
5 minute read
“We’re ready to introduce our new possibilities to clients”
The new construction of DV Fresh also includes a fully automatic supply and removal of the empty crates from a 17 meter high automatic warehouse to the various packaging lines
Peter Bauwens, DV Fresh: “We’re ready to introduce our new possibilities to clients”
“Our 15,000m² expansion means DV Fresh is ready for the future,” say CEO of DV Fresh, Peter Bauwens, and Dirk Verkinderen, its business manager. This Belgian company processes and packs vegetables. Growth is one reason for this expansion; the need to further automate is another. DV Fresh works according to the operational excellence model, where efficiency is central. “For that, automation is critical to remove human error from the process. But also, less manual handling means less damage to the vegetables.”
That is why the bulk of the company’s investment went to the handling process. They have bought several new processing, washing, and de-coring machines, automating much of the previous manual labour. “We’ve spent the most in the processing and washing areas. It speeds the process up considerably, which benefits both the freshness and the speed of service. Compared to before, quality has stabilized tremendously. And, we need fewer operators,” says Peter.
AUTOMATION
He has found that automation places different demands on staffing levels. Previously much of the work was done by hand. The focus has now shifted to people who operate machines and robots. DV Fresh, too, is aware of the labour market shortage. Yet, it is managing to fill its personnel needs well, says Peter, thanks to the Young Graduate Program. “We use this to help our people become dedicated specialists in their field.”
“DV Fresh now has a team of experts at the ready. They give their very best to serve our clients.” Staff are therefore an important focus for this vegetable processor. “Aside from investing in build-
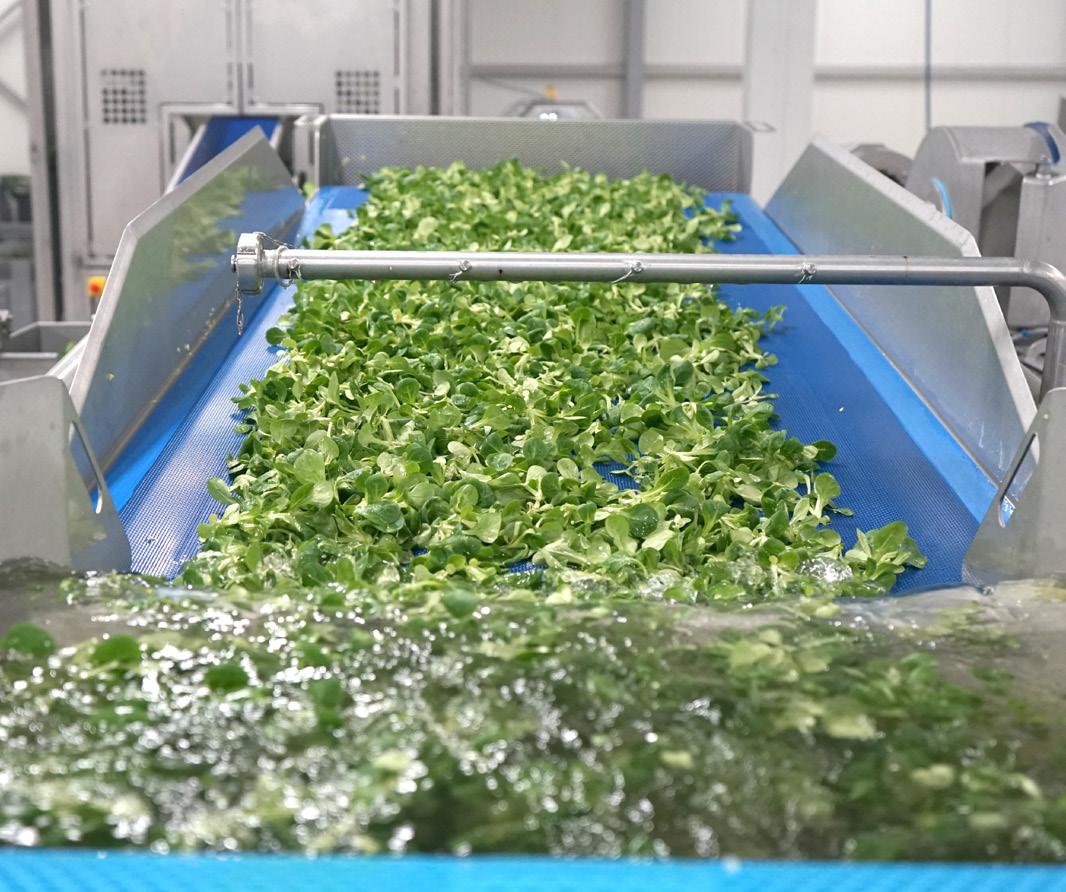
DV Fresh sees in addition to an increasing need for convenience, that consumers are also increasingly interested in organic and ready-to-cook products.
