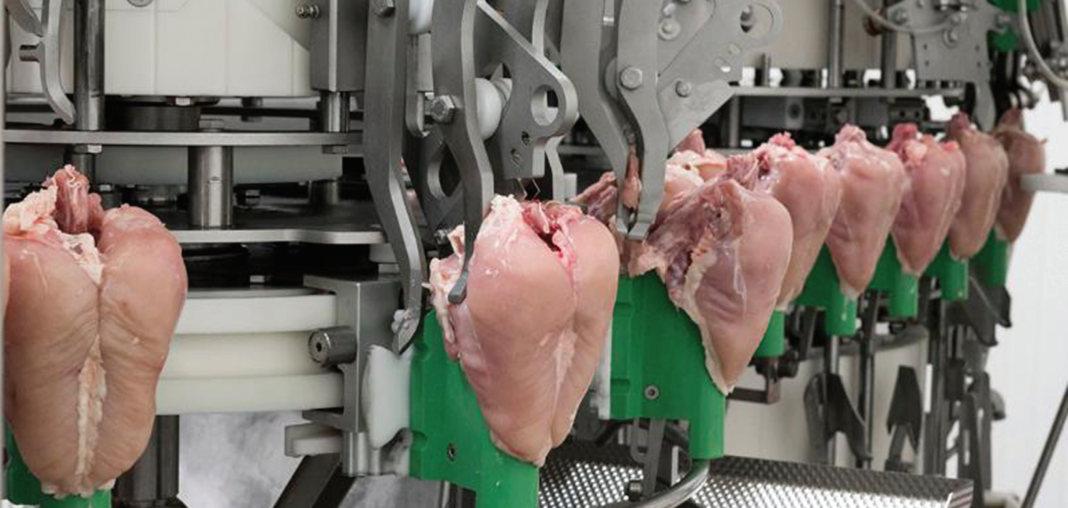
3 minute read
Benefits of automated deboning solution
Next-generation flexible and laboursaving breast deboning solution
Poultry equipment maker Meyn has introduced their new Rapid Plus Deboner M4.2 featuring the new semi-automatic loading carousel.
LABOUR AND FLUCTUATING market demands have never been so challenging in poultry processing. The effects of COVID-19 forced various processors to adopt measures like implementing social distancing and partly shift to other output products.
The pressure on poultry processors to be flexible with both their input and output has never been so apparent.Together with decreased dependency on labour and increased requirements on health and safety, processors are facing demanding times.
Meyn answers these challenges with the release of their new Meyn Rapid Plus Deboner M4.2 featuring the new semiautomatic loading carousel. This upgraded modular, configurable deboning solution takes the next step to meet the need for flexibility and saving labour. Reduces skilled labour and increases health and safety The Meyn Rapid Plus M4.2 with improved ergonomics enables processors to save up to 34 full-time equivalent (FTE) per shift, making the loading performance less dependent on the experience and skills of operators, leading to a more consistent input, which results in higher quality output.
Throughout the Rapid Plus solution, all required operators are standing on separate platforms. These platforms can be adjusted in height individually to ensure an ergonomic work position.
“The secret of the Meyn Rapid Plus is the heart and passion of the dozens of
Back meat harvesting carousel.
experts that worked on making this deboning solution the icon it is today. From engineers to manufacturing, service technicians, sales, everybody within Meyn has gone above and beyond into perfecting the entire Rapid Plus. You can really see that craftmanship when working with the Rapid. From the SAL, till the gear belt to the tiniest screw,” Marcel Verhagen, field support engineer said.
Better flexibility Meyn’s well-known Rapid series offers full flexibility. The solution can harvest all fillet and tender products automatically from both breast caps and front halves at high speed of 7,000 BPH.
Both input and output can be adapted to changes in market demands. Three preset touch-buttons enable the operator to adjust critical settings during production when product weight ranges change.
Additionally, the modular design of the Rapid Plus M4.2 provides poultry processors great flexibility to customise to the available floor space. The individual processing sections each have their own
drive and gear belt to move the product carriers.
The product carrier can be rotated in the best position for each individual processing step. Furthermore, the speed of the product carriers is varied across the system, slower at the place of manual operation and fast in automatic operation.
“Quality products produced at high speeds was our requirement. The Rapid Plus M4.2 perfectly caters to our needs,” Varun Reddy, CEO Sneha Farms, commented.
Training Meyn offers default training to achieve the
Image Credit: Meyn

SAL loading front halves in baskets.
best result with processing solutions. The Meyn Rapid Plus M4.2 training programme ensures that technicians understand the relation between input product characteristics, adjustments and the required end-product quality, for both production and maintenance.
The Rapid breast deboning concept has been globally praised by processors and their customers and proven to be very successful. All customers truly see the benefits of Meyn’s unrivalled deboning solution. Its flexibility, significant reduction of labour costs and a minimised dependency on labour (skills) and input variety make it a true deboning gamechanger. ■
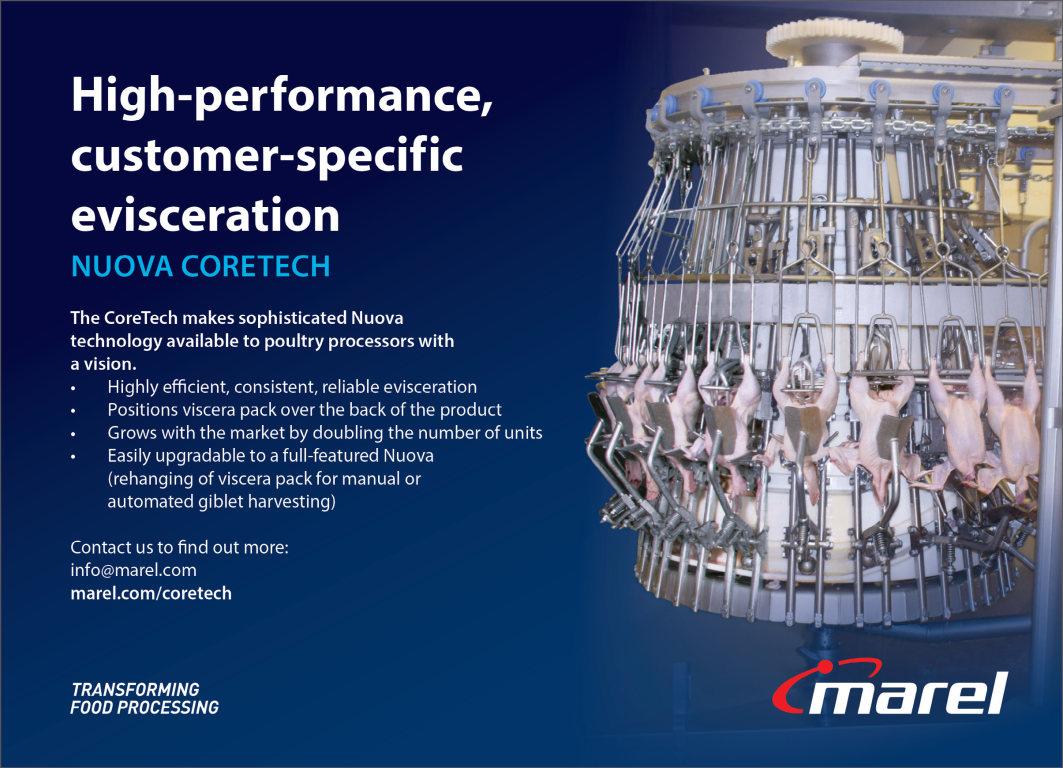