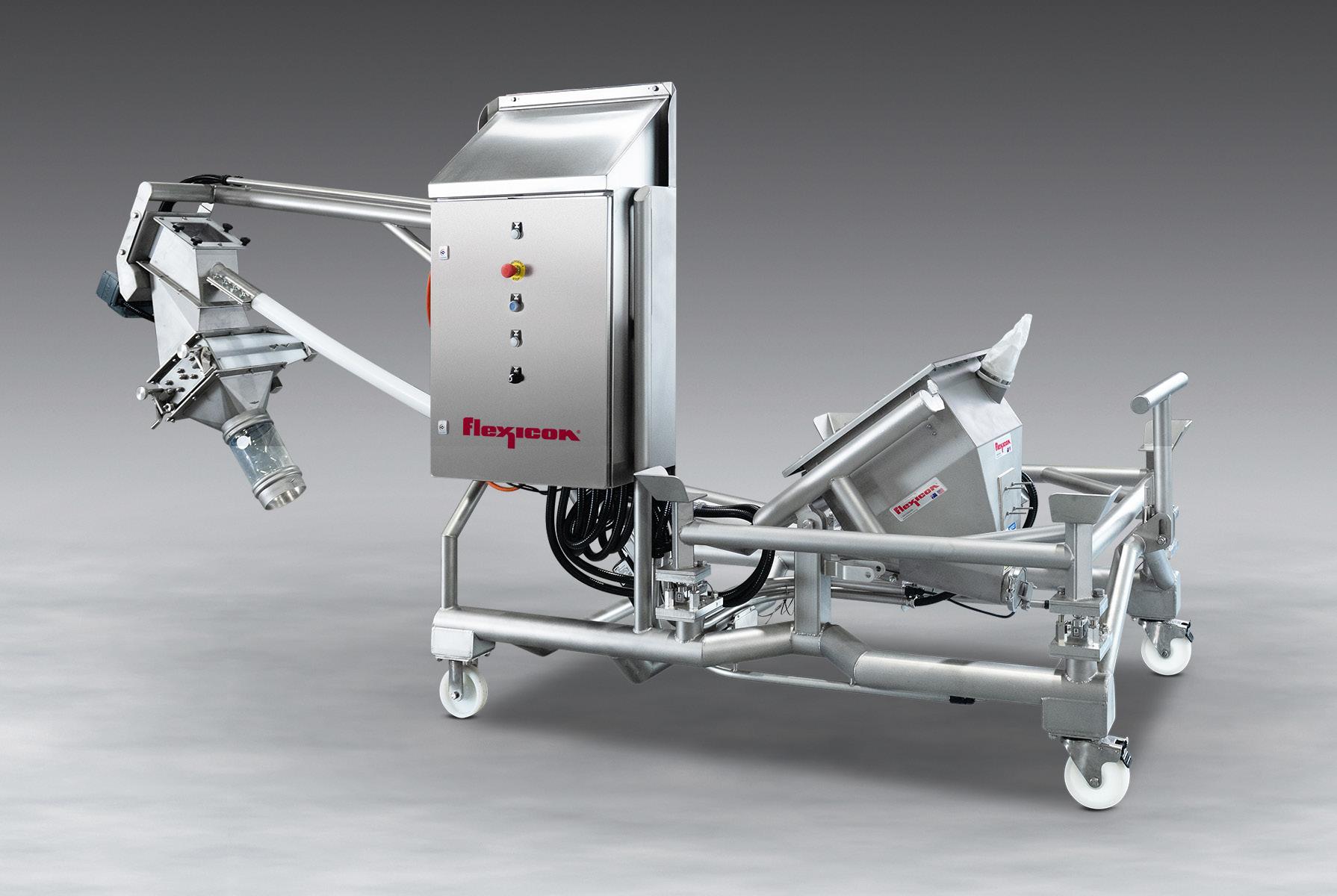
4 minute read
FEEDERS & CONVEYING
MOBILE SANITARY IBC UNLOADINGCONVEYING SYSTEM
A new Flexicon Mobile Sanitary IBC Unloading and Conveying System transfers contaminationsensitive bulk solid materials from Intermediate Bulk Containers (IBCs) to downstream processes, dustfree.
