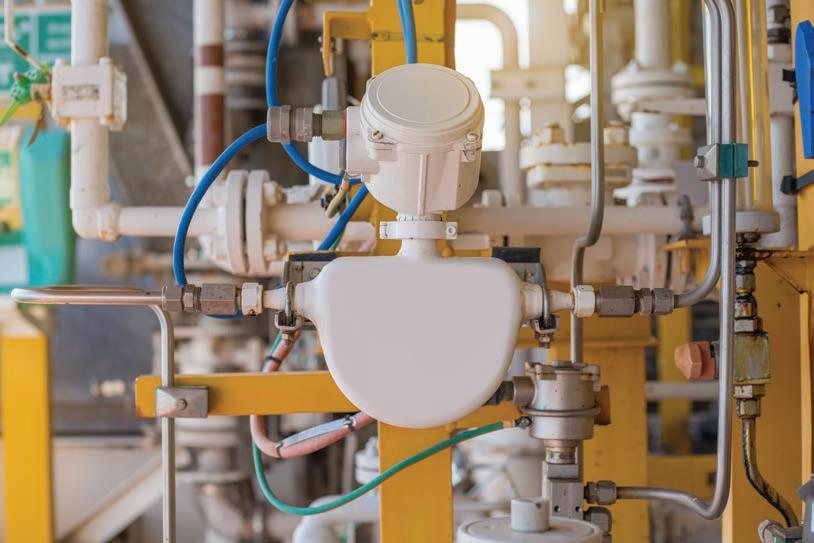
2 minute read
Flow management
UNDERSTANDING COMPLEX FLOWS TO OPTIMISE PRODUCTION
Digital technology is transforming flow management but a solid understanding of multiphase flows and fluid behaviour is essential for getting the most out of these innovation, writes Anna Pieper, multiphase flow leader, TUV SUD National Engineering Laboratory.
DIGITALISATION SHOULD DELIVER improved understanding of reservoir behaviour, but a good understanding of multiphase flows and fluid behaviours is necessary too. This is because environmental conditions can cause chemical reactions which reduce production and cause stoppages or the complete loss of the well. A focus on flow assurance is therefore necessary, using expertise and chemicals to mitigate or avoid such phenomenon
Production is often escalated by increasing the wells choke size, leading to a significantly larger drawdown at reservoir level. Over time, this may cause reservoir weakening near the well bore and the production of solids. The maximum critical flow before sand production will change over time, potentially producing solids which will cause erosion.While erosion modelling and associated standards indicate possible erosion rates, they can be optimistic. In reality, the instant the pipe is not strong enough, a burst can happen well before complete erosion of pipe wall.
If sand erosion and line pressure are not considered together, Computational Fluid Dynamic (CFD) models will be overoptimistic. CFD modelling should therefore be combined with Finite Element Analysis in
Operators should arm themselves with knowledge of multiphase flows to get the most out of oilfields.
real-time. Neither should corrosion be excluded from the analysis and should probably be a subject of study alone.
With time, a well will produce more water and for oil with long carbon chain components an emulsion will be created at the inversion point. The viscosity of the mixture will be at least 10 times greater than the expected oil viscosity for the same temperature, and this will lead to more friction and a significant decrease in oil production.
Test separation procedures do not accurately reflect a well’s behaviour under normal production conditions. An inline system that collects continuous data will help to optimise oil flowrate production and identify slugging, which can cause operational problems.
A more global or holistic review approach should therefore be used to account for all means of production optimisation. A one-stop solution provider should be considered, which can factor in all of the different impacts, cumulative effects and their contributions to the flow measurement, pipe integrity, chemical reaction and fluid behaviour. However, the most important factor is the confidence level in the validation of the technology used and the data produced. It is meaningless to deliver a confidence level number if there is not an associated uncertainty and some form of traceability that is aligned to the process and method that has been used to reference it. A more global or holistic review approach should therefore be used to account for all means of production optimisation.