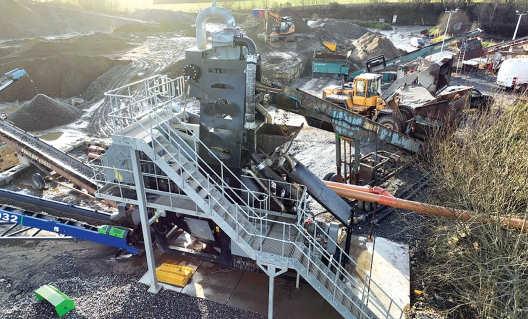
3 minute read
Overhead cranes move towards full automation

Kleiner, commenting on market characteristics emerging during the previous year, explained there is a significant increase in the number of tender documents specifying provisions for crane automation post-installation. Although Condra received no orders for fully automated cranes during 2022, the number of enquiries for such machines was up year-on-year.
“Repetitive crane operations such as those in refinery operations offer clear potential for increased productivity through automation,” said Kleiner. “South Africa has the technology and local manufacturing capability to deliver it, and now the market is becoming increasingly aware. I don’t think we will have to wait long before automation gains a foothold.”
Full automation implies zero involvement by machine operators. It is the ultimate step beyond an overhead crane in which the machine executes a limited number of pre-programmed, automated operations, but still needs an operator to control the crane during randomised, non-repetitive lifting functions (semi-automation).
Condra has offered full automation across its product range since 2020, the culmination of continuous development since the company’s first semi-automated crane installation at a Durban spice company in 2003. That machine comprised a grabbing crane installed to pick spices and transport them to specific points for release over hoppers servicing blending and packing operations.
Advancement indicators
Pointing to the motor industry for indicators of anticipated advances in overhead crane technology, Kleiner said that motor vehicles often led technological development in crane manufacture by several years, but that in the case of automation these roles had been reversed, with overhead cranes currently leading the way forward.
“Vehicle manufacturers were first to use computers to monitor certain mechanical functions,” Kleiner surmised. “Crane manufacturers lagged in this development, and it was a similar case with the control and smoothing out of lifting and lateral movement. It took time for crane manufacturers to introduce variable speed drives, whereas comparable control technologies had been present in motor vehicles for decades.
“This is not the case with automation, however.
MARC KLEINER, MANAGING DIRECTOR OF CONDRA
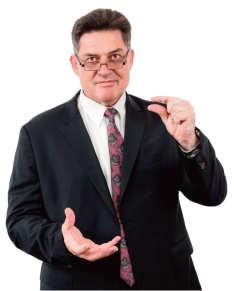
With automation, the crane companies are in the lead. The autonomous crane exists and is already performing useful work, whereas the autonomous motor car is still in the experimental phase.”
Kleiner noted that about one in five enquiries received by Condra now includes specified provision for future automation and provision of fitment and wiring points for the future attachment of cameras with cognitive movement control ability, the main requirements for automation.
A solid base for growth
Kleiner concluded, “Condra is in a good position going into 2023. We have a solid order book which includes contracts recently signed with steel companies and mines across Africa both above and below ground. Locally, our factories in Cape Town and Johannesburg are busy.
“The market is aware that Condra represents more than just crane manufacture and commissioning, offering design and engineering skills that dovetail with those of architects and structural engineers. We have considerable experience of working with these disciplines to deliver world-class, best possible lifting solutions within tight lead times. This is a strong foundation on which to build a successful 2023.” ■
Ensuring that crushed and screened products such as sand and aggregates are cleaned can really serve to boost the quality and ultimately revenue. By investing in washing equipment, companies can make the best use of material that is extracted from their site (with the added environmental benefits) and will be well placed to meet stricter aggregate specifications when they come.
In this space, the industry is well served by an array of equipment providers, vying to design and deliver the most efficient systems to meet customer requirements. This includes the likes of CDE which, last year at bauma, celebrated its 30th year of providing sand and aggregate wet processing solutions for the natural materials processing and waste recycling sectors. When it did so, the company revealed that CDE solutions have, over the past three decades, facilitated the diversion of more than 100 million tonnes of construction, demolition and excavation (CD&E) waste from landfills globally. It also referenced the milestone that the company has successfully delivered more than 2,000 proven solutions in more than 100 countries, marking its credibility across the globe.
A break with tradition
Terex Washing Systems (TWS) presence in southern Africa has been fostered through a 30-year partnership with multi-brand distributor ELB Equipment. The latter is one of the few South African companies who can offer a broad range of earthmoving, construction, mining and quarrying equipment from a single supplier and has established itself as a respected name within the industry in recent years.
The company notes that, since