
4 minute read
Challenges on the way to a circular economy
The adoption of digital technologies is critical for chemical companies to progress towards challenging circular economy goals, says Paige Marie Morse, industrial marketing director, Aspen Technology.
ACROSS THE CHEMICAL industry, sustainability is a hot topic for organisations, customers and investors alike. To remain competitive and relevant in the marketplace of tomorrow, companies must work to grow the “triple bottom line,” balancing the impact of their operations on people, planet and profits. ARC Advisory Group recently confirmed that most global chemical companies have sustainability initiatives in place, and they view digital technologies as critical to progressing their work, although many are struggling to adequately resource their efforts.
Surprisingly, the pandemic has only served to emphasise and renew the focus on sustainability. The collective health of communities and our planet, and the interlinked nature of climate, ecology and social crises, have all become clearer in 2020. Corporate resilience and long-term survival are common discussions these days, in boardrooms and investor events (albeit virtually at least for the foreseeable future). Sustainability is here to stay.
Meeting corporate sustainability goals
The sustainability challenge for most companies typically unfolds across two different timelines: short-term efficiency improvements to help reduce carbon emissions, water use and waste production for current operations, and longer-term efforts to develop new energy sources and products for the circular economy. Resource efficiency improvement remains an important immediate activity area for manufacturers who could see as much as a 30% reduction in energy use, according to the International Energy Agency (IEA). The IEA is urging countries to link pandemic recovery funds and energy efficiency improvements to encourage progress.
The path to a circular economy will not be an easy one for chemical producers.
Achieving a circular economy: an ambitious goal for chemical producers
Developing solutions to address the challenge of the circular economy exacts particular demands for the chemical industry. This concept takes the broad view that products and processes must be completely redesigned to cut emissions and waste, while also working to extend material use and regenerate natural systems.
The targets are ambitious, and businesses have a long way to go. In its recent report, Winning in a Circular Economy, Accenture says that of the 140 million tons of chemical products consumed in Europe each year, only nine million tons becomes available in recyclable waste streams. The report also explains that almost 70% of the material consumed is neither accessible for recovery nor recyclable since the chemicals are either dispersed in the environment or unable to be separated from the final product.
In early December 2020, BASF held its annual research press conference to present its Circular Economy Program as well as some of the challenges the company is encountering as it ramps up sustainability efforts. BASF has more than 20 circular economy projects underway currently with an aggressive target to convert 250,000 tons of recycled and waste-based raw materials into new products annually by 2025. “The path to a circular economy will require enormous effort on our part,” said BASF CEO Dr. Martin Brudermueller. “I am absolutely convinced that this is the way of the future: our success will
have a direct effect on our future profitability and competitiveness.”
Innovation strategies are fundamental for chemical companies to progress toward circular economy goals, and digital technologies are critical to accelerating this effort. Innovative supply chain solutions are already helping companies to better integrate post-consumer materials into their value chains, while advanced process control technologies are helping to lower energy use and waste generation in production processes.
Adapt your processes, stay profitable with AI-powered hybrid modelling
For longer-term product and process development, process simulations help researchers quickly screen a variety of alternatives to select the most viable and cost-effective option, whether for new polymer production or for chemical recycling processes, while also comparing the energy demand and CO2 emissions for each alternative. And these simulations are even more accurate and accessible using Aspen Hybrid Models, which combine artificial intelligence (AI) with first-principle model design and domain expertise. Engineers can now build enriched process models faster using machine learning to leverage simulation or plant data, integrating application knowledge including first principles and engineering constraints, without requiring deep process or AI expertise.
The value and importance of using AI to speed progress toward circular economy goals is highlighted by the Ellen MacArthur Foundation, which works to develop capabilities and policies to drive circular economy progress worldwide. AI is particularly valuable to aid design of circular products, enable new business models, and to optimise infrastructure. Ambitious global climate goals will require faster solutions and coordinated activities to ensure progress.
“AI technologies can be applied to three key aspects of a circular economy: design circular products, components and materials; operate circular business models; and optimise infrastructure to ensure circular flows of products and materials,” says the Ellen MacArthur Foundation, in its report Artificial Intelligence and the Circular Economy, 2019.■
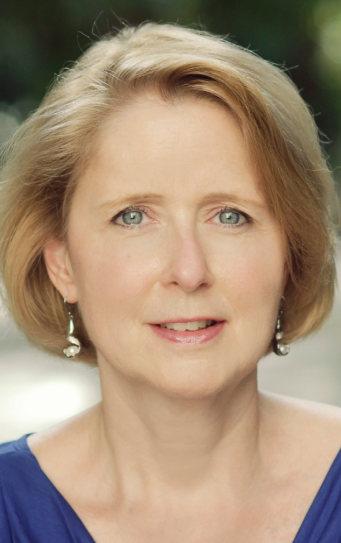
Paige Marie Morse, industrial marketing director, Aspen Technology.
Image Credit: Aspen Technology
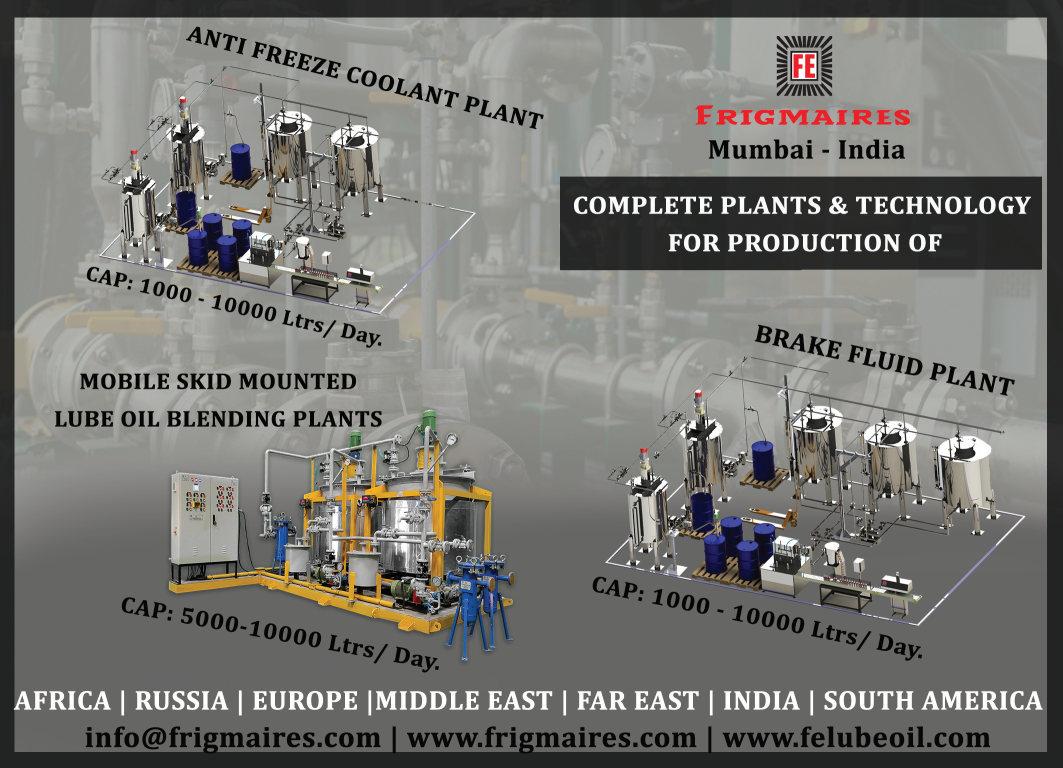