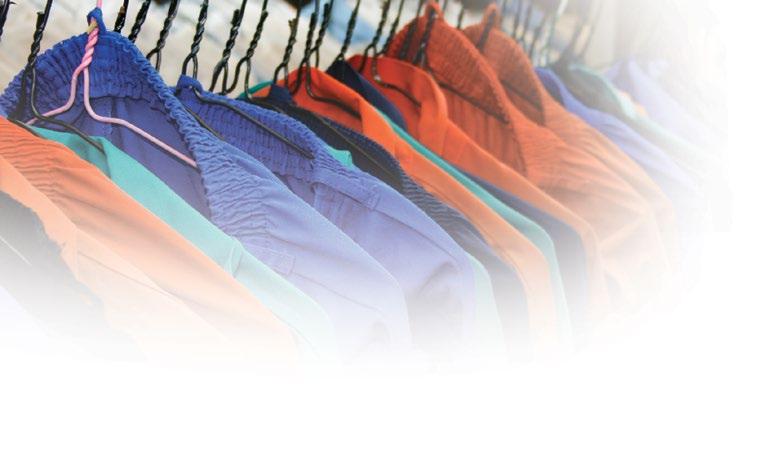
8 minute read
Laundry Review
For a facility manager faced with increasing volumes of laundry, innovative technology and equipment – like dispensing systems – offer the best solution to keep up with demand. Advances in sensors, computing power and connectivity are making dispensers smarter, delivering additional benefits to laundry facilities. Notwithstanding the size of a laundry, tools are now available to improve textile care, enhance safety and reduce the environmental impact.
Advertisement
A key requirement of successful laundry management is to understand what advanced equipment is already available and to stay informed on any developing capabilities. There is a diverse range of compact and cost-effective systems to investigate. The best laundry dispensing systems feature technology to simplify the installation process, reduce maintenance and enhance cleaning results, according to Hydro Systems.
These include low voltage machine interfaces, pre-wired systems and Auto Formula Select. Recent developments also allow certain systems to provide accurate chemical and water measurements to optimise cleaning results, reduce rewash rates and improve productivity.
Getting connected
The Internet of Things (IoT) – a network of connected devices delivering data in real time – is forging new paths for many industries, and chemical dispensing systems in laundry facilities are no exception. The IoT provides remote monitoring and control capabilities,
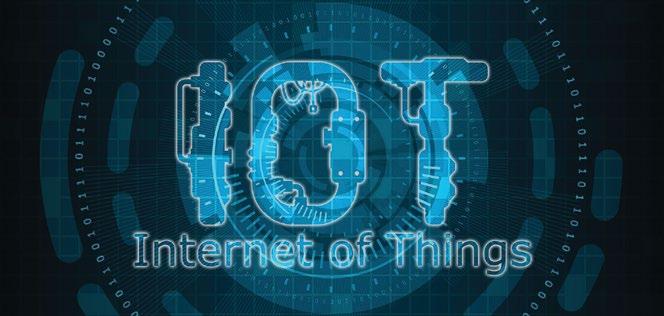
making it possible to keep tabs on chemical dispensing, even when you are not on site.
Smart dispensers ensure there is always adequate water supply and that chemical doses are delivered precisely, 100 percent of the time. Safety checks can be employed to protect equipment, employees and an entire plant. For example, if a leak arises, you will receive an alert from the dispenser and can take immediate action. Promptly stopping the leak reduces the risks of damage or needless downtime. Such dispensers also increasingly use sensors to check and monitor information such as the temperature of a load or the flow of chemistry, further consolidating integration with the washer.
Performance enhancing
Laundries typically rely on employees or their chemical provider to make chemical, water or machine adjustments, but this time-consuming responsibility can now be controlled by dispensers. The IoT tracks production processes and handles automated adjustments to dispense chemicals based on feedback from an accurate flow meter. This improves cleaning while reducing costs and waste caused by rewashing.
Data from sensors provides unique insight into the laundry process. The opportunities to take a closer look at key performance indicators like chemical usage by formula, volume of washes and average projection rate are better than ever before. This valuable information allows facilities to identify errors, reduce their recurrence and improve productivity.