The discharger frame is mounted on castors for in-plant mobility, while a hinged sub-frame supporting a surge hopper, flexible screw conveyor and support mast can pivot down for manoeuvring through doorways and low-headroom areas.
The IBC frame is forklifted onto receiving cups, which position the IBC outlet onto the surge hopper inlet. Material flowing from the IBC into the charging adapter of a flexible screw conveyor is propelled at an incline, and discharged into elevated process equipment and storage vessels.
The conveyor handles a broad range of free- and non-free-flowing bulk solids ranging from pellets to sub-micron powders with no separation of blended products. The flexible screw is the only moving part contacting material, and is driven by an electric motor positioned beyond the discharge point, preventing material contact with seals.
Ready to plug in and run, the mobile unit can serve multiple functions throughout the plant. It can be rolled to a cleaning station where a lower cleanout cap on the conveyor tube can be removed to flush the smooth interior surfaces with steam, water or cleaning solutions, or to fully remove the flexible screw for cleaning and inspection.
The system is available in carbon steel with durable industrial coating, with stainless steel material contact surfaces, or in all-stainless steel (shown) finished to industrial, food, dairy or pharmaceutical standards.
Flexicon also manufacture other configurations of IBC and bulk bag dischargers as well as tubular cable conveyors, flexible screw conveyors, pneumatic conveying systems, bulk bag conditioners, bulk bag fillers, bag dump stations, drum/box/container tippers, drum fillers, weigh batching and blending systems, and engineered plant-wide bulk handling systems with automated controls.
For information contact Flexicon Europe Ltd, +44 (0)1227 374710, sales@flexicon.co.uk, www. flexicon.co.uk
KEY TECHNOLOGY INTRODUCES NEW AUTO DIVERTER FOR VIBRATORY CONVEYORS
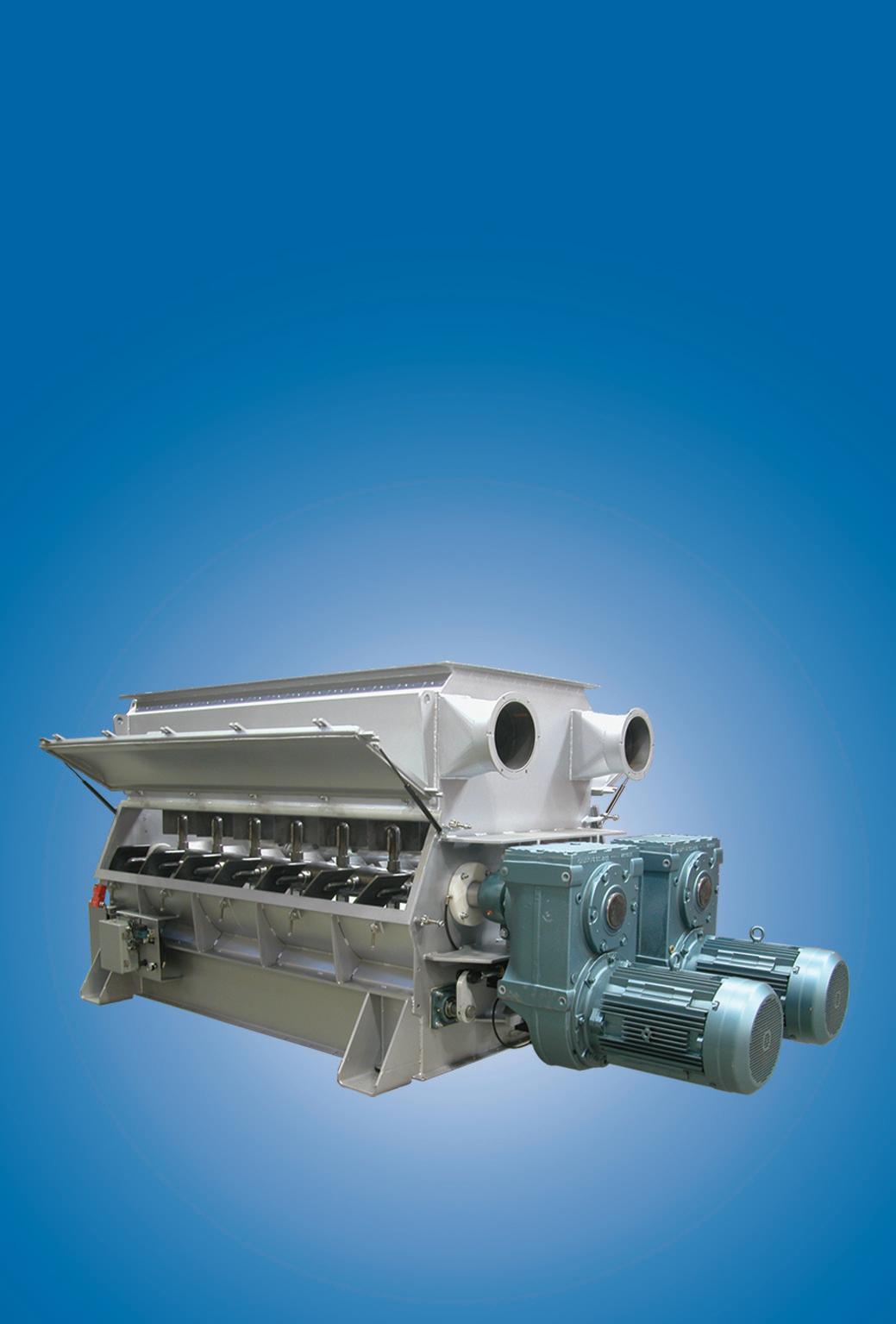
Key Technology, a member of the Duravant family of operating companies, introduces its new and improved Auto Diverter for its popular Iso-Flo® vibratory conveyors. Ideal for bulk product and packaging distribution lines, the Auto Diverter splits the product flow to two downstream systems, such as digital sorters or packaging machines, and changes the proportion of product going to each of the two lanes as needed. This patented Auto Diverter features a stronger diverter blade, an improved pneumatic hold-down system and more to achieve longer equipment life and greater accuracy for better performance of downstream systems.
