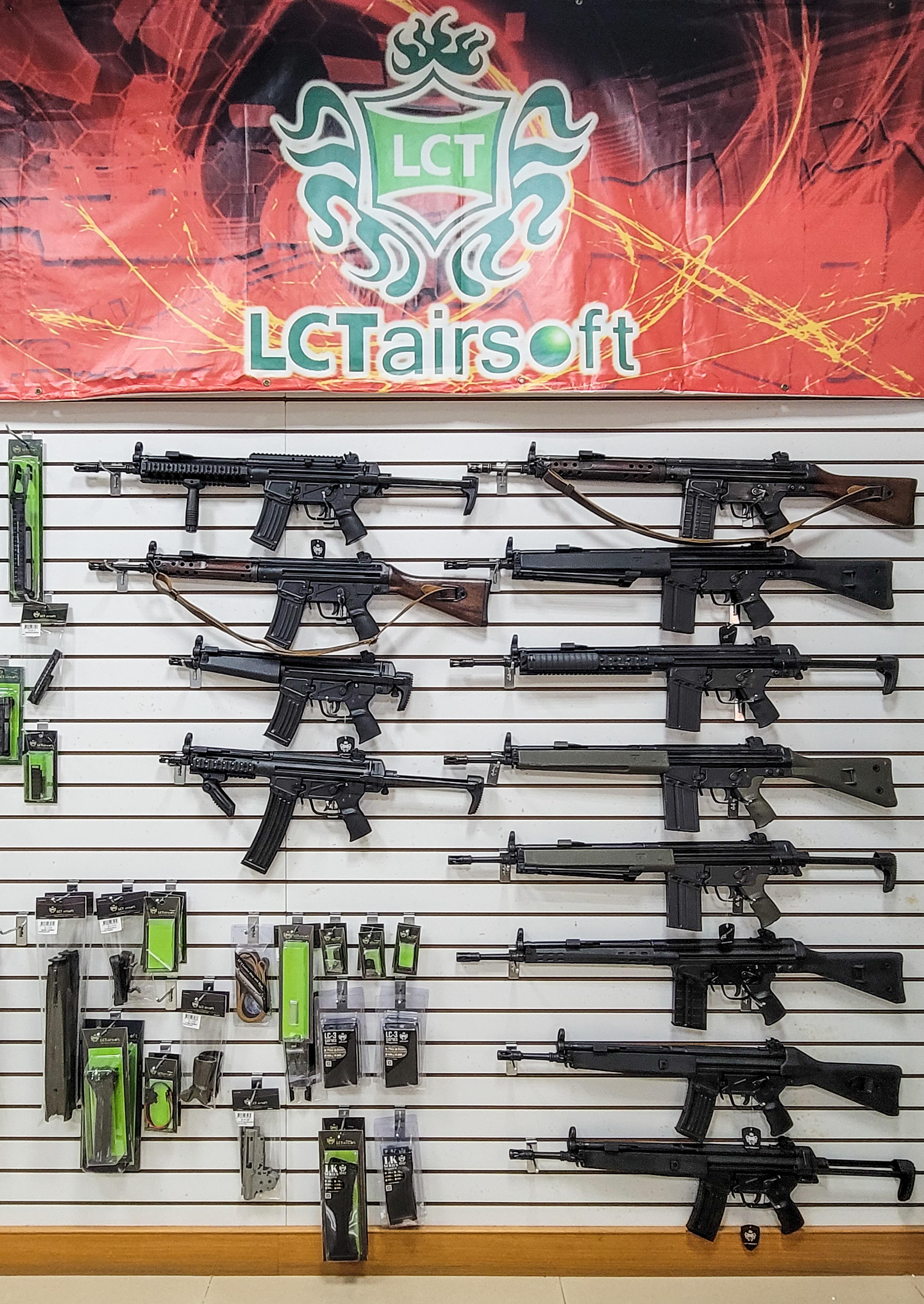
16 minute read
INSIDE AIRSOFT: LCT
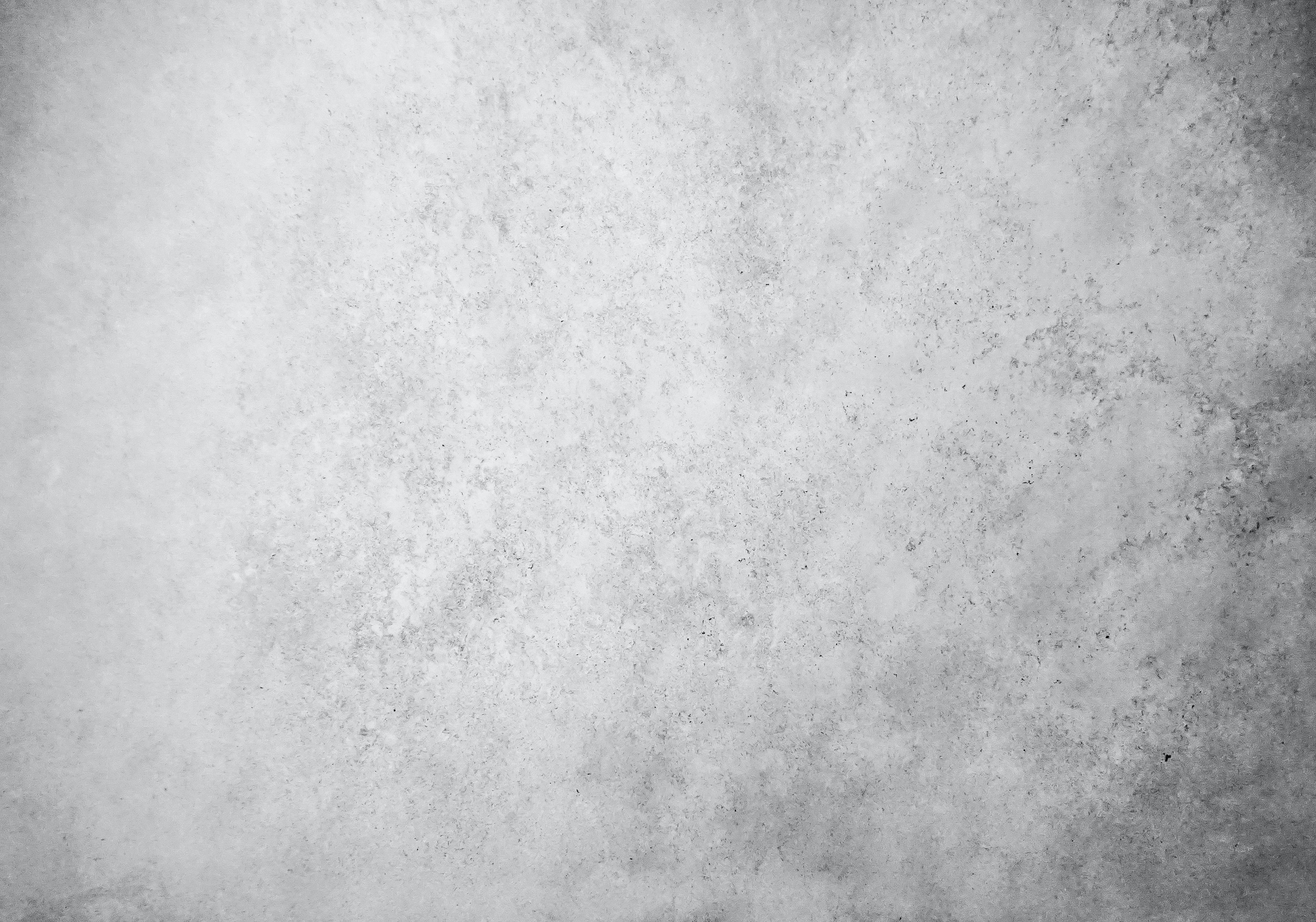
HAVING ONLY JUST MET THEM ONCE AGAIN AT THE MOA CAMPFEST 2022 THE WEEKEND PRIOR, STEWBACCA ORGANISED TO FINALLY GET AROUND TO VISITING LCT AIRSOFT’S MANUFACTURING FACILITY DOWN IN CHANGHUA, TO THE SOUTHWEST OF TAIWAN’S CENTRAL TAICHUNG CITY, HAVING TAKEN SOME EXTRA TIME OFF WORK FOLLOWING THE SHOW TO DEAL WITH THE USUAL ADMIN AND AFTERMATH, AS WELL AS SPEND SOME MORE TIME ON AIRSOFT RELATED THINGS!
