
13 minute read
Airplane part manufacturing gets compact with carbon nanotube
Airplane part manufacturing gets compact with carbon nanotube Aerospace-grade composites can now be produced with carbon nanotube film, eliminating the need for huge ovens or autoclaves.
weakness in a composite,” Wardle says. “An autoclave can push those voids to the edges and get rid of them.”
Advertisement
Straw pressure Part of Wardle’s work focuses on developing nanoporous networks — ultrathin films made from aligned, microscopic material such as carbon nanotubes, that can be engineered with exceptional properties, including colour, strength, and electrical capacity. The researchers wondered whether these nanoporous films could be used in place of giant autoclaves to squeeze out voids between two material layers, as unlikely as that may seem.
Amodern airplane’s fuselage is made from multiple sheets of different composite materials, like the many layers in a phyllo-dough pastry. Once these layers are stacked and moulded into the shape of a fuselage, the structures are wheeled into warehousesized ovens and autoclaves, where the layers fuse together to form a resilient, aerodynamic shell. Now, MIT engineers have developed a method to produce aerospace-grade composites without the enormous ovens and pressure vessels. The technique may help to speed up the manufacturing of airplanes and other large, high-performance composite structures, such as blades for wind turbines.
Out of the oven, into a blanket In 2015, Lee led the team, along with another member of Wardle’s lab, in creating a method to make aerospace-grade composites without requiring an oven to fuse the materials together. Instead of placing layers of material inside an oven to cure, the researchers essentially wrapped them in an ultrathin film of carbon nanotubes (CNTs). When they applied an electric current to the film, the CNTs, like a nanoscale electric blanket, quickly generated heat, causing the materials within to cure and fuse together. With this out-of-oven or OoO technique, the team was able to produce composites as strong as the materials made in conventional airplane manufacturing ovens, using only 1 percent of the energy.
The researchers next looked for ways to make highperformance composites without the use of large, high-pressure autoclaves. “There’s microscopic surface roughness on each ply of a material, and when you put two plies together, air gets trapped between the rough areas, which is the primary source of voids and A thin film of carbon nanotubes is somewhat like a dense forest of trees, and the spaces between the trees can function like thin nanoscale tubes, or capillaries. A capillary such as a straw can generate pressure based on its geometry and its surface energy, or the material’s ability to attract liquids or other materials. The researchers proposed that if a thin film of carbon nanotubes were sandwiched between two materials, then, as the materials were heated and softened, the capillaries between the carbon nanotubes should have a surface energy and geometry such that they would draw the materials in toward each other, rather than leaving a void between them. Lee calculated that the capillary pressure should be larger than the pressure applied by the autoclaves.
The researchers tested their idea in the lab by growing films of vertically aligned carbon nanotubes using a technique they previously developed, and then laying the films between layers of materials that are typically used in the autoclave-based manufacturing of primary aircraft structures. They wrapped the layers in a second film of carbon nanotubes, which they applied an electric current to heat it up. They observed that as the materials heated and softened in response, they were pulled into the capillaries of the intermediate CNT film.
The resulting composite lacked voids, similar to aerospacegrade composites that are produced in an autoclave. The researchers subjected the composites to strength tests. “In these tests, we found that our out-of-autoclave composite was just as strong as the gold-standard autoclave process composite used for primary aerospace structures,” Wardle says. The team will next look for ways to scale up the pressure-generating CNT film.
For more detail, contact: Jennifer Chu, MIT News Office http://news.mit.edu/

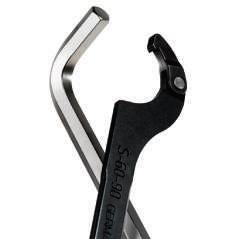
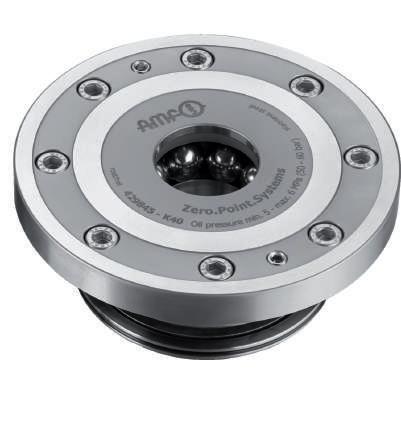
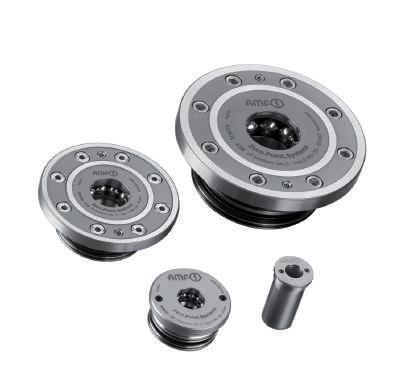
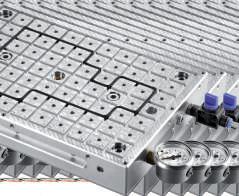
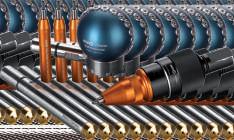
Energy supply system now easily configured online

Automatic interior separation and service life calculation An interior separation configurator is used in the online expert. It uses artificial intelligence or neural networks to determine the appropriate interior separation for the defined cable pool within seconds. Thanks to an integrated service life calculation, both for the energy chain and the individual cables, the customer can quickly and easily choose the most cost-effective system which safely meets their requirements. Another advantage: the intelligent tool constantly checks the configuration for plausibility, so the user can be sure the elements are coordinated.
