
8 minute read
Technical Insights: Dimensioning and Tolerances
from Access Insight - Winter 2021
by ACAA
TECHNICAL INSIGHTS
The articles featured in Technical Insights are to prompt thought and discussion to assist our members' question and evaluate their understanding of the technical requirements of Australian Standards and other national/international source material. Technical Insights is to intended to provide background information, a different viewpoint, a perspective from an individual with lived experience of disability or to prompt further discussion and/or research by you as an access professional.
Dimensioning and Tolerances
by Howard Moutrie
In June I posted this topic on the ACAA Forum and I feel it is worthwhile expanding and I apologise in advance that in the end this article becomes a forum for a particular issue I have rather than a purely technical discussion.
There are two separate issues, the first is drafting techniques and standards and the second is building tolerances. Although separate, they are inter-twined. With respect to tolerances, I tried to get this acknowledged in the latest edition of AS 1428.1 (yet to be published) and although I had support from the building sector it was rejected by the committee. The result is that the standard asks for a level of construction which is outside the standard practice and difficult to achieve in some instances.
Firstly, let us look at dimensioning. Architects, draftsmen and builders work, in accordance with AS 1100.301, on the premise that they dimension to the structural element, thus, the dimensions must allow for the application of any linings and finishes. So, for a toilet with a clear width of 1900mm the room should be dimensioned at least 1925mm. This causes no issues because the room is meant to be a minimum of 1900mm. Confusion can occur, however, when maximum dimensions are required. An ambulant toilet is required to be 900-920mm wide, however, this could be dimensioned at 930mm, which on face value seems incorrect but is actually allowing for the thickness of the wall tiles so that the finished dimension is compliant. Confusion can also be created if the architects indicate a corridor dimension at 1540mm, meaning it to be clear, but the builder will build the structure at this dimension based on the recognised drafting standards.
There is an exception to this. The above discussion relates generally to the setout plans or general arrangement plans. When detail plans are produced for the bathroom areas, these are typically produced for the fitout trades and assume the structure is built, thus, they may show the clear dimensions.
A complication to this relates to the selection of fittings and finishes. For example, a wall tile may be 6mm thick or 10mm thick. If the tile hasn’t been selected care must be taken by the architect to make the correct allowance. A common problem I see on site is that the accessible toilet is designed with a standard basin, with all the correct clearances, but then a larger basin is selected and the result is non-compliance. The access consultant, the architect, the interior designer and the builder need to be aware of the implications of these selections.
When reviewing the drawings it is important to understand the dimensioning methodology. This all ties into building tolerance too, but before I discuss tolerances it is worth digressing to a method of measurement which was developed in the 1970s /1980s and was popular with the government agencies but was never popular en-masse because it was confusing, particularly for the trades on site. This method of measurement accepted that builders needed a tolerance, so a wall would be dimensioned as a zone, say 200mm wide, even though the wall itself is only 190mm wide. That is why concrete blocks are called a 200mm block but are actually only 190mm. This method was based on the premise that the wall (or floor or door or window) would not be located accurately so a zone was given in which it had to be constructed. In theory, it all makes sense but when a builder wants to know where to build a wall, he wants an exact location not a zone.
So now to tolerances. If anyone has tried to build a structure, even a little garden wall, you will know that you are not going to get it millimetre perfect. Thus, you need to allow some tolerance. For building structure this may be 10mm but for joinery it may be 1 millimetre or even less. You also need to understand the construction sequencing. Drainage pipes for the toilets will be positioned in the concrete slab before it is poured – no walls in sight. As the concrete is poured it can exert substantial pressure and the formwork or drainage point may move. Then you come to the rough in of the services in the room; you now have walls, but they are the structural walls without finishes. The plumber needs to estimate where the fittings are to be located from this imaginary finished wall surface, so he estimates from the structural wall, but this may not be exactly in the correct location. Before you say well the builder should put the wall in the right position, for a masonry wall AS 3700 acknowledges that tolerances are required and considers that a wall is correctly located if it is +/- 10mm from its intended location. What is more, it can also be +/-10mm from plumb within a storey. Thus, it may be correctly located at floor level but not at ceiling level. Where do you measure the 1900mm width of the toilet?
Concrete wall around stairs and lifts poses other problems and can be particularly hard to control dimensionally. I have commonly seen corridors, with stair/ lift on one side which are not parallel because the concrete forms have moved. Some builders will just line or finish the walls in the non-parallel state but a quality builder, particularly if there is a special floor or ceiling finish which will highlight this issue will pack out the lining of the offending wall so that the 2 walls are parallel. I have seen a number of instances where this has resulted in a corridor designed to be a turning area of 1540mm wide (clear and with additional tolerance) finish being less than 1540mm as a result of the building trying to do a quality job.