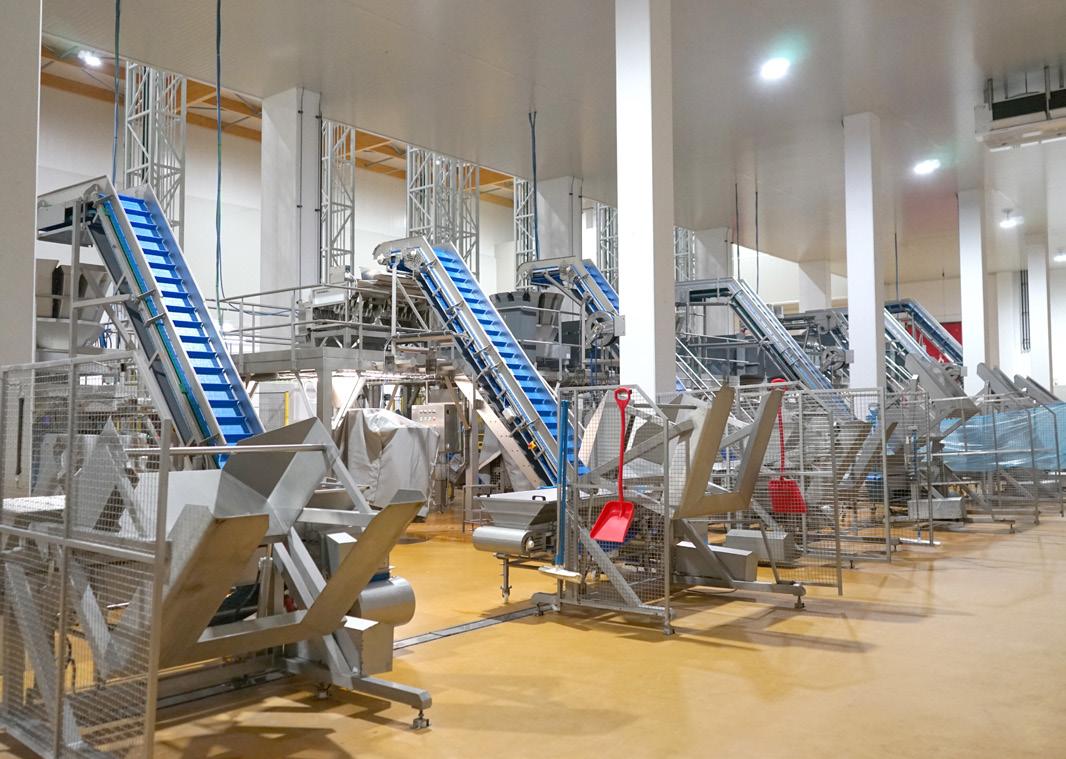
The packaging lines in the new factory Automation is one of the spearheads within the operational excellence model that DV Fresh uses
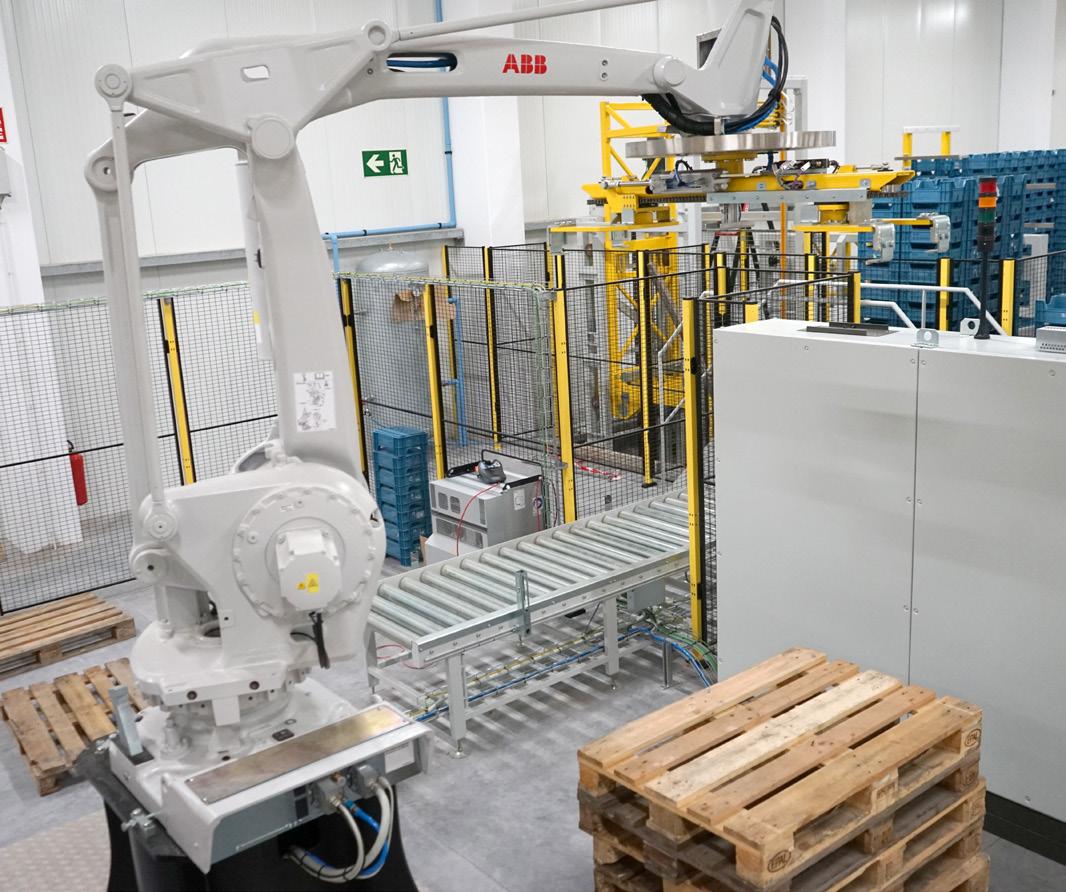
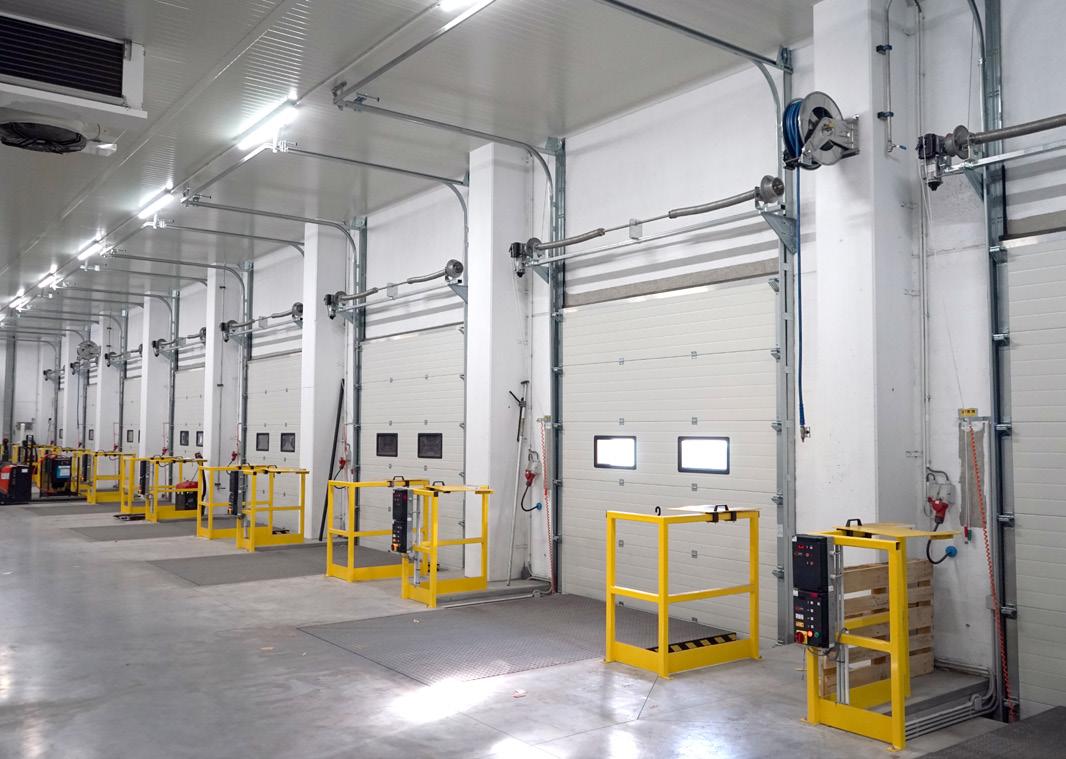
DV Fresh has taken into use eight new loading docks equipped with loading ports where there is no longer any temperature influence from outside during loading and unloading
ings, machinery, and partnerships with growers, DV Fresh also invests in people. Because we, through highly trained, driven people, want to add internal substance to our new building’s beautiful exterior.”
SHORT FLOWS
Also, during construction - started and completed during the global pandemic - DV Fresh emphasized short flows and avoiding unnecessary movements. An example is the fully automatic placing and removing of empty crates from a 17-meter-high automated warehouse to the various packaging