New igus online tool enables a quick configuration of harnessed energy chain system. Quick and easy configuration of complete energy supply systems are now ensured by the igus e-chain expert. With the newly developed online tool, users can design their own guaranteed ready-to-connect energy chain system, in just a few steps.
The quick way to a ready-to-connect energy chain is made even easier with the igus e-chain expert. With the aid of the new free-ofcharge and freely accessible online tool, users can design their energy chain system using a smartphone, tablet or a desktop computer. Be it an unsupported, gliding or hanging application, the configurator determines the energy chain that is optimally suited. To do this, the user simply has to open the e-chain expert, select the unharnessed or harnessed cables, enter the application and environmental parameters, decide on the appropriate energy chain from a pre-selection and configure it. In the energy chain configurator, the user can choose from over 1,300 highly flexible chainflex cables tested by igus as well as over 4,200 harnessed readycable drive cables. These are tested and, like all igus cables, come with a 36-month guarantee. On the basis of the specified cables and the application data such as installation space, movement and environment of the energy chain, the customer can choose from a selection of 1,50,000 e-chain parts for the most cost-effective solution. All igus products are tested in its own 3,800-square-metre laboratory. Configure together as a team and order directly The user has the opportunity to share the current processing state in the online tool with other people at any time via e-mail or hyperlink. Several team members from different departments can jointly design energy chain systems online at any time and anywhere, and process the CAD data. With one click, you can download the configuration or put it in the shopping basket on the igus web shop. The ready-to-connect energy chain system can be ordered online as the online tool determines prices and delivery times for every application configuration. Alternatively, the customer can also request an individual offer for their configuration.
For more information, visit: www.igus.in
