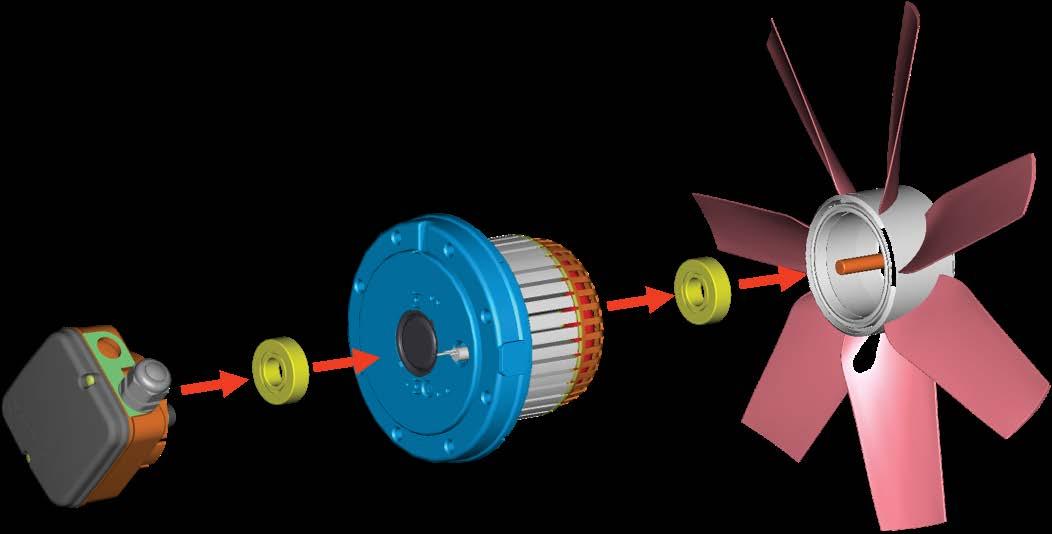
13 minute read
Skills Workshop
from HVAC&R Nation Summer 2020
by AIRAH
PROUDLY SPONSORED BY
AIRAH Industry Nights 2021
Advertisement
Skills summary
■ What? A close look at EC motors, including what they are, how they work, controls, benefits, and safety precautions. ■ Who? Relevant for anyone involved in the design, selection, installation, operation and maintenance of fans and fan systems.
EC MOTORS FOR HVAC&R FANS
EC motors, also known as BLDC motors (brushless DC), BLPM motors (brushless permanent magnet), are electronically commutated permanent magnet brushless DC motors and are from the external rotor motor family.
They are now used extensively in various applications, both for newly manufactured equipment and for retrofit into existing plant such as computer room AC units, refrigeration condensers and general HVAC systems.
This Skills Workshop explains how they work and the benefits they offer. It also covers details of their operation, and relevant safety precautions you should take when working with this equipment.
What is an EC motor?
You can think of an EC motor as an electric motor with a built-in variable frequency drive (VFD). These are very efficient motors with on-board electronics to allow for synchronous speed control with complete motor protection. This eliminates the need for contactors and overloads on the mains supply to the motors, and for shielded mains cable from the VFD to the motor.
EC motors tend to be more common in the smaller motor sizes, where the AC equivalents are far less efficient. AC motor or internal rotor motor efficiencies increase as the motors increase in power sizes.
As with all things, there are high-quality motors built to comply with the highest global standards with full R&D backup. There are also low-cost, reverse-engineered or copycat products that may seem similar at first glance, but often have little or no engineering support. Shortcomings in quality, performance, electrical compliance, and product support should be understood and considered carefully.
Different brands also have different inclusions and capabilities. Some can only do the basics, while others go “all out” with many programable and communication options.
What is an external rotor motor?
External rotor motors, known as ERM motors, are motors where the stator or stationary component of the motor is inside the rotor. These motors were originally designed for gyroscopes but became popular for fans because they are more compact than traditional internal rotor motors.
