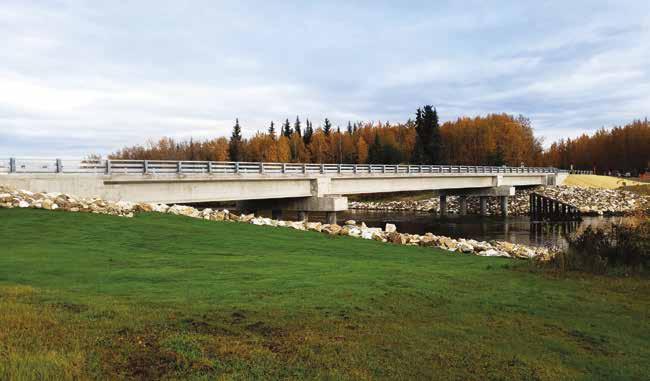
7 minute read
Rust Never Sleeps Prioritize corrosion control to lengthen an asset's lifespan
By Vanessa Orr
Just as the wood siding on a house will deteriorate if it is not painted or treated, the steel used in pipelines, buildings, machinery, and more will corrode if not protected from the elements. The most common cause is electrochemical reactions. Galvanic corrosion is when different kinds of metal are in contact with one another; electrolytic corrosion occurs most commonly when water becomes trapped between two conductors that have an electrical voltage between them, creating an electrolytic cell.
“There are four elements to a corrosion cell: anode, cathode, electrolyte, and a metallic path. The goal is to try to reduce or eliminate one of the four items that makes up that cell,” explains Cynthia Cacy, corrosion control engineering principal at Coffman Engineers. “Applying a coating, for example, removes the metal from contact with the electrolyte, or you can change the corrosion cell by introducing a cathodic protection system.”
For the latter case, Cacy gives the example of a water tank in someone’s home that has an anode screwed into the top of the tank. Because the anode is more reactive than the steel of the tank, it will corrode preferentially instead of the tank corroding.
“A cathodic protection system can be applied to any metallic structure, including pipelines, docks, offshore platforms, and tanks," she explains. “Boats have cathodic protection systems, and there are companies that specialize in designing cathodic protection systems for bridges.”
Depending on the object that needs to be protected, there are different corrosion control methods or approaches. In some cases, corrosion can even be prevented by choosing a noncorrosive material during the design stage.
“In older homes with copper piping, homeowners may experience pinhole leaks, which can become a nightmare,” says Cacy. “Newer construction uses various forms of plastic pipe that aren’t susceptible to corrosion.”
Knowing what kind of systems can help prevent corrosion is a specialty of Coffman Engineers, which provides cathodic protection system design, commissioning, monitoring, and maintenance for new and existing structures for the oil and gas industry, water/wastewater, federal, utility, and commercial markets.
“We do this as part of the design process,” says Cacy, adding that each client may also have its own specific guidelines or regulations that are required for corrosion control.
“The types of coatings recommended can depend on where you are putting the structure and how compatible the coating is with the environment it will be in,” says Cacy. “Some coatings don’t cure and adhere at really cold temperatures, so if you’re putting it on in the field, you wouldn’t use it in Alaska. For this and many other reasons, when possible, coatings are shop-applied, though there may be some touch-up work done later once the structure is in place.”
Engineering firm Michael Baker International also specifies the types of corrosion products and methods that should be used on everything from the pipelines on the North Slope to marine and dock structures at the Port of Alaska in Anchorage.
“The pipelines that we specialize in are unique compared to those in the rest of the country, so we may use some of the same coatings but for different purposes,” explains mechanical engineer David Stamp. “In the Lower 48, most pipelines are buried in the ground, which creates one set of corrosion problems. On Alaska’s North Slope, ours are above ground, which presents another set of corrosion challenges that requires a different approach to corrosion protection and coatings.”
Old Problem, Modern Solutions
Historically, pipelines were insulated with polyurethane sprayed between the sheet metal jacket and the pipe.
Shane Hadaller, President, Mericka Group
While this was at first thought to be adequate to protect it from corrosion, over time the polyurethane would fail and allow water to get through the insulation and create CUI, or corrosion under insulation.
“The modern approach is to apply fusion-bonded epoxy to the pipe before it is insulated, which provides a protective barrier when the polyurethane fails, protecting the pipe from any water that could penetrate the insulation,” says Stamp. “This is typically applied in the shop environment, as this type of epoxy requires specific temperature and cleanliness requirements that need to be controlled.”
While Stamp says that modern pipe doesn’t require much maintenance, pipes on the North Slope that have not been treated this way require a lot more effort to maintain.
“North Slope operators spend tens of millions every year removing existing polyurethane to expose corrosion,” Stamp says. “This is a huge problem for all lines built before the ‘90s.”
