
4 minute read
From Dutch pigsty to global sorting and packaging player
Tomato sorting line - Rollerstar
Aweta has been around for 55 years. It was started when the founder decided to help Dutch vegetable farmers. They wanted their tomatoes and cucumbers sorted more accurately. This business has now grown into an international one that provides total sorting and packaging solutions.
It may surprise you, but Aweta has offices in the Netherlands, Italy, and the United States. It also has a global dealer and service organization network. The company developed and built its first sorting machine in a former pigsty in the Dutch town of Nootdorp. "Adrianus Wilhelmus Tas (Aad) founder and namer of Aweta,” begins Norman van der Gaag, Aweta’s Sales Director.
"He comes from a farming family. He wanted to help growers by making mechanical sorting of greenhouse vegetables possible. He started Aweta in 1966. His first mechanical sorting machine was the beginning of Aweta's success."
Aad Tas Sr. predicted possibilities in simplifying production processes. In the years that followed, Aweta developed all kinds of sorting machines. They sorted greenhouse vegetables like tomatoes, cucumbers, and bell peppers by weight. The company has developed tremendously over the past 55 years.
"Camera techniques were introduced in the 70s. That made it possible to also sort by color and size. This resulted in an even more uniform product. Aweta expanded its production over time. It added machines for things like feeding, packing, and palletizing products. We went from just sorting to total fruit and vegetable sorting and packaging solutions. That includes software," Norman continues.
THE WORLD LOOKS TO THE NETHERLANDS
Aweta is active all over the world and has a broad network of partners. It has branches in Italy and the United States too. The com-
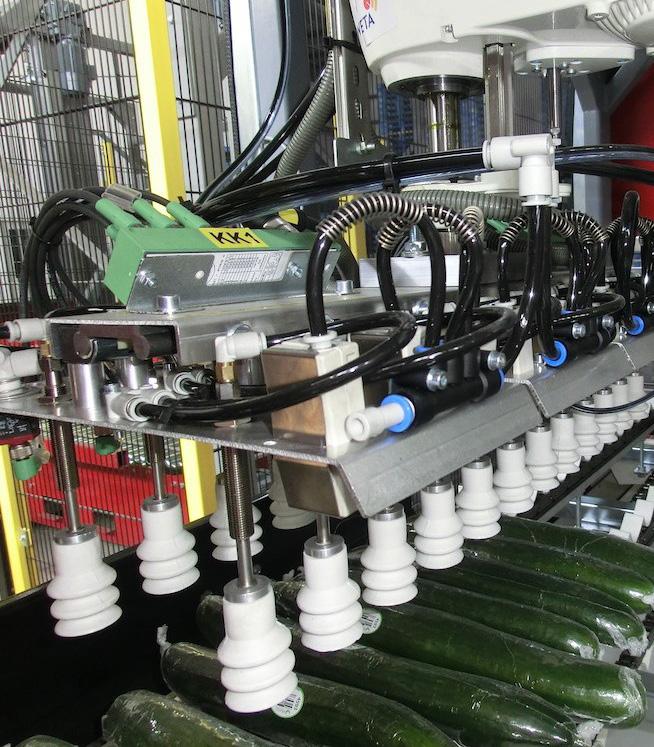
Cucumbers in an Aweta Qpack
pany offers total solutions for a wide range of fruit and vegetables. According to Norman, greenhouse vegetables still account for most of the business' revenues.