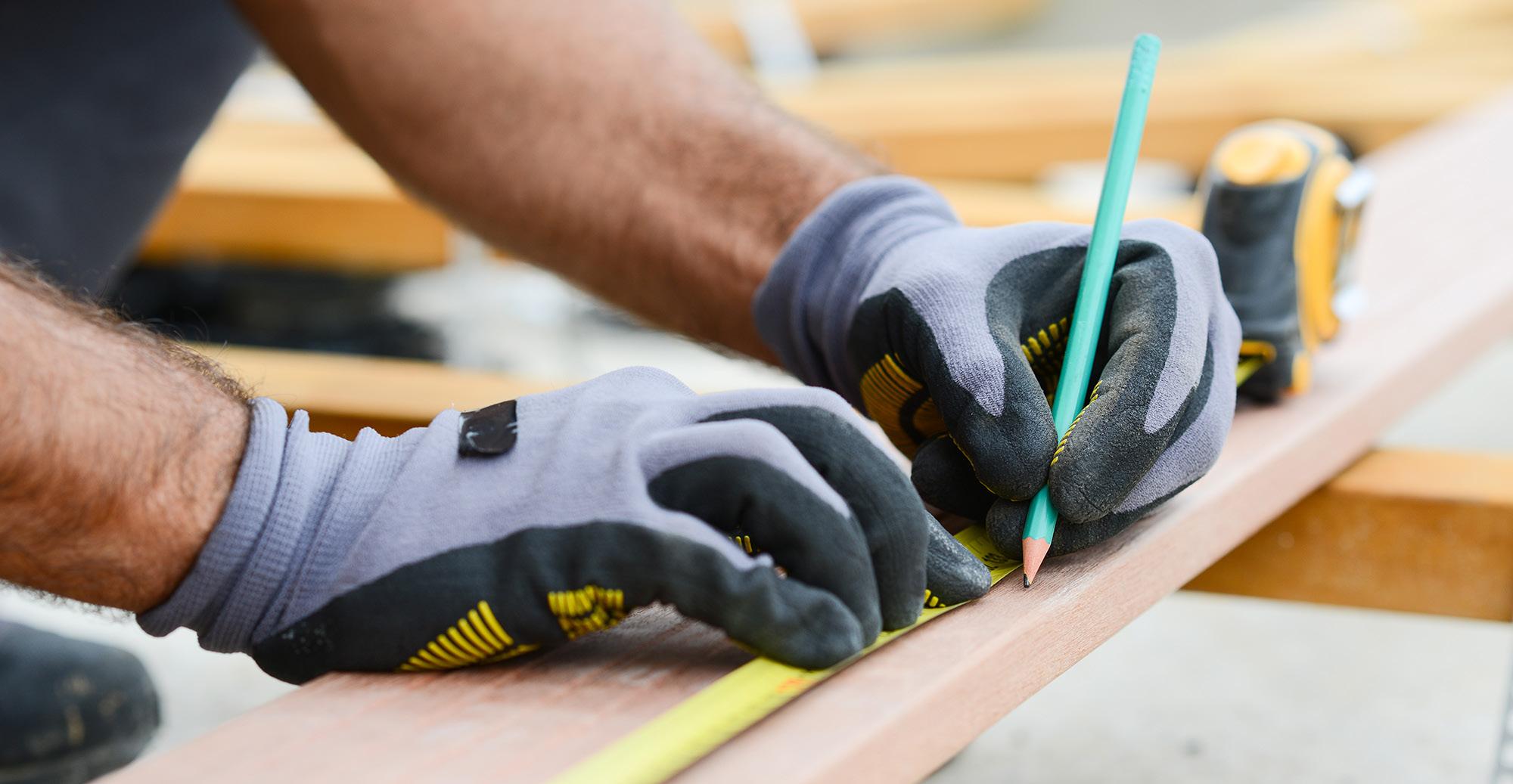
Let’s look at some other examples of building tolerance. All states produce a document which identifies acceptable building tolerances, they are all basically the same. The NSW document states that for the fitout of bathrooms, laundries, kitchens etc a setout can be 5mm from the designed position (and even further for elements longer than 1m). Yet AS 1428.1 provides no tolerance in some cases.
We find from AS 1428.1 that a step between two adjacent floor finishes is 3mm or 5mm if bevelled. Consider a tiled floor against a metal weather strip. This strip will be true and level, but the allowable tolerance between one tile and another is 2mm so at one point the strip may protrude the allowable 3mm and on the adjacent tile it will be 5mm. In this case I would expect the tiler to rectify this as he is in control of the interface but technically the tiling is compliant.
Finally, it is worth looking at the dimensions given in AS1428.1. Some dimensions are given as a maximum or minimum, this infers a range up to that dimension is acceptable, some are provided as a range, some are provided as a +/- and some are provided as a fixed dimension which then infers no variance is permitted. In many cases I cannot see the reason for such tight dimensioning. For example, in AS 1428.1-2009 the height for the shower hose attachment is given as 700mm +/- 5mm. Is the location of that so critical that it can only vary +/- 5mm, particularly when there is no horizontal dimension provided? Apparently not, because the next version of the standard will show it higher and in a zone, not a fixed location.
How to resolve the issue of tolerance? As I said at the start the Standards Committee decided that it was not their problem, the architects and builders had to sort it out. I agree that architects do not always make adequate allowance for building tolerance, but we should also acknowledge that building is not a precise art and provide more flexibility in the requirements of the access standards. In some cases, we may be justified in requiring particular dimensions but there is not a lot of science to much of AS1428.1. Let’s take door circulation spaces as example. They are all based on a notional 80th percentile wheelchair from the 1980s, a wheelchair which does not exist. A scale model was made of this fictitious wheelchair and moved around by hand to simulate its use. Then to play safe 50mm was added to each touch point to give some tolerance (so it does exist in access). Then when we decided to move to the 90th percentile wheelchair, again fictional, a model of this wasn’t made and tested. Just 50mm added here and there to the 80th percentile. This does not have a lot of science behind it. I think we have to be realistic about what we require and acknowledge the environment in which we are working.
Finally, let’s consider the BCA, clause D2.13 provides requirements for stair risers and goings. The clause requires that they be a constant height and length in a flight but, in acknowledgment of the need for building tolerance since the 2019 version, has accepted that they can vary – up to 5mm for adjacent risers and goings and up to 10mm overall within a flight.
We, as access consultants, will gain more respect from the building industry if we understand their issues and try to work together to create useful standards.
