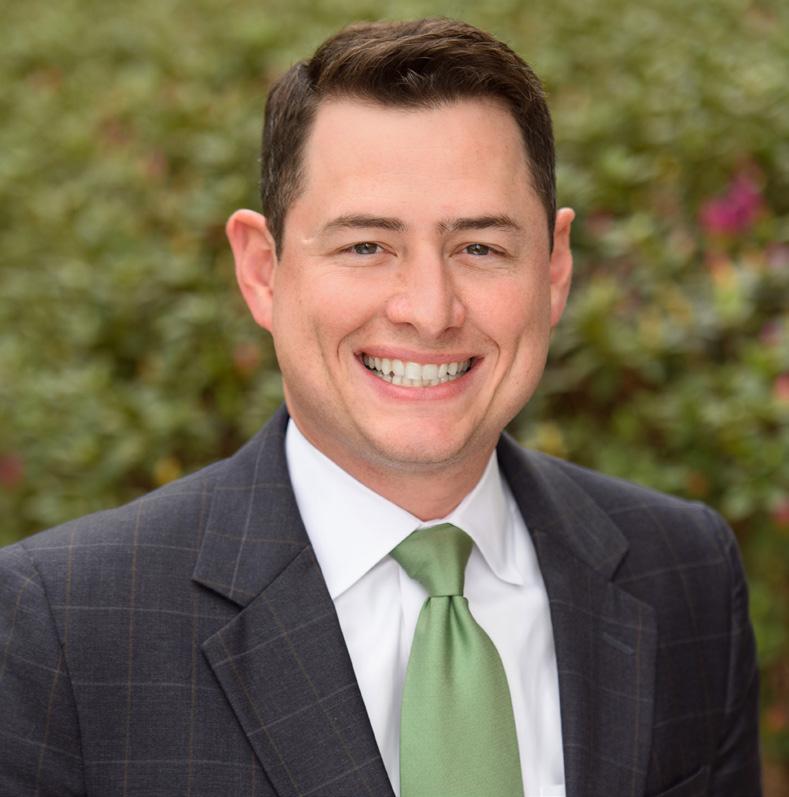
1 minute read
SWTC Update
SOUTHWEST TRAINING CENTER UPDATE
BACK TO BUSINESS AT THE SOUTHWEST TRAINING CENTER
By: Blaise Theard, Workforce Development Specialist
Nearly one year after hurricanes Laura and Delta, Southwest Louisiana is still on the road to recovery. The ABC Pelican Southwest Training Center is still pushing forward through the many obstacles we have experienced over the past year. While we were not able to offer the full slate of classes throughout the academic year, the SWTC team remained committed to training quality craftsmen and craftswomen.
The Southwest Training Center welcomed students back into the training facility in June of 2020 after the COVID-19 restrictions were reduced. Shortly after the start of the Fall 2020 semester, Hurricane Laura made landfall August 27th, 2020 and ripped through SWLA causing an estimated $12 billion in damages to Louisiana. The SWTC was shut down as the damage was being assessed. Six weeks later Hurricane Delta followed a very similar path through an already battered SWLA. The SWTC was forced to cancel the remainder of the Fall 2020 semester except for a few high school welding classes located in outlying areas. While the past year has been tough and trying, Southwest Louisiana will bounce back stronger than ever. The Spring 2021 Semester is in the books and the Fall 2021 Semester recently started in early August. The Southwest Training Center is dedicated to training the best craft professionals that our members need and deserve. Our trained craftsmen and craftswomen will be here to support our industry and SWLA for years to come.
With the Spring 2021 semester around the corner, repairs were being made to create a safe learning environment for our students. The Southwest Training Center was able to start the Spring 2021 semester in January. We were able to conduct classes during the day with our accelerated training, our evening training, and our dual enrollment classes at our high school satellite locations. A total of 496 credits were earned in the semester. Our dual enrollment classes wrapped up with 121 students completing the course. Of those students, 29 passed a weld test performed by thirdparty testing facility. These students earned either an AWS Basic credential for passing an Overhead T-Joint weld test or passing an Overhead Open V-Groove weld test to receive an AWS Advanced credential. With limited classroom space and minor delays of COVID, freezing weather, and major flooding, the Spring 2021 was still a success.