While I was at the MOA Campfest I managed to get hands on with some of their latest releases and do some obligatory posing in front of their LCT Airsoft branded backdrop emblazoned with an array of pictures of their products as well as their slogan; “We sell not only guns, but dreams”! So, off to see where they made these dreams I went.
Once again I found myself making use of the Taiwan High Speed Rail (THSR, our version of Japan’s bullet train… well actually purchased from them in fact!) to make a rapid exit from Taipei and move South to the typically even warmer climes of the midlands around Taichung. Arriving at the station I was greeted by the boss man himself Kevin, as well as Bella andBenita and treated to my first ride in a very nicely decked out Maserati; business is evidently going well, and no doubt with good reasons we’ll get to later.
Their hospitality only intensified with discussions of our personal histories as well as the general airsoft industry and scenes in Taiwan and back in the UK, and majorly players and issues in distribution as well as the usual comparison of firearms culture and relevant legislation as well as my own playing and competitive activities and history, all over an excellent Teppanyaki dining experience which meant the team nearly had to roll me back to the car Charlie and the chocolate factory style; the introduction to the team somewhat reflected the entrance in style that the company itself made to the airsoft market.
OLD EXPERIENCE, NEW DIRECTION
LCT (Li Cheng Technology) originally started out way back in 1982, producing more typical lifestyle implements the likes of cutlery or other household wares from metals by way of stampings and machined castings; this in itself is somewhat a specialised industry and manufacturing process that typically requires a great deal of experimentation and experience in order to turn ideas into completed products, using heavy machinery to physically fold or pound sheet metal stock into sometimes very complex shapes. This was certainly something which early modern-era real steel firearms manufacturers came to realise, with the Germans being masters of the trade and spearheading the use of sheet metal for use in more economical, lightweight and industrial scale production of small arms, with the likes of the rise of Heckler & Koch in the post-world WWII era in the remnants of the industrial heartlands of Germany with their increasing use of these methods to produce their world beating modern firearms such as the G3 and MP5; those may become relevant shortly.
With this long serving expertise in a niche manufacturing capability that few other airsoft producers had access or experience in making use of, LCT initially made a foray into subcontracting for other manufacturers as well as eventually producing a full steel construction Kalashnikov kit intended to build off a Marui platform in 2004.
This pivot towards our arguably somewhat contentious industry of ‘selling guns’ from more typical household implements was undoubtedly the result of Mr Lin’s own personal interest in firearms and toy replicas. With this initial success into an already competitive industry, especially here in Taiwan, airsoft increasingly became the focus of LCT’s activities to the point where the LCT Airsoft brand was generated as a separate entity a few years later in 2007, following some internal product development and integration of processes and components to enable LCT Airsoft to manufacture an increasing array of replica weapons along a similar theme, those with complex or predominantly stamped steel constructions.
This is where LCT Airsoft really began to make a name for itself and carve out a niche where others before would struggle to; given their own extensive competence with stamping and die technology they
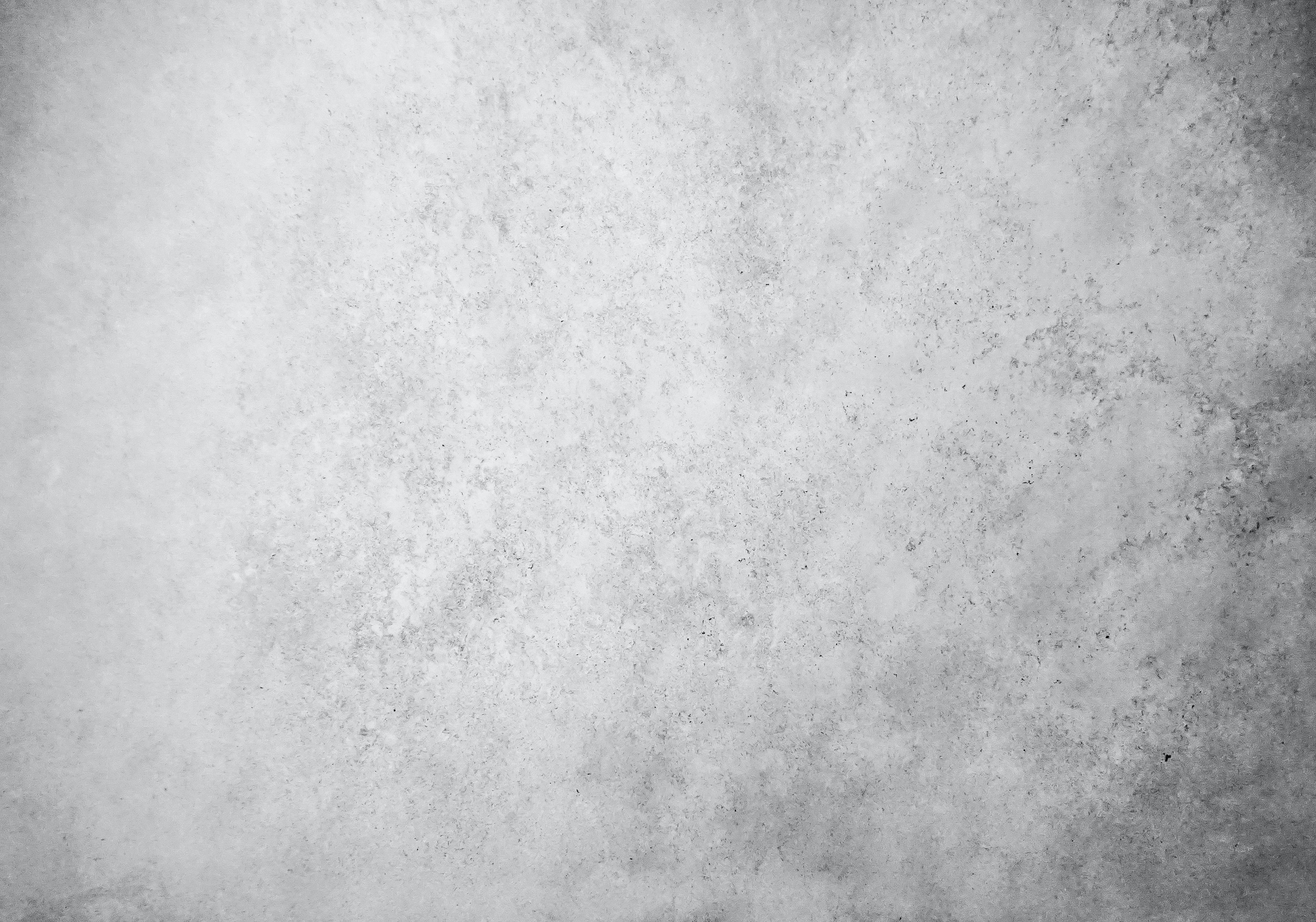

could progress with product development apace without the need to engage external expertise or sub-contractors for the majority of the essential structure of their replica guns, and with a deeper understanding of the capabilities of their own equipment and processes began to make inroads into varying families of real steel equivalents rifles, particularly focusing on ComBloc / OpFor / Cold War platforms.
The LCK series was a great initial success, and already extends to over sixty separate products in the line, with an ever increasing completion of replication of the whole family of real world examples of myriad different national origins and modifications; not just from the offering of the full steel ultra-realistic incarnation of the ubiquitous Soviet/Russian origin AKM many others produce replicas of, but increasingly niche versions such as the Hungarian AMD-65 with its forward canted vertical grip, or the AKMSU specialist carbine with its distinctive thumb hole foregrip, the real world equivalent of which still remains apparently mysterious in its true origins, nonetheless faithfully replicated among its numerous other family members.
LCT Airsoft tend to follow this mentality with their product lines and direction, an all-out assault on a chosen family of real world weapons, with diligent research into existing real world variants; products, additional option components or support equipment, as well as lots of hard work behind the scenes to ensure that their replica firearms are so close to the real thing in external appearance, build quality and dimensions that they can not only remain compatible with real steel accessories or furniture, but have indeed fooled some into thinking they are their real steel counterparts.
While I was visiting the TWAAA headquarters for a previous article on their activities, their current front man Mr Zhang and I were appreciating the limited edition LCT M60 AEG LMG which forms a centrepiece of their one of their displays. He was relaying to me how an American enthusiast and buyer at one of the shows
it was being exhibited at was chatting at great length with their sales team all with the intent of purchasing an array of what he was convinced were real steel machine guns until he was informed they were replicas; evidently they are doing an excellent job of making their airsoft guns true to form!