While operators do have to replace old lines that are too far gone, the more economical choice is to strip the pipes of old insulation and apply a coating to mitigate damage to that location. “CUI is an aggressive corrosion mechanism that can lead to pipe failure in three to five years, which is why most operators go through their inventory of lines that are susceptible, inspecting most if not all on a three- to five-year cycle,” says Stamp.
Intricate Painting
“People sometimes think that corrosion control is just painting over a surface and don’t understand what an intricate industry it is,” says Shane Hadaller, president of Mericka Group in Kenai. “You need to have very knowledgeable people who have experience working with paints and abrasives—who understand the different chemical components, the pot life, product data, mixing hazards, how to spray with PSI, and more.”
Mericka Group provides preservation and insulating services for a number of industries, such as corrosion control on fuel tanks, ships, bridges, oil platforms, military installations, and more.
“It’s not just something you spend a couple thousand dollars to hire people to do,” Hadaller adds. “It’s an expensive process that requires specialized equipment, like a $100,000 blast pot that contains sand for blasting.”
He notes that training in this field is very rigorous, and only two or three companies in Alaska, including the Mericka Group, are qualified to do QP1 and QP2, the highest painting and blasting industry standard used for asset integrity in the military.
According to Hadaller, 90 percent of corrosion control is preparation, which includes making sure that items that can corrode are thoroughly treated before they head to the field. When steel comes out of the factory, for example, it has a black sheen that needs to be blasted away to create a porous surface on which to apply corrosion treatment.
“We blast the black sheen that covers the pipe to SP7 or SP10 [surface preparation standards in mils, or thousandths of an inch], and then apply a three-coat paint process over the surface,” says Hadaller. “Each paint— the primer, mid-coat, and topcoat—will have specific specifications for mils, with a total overall thickness of 12 to 18 mils. Painting can take anywhere from eight to twenty-four hours, depending on drying time.”
While most corrosion paints are specified to have a fifteen- to twentyyear lifespan, durability depends on where the products are used. While water, salt, and wind shorten a paint’s lifespan, Hadaller says that ultraviolet sunlight is actually one of the biggest problems.
“Alaska is a very harsh environment, and most of our work is done on industrial infrastructure that is constantly being used and abused,” says Hadaller. “On a scale of one to ten, I would rate Alaska an eight. A ten would be something like a Navy ship, or tanks in the middle of an Arizona desert in 110°F temperatures.”
For this reason, he adds, the US Navy has one of the biggest corrosion programs in the world, spending $3 billion each year to protect its ships, which are repainted every five years.
While calculations can help forecast when corrosion might occur, many factors affect the rate, including the environment, whether a coating was applied in the field or the shop, and whether there is already something wrong with the structure, such as a bad weld. There are industry, state, and federal regulations that provide guidance and regulation, including the Association for Materials Protection and Performance, the Alaska Department of Environmental Conservation, and the Pipeline and Hazardous Materials Safety Administration, which provides federal oversight for the oil and gas industry.
On the Horizon
Because controlling corrosion is a constant battle, companies are always trying to find new methods, products, and technologies to make identifying and mitigating corrosion easier.
“Coatings are improving every day, as improved chemistry and a better understanding of corrosion problems enables companies to make better coatings for specific applications,” says Stamp. “Many of the advances made have also been focused on the inspection technology side, helping operators find and address corrosion.”
While operators have historically used X-ray technology to see through pipes to determine where corrosion has started—a process that is done by hand—robotic "crawlers" are now being used to search for problem areas.
“Inspectors used to have to set up an X-ray source and detector every foot or two along the pipeline, which was a time-consuming and expensive process,” says Stamp. “This led to the development of robotic crawlers that move along the top of the pipe, taking X-rays as they go. In some cases, you can actually see where the insulation has gotten wet but not yet corroded the pipe, which allows operators to prioritize that area for additional inspection or to remove the insulation before the pipe is damaged.”
Monitoring has also been simplified through remote data collection capabilities that allow companies like Coffman Engineers to make sure that cathodic protection systems remain operational. “Remote monitoring has really been embraced in Alaska because, instead of investing a lot of time to travel to remote cathodic protection sites, you can review data more frequently from data transmitted remotely,” says Cacy.
Companies have also become more proactive in preventing corrosion by incorporating corrosion mitigation methods into new construction designs. “If you are constructing a new structure or pipeline, it is much more cost effective to add cathodic protection at that time instead of pushing it to the back burner and worrying about it later,” says Cacy. “It’s like spending money now to paint a house or waiting several years to buy new siding; investing in corrosion control early can make an asset’s lifespan much longer.”