Fluid filtration for industrial fluids provided by BAPL
We at BAPL cater the fluid filtration requirements for industrial fluids at a very micro
level as per the requirement of the end user. Instead of just selling a standard product, we work with the end users to identify the pain areas and then we provide a suitable solution to overcome the problem. The products that you source from us works in a sustainable way at zero maintenance cost by supplying consumable-free product.
The typical applications in manufacturing industry are: • Water-based coolants • Polymer quenching • Neat cutting oils
Common problems observed with these fluids are: • Dirty fluid carry the micron size burr particles which creates scratch marks on the finish job
Contaminated fluid decreases the life of a tool To clean the tank, machine has to face breakdown which affects the production output Disposing these fluids is a major concern to the environment
Having an experience of 25 years in this industry, BAPL has developed a basket of products as a solution to the above problems, which will help you to save 50 percent cost on the expenditure on your process fluids. The products include: • Paper filtration system • Pressure driven centrifuge • Oil skimmer • Motor driven centrifuge
For more information, visit: www.centrifugallubeoilcleaner.com
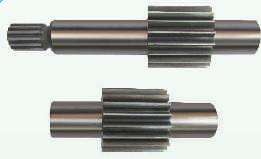
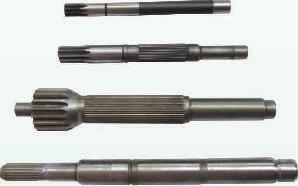



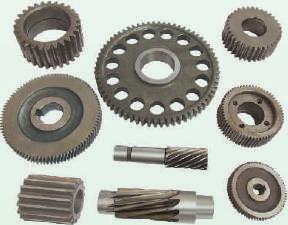
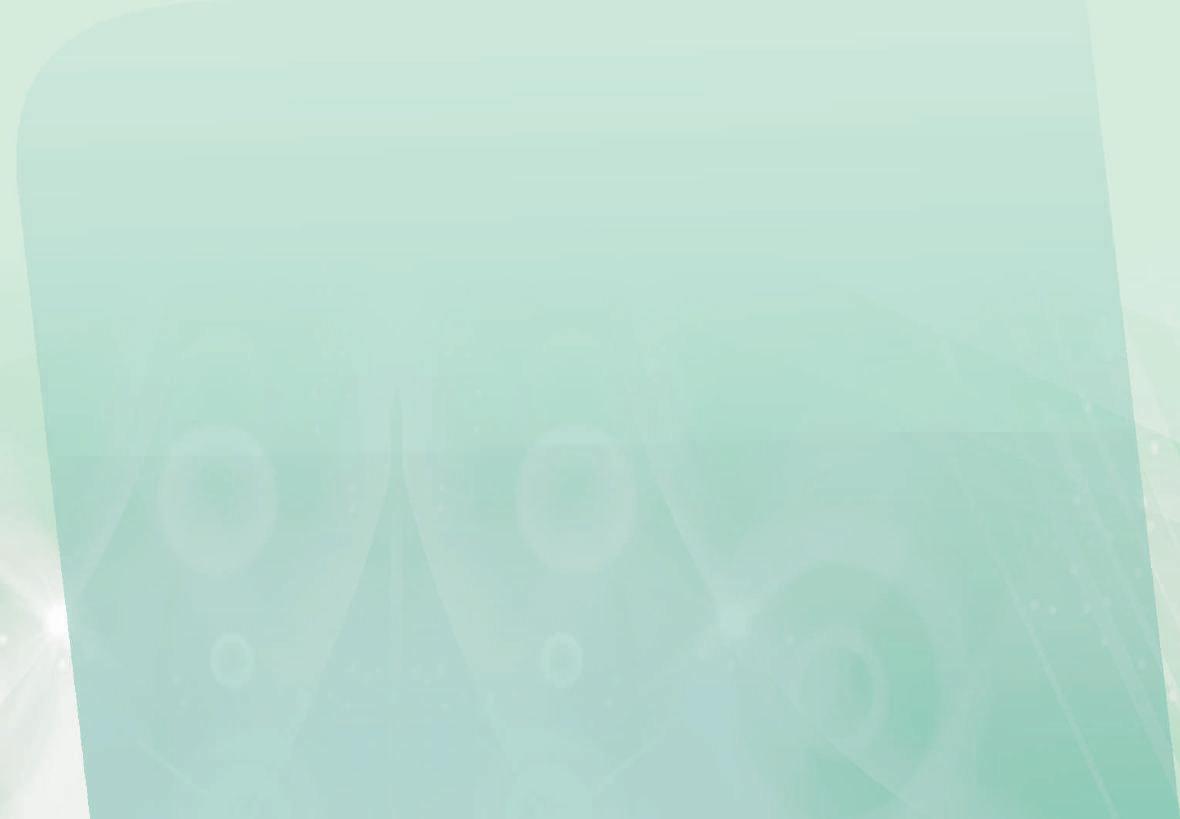
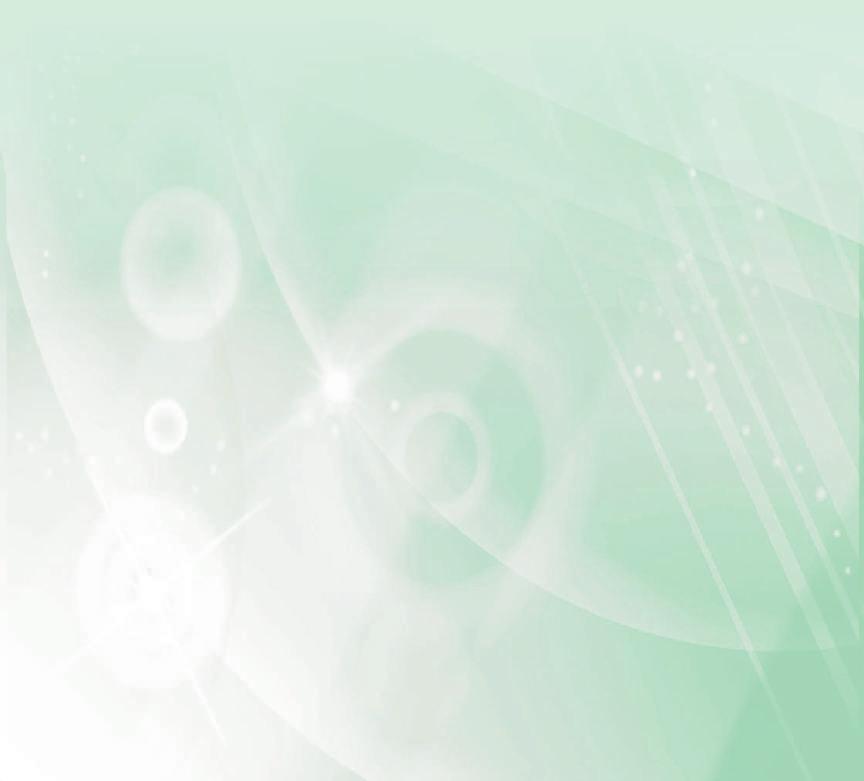
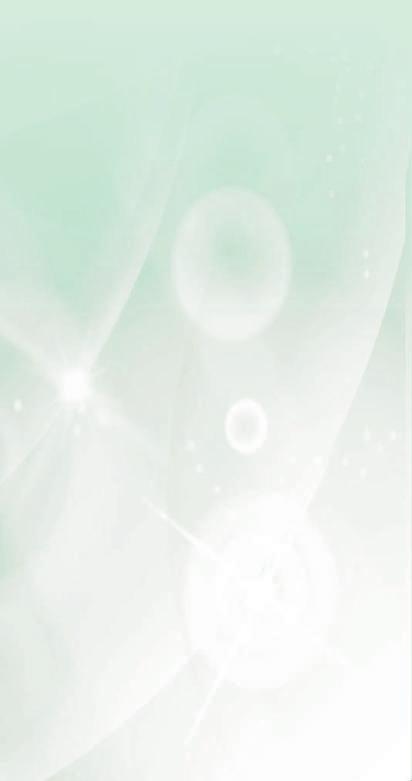
Making CNC grinding machines smart factory ready
benefits of a smart factory, each CNC grinding machine will need to be connected to a communication network.
Shifting towards smart factories does not mean scrapping the existing CNC grinding machines and having to invest in a whole new set of machinery. Here we take a look at what it means for CNC grinding machines to become smart factory ready.
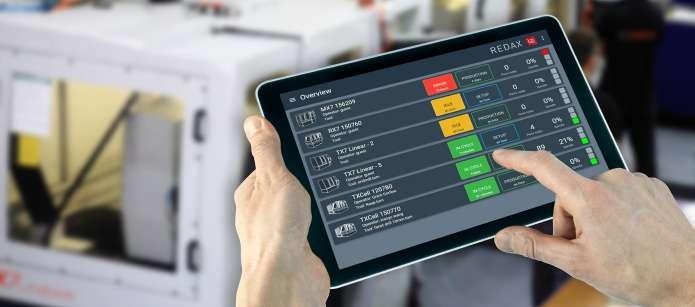
Smart factories are becoming the norm of the day in manufacturing, and companies are moving towards this space to improve their operational productivity and performance and stay ahead of the competition. But being smart factory ready does not involve completely revamping the existing technology in favour of modern, advanced equipment. It simply means upgrading some of the technology and changing the way the company thinks about how it operates.
