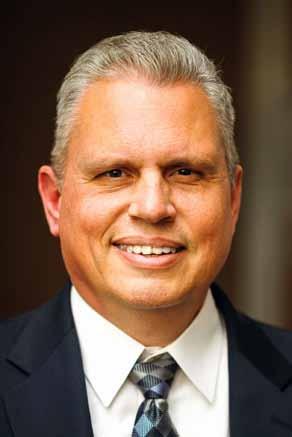
16 minute read
Xcelerating’ Digital Transformation: Siemens leads the way
Siemens has been providing a comprehensive digital twin and thread to the aerospace and defence industry to successfully execute the programmes that are transforming air travel, space exploration, and defence. How crucial is the digitalization of the industry in the present age and how to seam and support the process with its product and services? As companies seek to develop new products faster Dale Tutt and manage their costs Vice President, better, they also need to Aerospace and Defense Industry, Siemens Digital Industries Software manage their risks. And quite frankly, they need to develop high-performing products. Siemens, during the With all the innovation challenging times of Covid-19 going on, all the software pandemic, has been providing development, and the amount solutions to its partners and of electrification we’re seeing in new products, the benefits that customers to accommodate you get when you start using a changes and adapt quickly, comprehensive digital twin and helping them not just to the digital thread along with the survive but to thrive in solutions within our Xcelerator portfolio enables companies in this digital era. Dale Tutt, these industries to thrive in this age the Vice President of of digitalization. Our Xcelerator Aerospace and Defense portfolio, brings all our products Industry for Siemens and services together, and can scale to any size of the company. They Digital Industries Software, include CAD, PLM, manufacturing says his company will solutions, model-based systems continue invest in already engineering (MBSE), supply chain powerful manufacturing management and product support. It is also important to remember that solutions and foster Siemens, first of all, is a manufacturing digital transformation, company, and we have real-world ‘which is critical for the experience in the digital transformation A&D industry’. Excerpts of factories. We are able to leverage our own experience, as well as our Xcelerator from an interview: portfolio to help customers through their digital transformation. Before customers make any large investments in a new factory, they need to be able to simulate it and have the confidence that it’s going to work, whether it’s going to accelerate their process and increase their productivity. The power of that digital transformation is how much faster our customers can move when it’s time to start ramping up the production rate. If they are building aircraft, how can they move from getting the first airplane out the door to building 10, 20 or 50 a month? True digital transformation requires a strong understanding of your manufacturing processes. This is where what we call “virtual commissioning” becomes important. A customer can use simulation to validate whether their factory is going to meet their needs. Then, as they move from that initial factory setup to the production line, there is the continual opportunity to optimize production by leveraging data from the factory floor. Once the factory is up and running, the digital twin can be used to validate and optimize the production line and processes throughout the life of the factory. This is how companies become more flexible, better able to accommodate changes and accelerate all of their processes through the use of the digital twin. Digitalization is critical for these industries right now.
Who are the major clients worldwide?
Advertisement
Siemens serves almost every major A&D company in the world right now, as well as many medium and small-sized companies and start-ups. The list of major companies includes Boeing, Lockheed Martin, Northrop Grumman, Rolls Royce, General Dynamics Land Systems Division and Raytheon Technologies. In Russia, Sukhoi and United Aircraft Corporation are our customers. We also have customers in China, Japan, and Korea – really all over the world. In India, we work with clients such as HAL and numerous major Indian defence labs.
Additionally, major space players worldwide are using Siemens’ Xcelerator, including companies such as SpaceX, United Launch
Alliance and Rocket Lab. We have a lot of companies using our solutions worldwide in all sectors of aerospace and defence.
Global unrest is driving a significant investment in land defence systems modernization, and there is a high demand for technological advancement in sustainable weapons systems. What are the products and services offered by Siemens in land Defence system?
