
11 minute read
Motivos específicos de diferencias en los costes de producción entre empresas gráficas
from Alabrent 397
by Alabrent
Existen muchos motivos que pueden provocar una diferencia en los costes de producción. Estas diferencias representan, de hecho, la diferencia competitiva entre empresas. Con frecuencia las empresas se lamentan de los precios de la competencia suponiendo que no existen razones que puedan justificar esa diferencia. Si bien en muchos casos la diferencia entre los precios de unas empresas a otras se derivan de la simple voluntad de obtener ese trabajo en cuestión sin un análisis suficiente de los costes internos, en muchas otras ocasiones existe un gran número de motivos por los que los costes de producción pueden diferir de unas empresas a otras. Cada empresa debería descubrir sus propias oportunidades para progresar en este sentido y, con ello, mejorar su competitividad.
por Jaume Casals de RCC Casals Consultants, S.A.
Advertisement
Comentaremos aquí tan sólo algunos de esos motivos. Aunque en algunos casos puedan parecer obvios, no deben dejar de considerarse, puesto que condicionan el entorno de la empresa y se deben tener presentes para las decisiones oportunas en la dirección de la actividad.
Para cada uno de los motivos se describe y “discute” su relación con los costes de producción y las razones por las que llevan a diferencias entre empresas, y se dan algunas recomendaciones en cuanto a “qué se puede hacer” para progresar hacia unos costes menores.
Coste de los salarios
Incluimos dentro de este motivo las diferencias de costes de salarios que puede existir entre empresas y que afectan directamente al coste de producción. Se incluyen únicamente los costes asignables directamente a cada unidad de producción, y no los “indirectos” que se tratarán en otro motivo.
Las diferencias salariales pueden responder a múltiples causas. Al evaluar el nivel salarial de un operario frente a la media del sector, se debe tener en cuenta tanto el puesto de trabajo en cuestión como el rendimiento del operario. A pesar de que existen convenios que especifican el nivel salarial que corresponde a cada puesto de trabajo, en la práctica es frecuente que se incluyan complementos que generen estas diferencias entre empresas.
Si ya en una misma empresa existen diferencias salariales entre personal que realiza el mismo trabajo, es normal que existan diferencias entre personal de diferentes empresas aunque se realice el mismo trabajo. Por otra parte, también diferentes operarios de la misma empresa pueden estar dando un rendimiento distinto en cuanto a la cantidad y calidad de la producción obtenida, aspecto que probablemente justifique la diferencia salarial.
Al margen de estas razones suficientemente obvias, existen otras razones como la situación geográfica o la antigüedad del operario que afectan a los niveles salariales relativos entre personal con la misma dedicación.
Qué se puede hacer
En un momento en el que es difícil encontrar operarios válidos para determinados puestos de trabajo, es difícil conseguir un control total sobre este tema. Además, esta dificultad en encontrar operarios “válidos” hace que cuando se consiguen sean justificables niveles salariales muy superiores a los establecidos por convenio.
Sin embargo, es importante conseguir un cierto paralelismo entre el rendimiento en producción y el coste salarial. Los incentivos son una herramienta que pretende cubrir esta necesidad.
El sistema de incentivos debe perseguir el beneficio del conjunto de la producción y no de operarios individuales, por lo que debe valorarse de forma conjunta, consiguiendo una motivación entre operarios para el bien común. Los incentivos deben basarse a partir de una base salarial, y teniendo en cuenta el progreso en productividad (sin afectar a la calidad).
Es probable que un sistema de incentivos incremente el coste salarial. Realmente, si el sistema de incentivos está estructurado adecuadamente, se debería desear que este coste salarial se incrementara, ya que generaría necesariamente un incremento en la productividad que, a pesar del incremento en el coste salarial, permitiría obtener un coste de producción menor.
Coste de la estructura
También es habitual encontrar diferencias importantes en el coste de personal de estructura entre empresas que realizan el mismo tipo de producción.
Es muy frecuente el caso de empresas familiares que han crecido a lo largo de los años, y que habiendo pasado una fase de crecimiento importante, han entrado en un momento de recesión o de “control de los gastos” como consecuencia de un mercado más competitivo y una falta de actualización de la empresa en todos sus niveles. Probablemente no se ha encontrado al “hijo” sucesor adecuado, o el “padre” fundador no ha sabido delegar y adaptarse a las nuevas formas de entender la empresa.
En este proceso, se ha incorporado personal en la parte “de oficina” de la empresa durante los años de bonanza, que no se ha sabido racionalizar en los momentos en los que la producción ha bajado.