ADDRESSING WHO BEARS THE RISK OF PRICE ESCALATION IN CONSTRUCTION MATERIALS
By: Russel W. Wray, Wray & Associates
“It is never nice to take advantage of someone else’s misery.” Those were the words of a distinguished member of the bar from Kansas City, Missouri, Susan McGreevy, now retired who wrote about steel price escalation in 2004. At that time, “global forces” were causing “unprecedented” price escalation in steel and other materials. She reported that in one years’ time the price of rebar jumped from $283/ ton to $412/ton. (McGreevy, S., 2004. How to Protect Against Steel Price Increases. [online] Contractor. Available at: https://www.contractormag.com/management/mcgreevy/ article/20873251/how-to-protect-against-steel-priceincreases (Accessed Jul 19. 2021).) Once again, market forces fueled by a global pandemic are running up the price of steel to “unprecedented” levels. Steel has escalated in price 200% or more in less than one year. One contractor’s experience provides a dramatic example of price increases in steel. A 6’ x 12’ sheet of highway mesh cost $67 in March 2021 and by mid-July the price was $155 for the same sheet. Moreover, the supplier was unwilling to hold those prices for more than two days or until current supplies ran out. Commentators disagree about how long-lasting and pervasive the current price volatility will prove to be. Whether the product is lumber, steel, copper, fuel, pvc pipe, cement, or other items, and whether price escalation is caused by “global forces”, hurricanes, or some other calamity, price volatility of materials is a known risk. Moreover, by now we should all have come to the realization that what is “unprecedented” today may be small potatoes to what is “unprecedented” tomorrow.
One effective means to equitably allocate the risk of price volatility is to include provisions for that risk expressly in the contract documents. Doing nothing, and thereby allocating that risk solely to the contractor, comes at a cost to all parties involved. Unanticipated price volatility can (and often does) result in claims, disputes, delays, litigation, business failures, and bankruptcies, all of which interrupt project delivery and result in additional cost to the owner, as well as the contractor. Owners, both private and public, may ultimately bear the costs and the effects of price volatility ripples through the economy. At some point, volatility in construction prices becomes a matter of public policy to be addressed by legislation. the owner or the contractor. It is time the conversation is expanded to include other construction materials, and we must do so for the common benefit of all participants.
It is patently clear why contractors are concerned about price escalation, but why should owners, especially public owners, agree to pay more by including a price escalation provision in the contract for any material or component of the work? The truth is that it is in the interest of the owner, especially public owners, to address price volatility in the contract to obtain the best price for the work by reducing risk which, as at present, cannot be mitigated by the contractor in advance and help insure a successful project on time and on budget.
As an example, in the early 20th century, the changed condition clause was developed by the federal government to mitigate the “gamble” undertaken by a contractor for unknown subsurface site conditions not discoverable on a routine site visit and has developed into the differing site condition clause now standard in all types of public and private contracts today. The differing site condition clause is mandated by the federal government in all federal construction contracts and for use in state highway contracts funded with federal dollars. The American Institute of Architects also included such clauses in standard industry contracts dating back to the 1930s. It is well accepted that by including a differing site condition clause to mitigate that risk, contractors would not include a contingency for those risks in its price. Without the differing site condition clause, the contractor’s guess or gamble could provide a windfall to the detriment of the owner or, on the other hand, prove to be insufficient to cover the actual cost, and further could be a crippling blow to the contractor (who guessed wrong) resulting in abandonment, default termination, and reduced competition for future work. It is well accepted that by use of the differing site condition clause, the contractor would provide their best price for the work without a price contingency for unknown site conditions based upon the assurance provided by the owner that if the risk arose, the actual increased cost would be paid. Through sound pre-bid engineering assessments, those risks could best be identified and factored into the plans and specifications, as well as the budget.
At present, Louisiana law authorizes the use of price escalation clauses in public works contracts, but that authorization is not widely applied. DOTD contracts provide price adjustments for fluctuations in the cost of fuel and liquid asphalt, whether the price increases or decreases by more than a specified amount, and whether in favor of That same rationale underlies legislation, in whole or in part, such as: immunity to the contractor for defects in the plans and specifications; prohibiting no damage for delay clauses on public contracts; prompt payment legislation; and antiindemnity statutes, to name a few. Economic stability and risk management in construction is an issue important to all.