When we talk about products, services and solutions used in land defence systems, it’s really the same tools and solutions we offer throughout the A&D industry. Whether it’s in modelbased systems engineering (MBSE), product design, simulation & analysis, manufacturing or product support, the same tools and offerings are used for the design and development of land defence systems. We’re able to provide defence companies with an end-to-end and closed loop solution for the full product life cycle.
The pandemic has certainly created some challenging times for us, and a lot of our customers have gone through major changes as a result. But, the companies which were already on a path towards digital transformation were able to adapt more quickly.
Aerospace and defence industry in India has been thriving over the last decade with a consistent boost by central government through various policies. How does Siemens look at Indian market for its business? Could you shed some light on business in India?
As we look at India, we see huge growth opportunities for the A&D industry. Today, there’s a huge push to develop Indian products and Indian aircraft, to develop indigenously. We see huge potential in India with many growth opportunities for companies starting to develop new aerospace and defence products. Our role as a leader in digital transformation for aerospace and defence is to bring the Xcelerator portfolio to companies both big and small. We are helping customers with their digital transformation, and as a result of implementing our products, we see these companies designing, developing and verifying new products faster as they move into their certification programmes. Just as important is helping our customers for a smooth transition into manufacturing and product support. We see the business opportunity in India as a way how we could partner with these companies and help them be successful.
The COVID-19 pandemic has affected all sectors of industry over the last seven months, thus testing the endurance of most leading companies. How Siemens has managed to overcome the challenges posed by the pandemic?
The pandemic has certainly created some challenging times for us, and a lot of our customers have gone through major changes as a result. But, what we are witnessing is that the companies which were already on a path towards digital transformation were able to adapt more quickly as they moved into this remote work environment. Companies needed to make adjustments to how their factories were set up, and we were able to work with them providing solutions, for example, that enabled them to revise how their factories are laid out to ensure safe social distancing, while still maintaining productivity levels. Siemens has also worked with companies to add more automation. It’s really about working with our customers through this difficult period not only to help them survive, but to come out stronger and better positioned to produce faster with less cost as the economies around the globe recover.
In the quest to make products lighter yet stronger, manufacturers are increasing their use of composite materials in both aerospace and defence industries. Siemens Simcenter is at the leading edge of composite analysis and is widely used. Could you talk more about Simcenter?
While Siemens adds value through the individual solutions around design, analysis and manufacturing, the area
in which our customers see the most value is our digital thread that provides continuity from requirements into design, analysis and then into the testing and actual fabrication of the part. Through this comprehensive digital thread, the entire process can be completed as efficiently as possible with no need for data translations from engineering to manufacturing. It’s a fluid and seamless process that starts with Fibersim, which is integrated with our NX software for composite design and analysis. It is then sent to Simcenter to be analyzed for structural integrity, which is extremely important, especially for aerospace where the structures need to be as light as possible, yet as strong as possible. As the product moves from engineering into production, the digital thread continues with manufacturing execution systems and manufacturing planning systems. It further extends into the automation that’s used to build the parts and then after the parts are produced, for analysing and actually inspect those parts and to close the loop both on the quality processes and the manufacturing processes to ensure that the manufactured part meets the requirements of the design.
Model-based systems engineering (MBSE) also plays a major role here. It’s a big part of the composite design and manufacturing process. Through an MBSE digital thread, aircraft level requirements flow down into the structure and those requirements then flow into individual parts. Adhering to the most stringent requirements during the design of the product makes it easier to verify and validate
that those requirements are met in the end product. An MBSE digital thread streamlines and maintains connectivity back to the requirements from design through manufacturing and into use, creating a closed-loop environment.
Finally, I would like to mention additional technology that we see on the factory floor. For example, electronic work instructions as well as augmented reality (AR) can help ensure technicians are not just looking at where the ply layouts are located, but are able to incorporate newer visualizations. This can free up technicians from managing a lot of paper. The information is all digitalized and readily available. They can see how the parts move. As our customers develop more complex products it’s important to bring more visualization to the factory.
