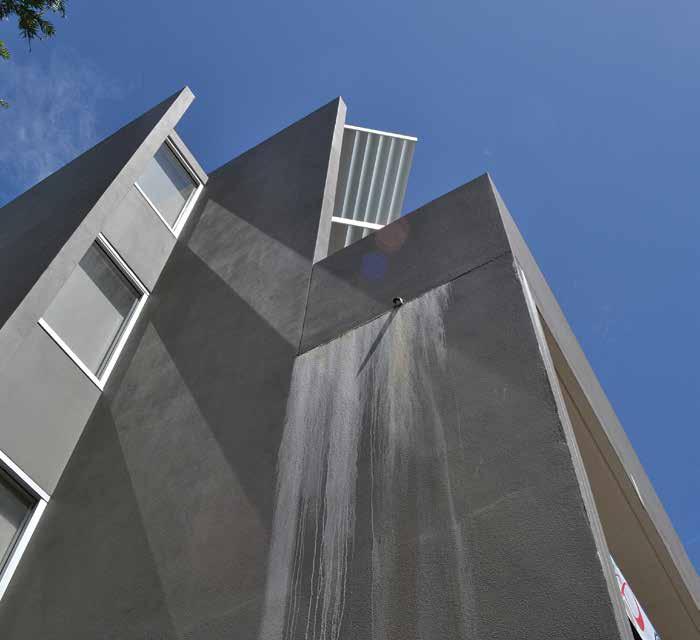
9 minute read
Why Buildings Leak: Part One
Most new, large scale apartment dwellings are beset with waterproofing problems within the first three years of the building’s life. We find it is common for one-year-old high-rise apartment buildings to have leaking podiums, leaking windows, ponding water in bathroom floors or balconies. That’s just the first year. It’s not just residential buildings either. One large scale, high profile, commercial building finished in the last few years in Sydney had $100 million of water leak related defects manifesting before the building opened. How is it that, in a sophisticated building industry with advanced reliable technologies in so many respects, we have such problems in keeping the water out? This article puts forward three propositions for addressing this question. Firstly, a discussion on the essential process flaw in our industry that allows these defects to occur. Secondly, how we can look at the design of a building more holistically to prevent water penetration defects. Thirdly, the quantity surveyor’s role in a more holistic approach to preventing leaks.
1. THE ESSENTIAL PROCESS FLAW
Analysis of the defects in thousands of home units and many large-scale commercial structures informs my perspective on the main cause of water leaks and cracking in buildings. In my experience, 90% of leaks and cracks are due to design and design coordination issues. More precisely, I find the leaks and cracks occur at the gaps between professional inputs. Forensic analysis of actual leaks and also an examination of the original
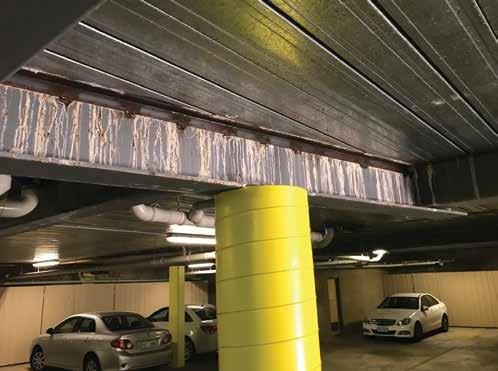
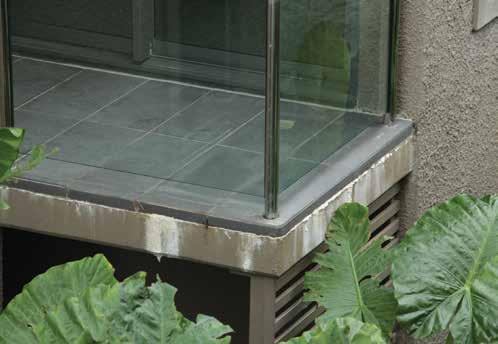

drawings usually reveals the leaks or cracks to be on the drawings two years before the works are carried out. It is that predictable. For example, in most new buildings we inspect there is at least an 85% non-compliance of the bathrooms with the relevant tiling or waterproofing. Consequently, it’s rare to find a bathroom or shower in a recently completed building with correct falls or adequate termination of the membrane. Our industry usually places the blame on the tiler and therefore the builder for not getting it right. However, when we check the drawings of these buildings, we see the seeds of the non-compliance were sown two years before in the selection of the floor to ceiling height for the project. How does the builder and therefore the tradesperson get the right falls if there isn’t sufficient floor to ceiling height to accommodate all the conflicting requirements of a modern hobless, frameless, doorless, stepless bathroom? How do we expect a podium not to leak when the structural engineer’s design has the movement joint placed between two large post-tensioned slabs placed in the middle of a planter box? When critical information on the long- term structural deflection of a podium slab is not shared, we end up with the rainwater outlets at the slab surface’s high points in five years? How do we expect a 1mm liquid membrane to bridge a construction joint which the structural engineer always knew had a long-term potential movement of 10mm, but didn’t think to let us know? In the conventional waterproofing model, only the architects, the waterproofing
membrane supplier and perhaps the waterproofing contractor have inputs to the process of keeping the water out. The structural engineer’s drawing will say ‘waterproofing’ as per the hydraulic engineer’s drawing. The hydraulic engineer’s drawing will say ‘waterproofing’ as per architect’s drawing. The architect’s drawing will show a thin black line ending mysteriously behind an adjacent element. Flashings are hidden or deleted. A layer of textured coating covering everything to make it all look solid. When we peer deeper into the building process, we see an absence of effective design co-ordination and complete reliance on a layer of goo. Project managers and developers are reluctant to spend the time and money on getting the necessary people in one room for longer than an hour to collaborate on design, address buildability issues, and assess the risk of leaks. This is particularly prevalent in design and construct contracts. Super specialisation of designers combined with design coordination by email means there is little opportunity to refine how the building, as a total system, fits together. As a result, the industry has developed a reliance on waterproofing membranes and sealants to do all the work. We design to meet all the usual planning and commercial imperatives then bring somebody in at the end to put a layer of urethane over the exposed bits. As an industry, we think we manage the risk of water penetration by getting a 20-year waterproofing warranty on a $100 million project from a subcontractor. It is a lazy and ineffective approach and lies at the heart of the water leak defect issue. We as an industry have succumbed to the siren call of the plastics age. We then try to fix these gaps in the design with sealant, on the run, during the works. ‘No more gaps’ by name and nature. How has this come about? We have collectively forgotten the simple pleasures of a well-placed downpipe and the elegant simplicity of a well detailed flashing. The timeless reliability of open drain joints, clear cavities and integral falls in concrete slabs. We ignore the fundamental principles of how water flows in and around buildings. We try to store it and block it then wonder why we fail.
