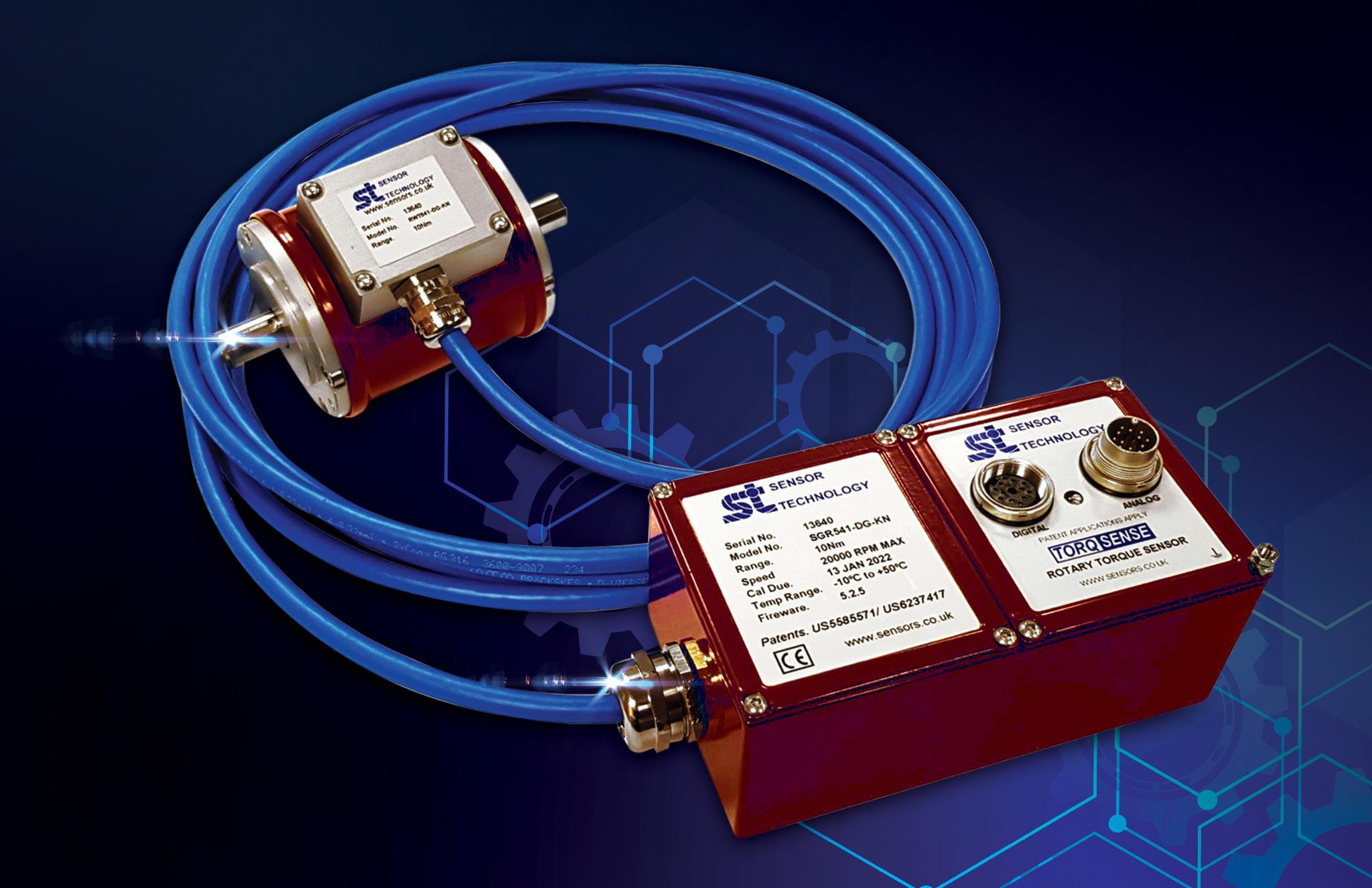
6 minute read
CONTROLS & SENSORS
NEW TECHNOLOGY CAPS PHARMA BOTTLING PROCESS
A regular customer of Sensor Technology Ltd has switched to its latest range of torque sensors.
The new TorqSense SGR530/540, being introduced throughout 2020 and 2021, measures torque using a full four element strain gauge bridge. With this, four separate strain gauges are fixed to the drive shaft of the plant or machinery being monitored. The gauges are aligned so that each measures shaft deflection in a different direction as it rotates under load. Electronics within the sensor collects readings from all four gauges and uses them to calculate the torque value in real time.
Sensor Technology has specialised in real time torque measurement for over 40 years, pioneering the use of wireless solutions based on radio frequency pick-ups that do away with the need for hard-wiring and unreliable slip rings.
Strict international rules apply to the manufacture and packaging of pharmaceutical products and require that the correct environment is maintained within the bottle or other packaging following capping. To this end, Regulation USP 671 provides a guide to the torque range to be used for screw type containers with varying closure diameters. By ensuring that bottle caps are successfully applied to the bottles within the required torque tolerances, the integrity of the product can be maintained.
Over the years Sensor Technology has worked with many OEMs to develop high precision, high speed machines for use in pharmaceutical plants and a range of other applications. One of these, an Oxfordshire neighbour of Sensor Technology, has for over 10 years incorporated TorqSense units into its capping machines.
Bottle capping is nearly always performed at very high speed, so that production targets are met. A major advantage of TorqSense is that it does not need to physically contact either the bottle caps or shaft of the torque head it is monitoring, instead using a radio frequency link. This means initial set-up and change over to new product runs is fast and efficient while operational reliability is not dependent on delicate slip rings.
“All you have to do is set up a TorqSense transducer in the capping machine and turn it on.” explains Mark Ingham of Sensor Technology.
