luxme conveyors, the THERMOLuxme adheres to the highest standards of food hygiene.
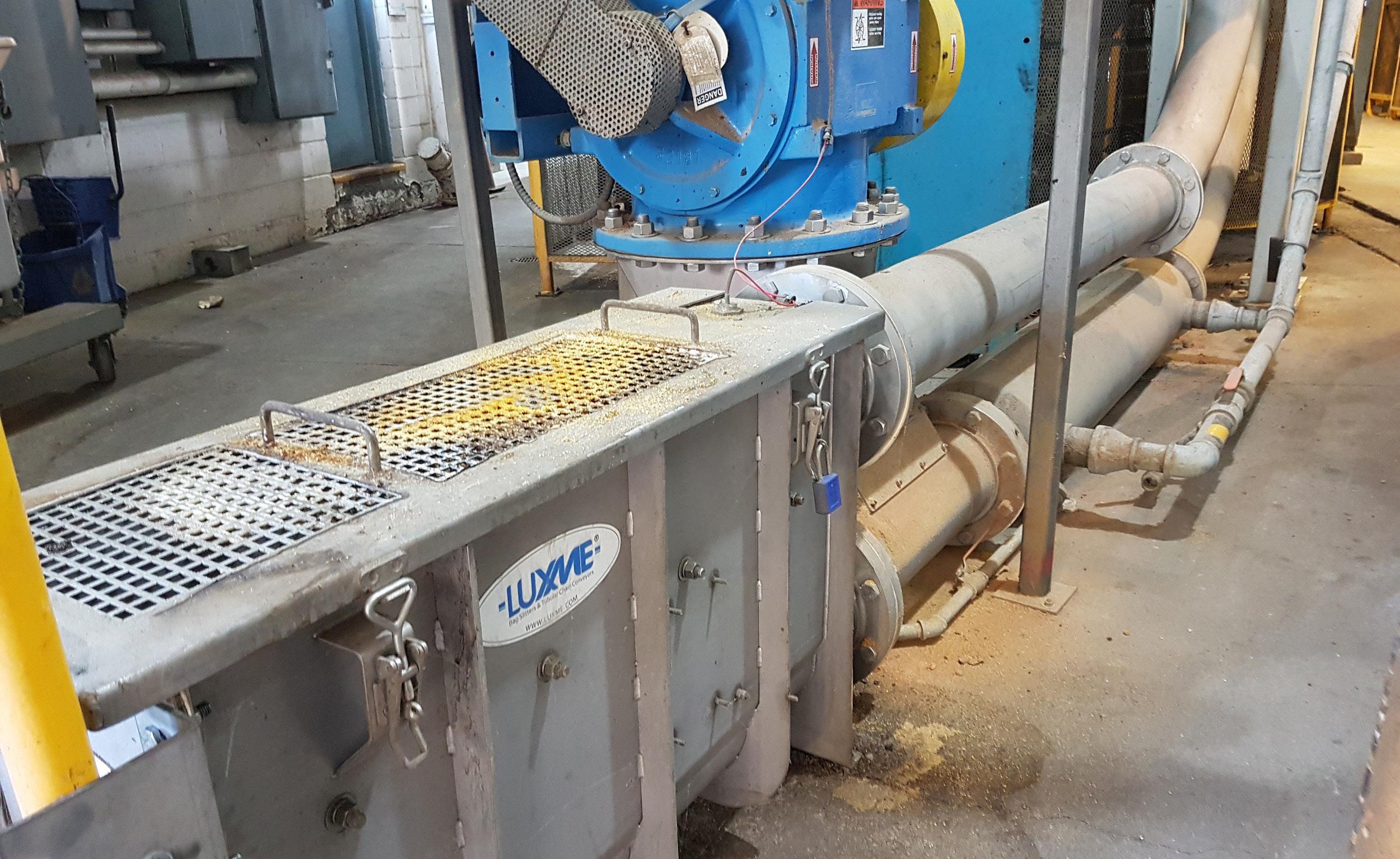
Comprising an enclosed, sealed pipe assembly, any gases or moisture emitted from the hot material during transfer are contained and vented through the internal pipework using either vacuum, forced air or inert gases, protecting the food and the workforce. As a result, the THERMOLuxme can safely convey and cool up to 31m3 of hot food products per hour, such as high-fat content organic powders and mixes, roasted nuts and snacks, pet food kibble and precooked potato cubes/foods, at the same time as ensuring that work areas remain clean, dry and dustfree.