A veces se crean necesidades
Las diferencias salariales pueden responder a múltiples causas. Al evaluar el nivel salarial de un operario frente a la media del sector, se debe tener en cuenta tanto el puesto de trabajo en cuestión como el rendimiento del operario burocráticas “ficticias” que se convierten en un peso excesivo en la estructura de la empresa.
Qué se puede hacer
Si bien en el área de producción es más fácil identificar las necesidades y las “sobrecapacidades”, en los departamentos administrativos (tanto de administración como de producción), no es fácil simplificar un proceso que se ha ido complicando con el tiempo.
Es importante realizar un estudio de organización (sea de forma interna o de forma externa a través de consultores especializados) analizando y desarrollando los siguientes aspectos (y en este orden):
- Análisis de las necesidades de la estructura de la empresa en cuanto a personal “de oficina”, definiendo áreas de responsabilidad y tareas específicas a resolver.
- Evaluar la necesidad de dedicación de tiempo para cada una de las áreas y definir los puestos de trabajo y los perfiles de personal necesario.
- Analizar el personal disponible y valorar su adecuación a la estructura “ideal” diseñada.
- Reconsiderar la estructura diseñada teniendo en cuenta la realidad del personal disponible. En esta fase se debe ser algo flexible para adecuar los puestos a las capacidades del personal disponible, pero no excesivamente. El objetivo es conseguir una estructura optimizada que funcione de forma eficaz. Probablemente se llegará a la conclusión de que se tiene que despedir o reubicar una parte importante de personal, y realizar un proceso de selección para conseguir nuevo personal para puestos estratégicos que garanticen el funcionamiento de la nueva estructura. Es habitual que después de este proceso se consiga una disminución de un 20% del personal, despidiendo de un 30% a 40% y contratando de un 10% a 20%.
- Finalmente, se deberá implantar y mantener la nueva estructura, definiendo y explicando detalladamente las responsabilidades y exigiendo el rendimiento.
Turnos de trabajo
Probablemente este sea uno de los aspectos que pueden afectar más a la diferencia de costes de producción entre empresas.
Es muy frecuente encontrar en una empresa máquinas de diversa antigüedad y con características similares en cuanto a formato y número de colores. Sin embargo, en estos casos también es frecuente que se esté trabajando a menos de dos turnos completos.
El coste de las inversiones en la industria gráfica es realmente muy elevado como para que no se obtenga el máximo provecho de ellas. Obtener el máximo provecho no significa utilizar los equipos durante muchos años “hasta que revienten”. El máximo provecho se obtiene con la optimización de los recursos y con las inversiones adecuadas.
En la comparación de costes de producción entre una empresa con dos máquinas 70 x 100 cm de cuatro colores trabajando 12 h al día y otra con una sola máquina trabajando 24 h al día, con toda seguridad la segunda conseguirá unos costes de producción mucho menores.
A pesar de que las horas de disponibilidad de los equipos sean equivalentes, en el primer caso existen paros (comidas e inicio y fin de jornada) que se transforman en menos tiempo productivo. Además, probablemente una de las máquinas será más antigua que la otra, por lo que el nivel de productividad será menor.
Si avanzamos en el tiempo, la empresa con una máquina la habrá amortizado mucho más rápidamente y podrá cambiarla antes por una de última tecnología. ¡Atención! Decimos cambiarla, y no añadir una máquina más.

Mientras, la otra empresa seguirá con las mismas máquinas. Con los años, la diferencia en productividad y, consecuentemente, en costes de producción, será muy grande.
Qué se puede hacer
Es imprescindible entender que se tiene que aprovechar al máximo los equipos más productivos, aunque sea a costa de detener otros equipos menos productivos. El personal disponible debe trabajar en los equipos más rentables para maximizar el beneficio.
Es posible que al adquirir un nuevo equipo no se quiera eliminar el antiguo por considerar que puede realizar producción válida, y sacarnos de un apuro en un momento determinado. Pero el equipo antiguo únicamente debe ponerse en marcha cuando no haya otro remedio. El equipo nuevo debe trabajar todas las horas disponibles, consiguiendo una amortización rápida del equipo y pudiéndolo cambiar cuanto antes.
Además, existe el tiempo perdido correspondiente a paradas para comidas y de inicio y fin de jornada, que en un sistema de turnos enlazado desaparece. La producción también se ve afectada en términos de calidad por efecto de estos paros.