Lucas Hale, Global Marketing Manager at ANCA CNC Machines, which is a company that provides practical, working solutions to extend unattended production, improve quality and ultimately deliver improved returns for increased bottom line profit, talks about how to go about this process.
Change the way you think about tool manufacturing In the factory of the future, running a factory won’t require a company to be as hands-on with what it produces anymore. Instead of a manual production line, it will have an integrated network of machines that is more efficient in manufacturing processes, intellectual property generation, tool design, customer responsiveness, cycle time, profitability… and the list goes on. Across the company’s business, automated machines will take care of the more laborious tasks before work begins.
With a bit of investment to upgrade your existing technology and facilities, you can reap the benefits of automation easily. Your team will be able to programme machines ahead of time, so that they are able to do what needs to be done throughout the day. And not only will your CNC machines manage the production, but they will also collect and analyse data and make automatic adjustments to production in real time to improve the way you’re running.
CNC grinding machines only need to be connected While the company will be able to make use of existing CNC machines, it will also have to embrace new technology. To work effectively with other machines and maximise the Having a machine connected to a network may seem daunting, but the benefits are unparalleled. The CNC machine becomes part of a smart, connected set of tools working together to make work easier. Depending on the age of the machine, the company can connect machines using either Wi-Fi (the best option to avoid messy cabling) or a cabled LAN connection. While newer machines are Wi-Fi-enabled, older machines can be retrofitted with a Wi-Fi adaptor and software drivers. Check with your vendor first to make sure the driver software is supported.