2. A MORE HOLISTIC APPROACH
There is another way, to counter this plainly ineffective strategy, we need to move from a total reliance on waterproofing to a remembrance of watershedding. This is a new term for an old concept. It’s simple, it’s elegant and it has a 2000-year guarantee. Vitruvius, in the 10 Books of Architecture written in 10 BC for Emperor Augustus, included descriptions of specific methodologies for keeping basements dry and defecting water from the tops of brick walls to prevent premature failure. There are more specifics on leak and crack prevention in his writings than in the current Building Code of Australia.
We employ the principle of watershedding when we design and build a cavity brick wall or a terra cotta roof. It’s there when we insist on having a window with a sub sill and weep holes. When we ensure there are good falls in the shower floor, it’s here when we include more rainwater outlets than we have to, rather than less than we need. It’s here when we consider and then allow for the 10-year dimensional change in the concrete slab rather than just looking at the day one dimension on the drawing. In our consultancy, we have coined the term ‘watershedding before waterproofing’ to describe this shift in the approach to design. It incorporates the concepts inherent within rain control theory which have been used in high rise facades for many years. But it is time to use these principles wherever the building is exposed to water – not just the facade. Most importantly consideration of these principles needs to commence right at the start of the design process, not just once the concrete starts to flow. Everyone in the professional team has a role to play in incorporating the principles including quantity surveyors. Here are some of the key steps in this approach.
1. Engage the architect, structural engineer, hydraulic engineer and quantity surveyor in the watershedding design process. 2. Predict where water will access the building exterior and its pattern of flow. Find the top three risks then focus on these. 3. Plan to gather the water then deflect, redirect and drain it. Do not store it. Always maintain flow, do not allow the water to become idle. The exception is when it is deliberately being stored for reuse, flood mitigation or for swimming.
4. Never underestimate the long-term value of a well-placed flashing. It should always gather, deflect, redirect and drain. 5. With walls and windows, look for the opportunity to create a cavity or similar void, thus neutralising air or hydrostatic pressure then collect it and redirect safely. Always use open drain systems for facades in preference to face sealed systems. 6. For protection from ground water, always use drained cavities in preference before membranes and agricultural lines.
7. For roofs, podiums and balconies, never design a flat slab for external use. Always have integral falls and hobs. Never rely on mortar topping for falls. 8. When designing a concrete slab, which will have finishes exposed to water, always design to take into account the 10-year shrinkage and deflection of the concrete elements. Similarly, the 10-year expansion of the masonry elements. Put that number on the architectural drawings for all to see. 9. In balcony and roof design, place your downpipes at the points in the slab which are likely to become low points in 10 years.
10.Predict where cracking will occur and take steps to mitigate. The structural engineer and concrete supplier are the most important waterproofers. The membrane is just the back-up plan. 11. Cure concrete with water. Thirsty concrete and windy days, during cure, make for lots of cracks and leaks. 12.In bathroom design, look at the floor to ceiling heights right at the start of the design process. Is there enough room to fit the tile and tile bed with a 1:80 fall in the shower and 1:100 in the bathroom? It may not be as easy as you think. Tilers, like most of us, can’t make something out of nothing. 13.Never include planter boxes or box gutters in the design. If they are necessary, then treat them as the highest risk item on the project. In describing these watershedding principles you will notice there is no mention of the waterproofing membrane or sealant selection. If you get the watershedding principles right, then you only need the membrane to provide the protection for which the membrane was designed for.
THE QUANTITY SURVEYORS ROLE IN WATERSHEDDING
If watershedding is essentially a design related issue, where does the quantity surveyor fit in? A quantity surveyor can reveal the bits that everyone else overlooked. Otherwise essential quantities and dollars can be missed. Few in the building process have a knowledge across all the technical facets such as the quantity surveyor, therefore the quantity surveyor role is vital to changing this defective building process. There is an opportunity for the quantity surveyor profession to become more aware of the importance of these watershedding principles and
ask why the essential elements are not on the drawings when the project is being priced. To ask the questions when walking the site doing progress claim evaluation. Did the basement and external concrete slabs have the curing required on the structural engineer’s general notes page? If not, what is the assessed diminution of value of the slab due to all the unplanned cracking? Do all the shower floors have the required falls? If not, what is the assessed value of a finished bathroom floor that might have to be ripped up in two years?
Ross Taylor is a specialist waterproofing consultant with over 40 years’ experience in the design of waterproofing detailing, diagnosis and rectification of water penetration issues in new and existing buildings.