“That's partly due to its head office’s location in the Westland, the Netherlands. Many leading greenhouse vegetable businesses are based here. There are constant-

Bell pepper cup sorting line with accuveyor buffer system Aweta’s factory in the Netherlands
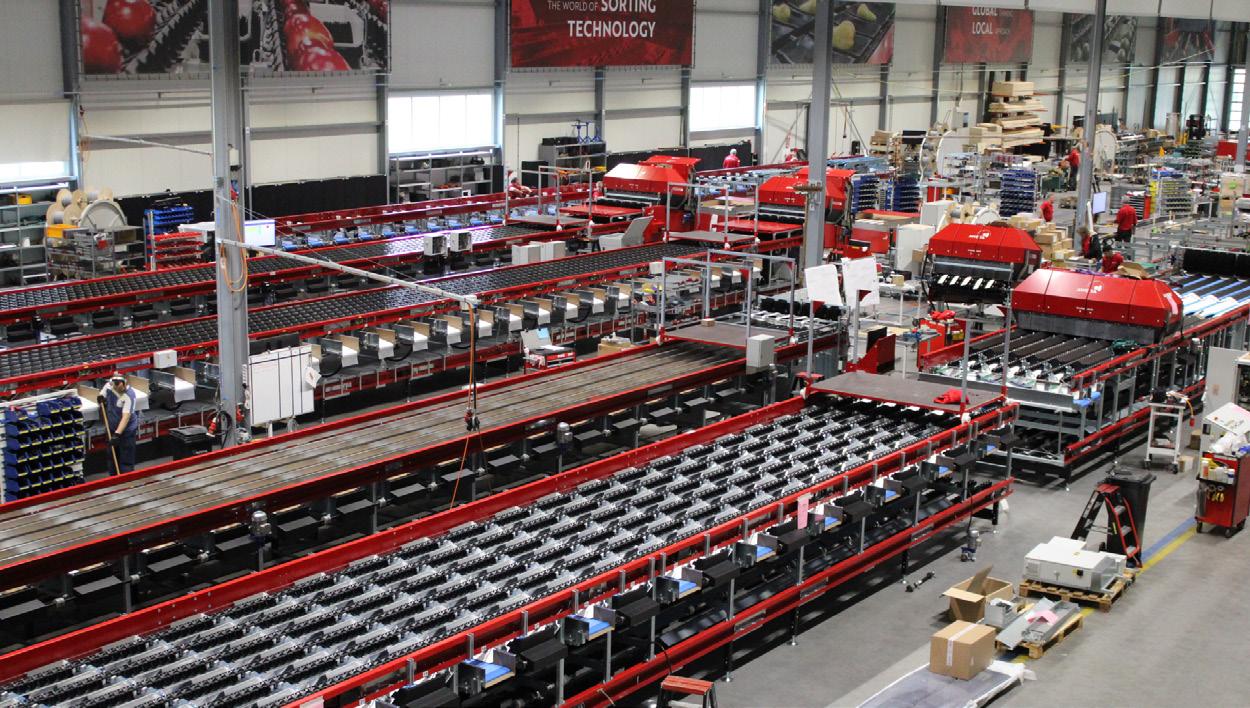
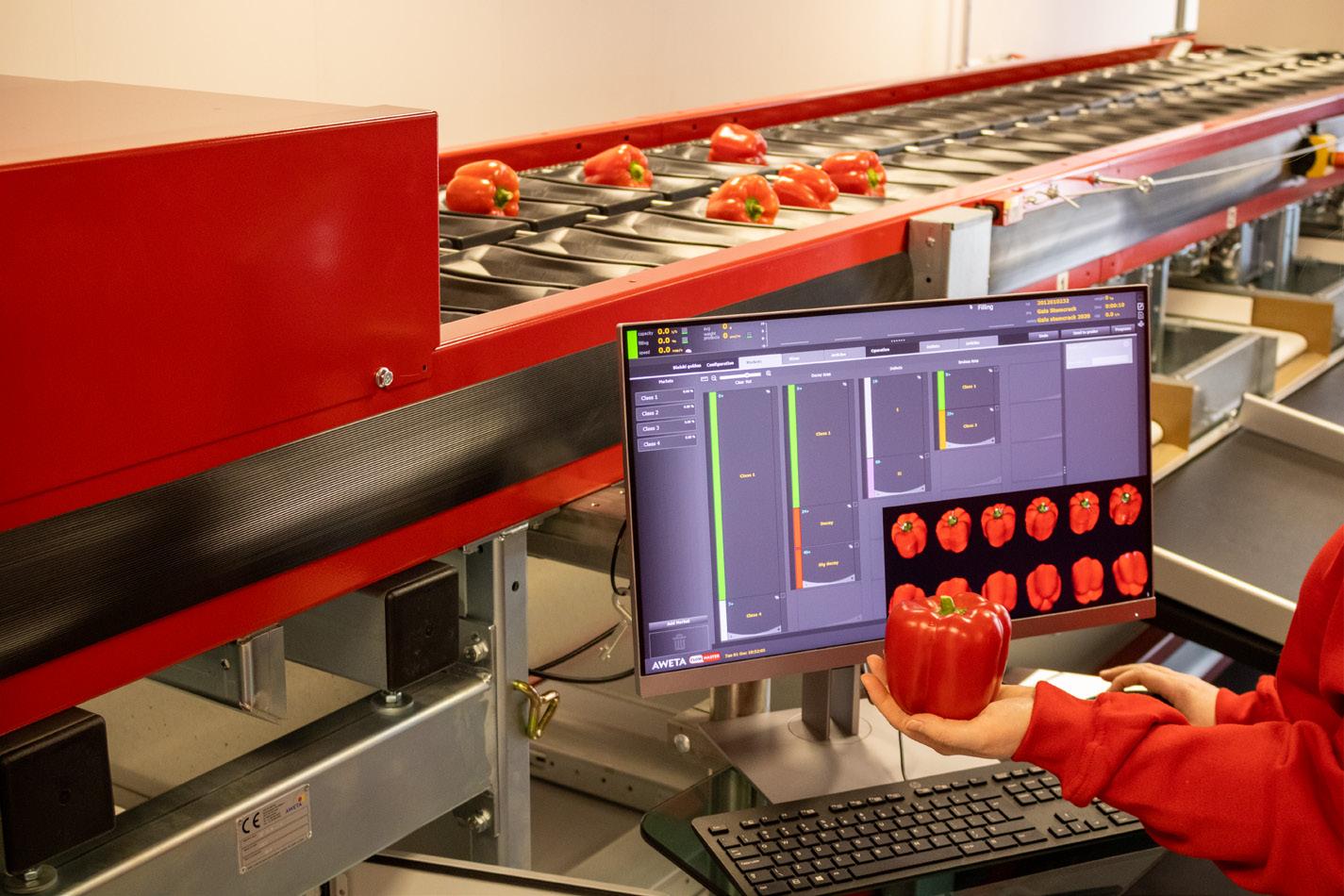
Flowmaster software system for a bell pepper sorting line
ly innovative projects being realized here. The whole world is watching the Westland. The Netherlands is truly progressive in the field of greenhouse vegetables."
Company upscaling is a major factor in these new solutions' development. Players are increasingly growing in size but don't want costs to rise proportionally. "Clients wanting to expand must be competitive and minimize their expenses. We can be important here. We supply machines that help deliver the highest possible quality while reducing operational costs. Sorting and packaging automation is a significant step towards reducing labor costs. There are all kinds of solutions for this nowadays, and new techniques are constantly being developed."
"Today, bell pepper and cucumber sorting, for example, is almost entirely automated. Robots are one of this processes' latest introductions. A robot now automatically fills cucumber boxes. The Netherlands is leading the way in this respect. Overseas markets like Canada, the United States, and Japan are now using this technology too. It means fewer hands on the belt, but certainly, also fewer hands touching the product. That is greatly beneficial, especially now, during this global pandemic," adds Van der Gaag.
MORE INSIGHT
Aspects that improve production efficiency also play a role. "When you select the optimal combination, a sorting machine can make a big difference here. It allows you to fill the packaging as precisely as possible. That process has been greatly optimized in recent years. It now requires hardly any manual labor to control." Norman mentions other great product data developments throughout the chain.