lines. “Here, we again combine efficiency and speed. Before, the empty crates were brought manually on pallets. Now they’re automatically supplied to the packaging lines, and when they’re full, they’re automatically removed again,” Peter explains.
Eight new loading docks are now in use too. They are equipped with loading gates where the outside temperature has zero effect during loading and unloading. With all these investments, DV Fresh is ready for the future. “We’re ready to supply our existing customers with ultra-fresh processed vegetables that, based on knowhow and via new technologies, set a new quality milestone. And we’re ready to introduce new clients in Belgium and its neighbouring countries to our new possibilities.”
CULTIVATION OPTIMIZATION
And those possibilities include the vegetables used for processing. Dirk - who sees that, along with convenience, consumers are increasingly interested in organic and ready-to-cook products - explains that not all varieties are suitable for processing. “The vegetables we need have to meet different conditions than those intended for the fresh range.” He points out that, for instance, automatic processing of lettuce requires the head to be of a specific density. And peeling straight, rather than curved, cucumbers produces less waste.
Variety selection is, therefore, important, as is optimizing cultivation. “DV Fresh has always relied heavily on its close collaboration with growers and their selection. Led by Dirk and his years of seed breeding and variety selection experience, together with a team of agronomists, we get the best out of its growers every day. That’s done with mutual respect and with a focus on long-term partnerships. And it includes working with growers to develop new farming methods that increase harvest security and ensure product quality,” concludes Peter.
