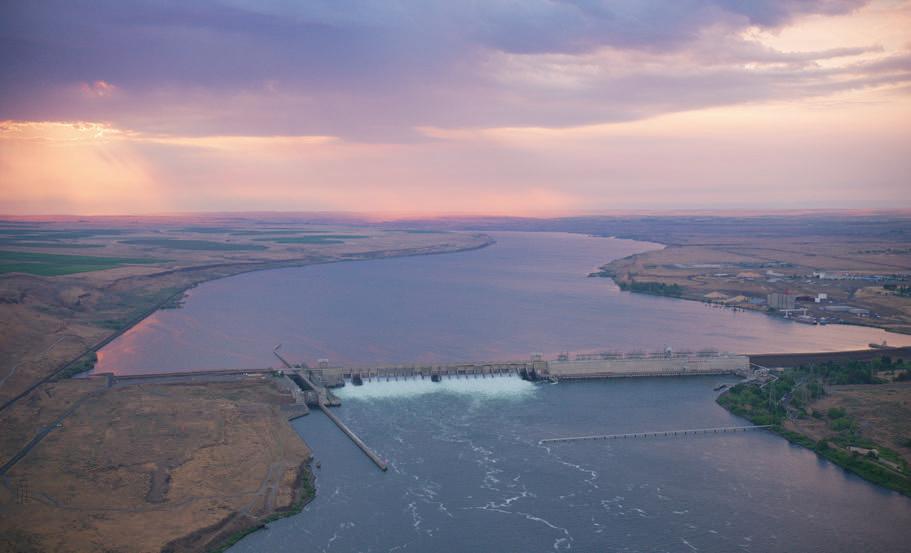
10 minute read
PRESERVING INFRASTRUCTURE DELIVERS SUSTAINABILITY
BY STRUCTURAL
Water management, transportation networks, structures that protect us from natural disasters, ports, and buildings – these are critical to society and are at the heart of USACE Civil Works activity throughout the United States. As the structures that make up these vital assets age and decay, what is the best path to maintaining continuity of service with sustainability in mind?
In 1987, the United Nations Brundtland Commission defined sustainability as “meeting the needs of the present without compromising the ability of future generations to meet their own needs.” As concrete infrastructure ages, it is often demolished, and new infrastructure is built in its place. How does this cycle balance with meeting the needs of future generations?
Building new concrete infrastructure consumes massive amounts of natural resources and has a significant overall impact on the environment. As society continues to grapple with the challenges posed by climate change, resource depletion, and rapid urbanization, extending the life of existing concrete infrastructure comes into focus. A recent paper published by International Concrete Repair Institute¹ states,
The thoughtful extension of the life of existing structures through careful repair and a commitment to longterm maintenance is a responsible answer to the reality of reducing our impact on the environment.
Increasing the service life of existing infrastructure is the essence of delivering a sustainable future, and the pathway extending the service life of reinforced concrete structures is proactive asset management.

The Power of Asset Management
Asset management has been defined as “a systematic process of developing, operating, maintaining, upgrading, and disposing of assets in the most cost-effective manner possible.” It is in the words systematic process that we begin to understand what is required to properly manage assets.
Developing a systematic process for managing concrete structures begins with discovering and analyzing their current state – the existing condition – and continuing to monitor and analyze, while simultaneously addressing repair needs at early onset, and employing protective measures when advantageous. As demonstrated in Figure 1, the cost of repair increases exponentially as concrete ages and can be kept lower by managing the assets proactively.
The total cost of ownership of concrete structures is greatly impacted by the owner’s willingness to invest proactively in life-extending repairs and protection. Reactive owners spend more in the long term. A lot more.
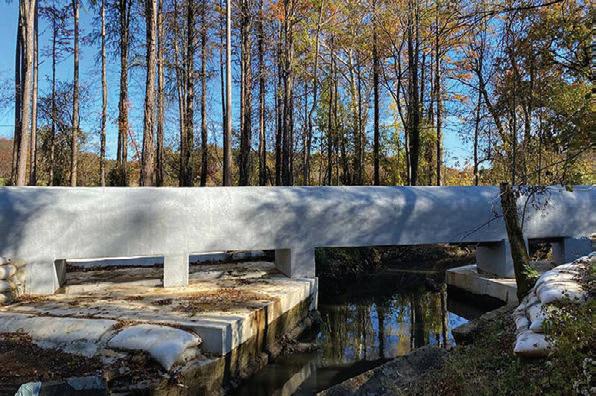
First Steps
Once the decision to put an asset management plan in place for concrete structures, what is the next step? As with other assets and systems being managed, best practice for concrete structures leads down a path of seeking assistance from subject-matter experts (SMEs). This assistance from SMEs can be internal or external.