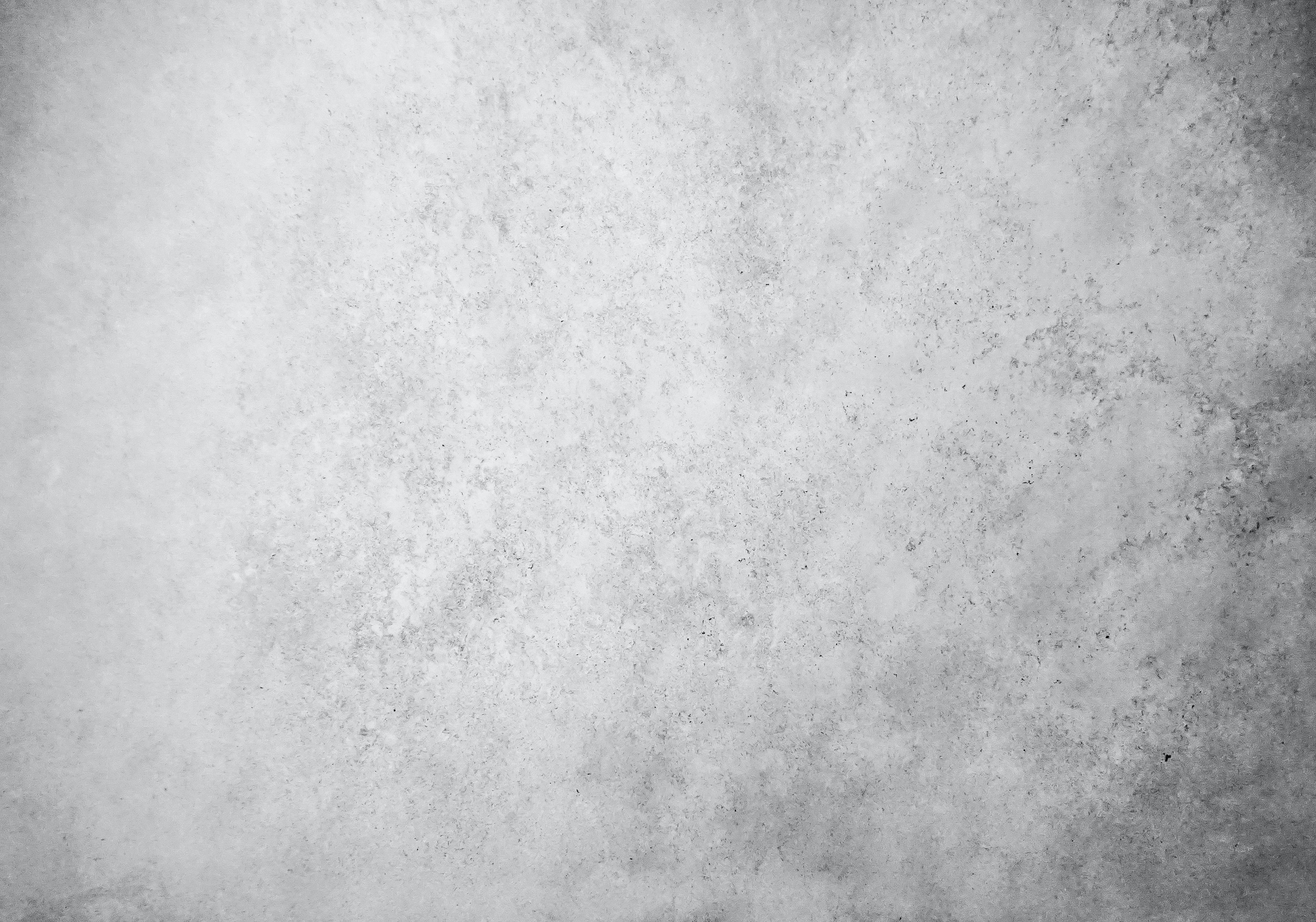
WHATEVER YOU WANT!
With the vast majority of all Kalashnikov-based firearms already recreated in such detail, from the earliest 7.62x39 AKM rifles, as well as carbine and light machine gun derivatives, 5.45x39 AK74 equivalents and even more recently the AK9 / PP19 9mm carbine and SMG variations, the hefty PK/PKM general purpose machine gun, and now their newest addition is an excellently produced replica of the SVD sniper rifle, being made available in traditional wooden grips, modernised polymer furniture, and even soon to be joined by the SVDS side folding stock variant! They are ensuring no stone is left unturned, and basically anything you might come across in the real steel world will be available in faithful replica format from themselves.
Aside from this near obsessive provision for all existing products which enable OpFor players to find something to go with basically any loadout or historical period you can possibly imagine, LCT Airsoft are also seeking to build their brand on the cornerstone of user choice. Along with the existing standard product lines available off their shelves, an extensive and ever-growing array of support components are also available to allow end users to heavily customise the appearance and handling of their own LCT products.
With various sizes and internal capacities of magazine, standard, extended, drum even ‘jungle style’ interconnected pairs, there are numerous
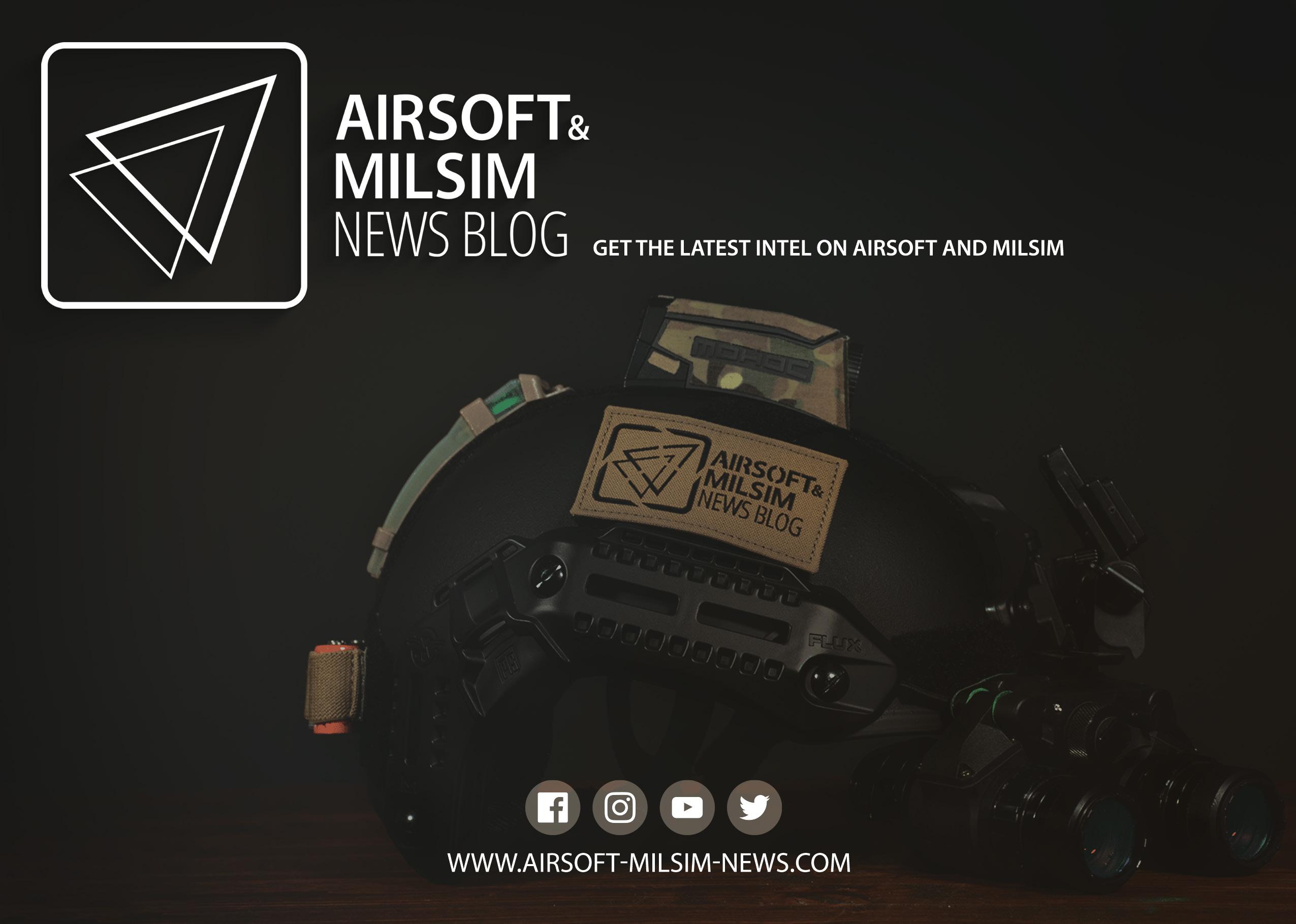
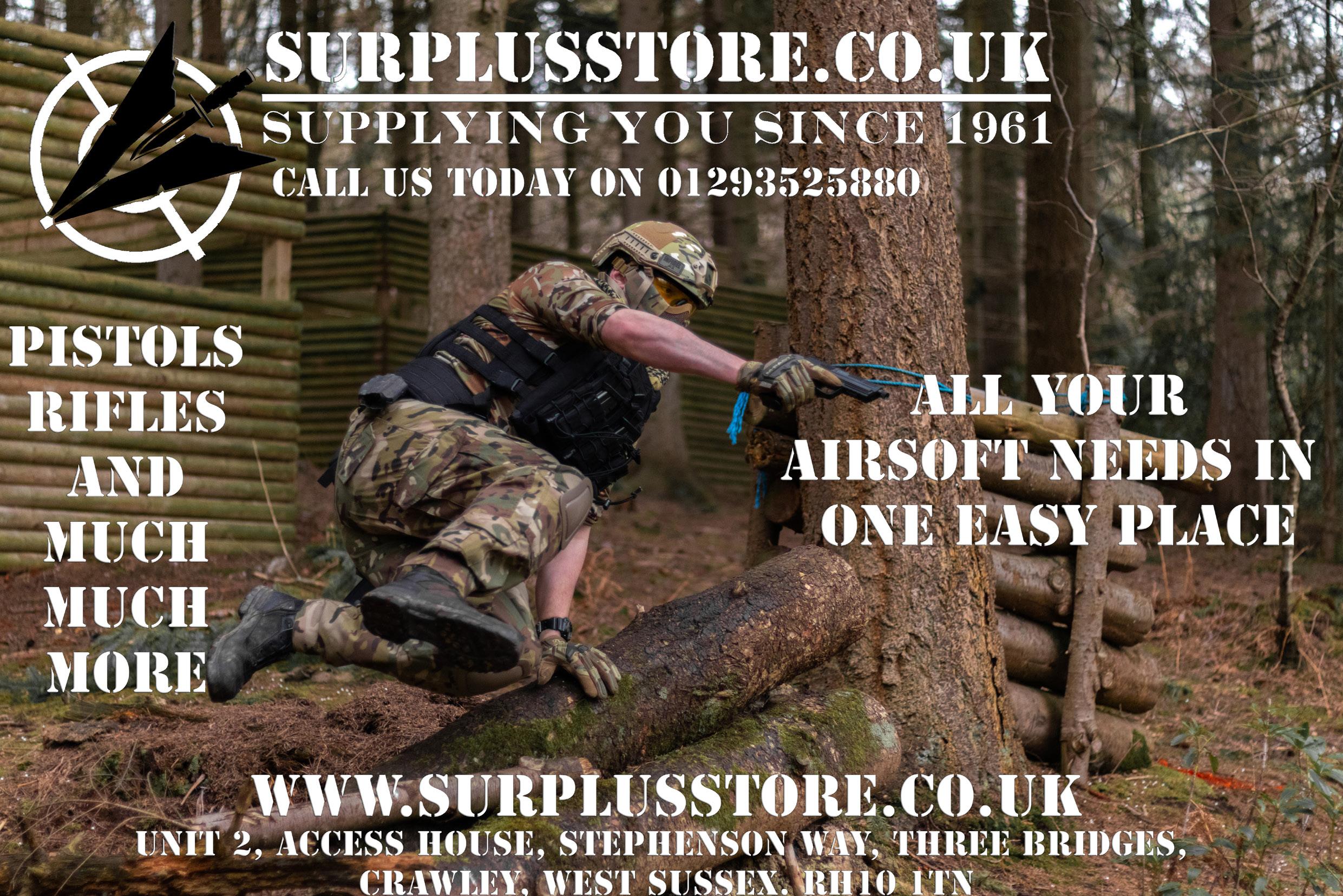

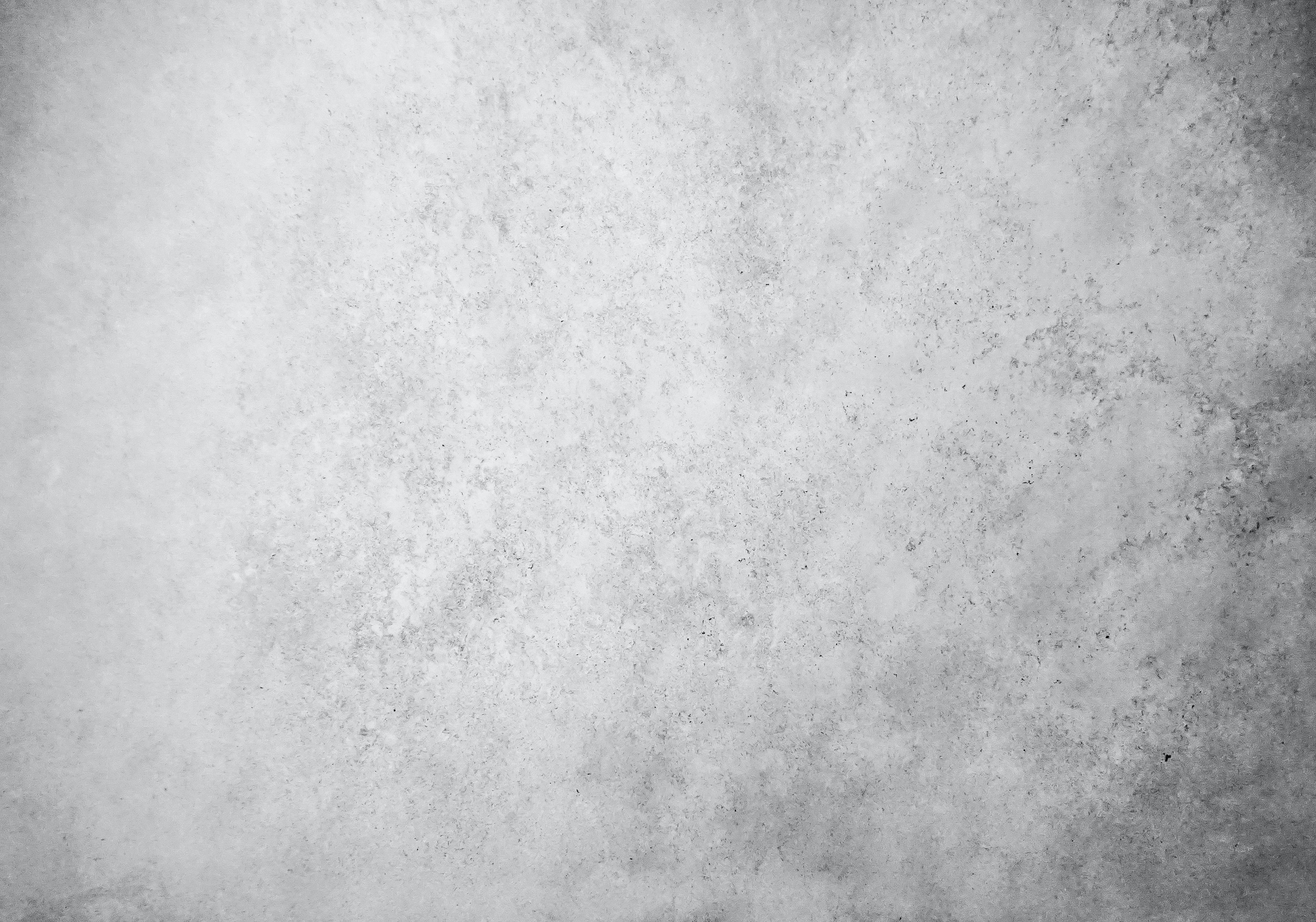
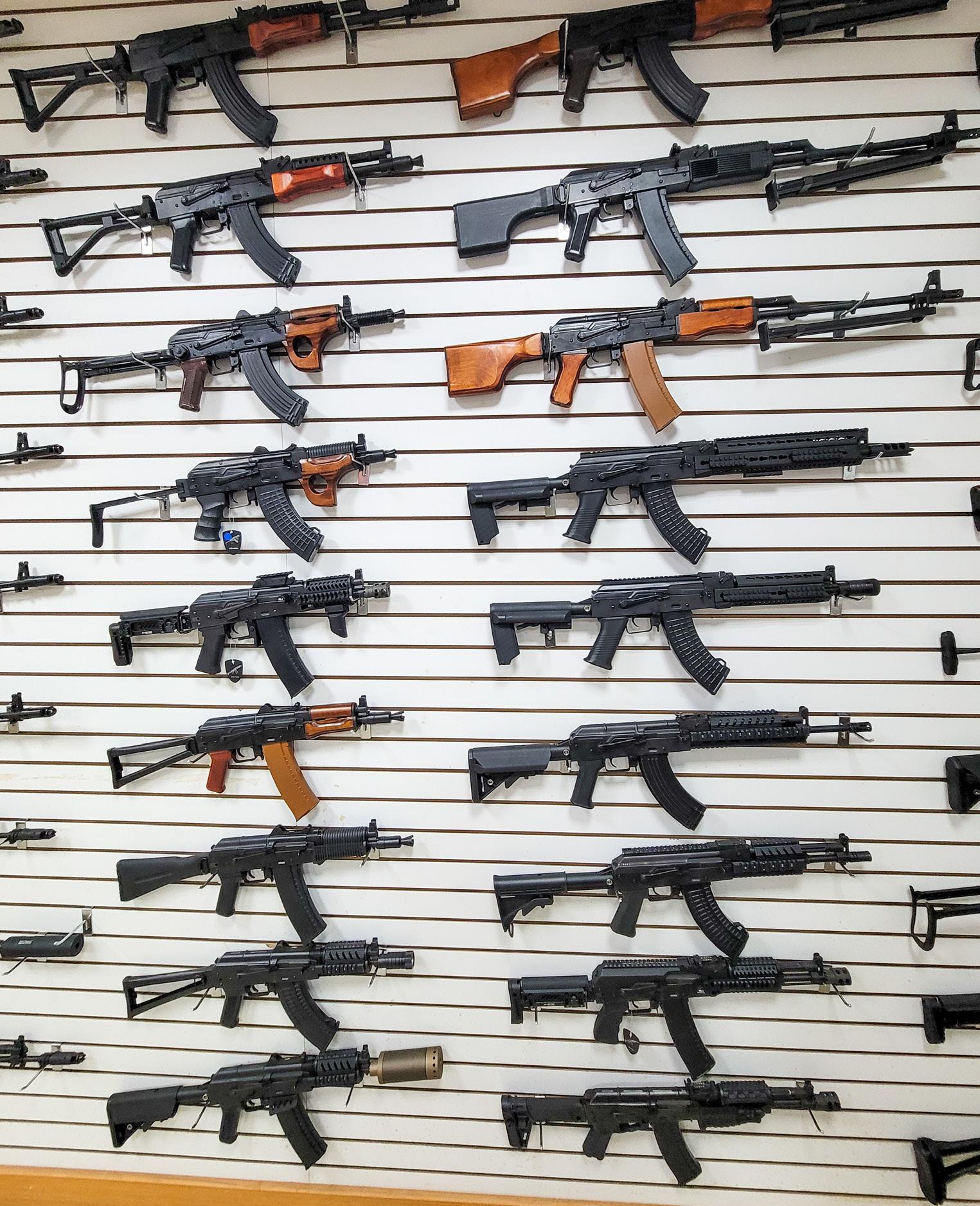