Exploit your niche, finesse your offering and charge accordingly As a small company, you’re able to offer a personalised service bigger business can’t. You understand your customers’ needs. You sell the precise product they need to keep their operation running. They need you as much as you need them. So, being small can be your greatest selling point. You can adapt to the market as it changes and respond to demand. Where potential customers may be frustrated by businesses with long lead times, you have the ability to turn things around quickly and with more flexibility. Customers wanting something you don’t manufacture yet can even be an advantage. With the tools and flexibility to make it happen, you can easily expand your offerings and show them how well you understand your niche.
This kind of specialisation is hugely valuable to a business. You’re not only providing labour and materials but access to years of knowledge and refinement. It’s been shown that customers will pay more for specialised products that offer this level of added value.
Embrace automation Most CNC machines, including those that ANCA produces, already come equipped with comprehensive, advanced software that allows flexibility in everything, from configuring set-up to adaptive processes like product gauging and automatic compensations, thereby freeing your team to work on more valuable tasks. By creating automated systems and processes, you’ll immediately have access to more information than ever before, and this is a huge benefit for you and your customers. Your machines will be able to alert you when you’re running low on materials. They will predict maintenance that’s required to keep them operating, so you avoid lengthy and expensive disruptions.
Better still, they can become part of a wider network of machines. Integrating with other factories will reinvent your supply chain process. Suddenly, your factory can integrate with your customers and your machines can speak to one another. Is your customer running out of a product you manufacture? The machine at your end can find out and start the production process without any intervention from you.
Move forward one step at a time Don’t worry; you don’t need to do all of this at once and
there are easy ways to add automation functionality: • Add after-market software or hardware accessories, such as lasers to measure tools in production and make sure they’re meeting required design and tolerances. • Retrofit with automation; robotic loaders mean lower costs and greater volumes. You can have a new robotic loader at a reasonable price installed into your machine to achieve the benefits oflights out or unattended machine production. • Enable machine connectivity on older machines through a Wi-Fi adaptor and software drivers to connect machines to each other and the wider factory. • Store tool files centrally with tools and wheel servers. Maintaining a database ofeach tool file that a machine can use for set-up is a great place to start with software. Your factory can store a whole range of files centrally, so each machine can access what it needs to get the process going.
Planning ahead for future success This might be brand new for your factory, and there are tricks you will need to learn. For example, did you know that if you’re moving jobs between machines, you will need to have the same version of software on each? And again this is an investment, but the efficiencies will weigh out the costs in a few months; it is about knowing what will be required to make your factory smart.
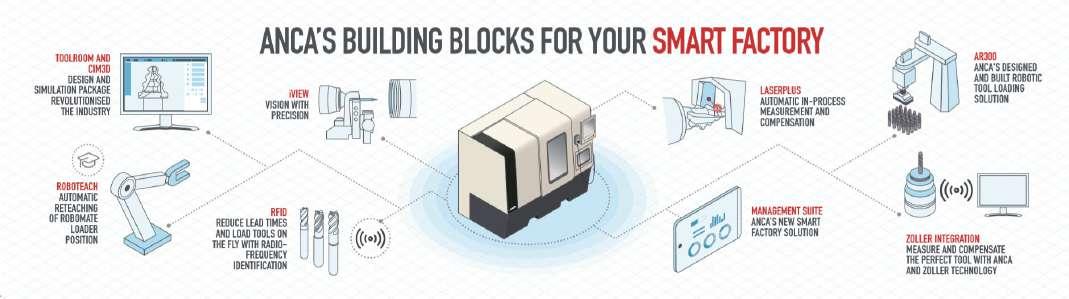
If scaled manufacturing is not your background, you might need more information before you scope out your strategy. ANCA can help you understand your specific requirements and also help you understand how to incorporate them into your supply chain. Whatever approach you take, you will need to invest in some degree of technology to keep your machines up-to-date and your operation functioning effectively. Without this, other companies will move ahead of you as they can produce more complex tools more efficiently. There are many ways to bring your CNC grinding machines up to speed for your smart factory. The most important thing is that you start.
For more information, visit: www.machines.anca.com
Compressed Air Treatment & Industrial Chilling

D ealership inquiries are solicited
Refrigerated Air Dryer
High Pressure Refrigerated Air Dryer
Heatless Air Dryer Water Chiller - Online
Water Chiller
Brine Chiller Micro Filter
Auto Drain Valves
After Cooler
Annair Drychill Tech (I) Pvt. Ltd. An ISO 9001:2015 certified Company Works: Unit No.101, I wing, Plot No-K1, Udyog Bhavan2, Additional MIDC, Anandnagar, Ambernath East, Thane-421506, Maharashtra, India Tel: 0251 262 0660 / 093209 50116 Email: sales@annair.com I www.annair.com