
2 minute read
Cannon Artes awarded contract to build desalination plant in Egypt
CANNON ARTES, A Cannon Group company, has been awarded a turnkey contract by the Suez Oil Processing Company (SOPC) to build a desalination and demineralisation plant in Egypt.
Cannon Artes is a leading global engineering and construction company which provides tailored water and wastewater treatment plants for the oil & gas industry. The Suez Oil Processing Company (SOPC) has awarded Cannon Artes the contract as part of the modernisation of the company’s Suez refinery. The contract is valued at an estimated €28.5mn (US$31mn) and the plant is expected to come onstream by the end of 2024.
Established in 1921, the SOPC refinery, located at the entrance of the Suez Canal and near the city of Suez, has a capacity of 3mn tonnes annually or 68,000 barrels of oil per day (BOPD). In a bid to boost sustainability through reduced environmental impact and energy efficiency, SOPC secured a €200mn (US$212mn) loan from the European Bank for Reconstruction and Development (EBRD).
The plant will be fed with water from the Red Sea and will be treated to provide high-purity demineralised water to feed high-pressure steam boilers as well as low-salinity make-up water for cooling towers. It will occupy an area of 7,140 sq m (76,900 sq ft) – the size of a football stadium – with an overall capacity for 30,000 m3/day (more than 1mn cu ft) and will rely on Cannon Artes’ capabilities and experience in both desalination plants and customised solutions for refineries.
“Cannon Artes will be responsible for all stages of this huge assignment from detailed engineering design, construction and delivery of the entire water treatment infrastructure including pre-commissioning and commission, and start-up,” said Pasquale Punzo, CEO of Cannon Artes.
“The scope of this major project provides our team unique engineering challenges and calls upon our vast expertise, technology and know-how to realise this milestone facility for the Suez Oil Processing Company.”
Parker releases new catalogue for its range of Bestobell cryogenic valves
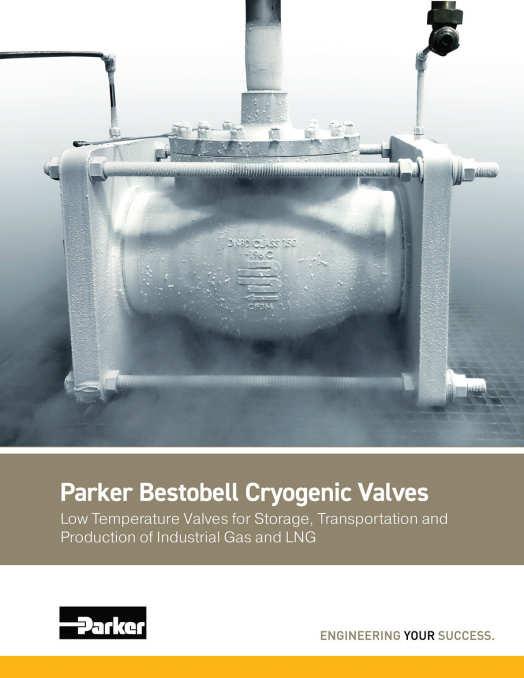
PARKER HANNIFIN, THE global leader in motion and control technologies, has launched a new comprehensive catalogue detailing its range of Bestobell high-performance cryogenic valves used in applications for the transportation, storage, and processing of ultra-low temperature liquefied gases. As a market-leading manufacturer of cryogenic valves, Parker’s 70-page catalogue offers extensive technical information on its products, materials of construction and detailed information on design conformance, certifications and approvals. Parker Bestobell valves are designed and manufactured in accordance with ASME B31.3, BS EN 1626, and BS ISO 21011 and are compliant with Pressure Equipment Directive (EU PED 2016): 2014/68/EU.)
The catalogue also benefits from detailed ordering sections for each valve type with simplified part numbering, allowing users to easily configure the product to the required specification. A complete list of spare parts has been added to the catalogue, also with simplified part numbering for customer ease. All part numbers contained in the new catalogue form part of Parker’s core range and are available to manufacture. Installation guidance has been provided for each valve type to ensure correct valve orientation. Detailed instructions can be found in the Installation, Operating and Maintenance Instructions (IOMs) for each product series, available to download from Parker’s website. Parker Bestobell’s range includes cryogenic manual and actuated globe, gate and ball valves, as well as check valves, safety and thermal relief valves, strainers, fill manifolds, and pressure regulators. Each valve has been designed to meet industry requirements to withstand temperature changes, possible expansion or contraction, and avoid deformation of its mounting.
To view the full range, download the catalogue at https://www.parker.com/content /dam/Parker-com/Literature/ Instrumentation-ProductsDivision/Catalogs/CryogenicValves-for-IndustrialGas-Applications.pdf
KPS introduces innovation to streamline high-flow fuel and chemical transport

KPS, A GLOBAL innovator in HDPE (High Density Polyethylene) piping, introduced the world’s first 6” (160/200mm) double wall conductive HDPE piping system.
This new system has been designed to combine KPS piping’s industry-leading safety and installer-friendly qualities with a high flow rate of up to 2,500 litres/minute to meet demand from applications including depots, fuel distribution, ports, mining, rail, data centres and many more.
A conductive inner layer allows static