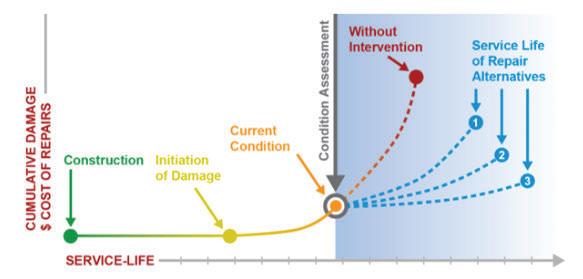
Concrete structures – the building envelope, dams, equipment foundations in a hydroelectric plant, or beams and piles on a port structure – are most often treated as secondary systems. And for secondary systems, partnering with external SME resources adds value because it brings the expertise to USACE and creates more time for internal resources to spend on primary systems.
Depending on the specific situation, the development of the asset management program will include elements such as inspections, analysis of inspection results, consultation on repair and protection options and contracting of elected repairs and/or protection systems. The team assembled should have an understanding and experience managing concrete assets.
Whether in-house, a hybrid model using internal and external resources, or turnkey outsourcing, the most important part of the word proactive is the active part. Whatever path is chosen, beginning the process of learning about the concrete structures being managed is better than the unknown of addressing concrete repair needs reactively.
Old-School Asset Management
A typical approach used for many years is to divide the asset management into steps and manage them separately as part of an overall program. This creates a compartmentalized program with a process that may look like the following cycle:
1. Owner procures and awards program management to an engineering firm.
2. Engineering firm executes inspection using subconsultants and subcontractors.
3. Inspection results are prepared and provided to Owner.
4. Engineering firm analyzes inspection results.
5. Owner and engineering firm review results and analysis.
6. Results and analysis create tiers of priorities ranging from continue to monitor to long-term to short-term repair needs.
7. Engineering firm prepares options analysis for Owner, and options are considered for short- and long-term repairs.
8. Owner determines repair scopes.
9. Engineering firm designs the repairs.
10. Engineering firm provides the repair designs to Owner.
11. Owner provides the design to bidding contractors and procures the repairs.
12. Owner awards to a repair contractor based upon bid results.
13. Repair contractor mobilizes to complete repairs.
14. Repairs are implemented by repair contractor.
Whether exactly like this, or similar, the above process takes place within effective asset management programs in many industries for concrete structures on an incremental timed basis. The frequency of inspections is typically determined by the criticality of the structures in the program.
The challenges in this old-school approach to managing concrete assets are significant – and lead to a lack of continuity and overspending. Each firm that is engaged has to be oriented to the site, the structures, proper procedures, and the Owner’s team. Consider also that each time a repair scope is completed it can be a different contractor with a different approach to repair implementation in the field.