From these original motors, blades were added to create the most common style of refrigeration fan seen for the last half a decade. In the chase for energy efficiency, the EC motor was developed.
Evolution of the EC motor
As energy efficiency became important, manufacturers started running close to the limits of the ERM AC motor, and began looking for other ways to improve motor efficiencies.
By taking a VFD, changing the AC rotor to one with permanent magnets and combining them, the EC motor was born. At the time, electronics were large and expensive compared with today, and due to the size, they had to be mounted in a separate box like a VFD and wired into the motor. In the mid-1990s, as electronics became smaller and less expensive, they were merged into the motor housing to create the more compact and user-friendly EC motor we see today.
Today the EC motor manufacturers are on the third and fourth evolutions of these motors. As the EC motor benefits became more understood and used in various industries, EC motors kept improving. Manufacturers also received feedback from the market and made changes for specific applications.
How does an EC motor work?
For the most common variety for use in HVAC&R, you supply standard AC voltage into the electronics, where it is converted to DC voltage through a rectifier and filtered with the help of capacitors to form a DC link. The inverter, using electronic switches called IGBTs, switches the voltage in a controlled manner to the motor windings to create the rotating magnetic field.
The advantage of having electronic switches is that it can control the magnetic field, making it stronger or weaker, faster, or slower, by changing the frequency and amplitude of this voltage to the
efficiency. When compared to an ordinary motor, In the case of an AC motor, the magnetic field is created due to current flow. Because there from slip, which is eliminated in the EC motor because it is a synchronous speed motor. The benefits of an EC motor are clear when fans AC motor, a frequency-controlled AC motor, of the main frequency, unlike an AC motor. An EC or OEMs to monitor the equipment 24/7 to eliminate most catastrophic failures. Using clever algorithms, the EC motor data can help predict more than just energy and maintenance bills.
Control In EC
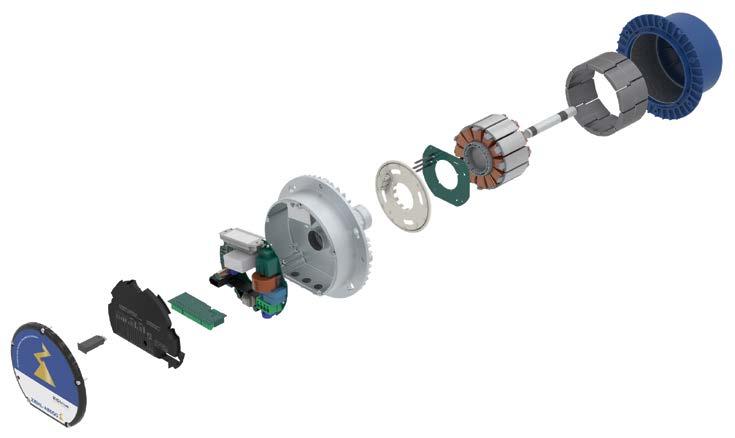
In an environment of systems that are increasingly integrated, monitored and controlled, EC motors offer wider options and flexibility. Most of the EC motors available today are equipped with smart technology and sensors. Options range from basic controls to high-level interfaces (HLI).