Peter.Bauwens@dvfresh.be Dirk.Verkinderen@dvfresh.be
#1 provider of Pulsed Electric Field systems for French fries and chips.
Healthier snacks, made from potatoes, vegetables and fruits with less fat, better taste, better colour.
www.pulsemaster.us
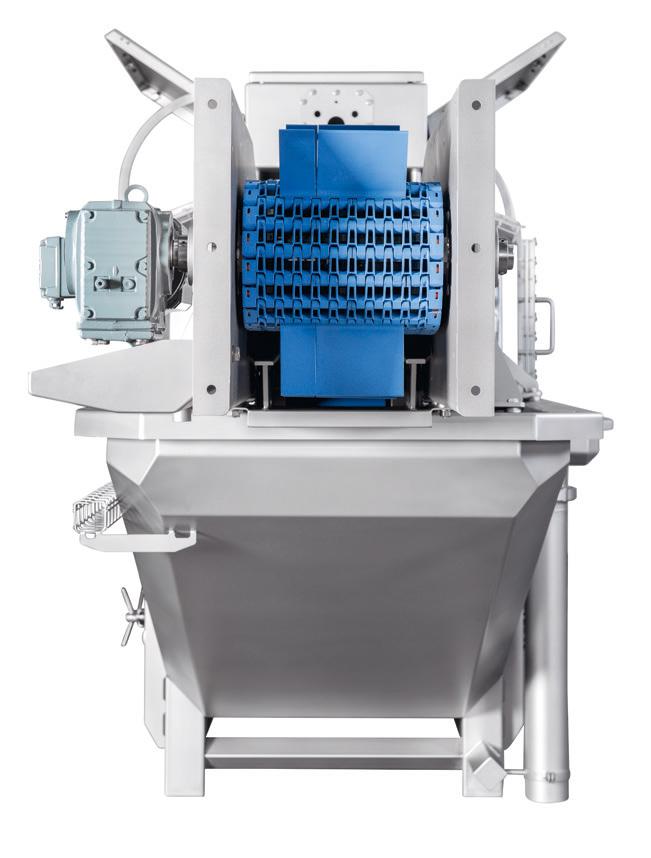

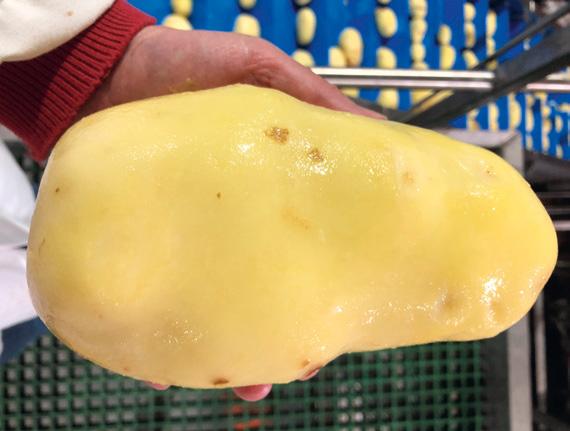
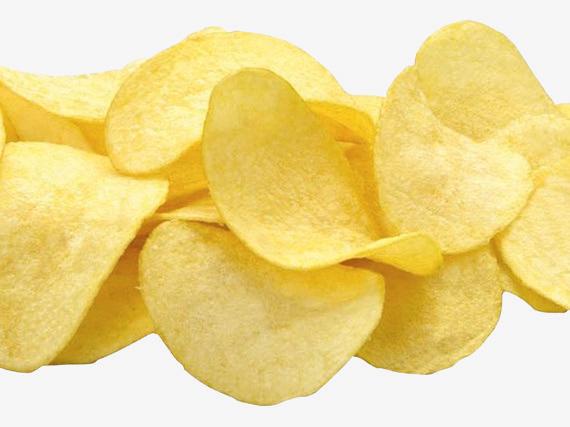
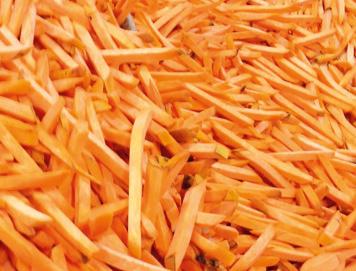
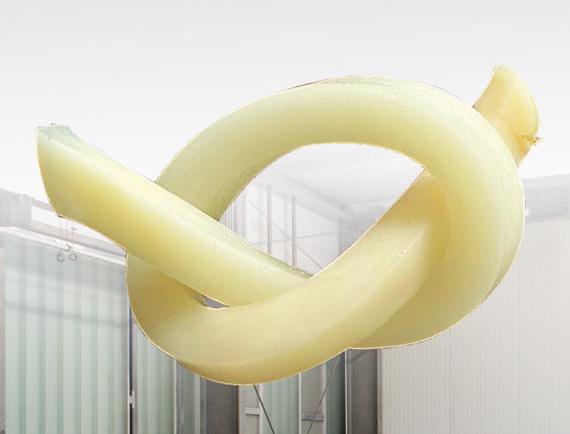
ON THE LEFTBANK WITH EXCELLENT CONNECTIONS TO HINTERLAND DESTINATIONS VIA MAINROADS AND SUFFICIENT BARGE CONNECTIONS TO THE IMPORTANT EUROPEAN PORTS.