ways to set up the feed system and user’s own load bearing gear to suit their play style or chosen loadout. Furthermore pistol grips, front handguards, rail interface systems, gas tubes, stocks and even full ‘Zenitco’ equivalent systems enable owners to really make their gun their own with exactly the look, feel and function that suits them and espouses their own play style or personal identity.
More recently LCT Airsoft’s product lines have diversified towards those aforementioned pioneers of the real world stamped steel firearms; Heckler & Koch’s products are a mainstay of airsoft the world over, and numerous media from films, TV and video games recount stories of their use in the hands of myriad counter terrorist or military forces, and LCT have turned their attention to answering the call of their fans and customers. Following a similar arc to H&K’s own releases, they furnished the airsoft community with the LC-3 to begin with, the largest and earliest rifle of the real world roller-delayed blowback series that followed work done on the Spanish CETME rifles prior to H&K’s rise in 1960s Germany. Soon further, shorter and intermediate calibre family members joined such as the HK33 (LK33), HK53 (LK53) while even their most recent LCT Fresh YouTube video alluded to the club foot stock and box magazine of the HK21 belt fed machine gun in production design drawings and 3D CAD models on screen; I imagine it’s purely a matter of time before they turn their attention to the MP5 and taking that market by storm with near indestructible replicas lovingly crafted in stamped, rolled and welded steel fabrications.
