
8 minute read
A WORLDWIDE WHIRLWIND
from May/June 2020 BoxScore: VR and AR Technologies Hold Untapped Potential for Boxmakers and Clients
Trade and pandemic concerns are among the greatest hindrances to the global supply chain
By Lin Grensing-Pophal
Advertisement
Just a few short months ago as we heralded the beginning of a new year and new decade, it was unlikely that anyone could have predicted the massive impact that a rogue virus would quickly have on countries and companies around the world.
By mid-March, global economies were shutting down (Italy), and such iconic destinations as Walt Disney World and various large Las Vegas casinos were also announcing indefinite closings.
Prior to the emergence of a disease caused by a new strain of the coronavirus—COVID-19—manufacturers were concerned about current trade situations, especially between the U.S. and China, and tariffs. The potential of a pandemic hadn’t likely caught the attention of many, but it has now.
As of this writing, as transportation and commerce are grinding to a close, there are few issues that eclipse the focus on the ongoing and ultimate impacts of COVID-19. But whether we’re talking tariffs or quarantines, there is only one certainty for the near future: uncertainty.
Tariffs and Global Commerce
Maia Linask is an associate professor of economics at the University of Richmond Robins School of Business. “The tariffs that the Trump administration has imposed on imports from China have increased the cost of parts and finished goods sourced from China,” she says. A U.S. company must choose whether to pass that higher cost on to consumers or not.”
If tariffs are announced in advance, U.S. firms try to stock up before the tariff goes into effect. That’s not always possible, though, Linask says, “due to capacity constraints in China or limited space on freighters.”
While companies that import components or goods from China can petition for exclusions, Linask says that the sheer number of these applications can be in the tens of thousands, so the waiting period can be long—“and even then it is likely that the application will be denied.”
The trouble with tariffs is that there are so many unknowns, such as how long they may be in place or when they might change. Despite these impacts and uncertainties, though, Paul Leclair, vice president and chief economist with Numera Analytics, says they represent only a mild negative in terms of the impact on global trade. But, he adds: “The problem with tariffs is more the uncertainty that they create.”
The issue is that nobody can predict what may happen down the road. “If you put tariffs on China at 10% and say it’s going to be that way for the next 30 years, that’s one thing, because everybody adapts to that and makes decisions based on that knowledge,” Leclair says. “But, if you’re imposing tariffs but you don’t know as a business
— Michelle Klieger, economist and tariff and trade expert
great sustainability story. It’s paper and recyclable and reused. If China doesn’t purchase discarded paper from the U.S. and turn [it] into new boxes, it will change the sustainability story.”
But while impactful, issues related to tariffs and the recovered fiber ban are taking a backseat to the most recent concern looming over manufacturers and virtually every other business in any industry around the globe: COVID-19.
if they’ll be around next year, or in six months, or if it’s going to get worse, all these unknowns create an uncertainty that causes businesses to pause in their investments, because they don’t have a clear view of what the rules of the game will be over a long enough period.”
Despite that uncertainty, Leclair says, he doesn’t predict things to heat up between now and the U.S. presidential election in November. “But, afterward, who knows?” he asks.
In the interim, though, manufacturers are being impacted by one of the side effects of U.S. trade restrictions on China: the ban on recovered fiber.
Recovered Fiber Ban
China’s ban on recovered fiber represents another global supply chain issue that directly impacts the boxmaking industry, says Leclair. As a January article in Resource Recycling explains: “Recent actions by the Chinese government indicate the country will likely ban imports of OCC and almost all other fiber grades in 2021. Such a move would come in the wake of industry-shaking mixed paper and plastic prohibitions already in place.”
The piece goes on to share some statistics on the potential impact of the ban. “According to a Resource Recycling analysis of data from China’s General Administration of Customs, in 2016, before China’s import ban, the country brought in roughly 31.4 million short tons of recovered fiber. [In 2019], through October, just 9.8 million short tons have been imported into China.”
Michelle Klieger is an economist and a tariff and trade expert; she’s the author of The Demise of Free Trade: The U.S.-China Trade War Explained. The ban, says Klieger, was in direct response to President Donald Trump’s tariffs. “The corrugated industry did not get pulled into the trade war until last year,” she says. “In response to Trump’s tariffs, China put countertariffs on recyclable products like scrap metals, copper waste, recovered fibers, and paper pulp.”
