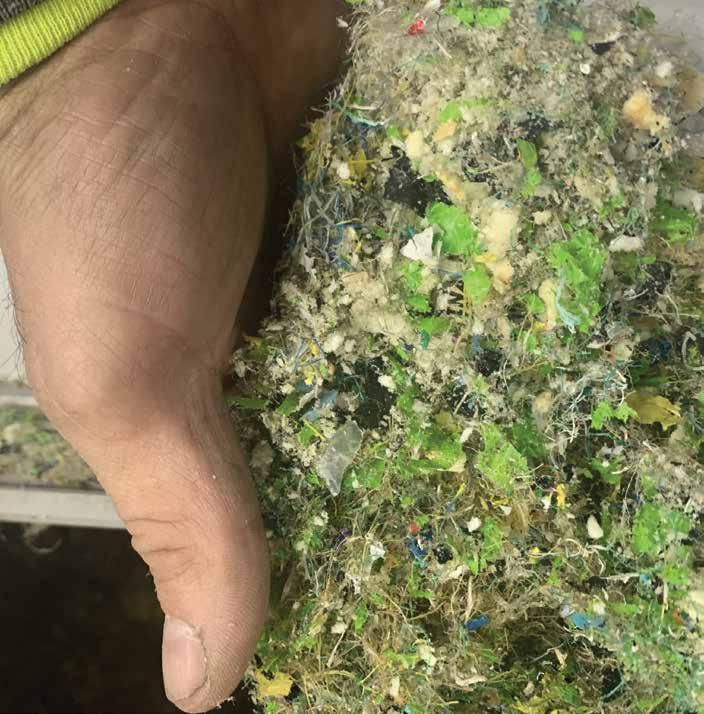
8 minute read
Mobile Plastic Recycling
A portable processor to repurpose ocean waste
By Vanessa Orr
While many people were trying to find ways to stay busy during the COVID-19 pandemic, Patrick Simpson, owner of PKS Consulting, was studying ways to save the environment. He was investigating the issue of marine debris—and plastic in particular—when he decided to see if he could find a solution to help keep Alaska’s coastline clean.
“I spent my time combing through Google Scholar articles and searching scientific journals and peer-reviewed science publications to figure out how to put my arms around the problem,” he recalls. “When looking at the state of current technology, I discovered three themes: assessment, collection, and utilization of plastic ocean waste.”
Simpson put together funding proposals focused on the collection and utilization aspects. Some envisioned the use of heavy-lift drone aircraft that could carry up to 1,000 pounds of waste off a remote beach. The idea that gained traction, though, is a mobile system to recycle ocean waste into plastic lumber.
In 2019, Simpson’s mobile plastic processing system earned funding from the US Environmental Protection Agency’s Small Business Innovation Research program, and Simpson also recently received funding through the US Department of Agriculture to use the same type of technology to recycle a different set of plastics.
The recycling system, housed in a 53-foot trailer, had its initial pilot demonstration last fall in Palmer. The shakedown tour goes to Seward and Soldotna this spring. Plastic waste fits through a slot in the side of the trailer, gets shredded into pellets, and is pressed into a flow molding machine. The output is a material shaped like boards or other construction products.
Because the unit is mobile, it can be used anywhere, saving communities the cost of the typical hub-and-spoke approach, in which they are required to ship their waste to another location for processing. This is especially important for rural Alaska communities, which can simply stockpile their waste at a single location until the processing system arrives.
