
14 minute read
Skills Workshop
from HVAC&R Nation February 2020
by AIRAH
PROUDLY SPONSORED BY AIRAH PROUDLY SPONSORED BY AIRAH
Skills summarySkills summary
Advertisement
■ What? An overview of building controls and the terms commonly used when discussing them. ■ What? A description of the different types ofwater-cooled condensers and cooling towers.
■ Who? Maintenance service providers, controls vendors and integrators, designers and contractors, construction and project managers, facility managers, building owners and developers, tenants and occupants. ■ Who? Relevant for mechanical contractors, consultants, OEMs and installers operating within refrigeration, air conditioning and process cooling and heating applications.
CONTROLS FUNDAMENTALS Controls are an increasingly important consideration in new building design and existing building renovation. They are directly linked to building performance and energy management, commissioning and retro-commissioning, operation and maintenance and broader links to building sustainability, building health and safety, and ultimately building satisfaction and productivity. The operation and control of environmental systems in buildings is a critical activity in terms of operating costs, environmental footprint, occupant comfort, and indoor environment quality. The operation of many building systems is sub-optimal and the performance of these systems can improve with better control strategies. Efficient buildings need efficient controls. This Skills Workshop provides a broad overview of control system fundamentals and explains some of the common terms used when discussing control systems. WATER-COOLED CONDENSERS AND COOLING TOWERS The condenser is a most important unit in a refrigeration system, as it is into this that all of the heat-laden vapour pumped by the compressor is forced under high pressure. It must be of greater capacity than the evaporator because the condenser must dissipate the mechanical energy from the compressor as well as the heat absorbed in the evaporator. Condensers are classified according to the type of cooling medium used – and are of three general types: air-cooled, water-cooled and evaporative. This skills workshop looks at evaporative condensers. This Skills Workshop also looks at cooling towers. All water-cooled refrigeration and air-conditioning systems must recirculate the water using cooling towers to cool the water by evaporation.
Evaporative (Type 3) condensers Evaporative condensers utilise both air and water to achieve heat rejection. The refrigerant flows into a condenser located in an enclosure; water is sprayed over the condenser to promote cooling of the refrigerant and air flows over the condenser to promote evaporation of the water and removal of heat energy. The water cycle is all in the condenser cabinet in this system. Longer refrigerant runs are usually needed to carry refrigerant to the evaporative condensers.
Usually the evaporative condenser is mounted out of doors; however, it is possible to locate an evaporative condenser indoors by providing air ducts linking the condenser to the outside. Evaporative coolers are often used in preference to cooling towers where the distance from the compressor to the preferred location of the condenser does not exceed 10–30 metres in a horizontal direction, or six metres vertically from the compressor.
At distances greater than these, problems of liquid condensing in the discharge line and flowing back to the compressor and of liquid refrigerant in the heads dictate the choice of separate water-cooled condenser and cooling water.
The cooling capacity is affected by the relative humidity of the air (water will not evaporate readily at high humidity) and by high water and condensing temperatures.
strainer solenoid stop valve
sight glass
liquid shut-off valve
thermostatic expansion valve evaporator
capillary tube
equaliser tube
remote bulb
liquid line
hot gas line suction valve
discharge valve suction line purge valve condenser shut-off valve
liquid valve emergency shut-off valve
rubber hose evaporative condenser
blower section
sprays
condensing coil
compressor unit vibration insulators liquid receiver pressure relief valve pump fusible plug liquid sight glass
Some systems pump the water to a tray located above the condenser and the water drips over the coils as air is forced through the coils. A fan operates to blow air over the condenser at all times when the condensing unit is operating. The water normally circulates continually, although, as with cooling towers, the fan may be slowed or turned off if water temperature falls too low. Fig 2 Typical custom-built evaporative condenser
Allowing for “bleed-off” of water to reduce the salt content, and for natural evaporation, such a plant would use only about three to four litres of water per kilowatt of refrigeration.
Cooling towers Strictly speaking, cooling towers are not part of the refrigeration system, but are used to cool the heat-laden condenser water so that it can be re-used. Cooling towers can use either natural convection or forced convection to promote airflow over the water droplets and improve evaporation of the water and therefore removal of heat energy in the process so the remaining cooled water can be recycled for reuse. However, the evaporation of water, plus the absorption of airborne pollutants by the water in the cooling tower, can cause costly corrosion problems. It is important, therefore, that the cooling water is monitored and chemically treated to reduce scaling and corrosion.
“Bleed” – In addition to water treatment, some of the water must be constantly “bled” to waste, to prevent concentration of solids as the water evaporates off. This is costly, as some of the treatment chemical is also lost and requires replacing. The amount of “bleed” varies according to the level of solids in the water (water quality) and the rise in water temperature.
Water flow rates through condenser tubes should be of the order of 0.2 litres/second per 3.5 kW of refrigeration, while flow velocities should be low enough to prevent erosion of the tubes at the end shields or “U” bends by solids in the water.