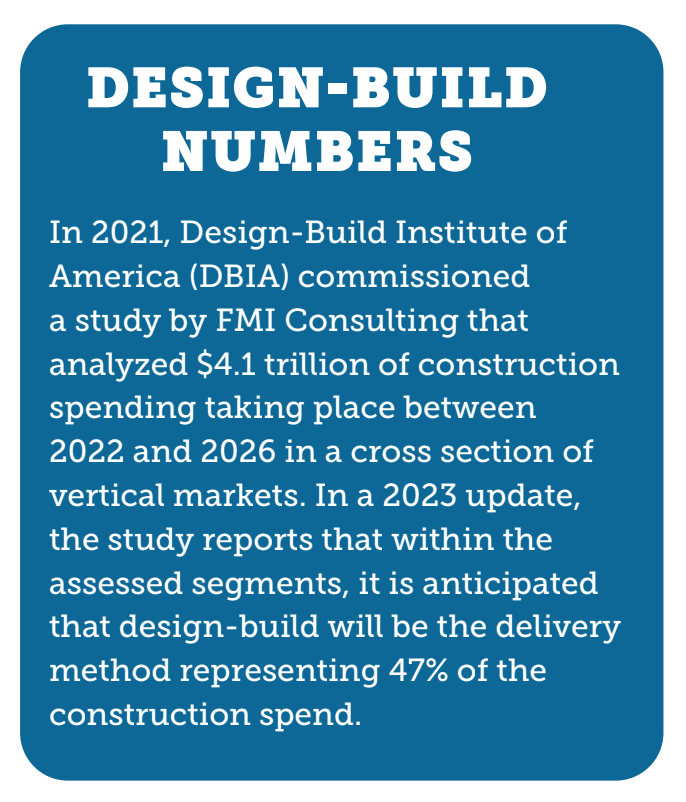
Another challenge is how late the repair contractor is brought into the process. The awarded contractor gets a set of plans, potentially a copy of the inspection report, and typically walks the site one time prior to establishing a price to the designed repairs. Because of this, it is not uncommon for the price of the repairs to exceed budget.
Any gap between what is designed and how the solution is constructed is resolved through change orders. The change order process leads to delays, and the costs escalate in two dimensions. This is especially relevant in managing concrete because if repairs are delayed for years after an inspection, the deterioration can worsen, leading to scope growth. In addition, the preparation of the concrete can lead to larger repair areas as sound concrete must be exposed to ensure the repair bonds properly.
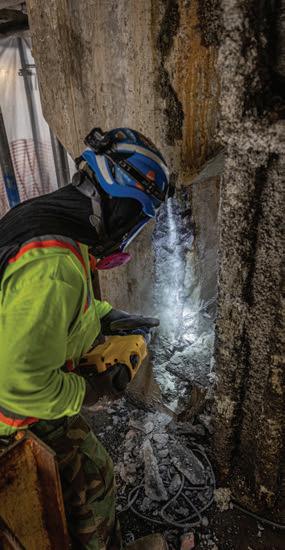
In long-term programs, these steps are repeated over and over with potentially different contractors each time a repair takes place. While concrete assets can be managed using this old-school approach, it is not the most efficient or cost effective.
21st Century Asset Management: Investigate-Design-Build™
Collaborative delivery of projects through design-build is a growth area in construction. Its growth can be attributed to overall efficiency and effectiveness in speeding up construction and slowing down cost overruns and change orders.
Design-build is a preferred project delivery method for addressing existing structures for similar reasons but amplified by the variables that are part of every repair project. It is most powerful when an extra step is added up front – investigation – creating a turnkey solution for managing concrete assets – Investigate-Design-Build™ (IDB™).
Programmatic management of concrete assets using an IDB™ approach creates a process similar to the following (subject to adjustment to meet specific USACE needs):
1. Owner procures and awards a multiyear program to a qualified IDB™ firm, such as Structural.
2. IDB™ Team established as Engineer Partner and Repair Contractor. In the case of IDB™ , the program is managed by the design-build partnership (i.e., Structural and its Engineer Partner). The IDB™ Team consists of technical, safety, and construction team members and focuses on root cause analysis, solution building based on budgetary requirements and the highest quality field implementation.
3. IDB™ Team, in collaboration with the Owner, develops asset management plan including investigation cycles and contingency plans.
4. IDB™ team executes inspection and implements any immediate repairs necessary during the allotted schedule.
5. Inspection results are prepared, analyzed, and provided to Owner, along with repair options, preliminary design(s), schedule and firm pricing information.
6. Owner evaluates, in consultation with IDB™ Team, and selects shortand long-term repair plans.
7. IDB™ Team implements repairs as scheduled using firm pricing established.
8. Continued monitoring of structures through program takes place by IDB™ Team and subsequent repairs are implemented as needed.
IDB™ brings all stakeholders together as a team from the outset, which creates a more effective program. The efficiency gained by having the engineer and repair contractor working together throughout the program is exponential. The repair contractor is on-site providing safe access during the inspections for the engineer, and over the course of the program hundreds of owner hours are saved without the need to ramp up different contractors as outlined in the old-school example process.
