
6 minute read
TOOL BOX TIP S - Repairing Composite Parts
TOOLBOX
BY: DAVID STARK
TIPS
RS 125 Seat - Before: This RS125 tail section was repaired using the techniques and materials in this article.
REPAIRING COMPOSITE MOTORBIKE PARTS
Fiberglass gas tanks, fenders, belly pans and fairings are on virtually every motorcycle at an AHRMA event, off-road or roadrace. This means almost all vintage or modern competition motorcycles have at least one composite part that will need maintaining, repairing, or fabricating.
The techniques and tips in this article are based on 20 years of experience fabricating, maintaining and repairing composite seats, fenders, fairings and belly pans for vintage and modern racing motorcycles and teaching and sharing those skills with other AHRMA racers. My personal mentor is an FAA-certified aircraft mechanic, inspector and instructor who has owned and maintained composite sailboats and aircraft for more than 50 years. He’s also an AHRMA racer who has fabricated and repaired parts (including entire gas tanks) for his roadracing and trials motorcycles. (Thanks for the lessons, Dad!)
As with other fabrication and repair work, such as welding, painting and machining, there are many philosophies and techniques as well as favorite products. The tips and techniques in this article are not the only way to work with composites and we welcome input from the ARHMA family about how you approach designing, fabricating and maintaining your composite parts.
A composite part is simply a component that consists of different materials. For this article, “composite” refers to motorcycle parts made from a combination of fiberglass mat or cloth and the adhesives that hold the part together. Successfully working with composites requires two skills shared by painting and welding: safety and cleanliness. The catalyzed adhesives we use are toxic and prolonged exposure can be fatal. Residue from sanding composite parts creates dust that, at a minimum, will irritate exposed skin and, more ominously, may have dangerous consequences if inhaled. We ALWAYS wear nitrile gloves when handling resin and catalysts and wear a respirator and protective clothing when cutting or sanding composite parts. This is particularly important when working with carbon fiber parts.
Oil- or gasoline-soaked composite parts are difficult, if not impossible, to repair correctly. We use a variety of solvents including isopropyl alcohol and Coleman lantern/stove fuel to clean parts before starting a repair and immediately before applying new cloth and epoxy. The Coleman fuel is inexpensive and will not leave residue that will contaminate the epoxy. Our molds also get a quick wipe down with one of these liquids.
In this article, we’ll focus on using fiberglass cloth and “epoxy” adhesives. We have successfully used these materials for years and they work great for vintage motorcycle parts. The strength, flexibility and durability of a composite motorcycle part comes from layers of either mat or cloth working together with an adhesive. Too much, or too little, of any component can make the part heavy, brittle, inflexible, weak or even all of the above. To ensure a longlasting and high-performance composite part, use the right combination of cloth and just enough adhesive to keep the part together. Slopping on epoxy to wet-out a section of cloth quickly and then leaving puddles of excess adhesive adds
Epoxies on Parade - The size and complexity of a composite repair job will determine the best epoxy to use based on its viscosity and cure time. Isopropyl alcohol is great for prepping parts and cleaning epoxy of gloves, mid-repair, and mixing cups post-repair. Tools of the Trade - Nitrile gloves, "acid" brushes, plastic cups and chopsticks. The gloves keep you safe, the cups and chopsticks are for mixing and the brushes for applying epoxy.
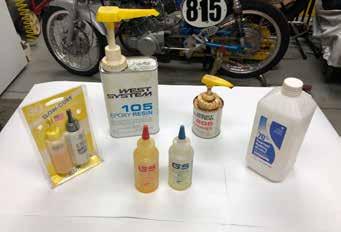

weight while not adding any strength. Squeezing the layers Place the first layer in the repair site and “stipple” on the together as the epoxy cures really adds strength to the final epoxy with the end of a small, inexpensive and disposable product. “acid” or chip-chaser brush. (Tip: Don’t try to clean and reuse
The fiberglass mat and cloth used in motorcycle parts your applicator brush.) Using as little epoxy as possible and is available in a variety of weights and weave configuration. not rushing this step helps ensure a good epoxy to cloth ratio. Many parts are originally fabricated in “female” molds using Add the next layers of cloth and additional epoxy until the cloth fiberglass mat. We use fiberglass cloth for all our repair is fully wet-out. A properly wet-out layup will have satin finish and fabrication work. Lightweight “s-glass” cloth in the 4- to with no visible epoxy puddles. Excess epoxy can be carefully 8-ounce range drapes easily over compound curves when blotted away using a paper towel or even toilet paper. using “male” molds and doesn’t soak up epoxy too quickly. The next step is to apply clamping pressure that compresses
For adhesives, we use West System 105 resin and the layers of cloth and epoxy together with the fending itself. associated hardeners, West System Five-Minute Epoxy, and An easy trick to distribute the clamping pressure is to use 15- or 30-minute epoxies typically marketed through hobby flexible cardboard or heavy cardstock with a layer of packing shops. Each adhesive is best suited to different types of tape on one side. Place the taped side of the cardboard repair and fabrication work. When mixing epoxy, avoid using against the wet-out cloth and then back this with a block waxed paper cups. We use disposable plastic cups, which of wood and your clamp of choice. Keep in mind that any also allow us to pop the cured epoxy out and reuse them. folds or divots in the material facing the layup will be molded Let’s put these materials together (pun intended) to tackle a into the final repair. Smoother is better when it comes few common composite repair and fabrication projects. to clamping surfaces. The packing tape also will act as a • Busted Boat Tail Blues • “release agent” and allow the cardboard “mold” to pop right
Your 1967 Bultaco Pursang MK 2 came from Spain with off after the epoxy cures. an alluring rear fender. Decades of clearing doubles and 24 hours later—depending on the temperature and humidity berm-busting has resulted in the fender cracking behind the in your workshop—the epoxy should have cured to the point top rear shock mounts. where the clamp system can be removed, and you can prep
The process to repairing this damage is similar to welding for paint. up a cracked metal part: clean the part, create a bevel joint In Part 2, we’ll cover repairing a hole in a belly pan and by sanding both sides of the joint to a fine edge and add new bringing a badly damaged seat back to race-ready condition material to fuse both sides of the damage together. In the and resources for learning welding example, the new material would be filler rod heated more about composite repair by a gas or electric welding torch. For a composite part, the and fabrication. new material is layers of cloth and epoxy. Keeping the gap as small as possible and stabilizing the part during the repair applies to both welding and composite work.
Creating a bevel tapering two to three inches from each side of the joint will allow several layers of progressively wider cloth to be laid into the repair site while keeping the final thickness of the repair close to the original thickness of the fender. The conventional wisdom is the scarf should taper at a ratio of 12-to-1 based on the thickness of the part being repaired. For this repair we would use West 105 epoxy because its low viscosity and long pot life and cure time gives us plenty of time to thoroughly saturate the cloth and remove excess epoxy. Fiberglass cloth in the 4- or 6-ounce range is easy to RS 125 Seat - After: cut and wet out and perfect for this repair. Part 2 of this article will describe, step-by-
step how this tail section was repaired.