As well as already producing a further family of AR derivatives (with twelve different models adorning the same wall as their growing H&K variants) opposite the other already full wall of AKs in their upstairs show room, LCT Airsoft are always looking to the longer term, and during our meeting their team relayed to me how most entirely new products or the first in each family tends to take a year or more to complete; thus new product lines tend to be planned on a two or three year upstream basis to account for development and testing time prior to release. Having seen for myself the extensive on-site library of dies and stamping tooling I can imagine it takes a great deal of time and effort from their engineering team to work out all the kinks, or perhaps put them into the metal itself.
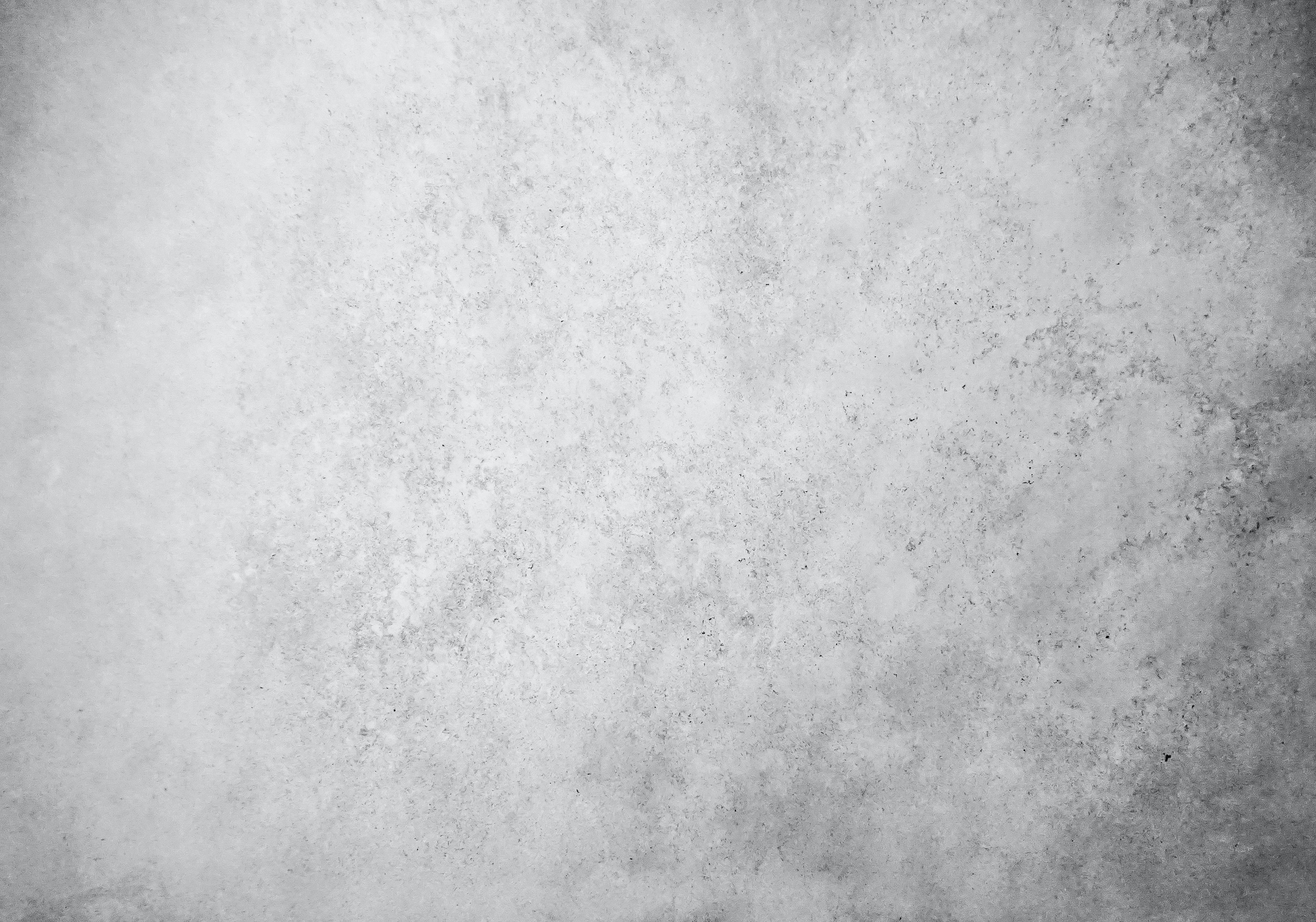
STAMPING THEIR NAME WORLDWIDE
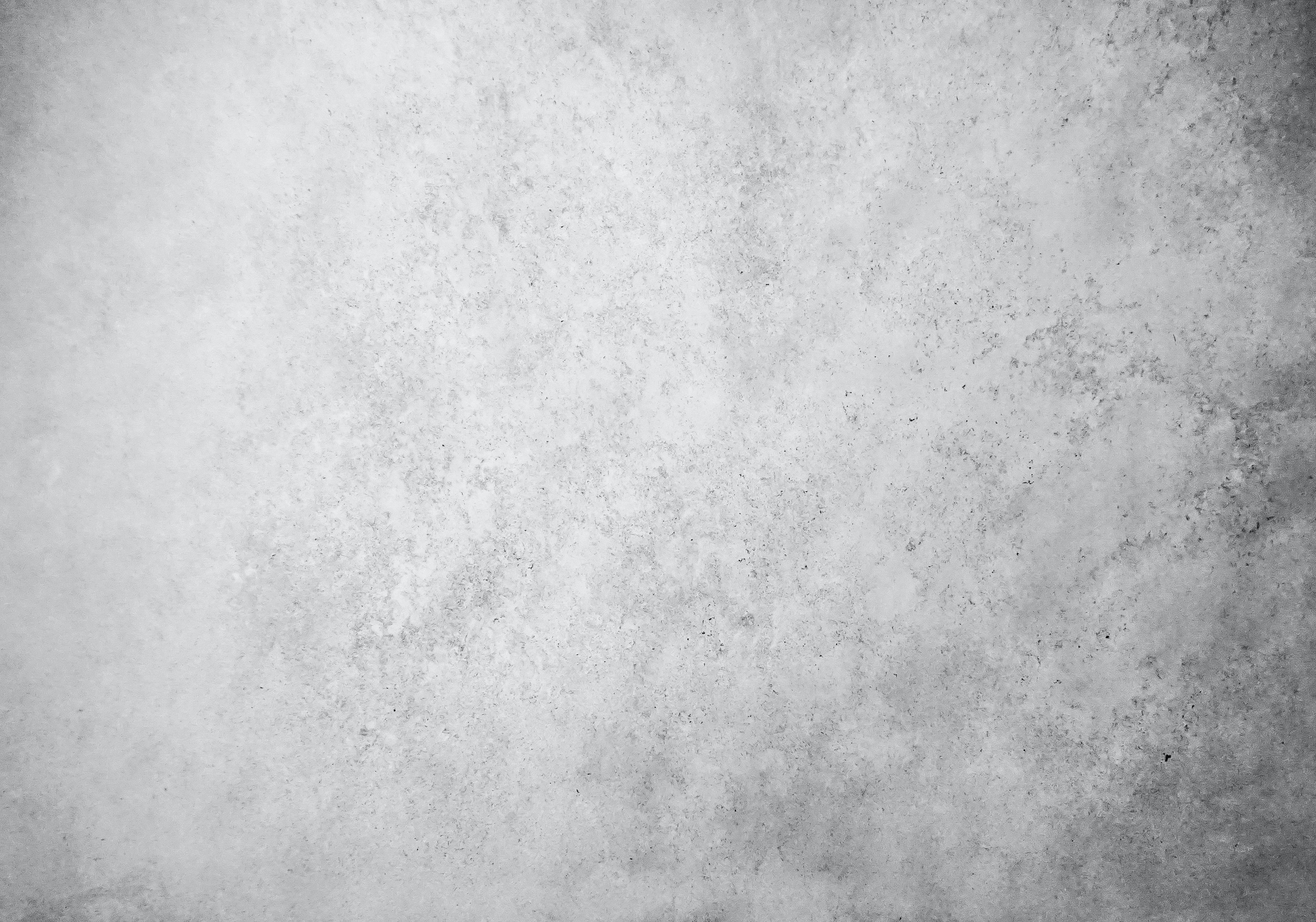
This continuing theme of focusing on their strengths through their product lineage has evidently created a world-beating formula in terms of sheer variety and completeness of each different platform they turn their attention to, and they were all too happy to show me around their own manufacturing environment and let me see for myself the people and processes behind the products that come out the other end.
While precision machined and plastic components have to be outsourced to other specialists (due in no small part to the sheer vibration in their factory floor environment from all the drop stamping equipment and constant beating of metal into intricate shapes which would no doubt upset the precision of CNC machines) the vast majority of their products and key components are made in-house, from flat sheet metal stock, all the way through stamping, grinding, riveting and spot welding of parts into whole sub assembly components such as receivers, folding stocks, top covers, gas tubes, magazine bodies. Even the internal gears are stamped out of a sheet and then precision ground to thickness, while most competitors would resort to metal injection moulding or CNC production processes.
Of course electrical components such as motors, battery connectors, wiring looms and other such off the shelf parts are bought in, and the few cast or CNC machined or polymer components are supplied from outside, but the bulk of production and testing still occurs on site, with a dedicated and experienced team of technicians. We followed the process and products through the factory floor and upstairs all the way to final platform assembly, testing and packaging (with three individual layers of quality control present during the whole process to ensure that what goes into the box and comes out the other end to the hands of a waiting end user!) is stringently controlled and guaranteed to please, and last.
This strive for repeatability and quality was also accented by LCT’s employment of the latest robotic arm welding system which has not only improved their output in terms of sheer numbers made, but ensured a consistent finish and aesthetic quality to all of their welded products. I saw their operator jigging and clamping up H&K front assemblies comprising the previously spot-welded receivers along with outer barrel, cocking handle tube, and sight block, then retreat and press the go button for the robot to go to work, putting all the welds in the places it’s needed, and none where it isn’t. Having come from a background in both heavy structural and hydraulic equipment manufacturing in the UK, I could certainly appreciate the quality control and reduced human fatigue this kind of system affords them!