Fig 3 Baltimore Aircoil counter-flow forced-draught cooling tower (Reproduced with the permission of Baltimore Aircoil [Aust] Pty Ltd.)
Because of fresh water shortages, the running of water to waste is limited by law in many places, and most water-cooled plants use a cooling tower to lower the water temperature again for recirculation through the condenser. These towers are erected on roofs of buildings or in other locations where air can circulate freely through them. Some buildings may use the one cooling tower to reject heat from many refrigeration and air conditioning systems located around the building but small cooling towers of a few kilowatts of refrigeration capacity are also available.
Cooling towers are divided into two broad classes:
• natural-draught or wind towers – where the circulation of air through the tower depends upon natural wind movement
• forced- or induced-draught towers through which air is forced or drawn by fans.
However, most large cooling towers are in fact a combination of both, having fans – controlled by temperature sensors in the water – which run only when the water temperature exceeds a certain set limit, usually about 25°C, or using fan motor speed control to vary fan speed to suit the load. When the fans are not necessary, these (usually) roof-mounted towers rely upon natural breezes to evaporate the water sprayed from the top of the tower.
Large towers suitable for plants exceeding 1750kW of refrigeration (for example, for office towers) use cooling towers with end or overhead fan or fans and generally plastic “fill” down which the water slowly cascades, against the incoming air. Figures 3 and 4 show a typical example, while Figure 5 shows an all-plastic variety of forced-draught cooling tower.
Regardless of the type of cooling tower, water circulation differs little from that shown in Figure 4. In operation there is a reservoir of water in a tank or basin at the bottom of the tower. From this basin, water is pumped through the water-cooled condenser; then, having picked up the heat of condensation, the water is forced to the top of the tower and out through spray nozzles or similar distribution devices over the cooling tower “fill”, over which it trickles down to the basin against the cooling airflow.
| HVAC&R Nation | www.airah.org.au/nation | February 2020 Fig 4 Diagrammatic representation of the cooling tower shown in Figure 3 (Reproduced with the permission of Baltimore Aircoil [Aust] Pty Ltd.)
that evaporates absorbing latent heat of 2250 kilojoules. In Perth, Western Australia, where on 35°C days the wet bulb temperature averages 24°C, water will cool to approximately 24°C by the time it reaches the basin and can be immediately recirculated. However, in more humid climates, the evaporation rate is lower, and towers must be much larger as the temperature drop would be much less. Dry climates provide the most effective cooling due to the low wet bulb temperature, but dry areas usually lack sufficient water for water-cooled condensing.
The water which evaporates is replaced by “make-up” water from the mains, entering through a float control to the basin. If the fan is thermostatically controlled and the tower is in a windy location, the fan will turn off if the water temperature falls below about 25°C.
motor
fan support
fan fan stack
sprinkler pipe
casing
fill
fill support louvre
water basin
tower support stand
Fig 5 Hyperbolic cooling tower
Figure 6 shows two important points which must be considered when using towers
Firstly, there is always an accumulation of solids which remain in the water after some has evaporated and, to prevent the concentration of solids creating corrosion or scaling problems, a percentage of the return water (depending on the characteristics of the mains supply and the evaporation rate) must be “bled-off” to waste.
Secondly, because in cold weather the problem of over-condensing can be a serious one, an automatic “bypass” valve will recirculate water through the condenser whenever the condenser water temperature falls below 21°C for air conditioning loads.
‘bleed off’line cooling tower
hot gas in
condenser
liquid out ‘bypass’
‘make-up’ water
Water treatment The inside of a cooling tower or condenser may become coated with, and attacked by, foreign materials both from the air (e.g., smog, chemical fumes etc.) and the water. These may be removed by water-softening or metal-cleaning materials, fungicides and anti-corrosive materials. Unfortunately, the treatment of one source of contamination often requires the addition of another chemical to offset the by-products of the first treatment, and so on, so that treatment is a very costly business with seemingly no single treatment satisfying the needs of any two plants.
Regular draining, or even excessive “bleed-off” is not the answer, as algae and scale can form in pipes and on surfaces with relatively fresh water. Again, a combination of water treatment and excessive bleeding is costly in materials, as the water treatment chemicals are lost in bleeding.
Despite all treatments, corrosion can occur if water is acid or alkaline. It can also be caused by electrolysis that occurs between various metals (for example, copper and steel) used in construction; this has been known to eat through 12-millimetre steel condensing plates in six months. Regular cleaning and inspection for rust and deterioration is necessary on all water towers and condensers and adds considerably to large plant operating costs. The development of all-fibreglass and plastic towers and components is an attempt to reduce this expense.
Water regulating valves The water flow rate through a water-cooled condenser is often automatically controlled by a water regulating valve (see Figure 3).
The valve is installed on the water line at the inlet of the condenser and is actuated by the compressor discharge, as in Figure 3.28. When the compressor is in operation, the valve acts to modulate the flow of water through the condenser in response to changes in the condensing pressure. An increase in the condensing pressure tends to collapse the bellows further and open the valve wider against the tension of the range spring, thereby increasing the water flow rate through the condenser. Likewise, as the condensing pressure decreases, the valve moves towards the closed position so that the flow rate through the condenser is reduced accordingly. Although the regulating valve tends to maintain the condensing pressure within reasonable limits, the condensing pressure will usually be considerably higher during periods of peak loading than those of light loading.