Figure 2 – Typical EC motor exploded view
windings. This rotating magnetic field causes the rotor with the permanent magnets to turn. Low voltage, typically 0-10VDC, or analogue input is mostly used to control the operational speed of the fan. The electronics monitor the speed of the rotor with the help of feedback through sensors. sensors, unlike an AC motor. A VFD can be installed, but this requires additional space, filtration and shielded cables – all of which increase costs. Microprocessors and connectivity Basic control Basic control options of an EC motor usually include on/off and 0-10 VDC, 0-20mA or pulse width modulation (PWM). Outputs from active sensors – which maybe 0-10V, PWM or 4-20mA – can be connected to most EC motors. Comparing this feedback to the speed set-point, the inverter varies the switching to match both. This set-point can be a speed or a torque that represents an airflow or a pressure value. EC motors have microprocessors on board for the necessary controls. Some also offer standalone or decentralised control without external controllers, by connecting sensors directly. Fault indication is another feature that makes troubleshooting easier. It is often indicated by a voltage-free relay contact inside the motor to provide external indication. The fault relay contacts Benefits of Some manufacturers do fault-logging on Closed (NC) or other via programming. Since the EC over AC motors these motors to quickly identify onsite issues. Fault logging can contain data on motor block, fault is indicated usually via an LED using flash code, the requirement of tools for diagnosis is minimal. Efficiency over or under temperature in the processor, motor or other electronics, overvoltage, over current, Alternatively, the fault could be identified using a computer, building management and control An EC motor usually has over 90 per cent line faults, wrong rotation, onboard errors etc. system (BMCS), or via Bluetooth if supported. energy savings are expected to be over 30 per cent. The prime reason for high efficiency is the lower losses in the motor. Some EC motors have onboard vibration sensors. This information is used along with the fault logging information and motor temperature sensors to Control via high-level interface (HLI) warn users long before a critical failure might occur. Apart from the basic control, EC motors also offers In the case of an EC motor, the magnetic field This technology makes it possible with IOT or cloud HLI options that are mainly used in the Building is partially created by the permanent magnet. systems to access the data, and for manufacturers Management System (BMS). This is usually installed is no current flow in the rotor of an EC motor, Rectifier to convert AC voltage into DC voltage DC link Inverter to feed motor there is no current loss in the rotor. + Some of the inherent losses in electric motors include copper and iron losses. Other losses include AC Power 1~ or 3~ Motor mechanical losses at bearing and bush friction Supply 3~ losses. Additionally, an AC induction motor suffers –0-10 VDC Control control signal Processor Feedback sensor are speed-controlled. The chart in Figure 4 shows the power consumption of a voltage-controlled Figure 3 – Typical EC motor schematic and an EC motor at different fan speeds. 110 At 60 per cent speed, the voltage-controlled motor consumes 550W whereas the EC motor only consumes 200W. A VFD-controlled AC motor consumes 50W more than EC at 60 per cent speed, and as speed increases this difference becomes greater, in favour of the EC motor. This is evident at full speed, with AC motor controlled by Consumption in % 100 90 80 70 60 50 40 60% ~55% 100% = = 550W 1000W VFD consuming 980W and EC motor only 800W. Therefore, in applications requiring speed control, ower 30 ~25% = 250W EC motors provide a better solution. P 20 ~20% = 200W 10 Overall cost 0 The need for an additional device for speed 30 40 50 60 Fan speed 70 in % 80 90 100 control (VFD) and cost of wiring AC motors makes EC motors cheaper. EC motors also offer high AC motor– voltage controlled power density and rotation in both directions. The AC motor–controlled by vfd maximum speed of an EC motor is independent EC motor can either be Normally Open (NO)/ Normally motor can be speed-controlled using output from Figure 4 – Typical AC versus EC motor efficiency comparison
by OEMs, which helps communicating to the equipment via the BMS communication network.
HLI enables the users to control and monitor in real time, making it more efficient. By varying the parameter of the HLI, this can be integrated in BMS programming. Depending on the BMS, the communication protocol used in the HLI can vary. Some of the common HLI options are Modbus, BACnet, Ethernet, EtherCat, and PROFINET.
How to work safely with EC motors
EC motors also offer various safety features. These include overload protection, locked rotor protection, false rotation, temperature sensors for overheating, line failure, and protection against over voltage.
All EC motors have capacitors inside and can provide significant electrical shock for several minutes after being turned off while they discharge. If the power to the EC motors is removed and the rotor is still turning, energy is fed back to the DC link. A rule of thumb is to isolate the EC motor from mains power, make sure it stops, then wait 3 minutes before working on the motor. But always check with the manufacturer.