This has made it more expensive for Chinese companies to import these products, she continues. “After the tariffs went into effect, Chinese purchases declined by one-third.”
Two things have happened since then, Klieger says: • Municipalities have stopped collecting corrugated and paperboard. “It’s too expensive to recycle it, so many places have stopped,” she says. • Chinese companies have purchased
U.S. paper mills so they can produce corrugated and paperboard in the United States and avoid the tariffs altogether.
“I assume these changes will drive up costs or impact quality,” Klieger says. “The part I find most interesting is that corrugated and paperboard has a
COVID-19 and Other Pandemic Concerns
First detected in China and now impacting the rest of the world, including the U.S., the virus called SARS-CoV-2 and the disease it causes—COVID-19 —became a public health emergency of international concern in late January, according to the CDC. On March 13, Trump declared COVID-19 a national emergency as schools and other organizations around the country began to feel its impact and the uncertainty related to the best actions to take to protect the public— and their bottom lines.
In February, Pierre Haren and David Simchi-Levi wrote an article for Harvard Business Review titled “How Coronavirus Could Impact the Global Supply Chain by Mid-March.” “We predict that the peak of the impact of COVID-19 on global supply chains will occur in midMarch, forcing thousands of companies to throttle down or temporarily shut assembly and manufacturing plants in the U.S. and Europe,” the article says. “The most vulnerable companies are those which rely heavily or solely on factories in China for parts and materials. The activity of Chinese manufacturing plants has fallen in the past month and is expected to remain depressed for months.”
It was the middle of March as of this writing, and some of these predictions are beginning to take shape.
Leclair says COVID-19 is the most pressing global trade issue right now.
“That’s really because it’s basically shutting down the manufacturing industry in China, or part of it,” he says. China is so critical to the global supply chain “because there’s hardly anything you can touch today that doesn’t contain something that comes from China; it’s obviously a key cog in the whole process.”
Chinese authorities, he says, “want to make sure that there’s no second peak in the coronavirus outbreak.”
While short-term travel bans are not likely to cause much disruption in existing supply relationships, says Linask, “as workers are prohibited from returning to work in China in order to control the outbreak, output stalls, and U.S. firms may be faced with a shortage of parts.”
Analytics company Dun & Bradstreet has taken a look at the potential economic impact of COVID-19 on a worldwide basis. Much of that impact has been in the manufacturing realm, according to the report: “Manufacturers are struggling
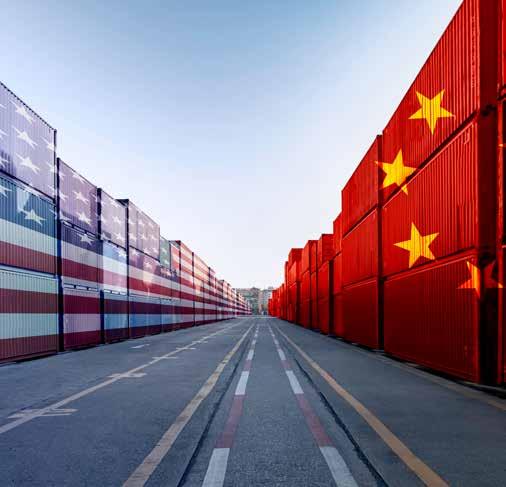
to get raw materials to their facilities and product to customers. In addition, many manufacturers will have to delay reopening of their facilities because of quarantines and travel delays detaining workers.”
The report offers some recommendations for manufacturers on how to protect their supply chains in the near and long term:
Near Term • Develop a risk-based assessment to identify and continuously monitor risks that impact supply chain productivity. • Assess your suppliers to ensure they will not negatively impact your business. • Monitor identified risks to ensure a complete and ongoing view of the supply chain and its risks. • Identify potential alternative suppliers.
Long Term • Build policies and contingency plans geographically. • Test and revise strategies to address growth and environmental changes.
In Closing
The three major forces that Leclair points to—the recovered-fiber ban, tariffs, and the impacts of COVID-19—are issues that manufacturers have no control over, he says. “These factors are basically things that they have to deal with and adapt to.” For now, he says, what that involves is cutting back on earnings forecasts.
Beyond that, for most manufacturers, it’s a wait-and-see environment as they consider ways to source and distribute goods with the least possible impact on their organizations, employees, and customers.
Lin Grensing-Pophal is a Wisconsin-based freelance writer and a frequent BoxScore contributor.