When the compressor “cycles on” again, the water valve remains closed until the pressure in the condenser builds up to the valve-opening pressure, at which time the valve opens and permits water to flow through the condenser. The opening pressure of the valve is approximately 50kPa above the shut-off pressure.
The water valve is set for the desired shut-off pressure by adjusting the tension of the range spring. The minimum operating pressure for the valve – that is, the shut-off pressure – must be high enough so it will not remain open and permit water to flow through the condenser when the compressor is on the “off” cycle. Since the saturation temperature of the refrigerant in the condenser can never be lower than the ambient temperature at the condenser, the shut-off point of the water should be set at a saturation pressure corresponding to the maximum ambient temperature in summertime at the condenser location.
The shut-off pressure of the valve must also be high enough so the minimum condensing temperature in wintertime is sufficiently high to provide a pressure differential across the refrigerant control large enough to ensure its proper operation.
Fig 7 Water regulating valve (Reproduced with permission of Danfoss [Australia] Pty Ltd.)
Electrically operated solenoids may also be used, connected to open when the motor starts and close when the motor stops. However, this system does not give precise control of head pressure, as does the pressure-operated valve.
Over-condensing Over-condensing in winter months can be a serious problem, particularly with remote air-cooled condensers, and water- or evaporative-cooled units, as liquid can accumulate in the condenser, starving the rest of the system. Also, overcapacity of the compressor under the low head pressures can cause inefficient operation of the refrigerant control and short cycling for the compressor.
On air-cooled units, special bypass valves are available which bypass discharge gas directly into the liquid receiver in cold weather. In the case of multiple-fan condensers, the bypass valves “off cycle” one or more fans as the temperature falls. Another way of controlling head pressure is to use speed controllers on condenser fan motors.
With simple water-cooled units, valves operated by head pressure are used to control water flow. With cooling towers and evaporative condensers, the water temperature should not fall below 20°C. Control can be maintained by:
• cycling the air-circulating fans off as the water temperature falls to 25°C, or
• bypassing some, or all, of the water directly back into the condenser or water reservoir without evaporation in the airflow.
Common faults and testing High head pressures on water-cooled plants are generally due to one or more of the following:
• air or non-condensable gas in the condenser
• restricted water flow due to pump inefficiency, air in the lines, valve or strainer restriction, or scale accumulation in supply or condenser tubes
• high relative humidity of atmospheric air onto the cooling tower, resulting in high water supply temperature.
Quick tests can be made, using thermometers only, to isolate these problems:
• The water temperature from the cooling tower and into the condenser should not exceed 30°C.
• The water out of the condenser should approximately be – but not exceed – 6K above the water-in temperature (eg water in at 30°C with water out at 36°C or water in at 27°C with water out at 33°C).
• The refrigerant condensing temperature should be approximately 5K above the water-out temperature (e.g., water outlet temperature = 35°C; correct condensing temperature, R22 refrigerant = 40°C; headpressure, R22 refrigerant = 1430kPa gauge).
Note: Condensing temperatures for water-cooled units may be as much as 20K below similar air-cooled units. This results in at least 20 per cent increase in cooling capacity. ■
suction discharge water regulating valve
warm water out
condenser cold water in from mains
Fig 8 Waste water system
liquid to control
This month’s Skills Workshop has been taken from Australian Refrigeration andAir-conditioning, Volume 1, authored by Graham Boyle, F.AIRAH.





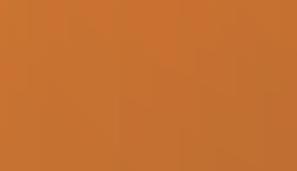
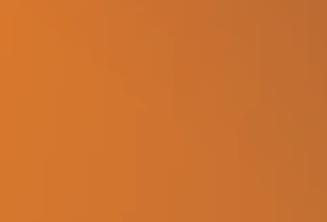




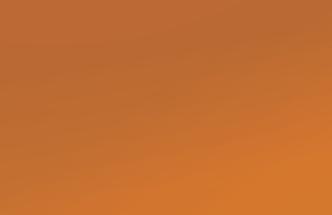





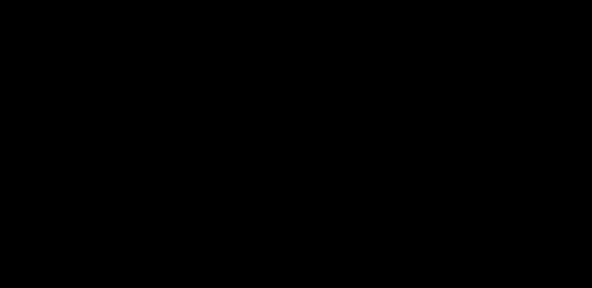