No se trata simplemente del paro en si mismo. Se trata de que el operario ajusta el trabajo para que se adapte a estos paros, alargando tirajes o preparaciones para hacerlos coincidir con el paro. De diferentes análisis de empresas, se ha concluido que los tiempos perdidos por efecto de este tipo de paros fácilmente son los siguientes:
- Tiempo perdido antes del desayuno: 0,10 h (6 minutos)
- Tiempo perdido después del desayuno: 0,20 h (12 minutos)
- Tiempo perdido antes de la comida: 0,40 h (24 minutos)
- Tiempo perdido después de la comida: 0,50 h (30 minutos)
- Tiempo perdido en el inicio de turno (sin enlace con el turno anterior): 0,65 h (38 minutos)
- Tiempo perdido al final del turno (sin enlace con el turno posterior): 0,50 h (30 minutos)
Con estos tiempos se ha construido la tabla siguiente que muestra la comparación de productividad por efecto de los turnos de trabajo. La columna de la izquierda muestra el posible aumento que se puede conseguir respecto a un sistema de turnos sin paros, considerando el tiempo perdido respecto al total disponible. Por ejemplo, en el primer caso de un turno de 8 horas con parada para comidas y desayuno, el efecto de los paros es de 2,35 h, que representa el 42% del tiempo de presencia total. En cambio, en un turno seguido de 8 horas representa tan solo el 17%. Creemos que es interesante analizar esta tabla e identificarse en ella, para ver el progreso que se puede obtener en productividad con simplemente cambiar el sistema de turnos.
La claridad en la información y el problema de los errores
Como vamos insistiendo a lo largo de este escrito, la productividad es un factor fundamental en el coste de producción. Juntamente con la productividad, la calidad puede influir de forma notable en el coste de producción, especialmente por dos motivos. Por una parte puede generar repeticiones, con el evidente coste que esto supone. Por otra parte, además de la calidad del producto, nos referimos también a la calidad con la que se trabaja. Una mejor calidad en proceso significa menos errores y consecuentemente mayor productividad.
Qué se puede hacer
La dirección de la producción no debe limitarse a resolver los problemas que van apareciendo en los tra- bajos que se van realizando. Se debe analizar las problemáticas que aparecen y establecer mecanismos para que no se repitan.
Aunque esto parezca evidente, no es muy frecuente que se actúe de este modo. La dinámica diaria no deja en muchas ocasiones ver más allá, o implantar medidas correctoras. Además, como consecuencia de pertenecer al propio sistema, no se identifican muchos errores como problemas, si no como algo “normal” del sistema de producción. Es muy importante ser consciente de estas limitaciones y conseguir abstraerse del “día a día” y evaluar objetivamente lo que sucede en producción.
A modo de ejemplo, damos a continuación una lista de algunos aspectos característicos en los que se generan pérdidas de tiempo o costes innecesarios, así como una breve recomendación para el progreso.
- Especificaciones insuficientes del cliente: Establecer una lista de parámetros a definir con el cliente.
- Especificaciones insuficientes del vendedor: Preparar una ficha de recepción del encargo adecuada a las necesidades, revisando, si es necesario, la existente.
- Especificaciones internas insuficientes, dentro de la orden de producción (generando consultas continuas de forma interna y pérdidas de tiempo): Rediseñar la orden de producción de acuerdo a las necesidades, y asegurar que se cumplimenta de forma adecuada.