Siemens Digital Industries Software has developed a new approach to assess the fatigue performance of 3D printed components to improve the understanding of the printed performance of the printed product. Could you elaborate more on Siemens advanced 3D printing technologies?
Additive Manufacturing (AM) holds a lot of promise for the A&D industry, and will eventually change how we design and manufacture components, as well as how we support products in the field. As manufacturers adopt additive, they will need to address regulatory challenges and understand how to optimize the performance of the printed component, which is crucial for aerospace products. And, as leaders in additive manufacturing, Siemens Digital Industries Software is developing and delivering simulation-based solutions to improve the understanding of the material structure and predict the performance of printed components.
One of these challenges for additive is the fatigue performance of printed components, since the AM process is highly dependent on the geometry of the parts - making it extremely challenging to predict the performance of AM materials. The key factors that influence fatigue performance include the microstructure of the printed materials, porosities within the printed component, surface roughness and residual stresses that result from the printing and sintering processes. The combination of these factors makes it difficult to have a single mathematical model to predict fatigue performance. If we are going to use AM for safety critical, load-bearing components, it’s vital that our customers be able to predict the effects of these additive manufactured-induced local artifacts on the fatigue performance of the part.
At Siemens, we have developed a new approach to assess the fatigue performance of 3D printed components by leveraging the power of machine
learning (ML) to develop a material model that can predict the effect of the AM-induced local artifacts on the fatigue properties of the material. Using ML, we are able to develop the fatigue properties, represented with SN curves, using a limited set of training data that is experimentally determined for different conditions such as orientation of the build, different surface treatments, and heat treatments, and then use this to predict the SN curves for untested conditions. Using ML, you are able to quickly develop a material model for your printed components that is flexible and requires limited testing to develop. With the AM-enhanced durability simulation in Simcenter 3D Specialist durability, you get the best of both worlds using experimental data and physics based modeling to improve your understanding of the fatigue performance of your printed parts. We are probably the only company that offers this type of approach to additive via our end-to-end digital thread.
The Royal Australian Navy has completed an overhaul of its configuration management framework and supporting information systems with the addition of Siemens Teamcenter aerospace and defence software. What is the role of such a tool for the navies worldwide?
We are seeing a lot of Navies, Air Forces, and I would extend this to Defence Departments in general, using the comprehensive digital twin and Teamcenter within the Xcelerator portfolio to manage product support. If the customers execute a major upgrade, they use Teamcenter to manage all of that data. The role of this tool, given the vast amount of information it takes to design and build a warship, is to store and manage data over the lifetime of that ship. Naval ships have extremely long lifecycles that may last 50 to 75 years and customers need to be able to manage each configuration and understand what work has been completed to maintain that ship throughout its entire lifecycle.
Teamcenter provides the best configuration management framework in the market today. The tool allows customers to know every serial number of each ship, all its configurations, and how well each configuration has been maintained. Because the ship builders have this information at their fingertips, they can start planning the addition of a new capability, like a new radar system, or if they want to replace an existing radar system. They have all the knowledge about how the ship has been constructed, and how it’s been maintained. They are able to quickly bring in new capabilities and do it faster, while reducing cost – all with less risk because they have confidence in knowing the configuration and knowing they are not going to have any surprises when they start doing the modification in the depot. I think that’s where companies are seeing the benefit of using Teamcenter in the Defence Departments around the world, and certainly with the Navies and Air Forces such as the Royal Australian Navy.
Digital transformation will be critical for the manufacturing industries to increase productivity, flexibility and accelerate innovation as leading service
provider and digitalization. What is the road map ahead for Siemens? Could you share the goals for the coming years?
When we look at Siemens’ goals for the coming years, we want to continue to work with companies to develop and provide new solutions to help customers improve on how they execute their programmes. We want to help them develop and certify new products faster, be more flexible in the manufacturing processes, and to help them meet the innovation challenges
OshoCorp Global has been accorded project sanction order for development & supply of 125mm APFSDS specialised ammunition for its mainstay battle tanks as per Make II guidelines of Ministry of Defence, Government of India. The selection process has been conducted over three years.