Future proof
Connected dispensers already focus on remote monitoring, reducing downtime and delivering important data on chemical consumption, but this is only the start. There is a competitive advantage to be gained from knowing what to expect and what to look for in new dispensing equipment. Chemical dispensing manufacturers are bringing the future closer through, for example: • Automated inventory management. Taking inventory is a task with few volunteers. Consequently, this often results in ordering too much or too little product. With dispensers taking on this job, laundries could improve the accuracy of their inventory management. By integrating chemical usage data into enterprise resource planning (ERP) software, laundry management systems or customer relationship management (CRM) software packages, dispensers could detect when a certain amount of chemical usage is below a designated threshold and automatically trigger an order for more. • Predictive maintenance. When a dispenser or washer requires maintenance, it’s not always obvious. Unplanned maintenance can result in downtime and costly replacements. However, dispensers may one day be able to provide predictive maintenance on downstream equipment by analysing data and recommending repairs and upkeep before problems arise. • Load-by-load data. Advanced dispensers may be able to log data for every wash for compliance purposes and to provide proof of sanitation. Having access to this data, from the weight to the temperature or pH of each load, will help laundries better manage operations and stay organised. • Data analysis. With more data comes more responsibility and quantities of information, which many laundry managers may find intimidating. The likelihood is that chemical dispensing manufacturers will expand their services to
include assistance in analysing and interpreting this raw data. They might also provide consulting and educational programmes to help managers and employees react appropriately when an alarm goes off and to instruct them how to analyse and organise data on their own. Smart dispensers are currently transforming the wash process. Technological advances ensure there is much more to look forward to. The future promises a laundry process that is even simpler, safer and more sustainable. However, in an industry characterised by tight margins, those facilities that are slow to adapt and adopt are unlikely to see it.
With this in mind, and with the aim to protect the health of our employees, the SoCom team started working remotely within a very short period of time. This was the first positive realisation from the coronavirus challenge: modern technology and flexible staff contribute to processes running as normal as possible without any gaps in accessibility for our customers. It is a team’s performance from a distance that highlights the strong solidarity within the team.
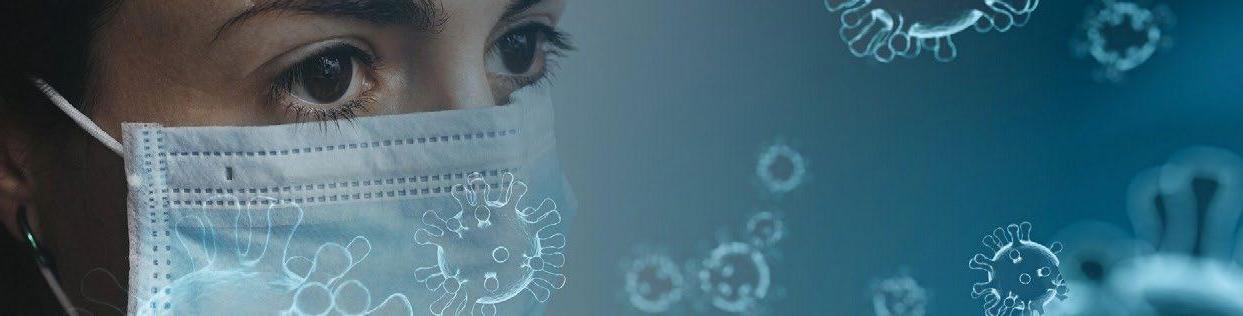
Positive lessons from the coronavirus crisis
Society is currently in a state of emergency, restricted to their houses, and economic challenges are abundant. The novel coronavirus or COVID-19 crisis has caused numerous challenges, questions and uncertainties in recent months, which has also impacted severely on the textile care sector. As a software service supplier, SoCom noticed this development clearly. Our customers who wash laundry for healthcare facilities are absolutely essential to society in such a health crisis and need all the support to guarantee smooth operations.