As EC motors have motor built-in protection, if the motor is not spinning but the power is still on, the motor could restart at any time without warning.
What to avoid.
• Incorrectly sized cables not based on motor specifications. • Using a VFD for power to the EC motor. • Never megger-test an EC motor unless you can separate the windings, normally not possible. • Using contactors and (using) current overloads.
They are an unnecessary expense and older contactors can cause damage to the DC-link. • Connecting 3~ to a 1~ EC motor. • Connecting high voltage to the controller side.
EC
) DC Ou t (max = 70mA
Control
) DC Ou t (max = 10mA Digital In
24V 10V GND D1
Analog In
E1
Contact rating max. AC 250 V 2 A
13NO 14 K1
Mains
L1
L1 L2 L3
N
10
2
PE
External speed setting 5 Off / On 4
10kΩ L1 L2 L3/N PE
Line voltage
1 Rating-plate
– + 6 Input 1… 10V 4… 20mA 1. Line voltage see rating plate 2. Relay output “K1” for fault reporting (factory function), max. contact load AC 250 V 2 A • During operation the relay is energised, i.e. the connections “13” and “14” are bridged • In case of a fault, the relay is de-energised • In case of a shutdown using the enable (D1 = Digital In 1) the relay remains energised 4. Digital enable input (factory function) • Device “ON” when contact closed • Device “Off” when contact open 5. External speed setting 6. Input 0… 10 V, 4… 20mA 7. PWM input, f = 1… 10kHz Overload the onboard relay contact by exceeding the current or voltage ratings. Using long analogue cables. Using one multi-cable for control and mains supply. Using HLI and not obeying the communication guidelines. Using standard EC motors in non-suited applications. Water ingress in EC motors can affect the electronics and can damage the motor. EC motors should not be used for smoke exhaust applications or in an explosive atmosphere. Do not connect 10VDC or 24VDC motor outputs from one EC motor to subsequent EC motor outputs.
Wiring requirements for EC motors
Mains
• An appropriately sized main circuit breaker with characteristic “C” and/or fuse of operating class “gG”, based on motor rating, is required.
This will protect the wiring and motor should a short circuit occur.
A local isolator may be used for added safety and compliance. No contactor and overload is required for the EC motors as all motor protection is internal to the motor.
Good practice is to use individual circuit breakers or isolators per motor to provide redundancy in multi-fan systems. Ensure 1~ fans are only supplied 1~ as per motor name plate, because connections are often similar for both ~1 and ~3 motors.
Appropriate cable to suite application and correct outer diameter for the cable glands used to provide correct IP rating. Moulded cable is required to maintain IP rating.
The use of shielded cables is normally not required but offers high protection against electromagnetic interferences.
Control
• Analogue input for motor speed specification, ensure correct voltage and polarity.
Typical approved cable types include,
AWG22 (2x2 twisted pair moulded cable).
Check with the manufacturer.
Maximum allowed wire length is generally 1,000m (CAT5/7 500m). Appropriate cable to suite application and correct outer diameter for the cable glands used to provide correct IP rating. Moulded cable is recommended.
The use of shielded cables is normally not required but offers high protection against electromagnetic interferences.
This month’s skills workshop has been provided by Mark Jones, AM.AIRAH, from Ziehl-Abegg. For more information visit www.ziehl-abegg.com/au/home/
Other considerations
Reducing the energy consumption is no longer just a trend, but usually a requirement and often a necessity for building compliance. This means there is a need for high-efficiency motors with lower impact on the environment. High-efficiency IE5 EC motors consume less energy for a shorter payback period. Because the motor runs more efficiently, it generates less waste heat. This means EC motors generally have a longer life, higher system efficiencies, and a reduced heat load for cooling the motor.
