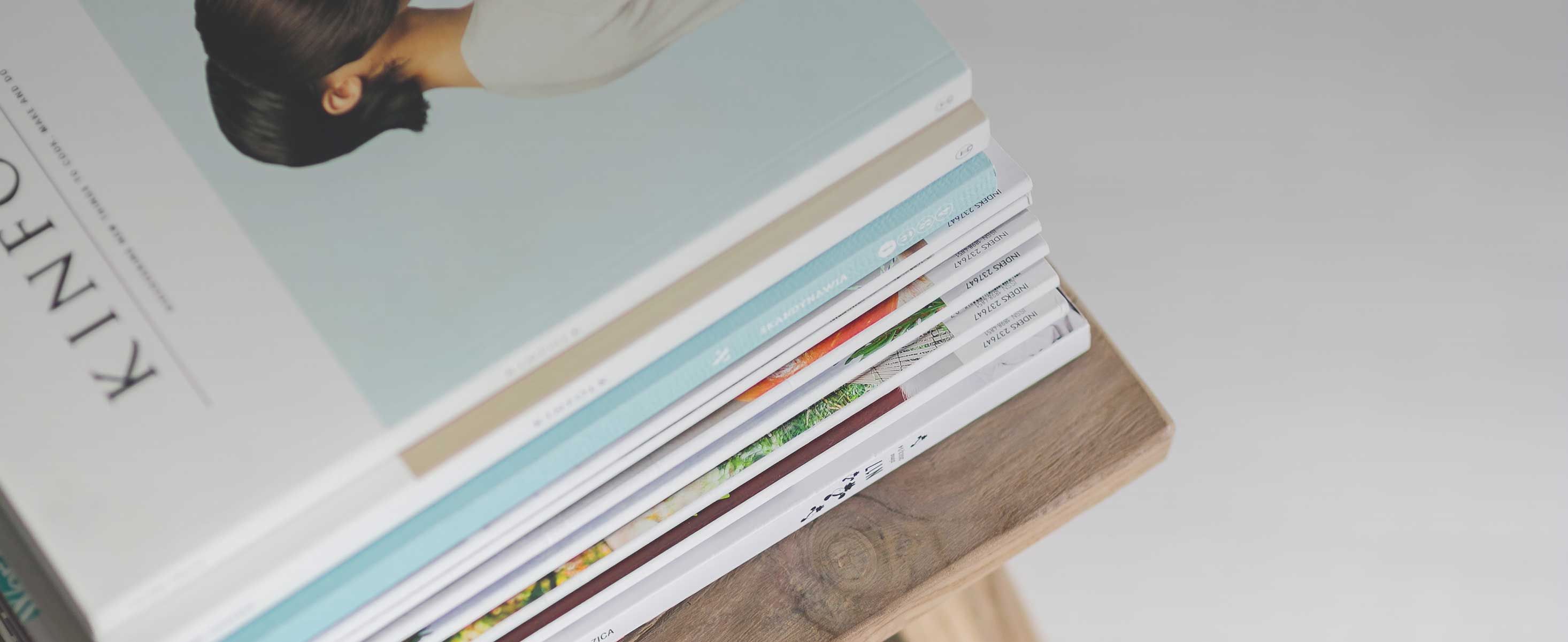
1 minute read
New robot aims to transform Japanese farming
individually suspended on leaf springs, chop organic matter, and break up coarse soil clumps so that the machine can mix soil intensively and work without clogging. The new Karat 10 cultivator is available in mounted and semi-mounted versions, with working widths between three and seven metres. A traction booster and the ContourTrack system which ensures an even working depth in hilly terrain are available for the semi-mounted models.
JAPANESE RESEARCHERS HAVE developed a robot that can help farmers practising Synecoculture. Synecoculture is a new farming method, involving growing mixed plant species together in high density. However, it requires complex operations since varying species with different growing seasons and growing speeds are planted on the same land.
Current technology can only automate a few tasks, and cannot make complex decisions. To address this gap, researchers have developed a robot that can sow, prune, and harvest plants in dense vegetation growth. The robot was developed by Takuya Otani, assistant professor at Waseda University, in collaboration with Sustainergy Company and Sony CSL. The robot manages a variety of mixed plants grown in the shade of solar panels, an otherwise unutilised space. This will ultimately aid sustainable farming and carbon neutrality. Additionally, the researchers developed methods for effective seeding. They formed equal-sized balls out of soil-coated seeds from various plants. They were uniform in size and shape as a result, making it simple for the robot to scatter seeds from various plants. Additionally, a user-friendly, human-controlled manoeuvring system was created to improve the operation of the robot. The system aids in tool operation, automatic sowing, and task switching. The new robot's compact and flexible body allowed it to successfully sow, prune, and harvest in areas of dense vegetation while minimising interaction with the surroundings. In addition, compared to a simple controller, the new manoeuvring method allowed the robot to avoid obstacles 50% better while cutting down on its working time by 49%.
“It has a four-wheel mechanism that enables movement on uneven land and a robotic arm that expands and contracts to help overcome obstacles. The robot can move on slopes and avoid small steps,” Otani said. “The system also utilises a 360 degree camera to recognise and manoeuvre its surroundings. In addition, it is loaded with various farming tools — anchors (for punching holes), pruning scissors, and harvesting setups. The robot adjusts its position using the robotic arm and an orthogonal axes table that can move horizontally.”