Significantly, the new SGR530/540 sensors are designed to be drop-in replacements for the older RWT430/440 units they are replacing. They are the same size and shape as their corresponding older model, with the same mounting holes, cables in the same position etc.
“All we have had to do to the capping machines is a straightforward swap-out of new for old. It only takes a few minutes,” explains Mark. “Our new SGR TorqSense units are getting a realistic long-term work out on the capping machines, working for long hours at high speed, where they are required to be 100% reliable and consistently accurate.”
Fast and accurate torque measurement is becoming more and more important as all sectors of manufacturing automate their physical processes while also needing to improve the recording of production performance data. TorqSense is used in many industries from automotive to materials handling, test and measurement, FMCG (fast moving consumer goods) production, power generation etc. Sensor Technology is working with user-partners in many sectors to assess the new SGR units in a range of working environment.
www.sensors.co.uk
PARKER IQAN-XC4X EXPANSION MODULES NOW CERTIFIED FOR FUNCTIONAL SAFETY
Certification facilitates easier system implementation and machine design in mobile hydraulic applications demanding higher levels of functional safety
Parker Hannifin the global leader in motion and control technologies, now offers its IQANXC41, -XC42 and -XC43 expansion modules with certification according to IEC 61508 safety integrity level 2 (SIL2). This development makes it possible to use the modules as part of machinery safety functions up to EN 13849-1 Performance level d (PL d). With safety-certified expansion modules, engineers can simplify system implementation and machine design in mobile hydraulic applications demanding higher levels of functional safety. Such applications include those relating to material handling, construction, aerial platforms, and specialty vehicles like refuse trucks, for example.
The new development from Parker means that both types of controllers on the latest IQAN platform - MC4x master controllers and XC4x expansion modules - provide several safety-certified versions so that machine designers have many options at their disposal. For instance, design engineers can now assign critical I/O to a module at the best physical location on the machine, reducing wiring complexity and cost. This modularity enables easy upscaling or downscaling with pin-compatible units.
An important feature of the XC4x is Parker’s newly designed protocol, which is both safe and bandwidth efficient. The protocol supports both classic CAN (250 and 500 kbps) and CAN FD up to 500/2000 kpbs. Notably, in a system where all outputs that control hydraulic valves are safe to begin with, the application designer does not have to introduce additional components and complexity in order to implement basic stop functions.
IQAN is an electronic control system for mobile hydraulic applications with the highest focus on functional safety, precision control and ease-of-use. At the core of the IQAN family is a fully integrated solution of controllers and displays, with the IQAN software toolchain facilitating configuration and maintenance tasks. IQAN is safe, fast, and powerful to use.
The IQAN toolchain consists of three core software suites: IQANdesign for application design, IQANsimulate for simulation of the application, and IQANrun for service and diagnostics. Thanks to Parker’s co-development of IQAN hardware and IQAN software, users get to benefit from plug and play functionality and increased safety performance.
There are numerous advantages of using IQAN for functional safety. For instance, when using IQANdesign, a high-level graphical tool for quick and easy system layout and machine function design, there is no need to compile the application or embedded software (Parker compiles and verifies all embedded software and the IQAN application interpreter). Users of IQANdesign can highlight and document safety functions, guided by project check. In addition, designers can easily create the intended function and take advantage of predictable real-time performance.
Ultimately, multiple IQAN master modules can be combined seamlessly with Parker IQAN protocols for exchanging safety-related signals with realtime performance between modules. From a safety perspective, it is a great advantage for the developer that the controller and diagnostics tools are designed to work together. It is far easier to provide a reliable and carefully considered interface when everything belongs to the same system of software support tools and controller hardware. IQAN easily implements safety-related devices with generic support from SAE J1939-76 for safe communication with sensors and other input devices.
For more information, please visit: https://ph.parker.com/de/en/expansioncontrollers-iqan-xc41-xc42-xc43-xc44
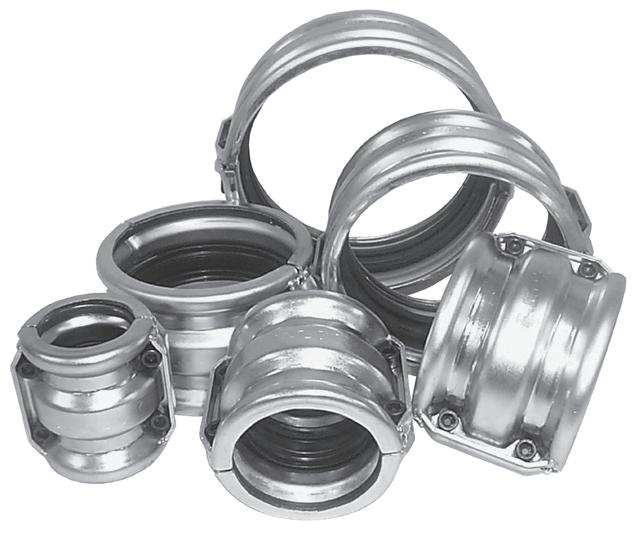
Tuf-Lok ring grip pipe and tube couplings are rugged, heavy duty, self-aligning and self-grounded couplings with a high end pull. They can be used for almost any application where pipe or tube ends need to be connected. The Tuf-Lok self-aligning couplings install quickly and easily with little effort.
Features
• Self-aligning • Self-grounding • High pressure rated • Full vacuum rated • Stainless or mild steel • Usable on thin or thick wall pipe or tube • Low cost • Reusable • Absorbs vibration • Externally leakproof
Tuf-Lok (UK)
Tel: +44 (0) 1706 822512 Email: sales@tuflok.co.uk • www.tuflok.com