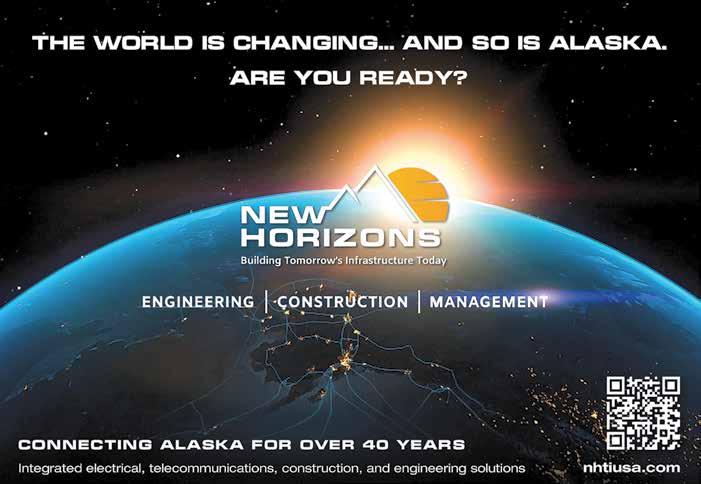
“This concept was really emotionally driven,” says Simpson, a fourthgeneration Alaskan who grew up in Cordova. “My father and brother are commercial fishermen, and though I get seasick on the water, I’ve spent a lot of time on these beaches. Seeing them littered with plastic and Styrofoam really concerns me because heavy storm tides break it up into smaller pieces that become microplastics. These make their way into our food supply, so we need to get it off the beach when it is still in macro plastic form.”
Simpson adds that Veronica Padula’s PhD thesis for the UAF School of Fisheries, in which she performed necropsies on every species of bird in the Bering Sea, added even more weight to the issue. “Without exception, she found plastic in every species, including some in the birds’ muscles where it metabolized,” Simpson explains. “Some plastic was found in bird gullets, and because it doesn’t digest, they were starving to death. Her work in Alaska is telling us that the problem is already here and that we need to start solving it now.”
From Design to Destination
After designing the mobile recycling unit, which Simpson is marketing through PKS Consulting subsidiary Alaska Plastics Recovery, he took his idea to Paul Vanderpool, president of American Cierra Plastics in Auburn, New York, to create the prototype.
“Paul has forgotten more about plastics than I’ll ever know,” says Simpson. “I traveled to New York three times, and he not only worked with me on the design but also trained me on the equipment and has offered continuous guidance since it arrived in Alaska.”
The company helped Simpson develop the prototype affordably, building it out of used items instead of new materials. Built brand new, a mobile recycling unit could run between $1 million and $2 million; working with American Cierra Plastics, Simpson was able to come in at roughly $400,000.
“Unfortunately, that didn’t include shipping,” says Simpson, noting he was quoted $21,000 to move the machine from New York to Alaska, but that increased to $29,000—an 8 percent increase in the fuel surcharge—when it shipped less than thirty days later.
Vanderpool’s company had manufactured a product focused on ocean waste before, but he says Simpson brought a concept for a different type of unit.
“Patrick is a guy with great vision and a lot of heart,” says Vanderpool. “When he gave me a call and said that he wanted to work together and that he had a grant but a limited budget, I wanted to see what we could do. We’d already done an ocean waste project with someone else, but it wasn’t mobile. I knew we could build what he wanted.”
Rise Above
Since 1976, LBB has represented individuals, businesses, and communities in every region of Alaska. LBB’s Real Estate Team is a group of seasoned attorneys who know how to achieve their clients’ complex commercial real estate goals effectively and efficiently.
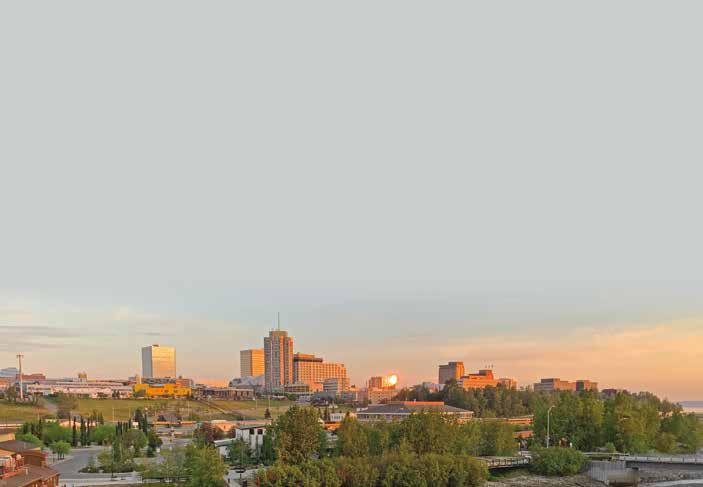
Fitting all parts of the plastics processor, from shredder to extruder, inside a 53foot container means the unit can move to communities where waste is collected, starting with Palmer.