Available in 4, 5, 6, 8 and 10-inch diameter options, the THERMOLuxme preserves product integrity by smoothly gliding food powders through the custom-designed chain and disc conveyor without pinching or crushing. With carbon steel, stainless steel 304 or 316L low-carbon stainless steel construction, it also comes with the option to specify glycol cooling chillers for applications with high inlet-to-outlet temperature differentiation over short transfer distances.
Navam Jagan, President of Luxme International, states: “With a cooling differential of 217°C while conveying product, the THERMOLuxme is designed to save food producers money and floorspace by eliminating the need for an additional cooler or chiller station. It also keeps the work area – and therefore the workforce – safe and free from dust.”
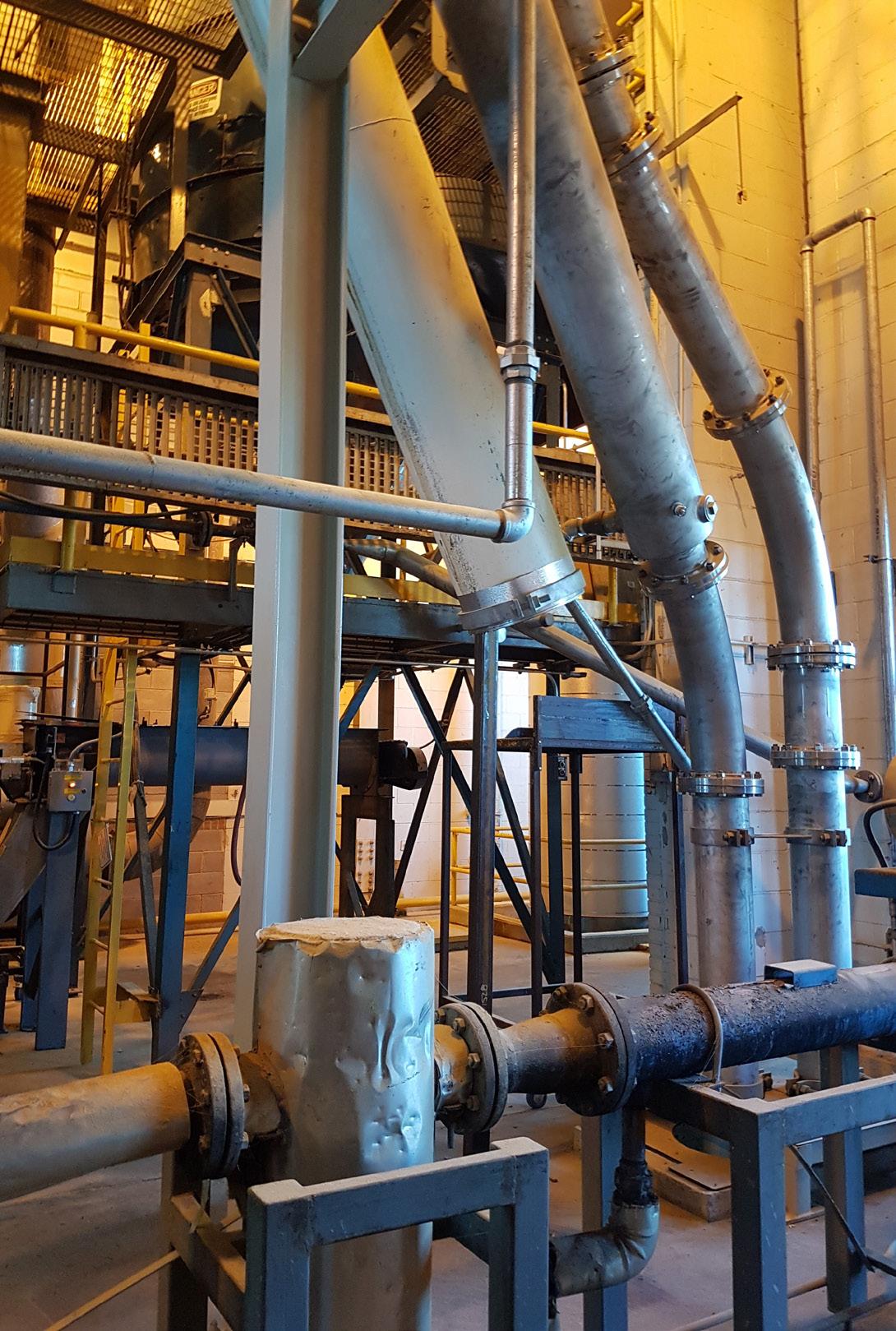
KEY TECHNOLOGY INTRODUCES VERYX® DIGITAL SORTERS FOR PET FOODS
Key Technology, a member of the Duravant family of operating companies, introduces its VERYX® digital sorters for pet food products. VERYX, which integrates seamlessly with Key’s world-class material handling systems, finds and removes foreign material (FM) and products with defects to improve product quality, eliminate the chance of cross-contamination and protect brands, all while minimizing labor.