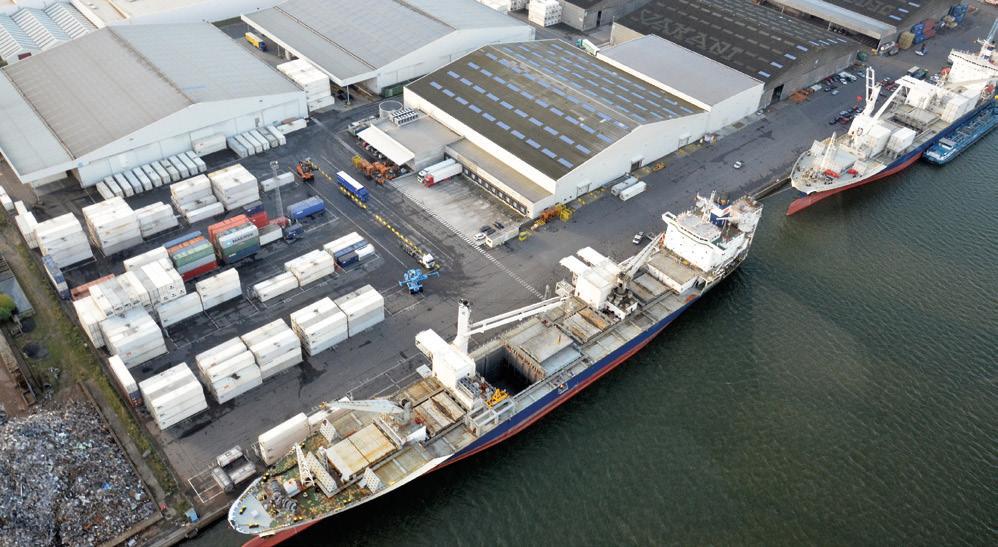
EFP being specialized in handling fruit and perishables (mainly bananas) situated at a multi purpose water related terminal containing: • 13600 sqm coldstore • 8100 sqm dry warehouse for export • Container hub & repair site of 17500 sqm and 500 reefer plugs
STRENGTHS:
• Expertise in stevedoring • Liable in Warehouse Management • Excellent Warehouse Management system with barcode scanning for track and trace • FAVV approved • Experienced and skilled employees to
For further info do not hesitate to contact EFP directly on info@eurofruitports.com · www.eurofruitports.com