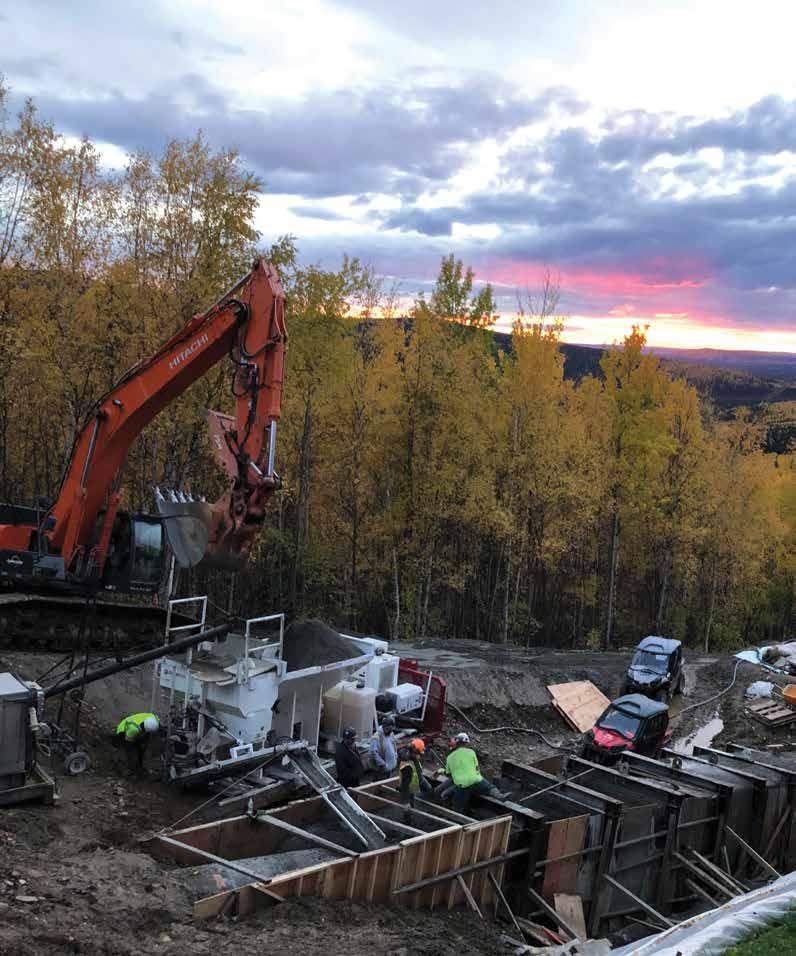
13 minute read
OIL & GAS
45 Years of TAPS
800 miles between Alaska as it was and Alaska today
By Tara O’Hanley
Ahtna, Inc. F orty-five years after the first tanker left Valdez carrying North Slope oil to market, many of today’s worries echo past headlines. Inflation was a major concern. Energy costs were skyrocketing. New construction was stalled due to increasing costs, a shortage of available labor, and constraints on the global supply chain. Far-off wars were influencing global energy commodity markets. And, like today, drilling for oil in the Arctic was offered as a solution—albeit today it comes with heightened concerns for the environment.
Into this political landscape, the Trans Alaska Pipeline System (TAPS) was born. Three years of construction—and nine years of political wrangling—culminated with the first oil entering the pipe at 10:06 a.m. on Monday, June 20, 1977. Workers and civilians put their ears to the 48-inchdiameter steel casing to listen to the crude flowing through the 800-mile-long pipe. Six weeks later, on August 1, the tanker ARCO Juneau carried away the first load. Alaska would never be the same.
For this quinquadragennial, celebrations at Alyeska Pipeline Service Company are largely employee-focused, with outward observances held in reserve for the golden jubilee in 2027. The public-facing anniversary takes the form of “Memories and Milestones,” a retrospective on Alyeska’s website, alyeska-pipe.com, with historic photos, news articles, and reminiscences.
“While we celebrate all of the things that the TAPS designers and those who constructed the pipeline anticipated,” says Chief Communications Officer Michelle Egan, “those who’ve come since have continued to do that. The engineering marvel is this constant renewal with the workforce that we have and the minds that we have working on solutions.”
Ahtna, Inc.