A CALL TO ARMS
With an ever-growing ecosystem of turnkey solutions as well as wide arrays of customisable components already produced, LCT Airsoft have some long term thoughts of moving towards the pistol market as
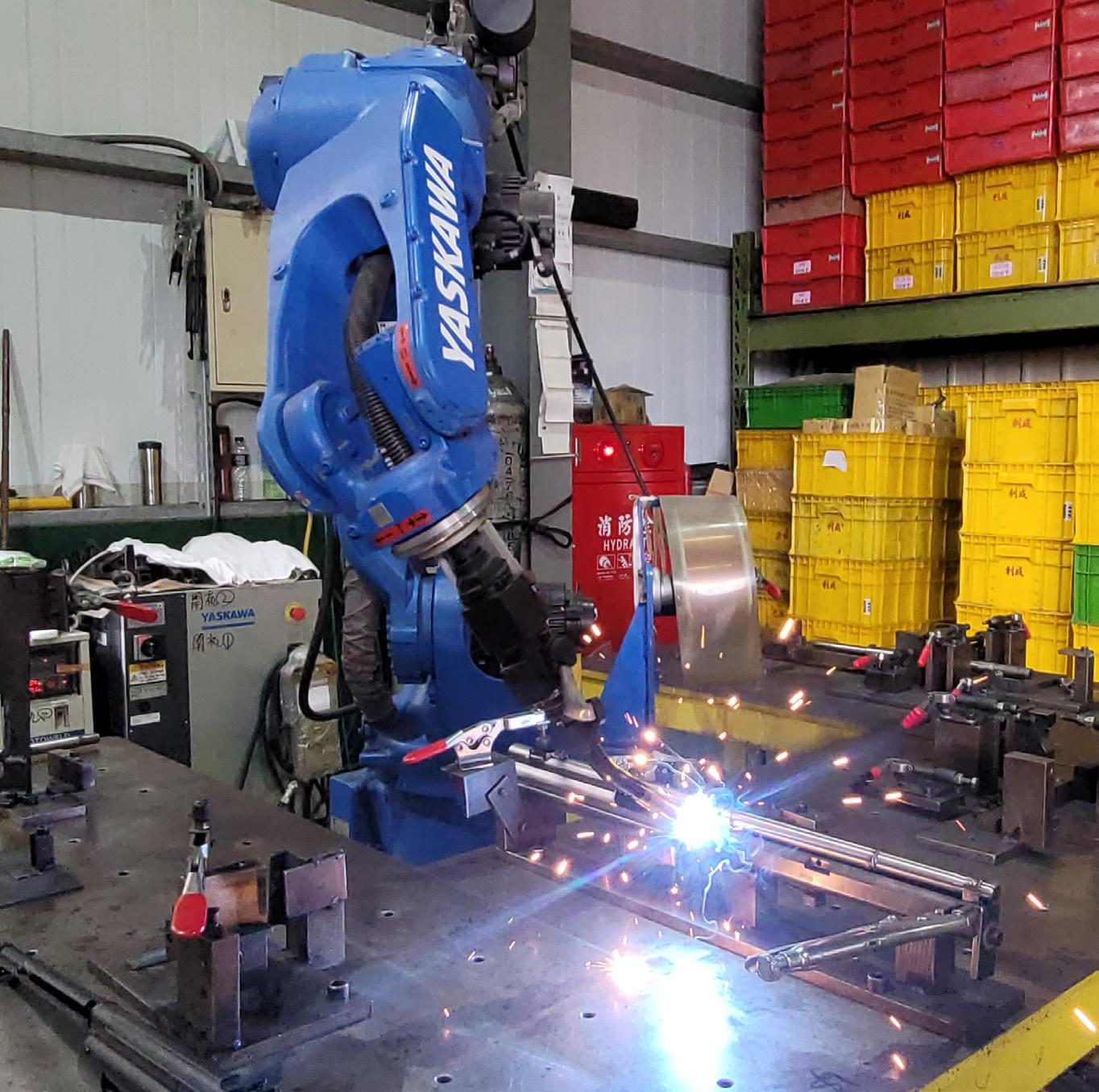
well, but I imagine given the sheer workload and development cycle time they’re already undertaking it might be some time yet before they take the leap. They’re already doing a sterling job of attacking the niche and complicated platforms that many other manufacturers seem to shy away from, personally I’ve spent the last few years chewing Bella’s ear about one model in particular, in no small part due to end users in the UK and elsewhere cajoling me to ask LCT to furnish them with a replica that does the original adequate justice and would no doubt live up to the real steel durability.
For fans of the L1A1, the commonwealth service variant pattern of the FAL, LCT Airsoft are very much interested in producing a replica at some point; however to do it justice, and their usual due diligence, has been difficult thus far; trying to get hold of genuine components can be not only an issue in terms of legal pitfalls in Taiwan, but also in terms of them being somewhat rare these days, certainly in the kinds of permissive environments where civilians could purchase one and help with the required data package for reverse engineering.
Thus, along with their call for photographs or videos of end user’s exploits with their existing products for their community outreach and calendar and video feature competitions, LCT could also use feedback in terms of anyone who can help them source the appropriate information to help realise this particular dream, one that many seem to share, of an LCT Airsoft-produced true to scale L1A1 SLR AEG; if you have a deactivated or functional real one, or components thereof, perhaps you can contact them and help bring the product to realisation as laser scans or other data packages would no doubt be of assistance to them.