The golden rule analogy by Ms. McGreevy in her 2004 article is sound, but owners should recognize where their self-interest lies by inviting contractors to bid their best prices by first reducing or eliminating risk of extreme price volatility at the time of contracting that cannot be accurately identified and factored into a bid by the contractor. An alternative approach to a price escalation clause is to allow for and pay stockpile material cost. Contractors may or may not be able to lock in a price for certain materials at bidding, much less obtain those materials when needed months after signing the contract. Compensating the contractor for buying materials up front and stockpiling those for use on the job is another means of allowing the contractor to mitigate price volatility, as well as material shortages. This presents unique challenges beyond the scope of this article. How many more “unprecedented” global events or storms must befall us before we, as an industry, address these issues before the next one arises. What is the role of legislation in requiring price escalation provisions to allocate the risk to protect the construction industry, vital to our economy and national defense? All parties—general contractors, sureties, lenders, subcontractors, suppliers, owners, design professionals, etc. bear the risk and should be interested in furthering this conversation. Russel W. Wray is an attorney and owner of Wray & Associates (www.wraylaw.com) and practices in Louisiana. This article is informational and should not be used as legal advice. One should independently consult with an attorney, prior to relying on any of the information provided herein. Wray & Associates © 2021
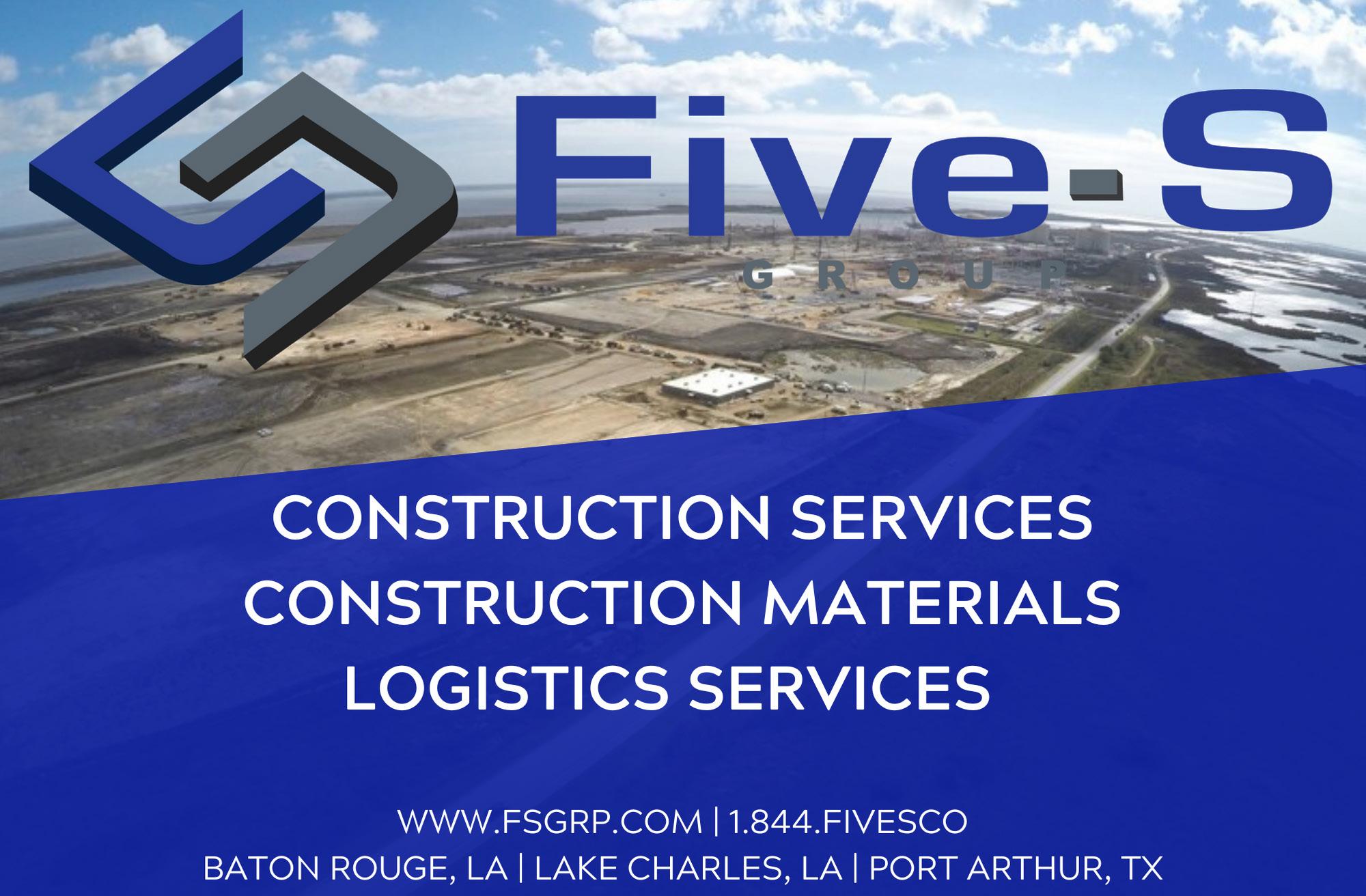
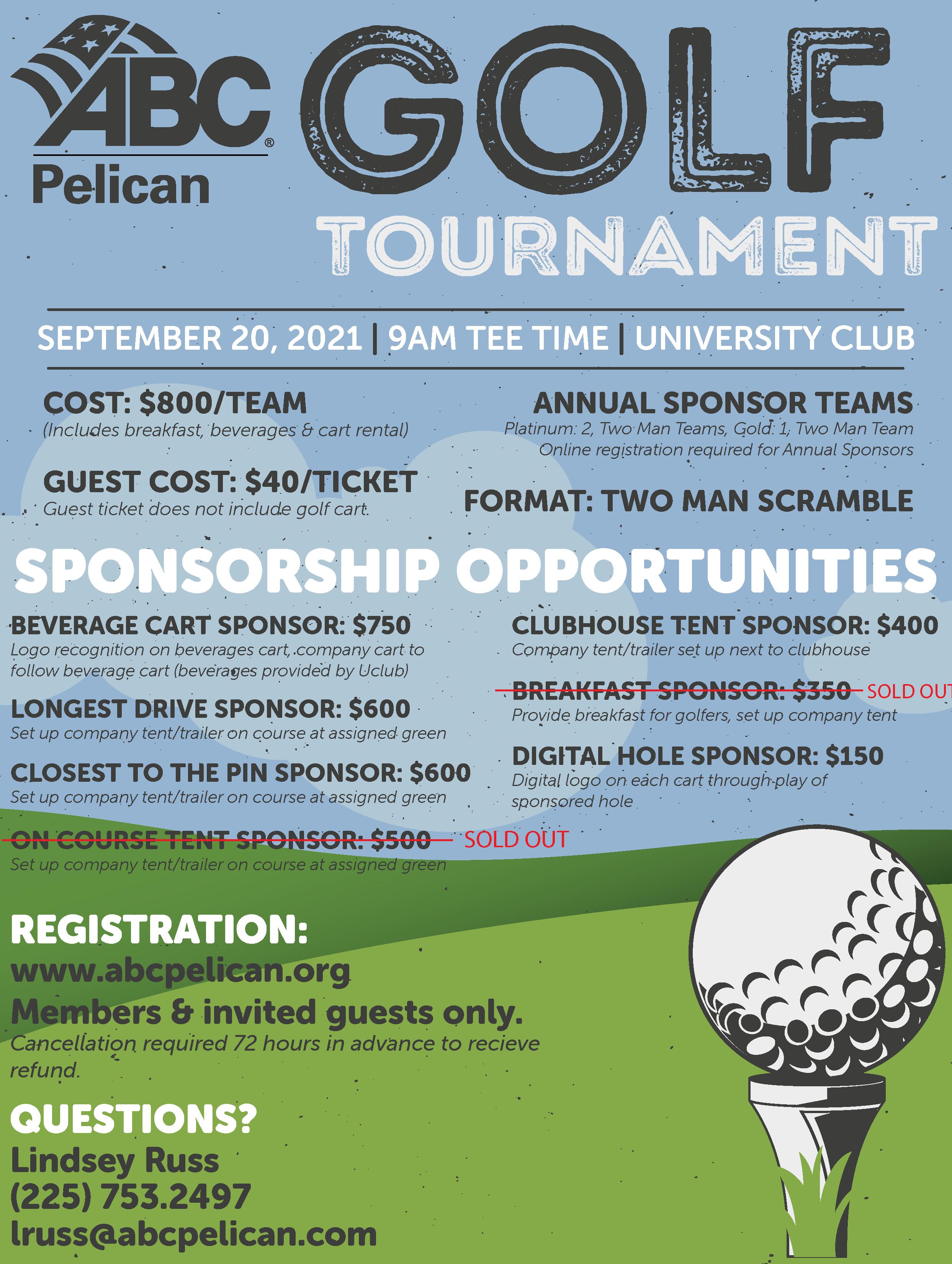