
3 minute read
healthcare laundry Introduce ERP software and digital companions to
Introduce ERP software and its digital companions to stay ahead of the curve
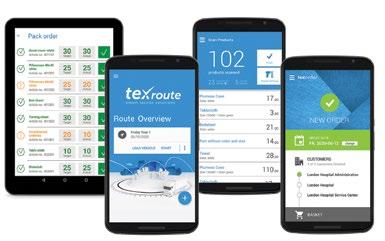
Advertisement
ERP software makes procedures comprehensible, simplifies processes and helps the company to organise the workflow. If innovative app solutions are added, the package is complete. Data is available in real-time, from anywhere and at any time, now we are talking about end-toend digitisation.
It is also becoming increasingly important for medium to smaller textile care companies to stay up to date. The introduction of an ERP software solution can help, especially for industry-specific tasks, such as those encountered on a daily basis. Software tailored precisely to the needs of a modern textile service provider is the tool of choice.
Processes must run optimally, be perfectly co-ordinated and deviations must be identified quickly. To achieve this, processes and data must be transparent. “In future, modern and future-proof production and logistics concepts will require a large amount of information, about the laundry item itself, current product status, product quality and process progress. Effectively this means transparency in the entire operation. This is exactly what our software helps customers to achieve,” says Michael Wieser, Sales Director of SoCom Informationssysteme GmbH. “TIKOS as a complete solution for laundry service providers covers the entire production process of a laundry. As an industry specialist, and because of
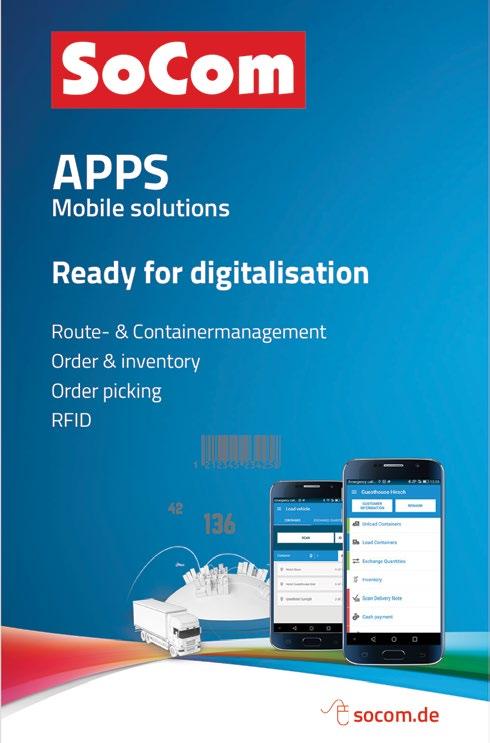
ongoing customer SoCom Apps engagement we are aware of the special challenges. Therefore, we are able to provide fast and competent assistance in the event of new requirements.”
Well organised with innovative apps
The process design starts with the customer. Innovative app solutions such as the SoCom app texScan enables mobile inventory to be carried out within seconds via smartphone, directly at the customer’s premises. Customers can now scan inventory or other movements.
With the app solution texOrder, orders or inventories can be made at hospital wards, nursing homes or hotels by the customer without any special training. Information is transmitted directly and is available offline.
The texRoute app is available tailored exactly to the logistics needs of a laundry. With this app, mobile route management as well as container management can be organised comprehensively and profitably. Overlooked or incorrectly loaded containers, which can ruin profit margins, no longer occur. The issue of container shrinkage is also a thing of the past. As with parcel delivery, the customer’s signature can be obtained for container delivery.
Live tracking is possible via a web portal - the current delivery status, set-up times, travel times and dwell times at the customer’s premises can be viewed at the touch of a button. The customer is informed via email, even before the driver arrives. This means that the customer can prepare everything right away - the right containers with the right laundry items to the right pick-up location, thus reducing loading times.
The texEasyPick app offers support in the field of picking. Orders can be picked easily, paperlessly, and stock is adjusted automatically. Production managers can see the live status of all open pickings at any time and change the prioritisation of individual pickings immediately. Due to the direct interaction of the individual app solutions, the additional container and parking space information stored in texEasyPick can be transmitted to the driver and displayed via the texRoute app.
While all the abovementioned apps are designed for special applications, the texUniScan app covers different fields of application. All barcodes or QR-Codes are captured by a smartphone or tablet camera or external scanner and transmitted directly to the TIKOS database. “What the app captures and reports back in a processed form is determined by our customers - according to operational requirements”, explains Wieser. Therefore, the range of application of the texUniScan app is enormously comprehensive and flexible. Expensive PC-workstations are no longer necessary and smaller processes can be controlled directly in production by the customer himself, thanks to digital companions.
For more information visit: www.socom.de