VERYX can be configured to sort a wide range of pet foods. When installed at the end of the line, it helps ensure final product quality for kibble, chews and treats including dried, dehydrated and freeze-dried products. When installed upstream near raw receiving, it inspects ingredients such as frozen proteins and other ingredients for wet pet foods. By detecting the color, size, shape and/or structural properties of every object, VERYX removes plastics, glass, paper and other FM, as well as product defects, as defined by each pet food processor.
“Our vibratory conveyors and mechanical grading systems have had a strong presence in this industry for a long time – almost every leading pet food brand around the world relies on our equipment, and we understand their unique needs. Now that these processors are seeing the value of digital sorting, we’ve leveraged our pet food application expertise to develop VERYX for these applications,” said Marco Azzaretti, Director of Marketing at Key. “Consumers are demanding higher and higher quality pet food, and VERYX can help manufacturers elevate their product quality to the level of human grade while improving the efficiency of their operation.”
Key can integrate VERYX with a variety of their vibratory and mechanical grading solutions for transferring, scalping, size separation, fines removal, product distribution and more. Iso-Flo®, Impulse®, Zephyr™ and Marathon® vibratory conveyors, as well as their rotary separation equipment, are all suitable for pet foods, depending on the application. Built for rugged reliability, Key’s material handling solutions enhance sanitation with features such as open designs, fully-welded frames, nickel-plated finishes, oil-free

drives, optional pan covers and more.
Each VERYX is tailored with the optimal cameras, laser scanners, lighting, ejection system, product handling and software to meet each customer’s specific requirements. Utilizing in-air inspection, VERYX sees all sides of the product with no blind spots. Nextgeneration cameras and laser scanners offer twice the resolution of previous sensor technology to find smaller FM and defects. Available in different widths, VERYX satisfies a wide range of capacity requirements.
To maximize FM and defect removal, VERYX can be equipped with Key’s proprietary Pixel Fusion™ technology, which combines signals from multiple cameras and laser scanners at the image pixel level to more clearly identify even the most difficult-to-detect FM and defects. Pixel Fusion helps VERYX to better identify specific FM types and enable the optional FMAlert™ function to send a smart alarm if a critical quality problem occurs, so quick corrective action can be taken. FMAlert also saves a time-stamped image of every critical piece of FM detected by the sorter, which helps processors document and pinpoint product quality events and trends.
Key equips every VERYX with their Discovery™ suite of software capabilities, which enables the sorter to collect, analyze and share data while continuing to sort product. By harnessing data about the sort process and about every object flowing through the sorter, Discovery can reveal patterns and trends that improve sorting and control upstream and downstream processes. The information that Discovery provides allows processors to better manage incoming raw materials and optimize processes, achieving the next level in operational efficiency.
VERYX eliminates the need for manual inspection, which decreases labor costs and ensures more consistent FM and defect removal while maximizing yields. To ease use and simplify operator training, a highly intuitive UI provides different views to users of various levels depending on their needs. Recipe-driven operation ensures customers can count on consistent performance from their VERYX sorter day in, day out. Operator qualification requirements are reduced, allowing a minimally-skilled individual to become a proficient user of the system in less than one hour.
Key manufactures equipment in both the U.S. and Europe, supports customers worldwide through its extensive sales and SupportPro service network and offers integration services, from pre-engineering to line start-up. Complete line solutions can include the integration of third-party equipment along with Key’s sorting, conveying and processing systems to meet the specific needs of each application. For more information, visit www.key.net.