In the wake of the COVID-19 crisis, special cohesion and commitment to others is clearly evident elsewhere. The German textile care association (DTV) and the British Textile Services Association (TSA) have shown in recent weeks how important it is to unite people with the same interests and how necessary it is to stand together, especially in extraordinary times. As many laundries fight to be recognised as ‘systemically relevant’, one attempt/strategy in aid of this has been to provide emergency care for children of employees to allow the parents to continue their work. It is also the supply chain that provide laundries with disinfectants and personal protective equipment, which plays a role here. Both DTV and TSA are committing to the laundries and are trying everything to draw attention to the problem – a great sign that textile care businesses are not isolated during this pandemic.
For more information visit: www.hydrosystemseurope.com
editorial SoCom
We are all hard hit by the impact of the COVID-19 pandemic. It is the additional uncertainty, how and when a state of normal will return, that causes us all to suffer. However, at SoCom our goal is certain: we are fully committed to our customers, now and in the future, because only if we look positively towards the future, can we successfully contain this global pandemic together.
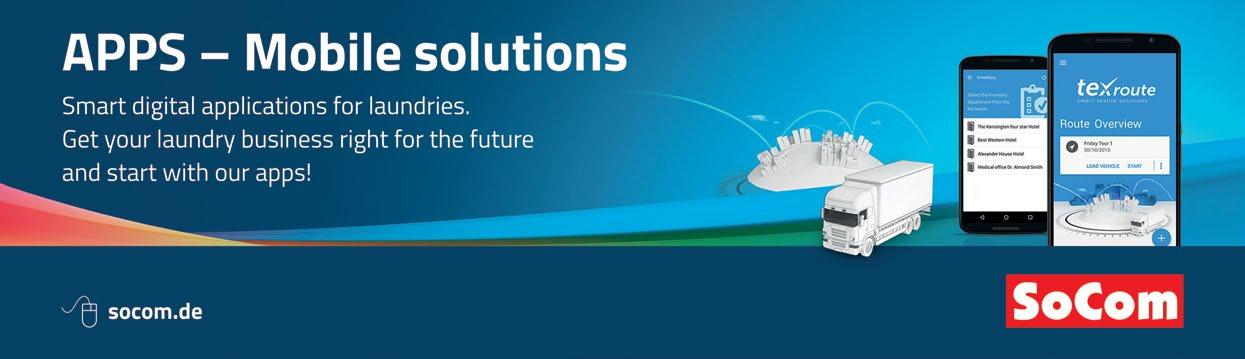
Be part of the official African delegation to visit the bustling city of Amsterdam and the world’s largest professional cleaning exhibition
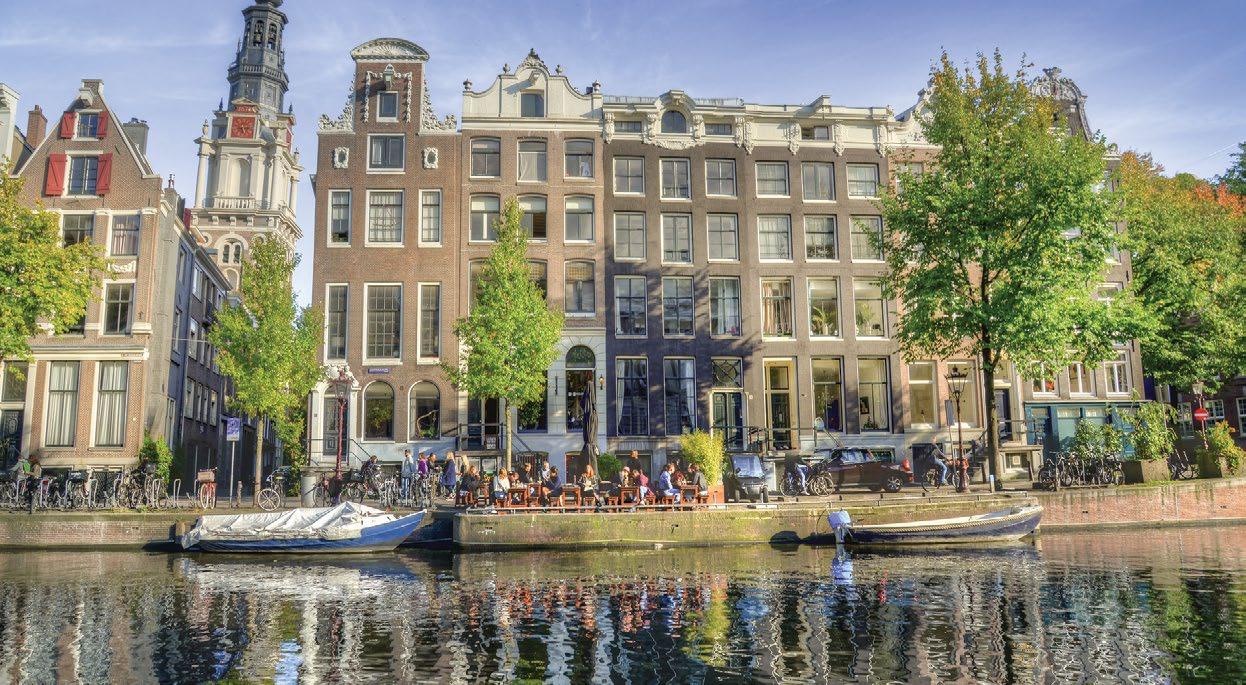
Holland’s capital city is a hub for happy cyclists, beer-drinkers, tourists and art-lovers. Amsterdam’s go-to bohemian vicinity brims with coffee shops, bars and restaurants, and the renowned Albert Cuyp market is well worth a visit.
