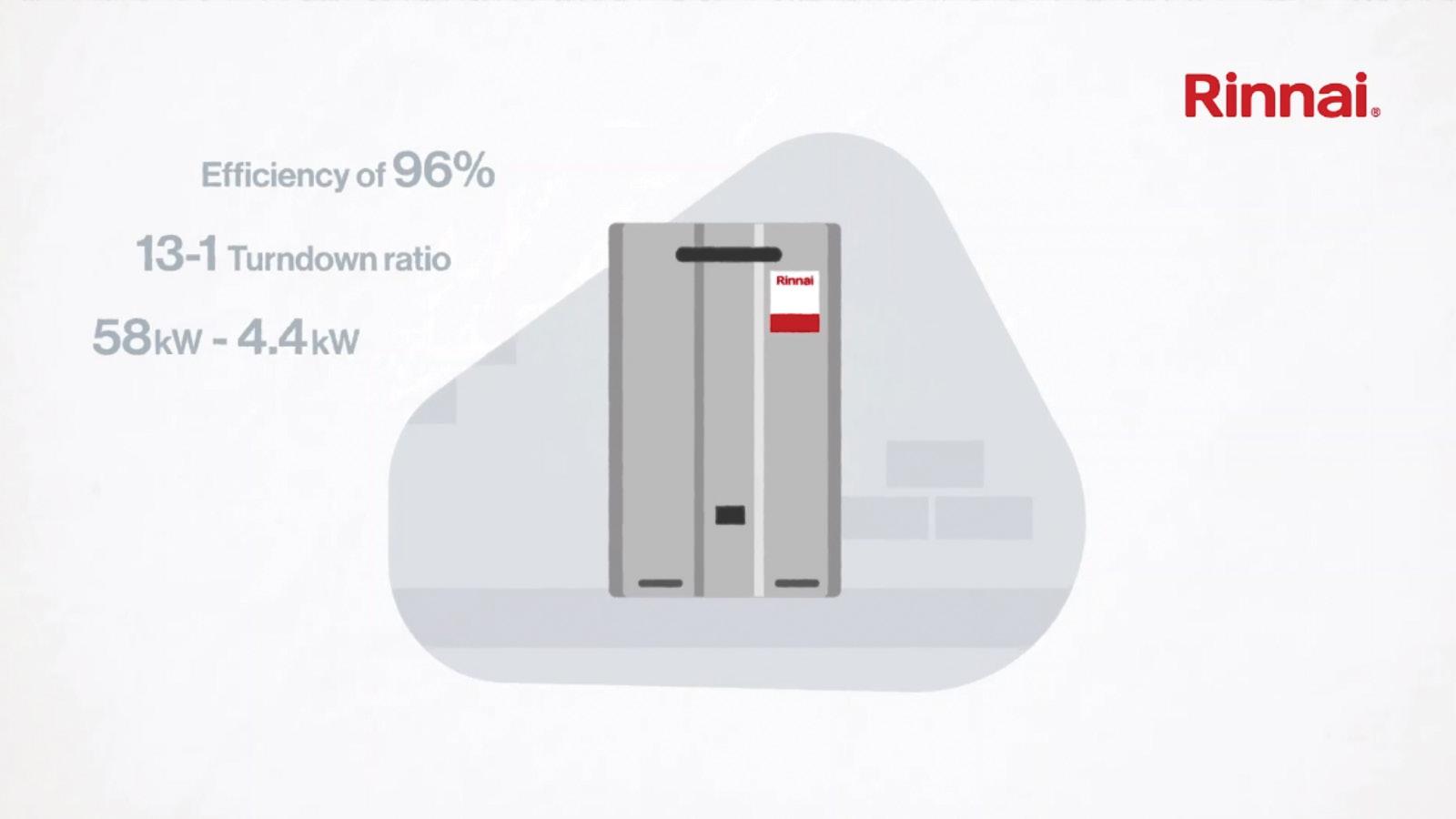
2 minute read
RINNAI HYBRID SYSTEM PROVIDES PRACTICAL, ECONOMIC, AND TECHNICAL SOLUTION AT LUXURY COMPLEX IN THE CITY OF LONDON
Rinnai Low-GWP 55kW Heat Pump, bespoke thermal stores, Plate Heat Exchangers and 10 cascaded I2HY20 Hydrogenready continuous flow water heaters specified at new development in the heart of Farringdon district of London.