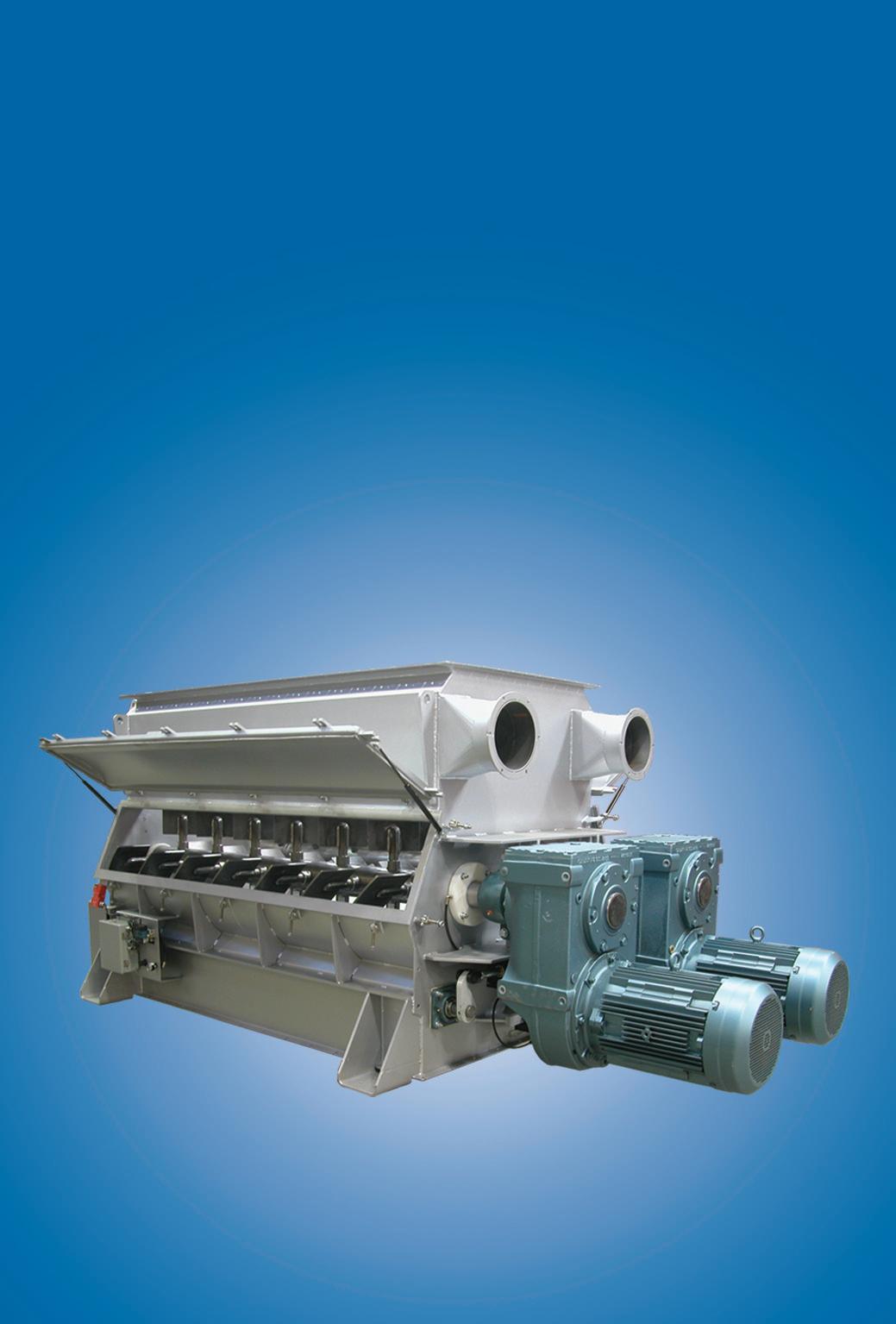
ABOUT KEY TECHNOLOGY, INC.
Key Technology is a global leader in the design and manufacture of automation systems including digital sorters, conveyors and other processing equipment. Applying processing knowledge and application expertise, Key helps customers in the food processing and other industries improve quality, increase yield, and reduce cost. Key manufactures its products at its headquarters in Walla Walla, Washington, USA; Beusichem, the Netherlands; Hasselt, Belgium; and Redmond, Oregon, USA. Key’s domestic facilities are certified to the ISO 9001:2015 standard. Key offers customer demonstration and testing services at five locations including Walla Walla, Beusichem, and Hasselt as well as Sacramento, California, USA and Melbourne, Australia; and maintains a sales and service office in Santiago de Queretaro, Mexico. Key is a Duravant Company.
ABOUT DURAVANT
Headquartered in Downers Grove, IL, Duravant is a global engineered equipment company with manufacturing, sales and service facilities throughout North America, Europe and Asia. Through their portfolio of operating companies, Duravant delivers trusted end-to-end process solutions for customers and partners through engineering and integration expertise, project management and operational excellence. With worldwide sales distribution and service networks, they provide immediate and lifetime aftermarket support to all the markets they serve in the food processing, packaging and material handling sectors. Duravant’s market-leading brands are synonymous with innovation, durability and reliability. Visit www. duravant.com.
High Efficiency Drying or Cooling of Bulk Solids
The Bella dryer/cooler offers thermal efficiencies to 80 percent or better because air flows around material while it is suspended in the weightless zone. The result is a more consistent material.