EC motors do not generate motor noise associated with speed control, providing improved occupant comfort. EC motors can maintain higher efficiencies even at much lower speeds than AC motors can operate. This unique feature enables them to be more versatile, replacing conventional fan models with new EC fan models.
Some EC motors can also be programmed for use in zone pressurization systems or “fire mode” for fresh air supply systems, offering true run to destruction, bypassing all motor safeties, and being fully compliant with AS/NZS1668 Part 1. Complying with this standard requires that all motor protection needs to be bypassed while in fire mode. Note that complying to this standard is only applicable for use in fresh air supply applications – no EC motor can be used for smoke exhaust or hot gas exhaust applications.
Retrofit with EC fans
AHU fans make up about 30 per cent of a building’s energy consumption. Replacing low-efficiency belt-drive fans with direct-drive fans with EC motors could potentially reduce the electrical consumption by 10-30 per cent.
The ability to replace large traditional AHU fans with several smaller EC fans eliminates the logistical challenges for traditional large scroll fans at end of life, upgrade, or replacement. Typical EC plug fans can be carried by one or two people through standard doors, lifts and into existing AHUs without crane lifts or the major structural complications required to bring replacement scroll fans into existing built-up AHUs.
Because EC motors are typically smaller in size, benefits can be gained both in overall system efficiency and system redundancy using multiple fans in parallel to achieve the same duty.
Other retrofit applications include refrigeration, cooling towers, filter units, energy recovery units, and kitchen exhaust systems. These can hugely benefit from reduced noise levels, increased efficiency, improved air performance and other savings.
Given all these benefits, it is easy to think that if it is EC it will be better. But selection is still critical – not all EC motors are the same, and choosing the wrong one can have negative effects on your project goals.
A final consideration: There is no use having the most energy-efficient motor on the least efficient fan impeller. You must consider the complete fan assembly to meet the desired project specifications. ■
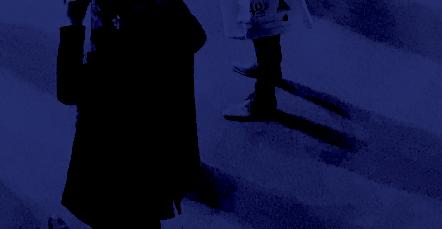
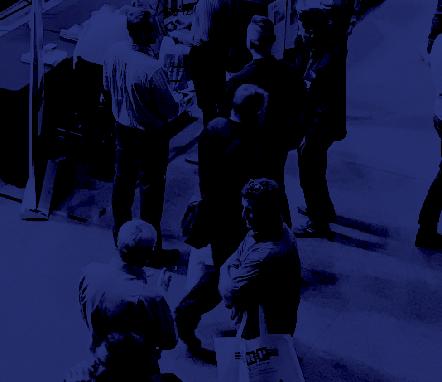
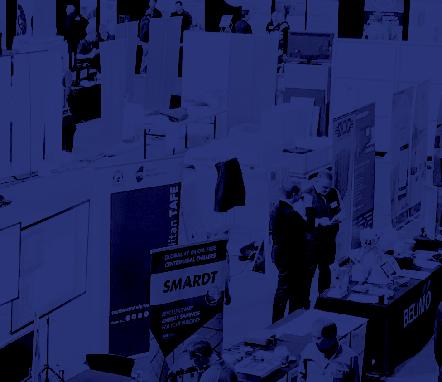
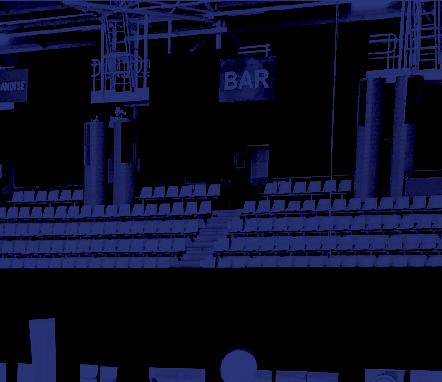