On this site Rinnai’s Hybrid H2 array of Low-GWP 55kW heat pump plus bespoke hot water stores, with optimised coil transfer to maximize heat pump performance, have been combined with ten cascaded Hydrogen blends ready (I2HY20 certified) continuous flow water heaters. The systems were delivered in one complete consignment, ready for installation at a new multi-million-pound development in the Farringdon district near the City of London. The expansive complex will comprise of a new luxury hotel, prestigious & contemporary office space plus affordable housing units.
The multi-purpose use of the site meant that only a fit-for-purpose design would satisfy the practicalities and nuances of space, demand and energy usage in ensuring hot water requirements are met and exceeded 24/7.
The site was originally a Victorianera schoolhouse for poor children. It was a ‘Ragged School’ - the term ‘ragged school’ was used by the London City Mission as early as 1840 to describe the establishment of schools, ‘formed exclusively for children raggedly clothed’. From around 1845 until 1881, the London ‘Ragged’ schools gave rudimentary education to about 300,000 children who were the poorest of the poor - orphans, waifs and strays.
The expansive retro-fit site will pay respect to this heritage with many of the original features retained in the 150+ bedroom luxury hotel, almost 20,000 sq ft of opulent capital city office space and nine new-build affordable residential units. The hotel group already has one other unit in London with two others planned.
Comments Darren Woodward for Rinnai, ’The site is very complex and still has many original features from the Victorian era – meaning that a full and comprehensive site survey with capital expenditure, operational expenditure and carbon modelling was conducted. We paid special attention to the practical requirements of the site which included 150 luxury bedrooms that needed constant hot water on demand, but we also needed to meet the site’s decarbonisation credentials. The overall system design meant that a truly hybrid system employing a heat pump, plate heat exchangers, bespoke thermal stores plus Hydrogen-ready hot water heating units was supplied in one complete consignment. www.rinnai-uk.co.uk/about us/H3
“We believe that a solution like this is the way forward on the bigger retrofit sites in London and all other UK cities. Once we had the data for capital expenditure, operational expenditure and carbon modelling we were able to demonstrate to the clients a value proposition of a delivered-to-site-inone-package. This site has proven that Hybrids can create a practical, economic and technical feasible solution whereby all technologies and appliances work efficiently in terms of operational costs and lowering the carbon footprint without impacting overall system performance.
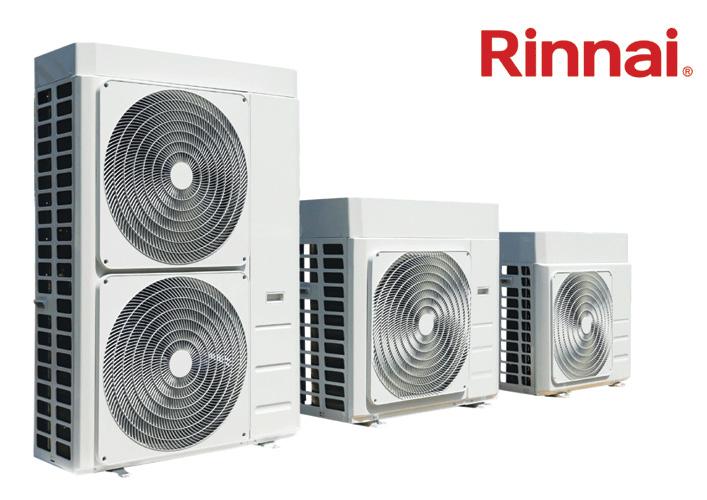