“Vibratory conveying equipment, including diverters, take a beating during routine operation. Product moves through shakers with immense force over long periods of time. For that reason, robust automatic diverters are challenging to design – most equipment manufacturers won’t even try,” said Rudy Sanchez, Process Systems Product Development Manager at Key. “We did a lot of research and testing to develop a new diverter system that improves reliability and extends the life of this unit in even the most demanding production environments. Our Auto Diverter is a very unique solution.”
Suitable for dry, frozen and wet applications, the Auto Diverter can handle virtually any free-flowing food product including fruits and vegetables such as cut and whole potatoes and cut and whole corn, as well as nuts, candies, snacks and more. Available for beds up to 1830mm (72 inches) wide, it can be equipped with a blade up to 1200mm (47 inches) long.
The redesigned Auto Diverter features a stronger, thicker diverter blade for better product handling and equipment longevity. Now bolted, instead of welded, the blade can be easily removed for cleaning and maintenance. The new pneumatic hold-down system anchors the blade to the surface of the bed to withstand a greater amount of product force without shifting from its programmed position. For better product control, each diverter is customized to guide product away from bed corners and features a blade that matches the product depth
To accurately divide the product stream, the Auto Diverter’s pneumatic actuator moves the blade precisely into each position needed. Using only the controls and no manual adjustments, an operator can split the two product outfeeds and implement quick and easy adjustments including blocking an entire lane for maintenance of downstream equipment. Featuring fullyintegrated and optimized controls, the Auto Diverter can be operated locally at the user interface. Additionally, it can be programmed to be controlled via a plantwide network and/or automatically controlled by downstream equipment.