With the shop floor tour completed I was taken to the aforementioned showroom and got an appreciation for the sheer scale of the products and the range of them, as well as experiencing the latest in LCT Electric Blow Back (EBB) optional add-on kits in an array of their HK and PP19 platforms, getting a chance to test out and compare them on camera for an upcoming episode of LCT Fresh on YouTube, so keep your eyes peeled for that. I also had the chance to try out their second generation SVD replica; the first batch of a thousand or so have already been completed, but their next variant will also include a MOSFET enabled electronic trigger. Having owned the Real Sword SVD back in the UK, the LCT offering definitely felt familiar in the hands, but the responsiveness of the gearbox, even with a high rated spring installed, was definitely a marked improvement, and no doubt the realistic production methodology of forged steel receiver billets which are then extensively machined removing the vast majority of their weight will please the engineering and gun geeks among you all as much as it does me.
Finally I was introduced to some of the further upcoming releases; with an innovative ergonomic grip that can be fitted under the front handguard tactical rail and removed with two push pins that allows for rapid access to (and changing out of) the battery powering the host LK74 gun, as well as a limited edition highly polished hand finished stainless steel AKM that you can literally see your own reflection in, and even an L3K carbine variant of the full sized 7.62x51 G3 replica with a shortened front handguard making it much handier.
Having had a very productive and insightful day on site with LCT Airsoft we went over my notes one last time and ensured I’d got all the in depth pictures I needed to before they saw me off at the THSR station and I headed off into the sunset, somewhat literally, back to Taipei as the day’s light faded, and I felt somewhat drowsy from the adventure and large lunch I’d been treated to, nearly drifting off on the train to some of LCT’s dreams.
I’d like to sincerely thank Mr Lin, Bella and Benita for their very much appreciated hospitality and great openness and access to their facilities, procedures and plans that’s allowed me to share with you in such depth the work going on behind their products. AA
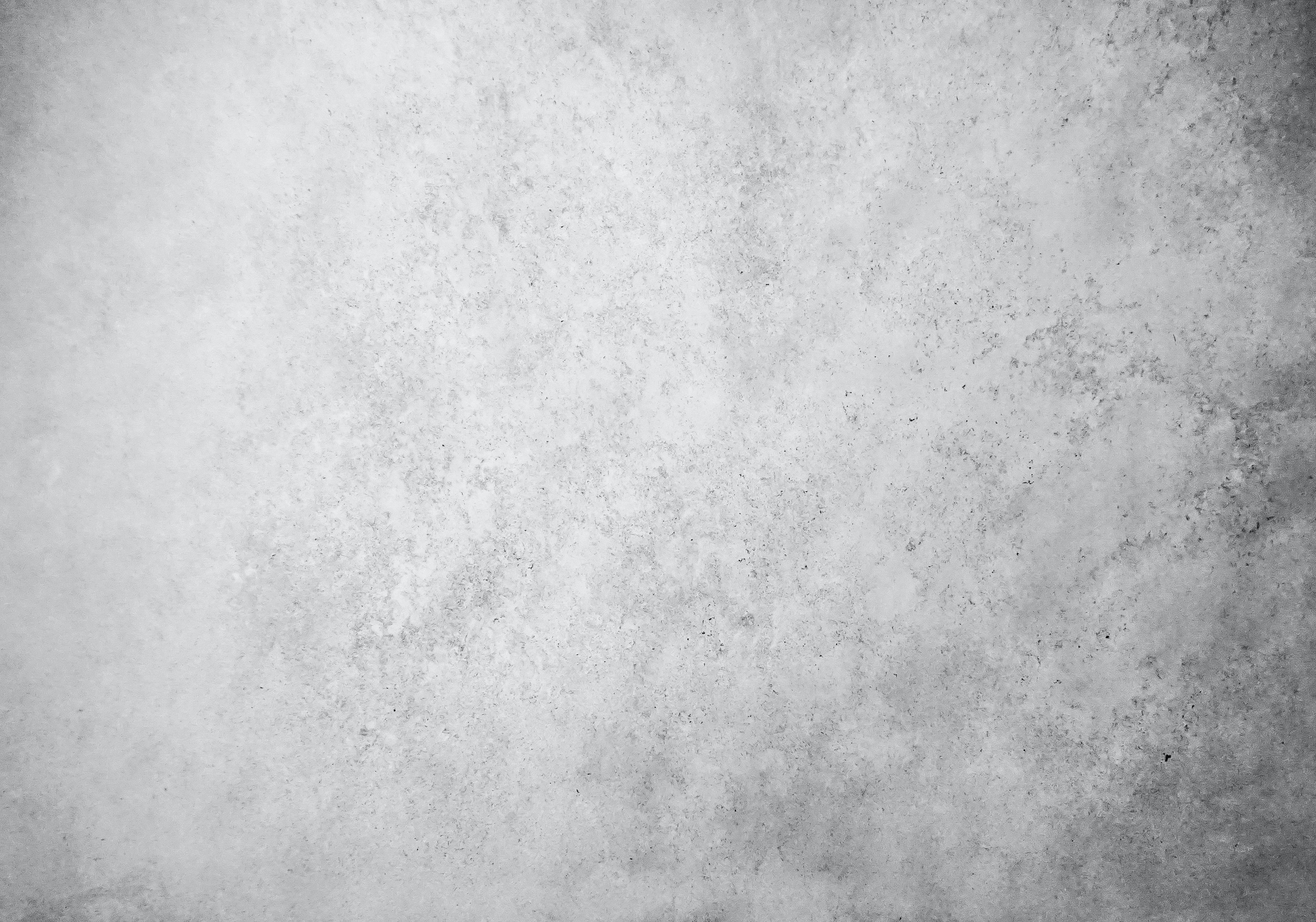
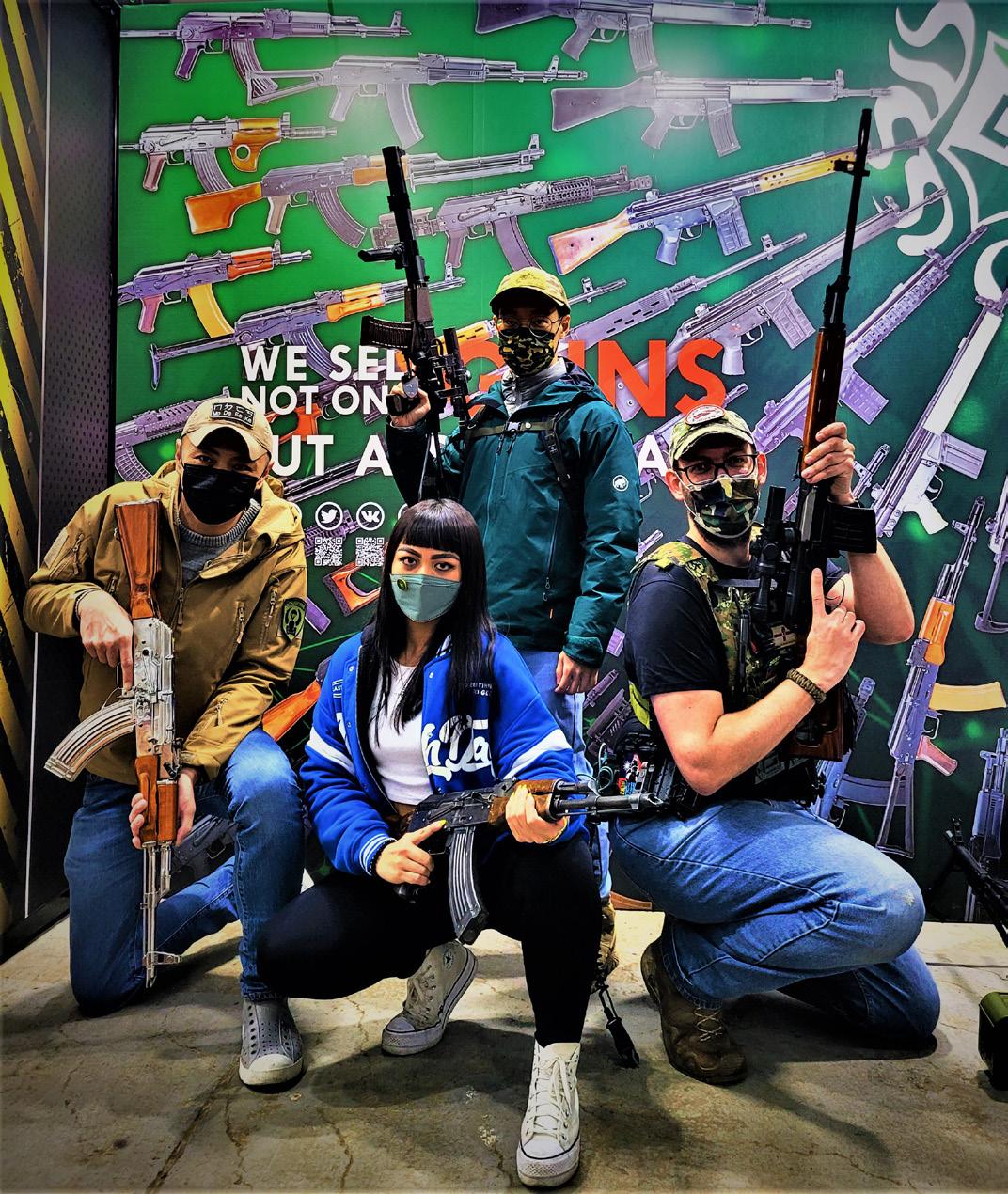
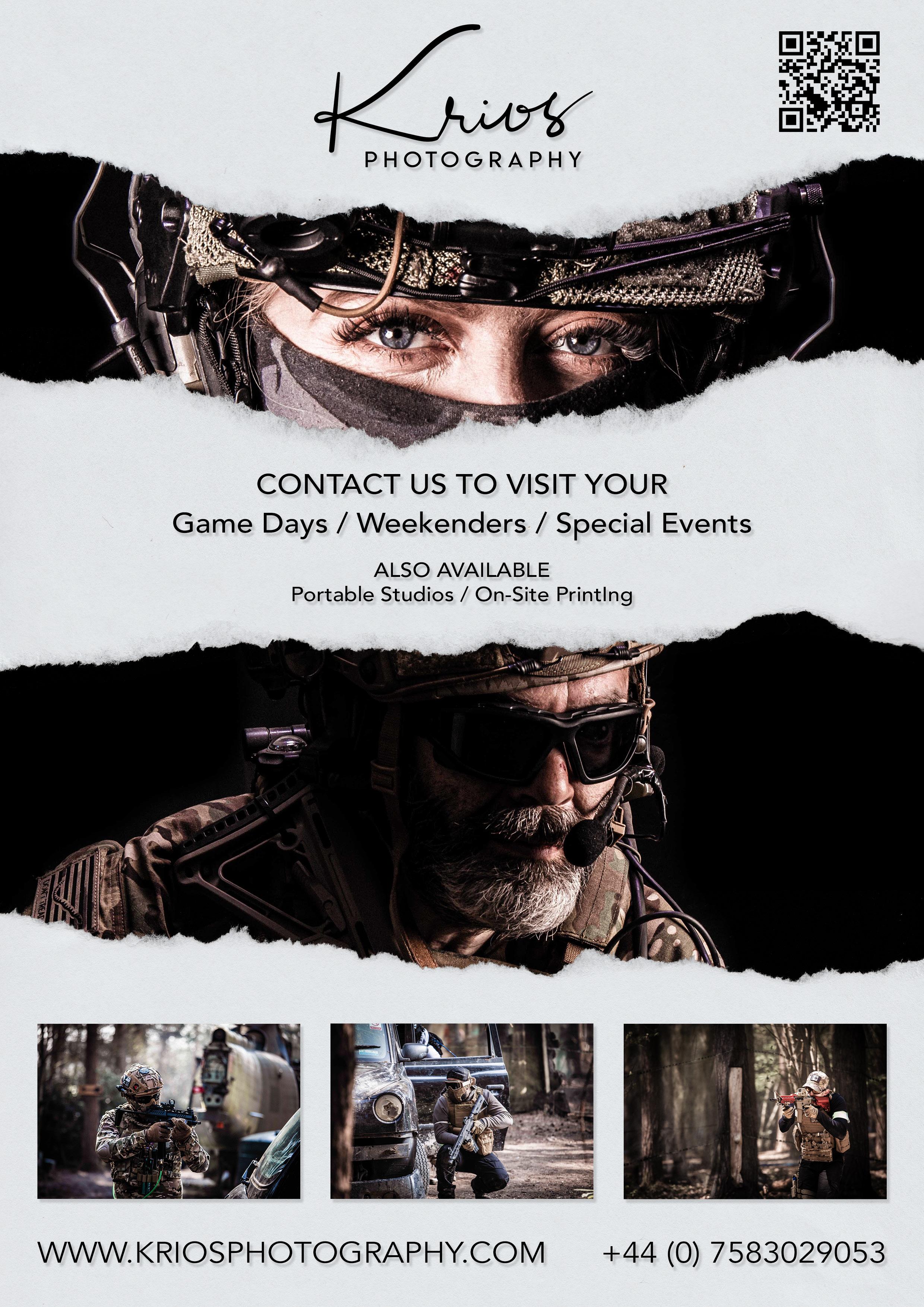