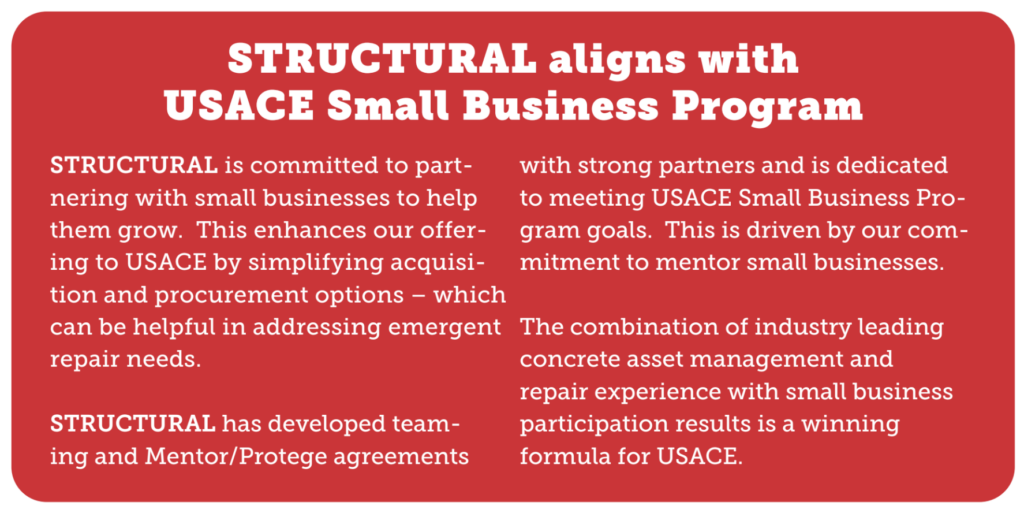
As inspections are taking place, the repair needs are being evaluated and preliminary designs are taking place. These designs are informed in real time with constructability reviews completed by the same project management that will be overseeing repairs in the field. This is often where unique solutions are found to address the owner’s needs. In addition, minor immediate-need repairs can potentially be completed during the inspection time window, streamlining the entire program.
Major repairs, when needed, can be intricately planned to save time and money, because through IDB™ delivery, all stakeholders participate in building the plan around the owner’s budget and schedule requirements.
Accommodating Changes
The same sustainability concepts apply to the upgrade of infrastructure to accommodate operational modifications, other changes-of-use, or code compliance. Increasing the loads on existing concrete infrastructure, for instance, does not necessarily mean having to build new concrete infrastructure to accommodate.
A recent example is a gantry crane upgrade at McNary Dam, which required structural enhancements to 48 concrete beams. Using an IDB™ approach, USACE and Structural safely and successfully implemented an innovative 1-sided enlargement of the beams, which streamlined the project schedule and implementation of the gantry crane upgrade. To learn more about the McNary Dam project, click here or visit www.structural.net/mcnary/.
Looking Forward
Bringing engineering, technology options, repair contracting alternative procurement methods together is what Structural delivers to long-term concrete asset owners, like USACE, through IDB™ . Over time IDB™ drives the lowest total-cost-of-ownership and effective, efficient sustainability of concrete structures.
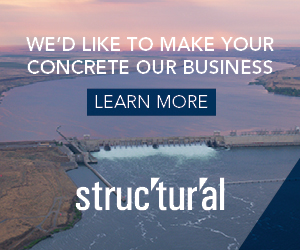
As we look ahead, fewer resources may one day necessitate placing a higher priority on preserving existing concrete infrastructure over building new. While building new structures may continue to thrive in our generation, we can also look forward by investing time and energy into maintaining and extending the life of the concrete structures all around us.
______________________
¹Sustainability for Repairing and Maintaining Concrete & Masonry Buildings – by ICRI Committee 160, Sustainability: Donald (Leo) Whiteley (Chair), Kurt Goethert, Fred Goodwin, H. Peter Golter, John Kennedy, Tanya Wattanberg Komas, Jessi Meyer, Matthew Petree, Bryan Smith, Stephan Trepanier, David Whitmore, and Pat Winkler
______________________
The appearance of or reference to the U.S. Army Corps of Engineers, the U.S. Army, the U.S. Department of Defense, or the U.S. Government does not imply or indicate endorsement by any of these entities.