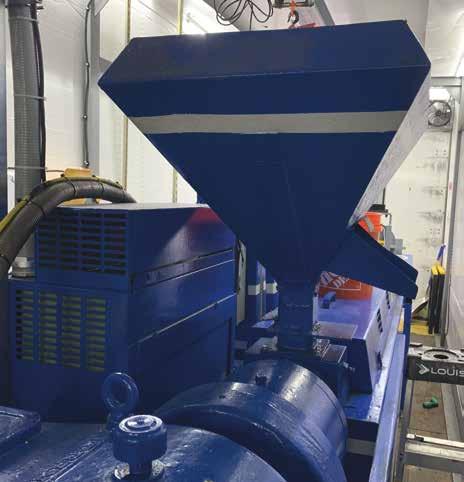
PKS Consulting, Inc.

American Cierra Plastics previously worked on a recycling system that could go into shipping containers and be dropped out of a cargo plane, but Vanderpool says that it was much smaller. “Not a whole factory like Patrick had in mind,” he adds.
Just One Word: Plastics
American Cierra Plastics has a long history of expertise, going back more than a century to the first synthetic plastic. Originally known as Auburn Button Works, the company made Bakelite buttons for US Cavalry uniforms before evolving to make Bakelite distributor caps for cars.
“Auburn Button Works also made plexiglass hula hoops and phonograph records before vinyl,” says Vanderpool. The button manufacturer changed its name to Auburn Plastics in the ‘50s.
Vanderpool’s father, a chemist, worked at Auburn, and Vanderpool followed him into the field, landing an internship with Auburn Plastics. “I grew up spending my summers in the factory in the laboratory, making plastic resins and compounds and working on equipment to keep it running,” he says. “I fell in love with it.”
After starting his own plastics company, in 1975 Vanderpool’s father returned and they bought Auburn Plastics, shifting its focus from auto parts manufacturing to the recycling industry.
“His theory was simple: why buy prime virgin material when you can make things out of recycled materials?” says Vanderpool. “We bought post-industrial scrap from other manufacturers and recycled it to supply customers with high-quality products made out of recycled scrap.”
Vanderpool started American Cierra Plastics to continue to service companies that had more waste than they could handle.
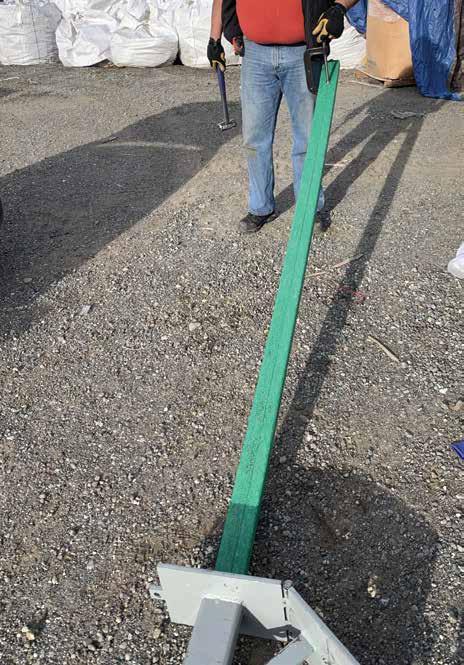
“We got catapulted into this industry through people needing our help,” says Vanderpool. “We realized that there were not enough plastic recycling manufacturers in the United States and Canada to handle the large amount of waste collected that is not being utilized, so we decided to take our vast knowledge and understanding that has been beneficial to so many of our customers and put it to good use ourselves.”
American Cierra Plastics now provides composite products for landscaping, marine, construction, industrial, mining, and fencing use. It also makes products from textile waste. The company also supplies machinery to other companies making products from waste: one turns plastic pipe waste into pallets, and another provides jobs for people with disabilities to make park benches and tables.
