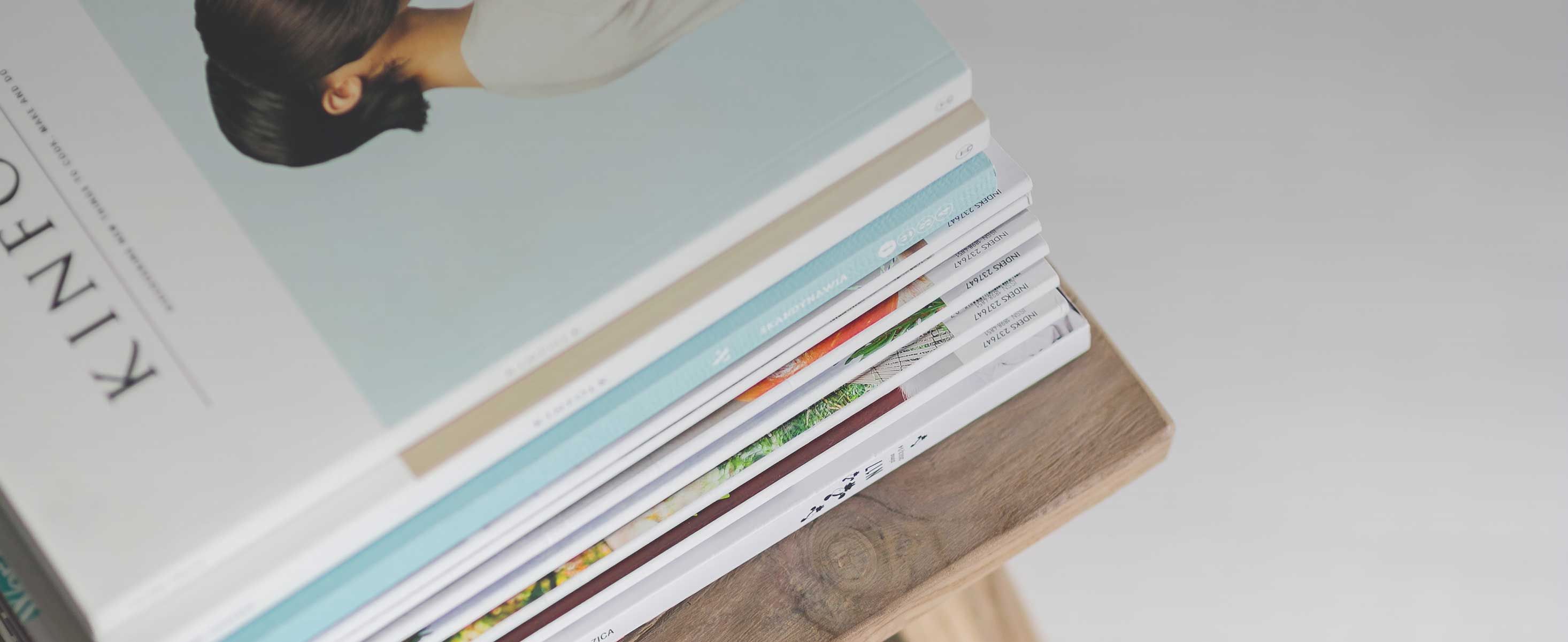
2 minute read
A Process Improvement Plan
BY LEVI COLVIN
When one thinks of a successful corrugated industry, it is common to think of a company with an outstanding safety record along with top-notch quality, low waste, and, of course, high productivity with margins that are so profitable, everyone is winning all the time.
Advertisement
In reality, most corrugated plants are low-margin, high-waste, low-production, and not as profitable as most desire to be.
This can all be attributed in some part to a sustainable and reliable structure that yields results day in and day out. A formula does work, and it starts with equipment, management, and dedication to a process improvement plan with everyone on the team involved.
This plan consists of an overview of the equipment with an audit to record calibration, excessive wear in parts, zero registration, and consistency in tooling (e.g., print plate 2" set back).
Once the audit is completed and reviewed with the management team, it is necessary to allocate the cost to correct the needed areas in the audit to bring the equipment back to the original equipment manufacturer. In the interim of calculating the cost of audit findings, the next step is to track all wear items on the equipment and determine the timelines of specified wear items so all wear items can be checked and compared with their specific timelines of wear on a tracking spreadsheet. This will allow for the knowledge of when the item wears out and when to change it before failure. The tracking is necessary to calculate the cost to projected versus actual and will give the team dialogue of effectiveness during tracking periods.
It is crucial that the equipment is also set for weekly preventive maintenance, which would mean the machine is set for downtime each week for four to eight hours, depending on the equipment. A team of maintenance and operations staff would then begin to check the equipment for wear related to grease, oil, print chamber system components, and shafts, which areas of the machine move throughout the day. Most machines have a manual and care plan associated with them; this care plan should be documented for equipment reliability.
It is normal for any equipment to become dirty in the corrugated industry; most components on the equipment can be blown off, wiped down, etc. One important area that gets overlooked on any piece of finishing equipment is the ink area. Managing the ink process is important and will keep many areas of any equipment clean and free from unwanted downtime. These ink checks should be done every half-hour to keep pH and ink viscosity at 8.5 pH to 9.5 pH and 18 to 23 seconds viscosity using a No. 2 Zahn cup method, respectively. For many plants, this is not common practice; if it were, machines would be free from ink on the floor, ink shafts, and bearings. Not managing ink creates a lot of unwanted and unplanned downtime.
With this plan, you will create a successful and reliable team, plant, and equipment suite that will yield sustainable results.
Levi Colvin is field service supervisor at Mitsubishi Heavy Industries America Inc.’s Corrugating Machinery Division. Any inquiries related to this article can be sent to Christine Little, senior sales manager, at 410-935-7835 or clittle@mhicorr.com