The 125mm APFSDS (Armour Piercing Fin Stabilised DiscardingSabot) ammunition is the primary tank ammunition, utilised for destruction of enemy tanks. The advent of superior protection technologies now available globally, results in improved protection levels of Armoured Fighting Vehicles (AFVs). The aspect of DoP (Depth of Penetration), which defines the terminal effects of the ammunition, is a major consideration to defeat the enhanced protection levels of AFVs.
Ashutosh Khate, CEO, OshoCorp Global said that the company is developing and manufacturing an improved APFSDS Ammunition with Global Outreach for Collaborative Partnerships was held under the aegis of Department of Defence Production, Ministry of Defence through SIDM.
This webinar was part of the series which are being organized with friendly foreign countries to boost defence exports and of the future such as more autonomous aircraft, green propulsion, urban air mobility and high-speed transportation. We will continue to develop more powerful solutions for MBSE in order to accelerate product development. We plan to add more simulation and analysis tools that will replace physical testing with virtual testing to accelerate or streamline certification processes. We will continue to invest in our already powerful manufacturing solutions, bringing more simulation to support minimum DoP of 530mm and higher, in order to enhance the lethality, within the existing ‘safety’, ‘consistency’, and ‘shelf life’ criteria. This ammunition will be fired from the existing barrels, presently fitted on the T-72, T-90 tanks.
OshoCorp design & engineering team has been working on development of 125mm APFSDS Ammo project as per the end-user requirements and confident to manufacture the same as per the Make II guidelines of Indigenous content. Initially there is need to develop upto 250 rounds each for T-72, T-90 tank platforms for trial and approval, subsequently produce Quantity 85,000 rounds of ammunition. This project is being executed by OshoCorp’s weapons and Ammunition achieve defence export target of $5 billion in the next five years.
Key officials from both sides participated in the webinar and spoke about the need to leverage opportunities for modernizing armed forces and in indigenization of the defence industry.
Indian companies such as L&T Defence, Ashok Leyland Limited, Bharat Forge, Tata Aerospace and virtual commissioning of production lines, augmented and virtual reality (AR/VR) to improve the technicians’ experience, and data analytics that will help companies enhance and further optimize their production lines and processes. And finally, we will continue to extend these solutions to enable our customers to improve their product support processes. We will continue to partner with our customers to foster their digital transformation, enabling them to not
OshoCorp receives 2300 Cr. Army order for 125mm APFSDS Tank Ammunition
just survive, but thrive in the digital era. division “vSalute”, said Khate. The project will help our country towards self-reliance in specialised Ammo manufacturing technology and fulfill the Prime Minister’s vision of AtmaNirbhar Bharat. Col PK Juneja, Head Special Projects at OshoCorp, said that the current project cost is more than INR 2300 Crores (USD 330 Million) and it has huge potential to generate future domestic & export business which can be many times more than the current project cost, as ammunition is a continuous requirement and current demand is based on backlogs. In the export market, the countries using T-72and T-90 tanks can be benefited by purchasing India
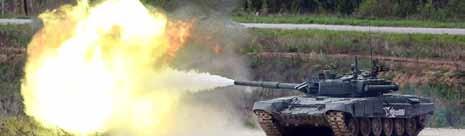
India- Indonesia Defence Partnership Expo
Awebinar between India and Indonesia with the theme “Indian Defence Industry
developed 125mm APFSDS Ammunition. Defence, MKU, Goa Shipyard Limited and Bharat Electronics Limited. made company and product presentations on major platforms / equipment. From Indonesian side PT. Pindad, PT. Pal, PT. LEN, PT. Dahana and PT. Dirgantara made presentations.
The webinar was attended by more than 150 participants and more than 100 virtual exhibition stalls have been set up in the Expo.