In addition to working with Simpson to create the mobile processing system, Vanderpool also provided guidance on how to use the recycled material.
“Even as simple as it may seem, there’s always a catch—it’s a bit of a learning process to understand the do’s and don’ts of this type of machinery,” he says. “You don’t want trash in, trash out.”
Vanderpool notes that plastic additives or water can cause issues with the end product.
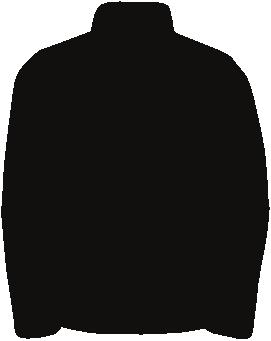

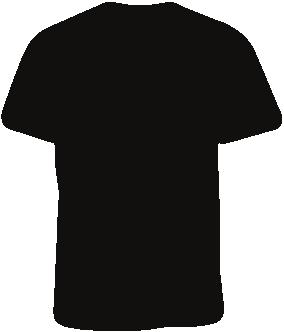
“It was a pleasure working with Patrick—he’s a quick learner and he’s been a great student,” Vanderpool continues. “The fun thing about it is that he had an idea, he followed through with it, and now he’s out there doing it. He’s taking waste materials as they are, and he’s repurposing them as we all hoped could happen.”
Litter into Lumber
Simpson’s design and Vanderpool’s technical know-how created a machine that can be moved around Alaska to recycle ocean plastics into recycled plastic lumber. While Alaska Plastics Recovery is currently making lumber in three different sizes, Simpson says products can be customized 100 different ways.
The cost of the recycled plastic lumber is higher than wood—roughly two to three times more expensive than the market price of wood—but it has a much longer lifespan, saving users money over time. The recycled product doesn’t splinter or rot and is easy to maintain, compared to wood, which would need to be replaced three to four times during the recycled product’s 25to 50-year lifespan.
“Right now, we’re working on finding a market for the recycled lumber that we’ll be making when we fire the machine up this spring,” says Simpson. “We need to do a lot of consumer education to show them what a bargain it actually is.”
Simpson has been meeting with municipal parks departments, contractors, architects, and more to share this message and to promote plastic lumber’s use as trim for gardens and hedges, for boardwalks, or for railings. In February, Mid-Valley Recycling in Big Lake awarded $5,000 for PKS Consulting to make picnic tables from its Grizzly Wood product.
“We also check a lot of boxes when architects and designers are focusing on LEED certification for buildings,” says Simpson, who adds that his products are currently undergoing third-party testing to make sure that they meet required standards.
While he has many ideas of how the recycled lumber can be utilized, he is also looking to the market to help decide what other uses could be beneficial. “For example, I saw a mold for a park bench out of Wilmington, Delaware, that I liked very much, but the quote for the mold was $15,000— you’d have to sell a lot of park benches,” Simpson says with a laugh.
The choice of molds depends on what the market calls for. “If people have ideas, I hope they reach out to me,” Simpson says. “There could be some really cool applications out there, and I just don’t know about them yet.”
As more people learn about his invention—and see it working in pilot projects throughout the state—Simpson hopes that he can make inroads into what is an ever-evolving industry.
“Plastic recycling is becoming something that more companies are investing in, and the marketplace is really in flux right now—there are a lot of moving parts,” he explains. “I went to the largest recycling show in the country held in Washington, DC, and they were focused on there not being enough capacity to feed what’s being built. There was such a large surge of recycling centers at one time that they were starving for plastics to come in.”
The market niche Simpson sees for Alaska Plastics Recovery is smaller communities that have more waste than they can handle. “Right now, a lot of municipalities are also outsourcing their recycling or using a hub-and-spoke model instead of having a company come to them to do distributed recycling, which is my model,” he adds. “It might make sense to have microhubs in areas like Anchorage that have a significant population, which I’m also open to doing.”
While teaching people that ocean plastic can be seen as a resource— and not as trash—may take some convincing, the use of the mobile plastic recycling unit could ultimately make a positive difference in the health of Alaska’s ocean environment.