These include harvest registration and track & trace. With harvest registration, the machine provides insight into what has been harvested. That is includes color, size, deviation, and yield per hectare. This is vital information for optimizing cultivation. It can ultimately even determine which products of which grower are best suited for end-customer requirements.
INTERNAL QUALITY SELECTION
"Greenhouse vegetables are already quite uniform in size and shape. Not so products that grow outdoors. These have to deal with all kinds of influences, like the weather. Consumers are becoming increasingly picky, and so are retailers' demands. Camera systems that can ensure uniformity are, therefore, needed more than ever.”
“We can now not only sort by external but also by internal quality,” adds the Sales Director. “These methods can, for instance, detect fungal development inside bell peppers. That is a huge step forward, especially for supermarkets. They can distinguish themselves with their fruit and vegetables, in terms of price, quality, and packaging."
USER-FRIENDLINESS, FIRST-ANDFOREMOST
The installations may be growing in size and complexity, but the Aweta software used to control everything is as user-friendly as it can be. "It's crucial for us that anyone can operate these machines. So, we make as much of the process as possible visual, with product pictures and real-time images."
Looking towards the future, there is still plenty of room for expansion and improvement, Norman concludes. Camera technology and software, for example, are constantly evolving. And the need for particular automatic packaging still offers many possibilities. (CH)
nvdgaag@aweta.nl