During the fall of 2020 the world of professional cleaning will gather in Amsterdam at what is regarded as the world’s largest exhibition of its kind. This is your opportunity to view the latest cleaning technology and updates on global trends and developments while connecting with cleaning professionals from over 143 different countries. The exhibition floor stretches over several halls and is divided into eight specific segments, namely: high pressure; laundry; management; mobility; steam cleaning; washroom; waste solutions; window cleaning; and healthcare. The other three segments – machines, equipment and detergents – are fragmented and can be found in every hall. The first Interclean exhibition took place in 1967 and it has since developed into the world’s leading trade fair for the professional cleaning industry.
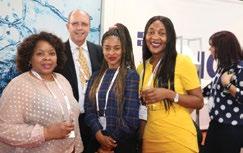
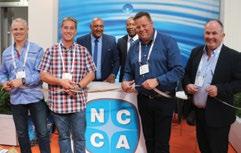
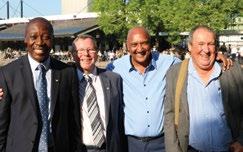
“I have really enjoyed the trip, learned a lot about new technology and will surely
implement some systems. The trip was very well organised.”Awie Human, Branson Chemicals
“Thank you for an amazing trip. It was well planned and executed. It was fun and also very
beneficial.”Simon Barrett, SB Marketing
Tour departs Saturday 31 October 2020
Interclean 2020 tour package:
• Five-night 4-star accommodation in Amsterdam, including breakfast • Direct flights to and from Amsterdam • Hotel/airport transfers, welcome drinks on arrival including activity • Day-trip sightseeing tour to Rotterdam in luxury coach including tour guide and lunch • Transfer – hotel to RAI exhibition centre on opening day • Three-day city tram pass • Two-hour evening canal cruise through Amsterdam city canals including drinks and snacks • Farewell three-course dinner including all drinks at a traditional Dutch restaurant
Tour package rates subject to exchange rate fluctuations
New Interclean 2020 show dates
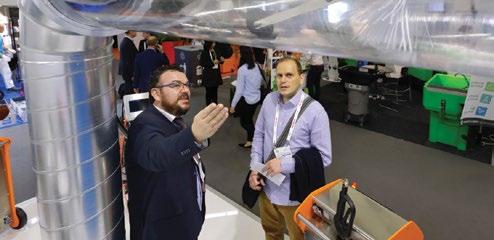
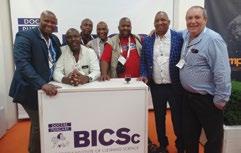
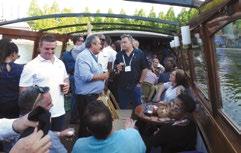
3 - 6 November Amsterdam, The Netherlands
“With the new dates we have ensured you will still be able to see all of the original major exhibitors.” Rob den Hertog, director Interclean.