- Falta de revisión del cliente: Formalizar la realización de una revisión en fase avanzada o identificar trabajos específicos como trabajos en los que es necesario una revisión en profundidad.
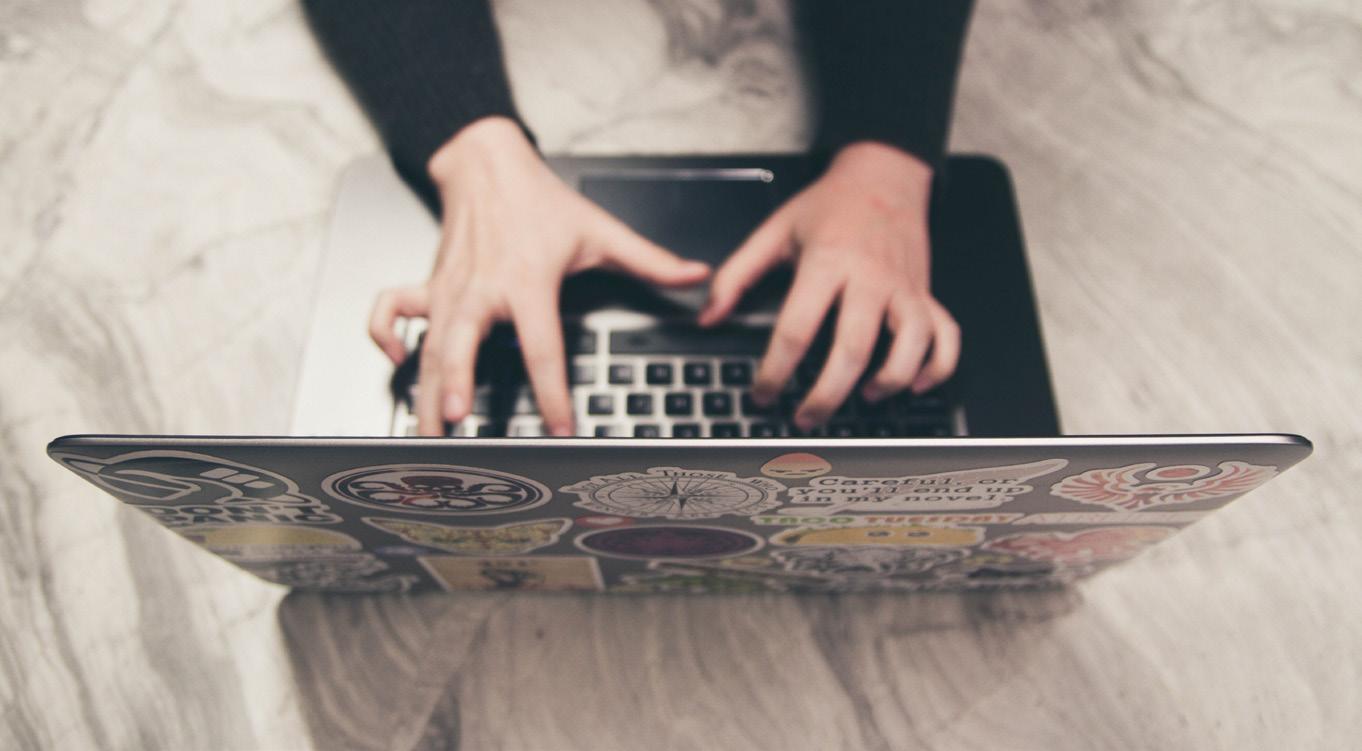
- Falta de elementos de comparación: Preparación de pruebas más completas o más frecuentes.
- Falta de revisión antes de producir la película (o la plancha en procesos CTP): Formalización de un sistema de revisión documentado, utilizando sistemas automáticos de revisión (preflight).
- Influencia de las prisas: No deberían existir como tales. Se debe conseguir una agilidad suficiente en el sistema sin perjudicar la calidad, a través de metodología y estandarización.
- Falta de aseguramiento antes de pasar a producción o al pasar de una fase a otra del ciclo productivo: Seguir las especificaciones dadas para cada etapa. Formación de una Oficina Técnica.
- Errores sin crear la acción correctora: Análisis de cada error e implantación de la medida correctora correspondiente para el futuro.
- Falta de revisión más fiable de los textos: ¿Los correctores son suficientemente capaces? Mejorar la formación del personal.
- Falta de concienciación colectiva: Informar y comentar cualquier fallo ocurrido, contabilizar el número de veces que se produce y su coste, y animar a su disminución. Existen formas establecidas de gran éxito en este sentido.
El tiempo de la puesta a punto
Nos referimos en este apartado al tiempo dedicado a la puesta a punto de la máquina para la producción del trabajo.
Hasta hace unos años, en las ferias internacionales se presentaban las máquinas haciendo bandera de las velocidades de producción que alcanzaban. Hoy en día, el objetivo de los fabricantes es conseguir que los equipos permitan una preparación de la producción en un tiempo menor, y no tanto un incremento en la velocidad de producción.
Esto se debe a que existe una tendencia clara hacia tirajes más cortos, de forma que el tiempo de puesta a punto está ganando importancia relativa respecto al tiempo total de producción.
Cualquier mejora en este aparado significa directamente una mejora en los costes de producción del trabajo en cuestión.
En este sentido, no son simplemente las características del equipo de producción lo que condiciona la posibilidad de un menor tiempo. Hay dos factores más que afectan directamente a este tiempo. Por una parte está la metodología seguida en el cambio, y por otra, las condiciones en las que llega el trabajo a esa fase de producción.
Qué se puede hacer
Naturalmente, se puede invertir en equipos que mejoran este aspecto, tales como máquinas con preparación automática o semiatuomática, o equipos de CTP en el caso de la impresión que generan planchas que, por sus condiciones, permiten un cambio mucho más rápido (probablemente este sea uno de los mayores éxitos en la inversión en un equipo CTP).
Sin embargo, hay muchas otras cosas que se pueden hacer y que no cuestan dinero.
Fundamentalmente, es posible actuar en dos sentidos. Por una parte se puede analizar la forma en la que se realiza la puesta a punto y establecer mejoras en el procedimiento para conseguir un menor tiempo y más constante.
Por otra parte, la estandarización que antes se comentaba en las fases previas de producción (y también en la puesta a punto y la producción posterior), debe permitir que la forma en la que llega el trabajo a la puesta a punto sea suficientemente predecible como para que ésta sea fácil y rápida.