Designed to maximize sanitation, the Auto Diverter features scalloped welds throughout its stainless-steel frame and blade. The actuator is positioned underneath the conveyor bed to help maintain food safety. Compared to traditional diverters, where an operator must manually reach over the shaker bed to reposition the blade, the Auto Diverter improves operator safety and ergonomics while reducing the risk of foreign material introduction to the product stream.
High Efficiency Drying or Cooling of Bulk Solids
The Bella dryer/cooler offers thermal efficiencies to 80 percent or better because air flows around material while it is suspended in the weightless zone. The result is a more consistent material.
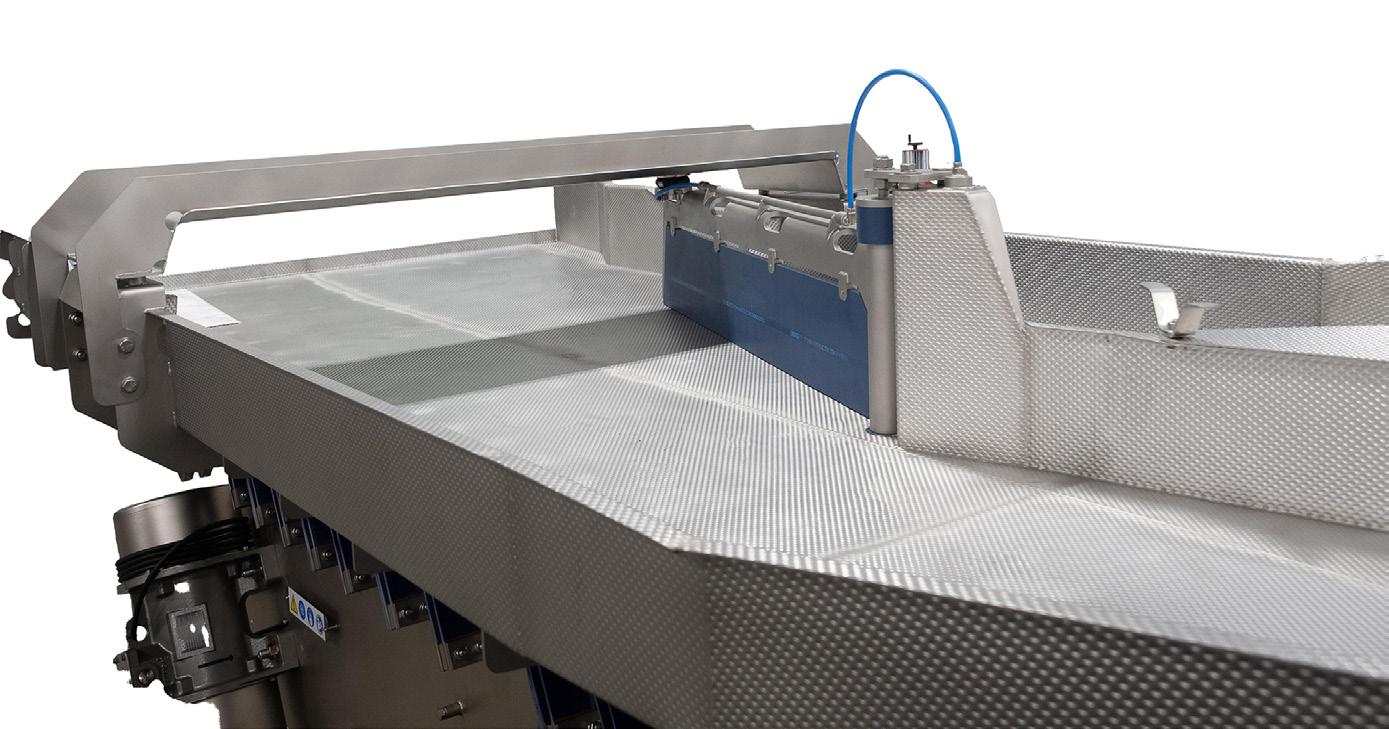