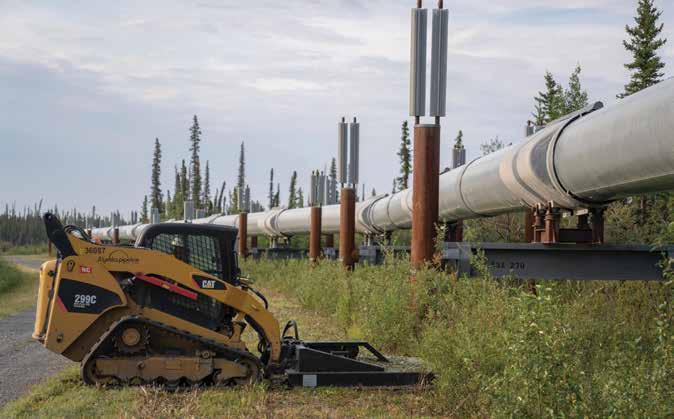
Announcements of the discovery of oil at Prudhoe Bay State Well No. 1 in 1968 prompted the most experienced petroleum professionals in the world to team up to bring the oil to market.
Up to then, each company involved in the construction of TAPS had been doing its own studies, such as whether it was even possible to build a pipeline, how much it would cost, and how long it might take to build it. In the fall of 1968, just months after the discovery, each of the owners began assembling all this technical information into an intercompany task force to lead a feasibility study. The task force later incorporated to become Alyeska Pipeline Service Company, the nonprofit contractor that operates TAPS to this day on behalf of ConocoPhillips, ExxonMobil, and Hilcorp.
The task force estimated a construction cost of $900 million and anticipated completion around 1970. Neither estimate was close. If only the real world were as simple as the controlled environment where engineers make their plans. TAPS found itself at the crosshairs of one social, political, and environmental issue after another—even in areas which had necessitated little more than a rubber stamp for projects before it. Congress wouldn’t cut through the Gordian Knot of land claims and environmental challenges until 1973, passing legislation to restrict federal and state regulation of TAPS construction—less than a month after OPEC announced an oil embargo, not too coincidentally.
Land rights weren’t the only impediment to progress along the pipeline’s route. Laborers were looking to expand worker protections, as well.
At a time when construction was slumping across the United States, workers, unions, and contractors were eager for a bite of the massive project. In April 1974, Alyeska arrived at a broad project labor agreement that has been credited as a driving factor in the on-time completion of the project, with labor costs that remained within estimates. In exchange for a 100 percent union workforce, the AFL-CIO’s Building and Construction Trades Department (now known as North America’s Building Trades Unions) and the heads of sixteen “As we continue to grow in understanding every day about the risks associated with the operation, we’ve set up our automation, our pressure protection system, and other safety systems to keep us operating and to keep our folks safe.”

Thomas Marchesani, Vice President of Risk and Engineering, Alyeska Pipeline Service Company
Innovative, cost effective housing with all the comforts of home

Air Systems Deliver Fresh Air to Each Room!
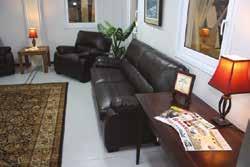
• Arctic tough • Turn-key set up • Rapid mobilization • Custom built • Easy to relocate Let us build your next modular facility
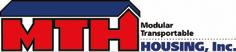
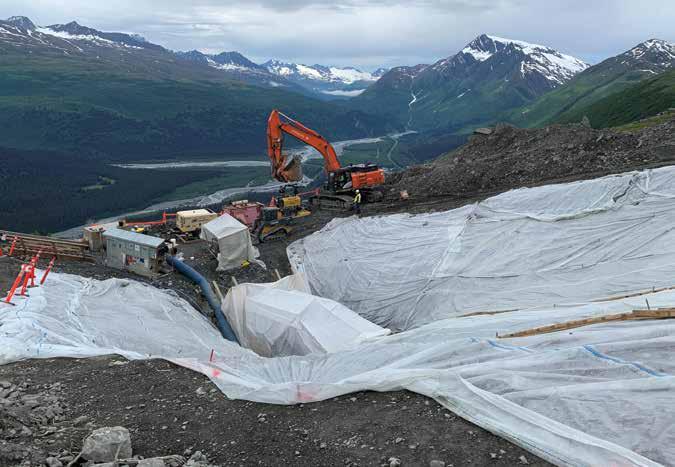
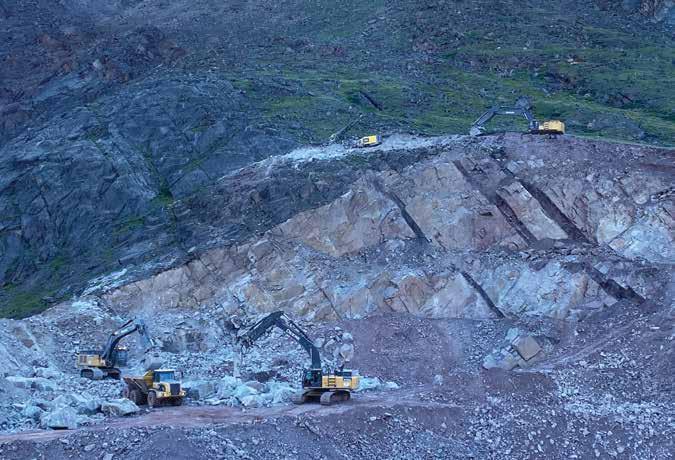
traditional craft unions agreed not to strike, picket, or stop work for the duration of the project. This kind of treaty between labor and management had been used previously by the federal government for the Apollo program of the ‘60s and by the contractor that built Disney World in Florida—but at that point it was considered somewhat unique for an owner to make an agreement of this sort.
Alyeska’s manager of labor relations during construction of the pipeline, Gayle Sheridan, considered this pact to be the “most effective and enforceable agreement ever arrived at” and credited to it the fact that the project never experienced system-wide stoppages, and any skirmishes were extinguished within a few days.
Continuous Flow
A handful of Alyeska Pipeline workers are still around from 1977. Egan notes that audit manager Mel Jessee is one 45-year veteran of the company, and there are a couple of others.
Amid that continuity, though, some things inevitably change. “There are a bunch of things that we’ve learned about operating it that they didn’t really need to think about,” says Thomas Marchesani, Alyeska’s vice president of risk and engineering, of his predecessors. For example, “If you’re running a million barrels a day, cooling as you move down the line is irrelevant.”
TAPS is no longer pumping a million barrels per day. Throughput is half of that, with ramifications for operations all along the pipe. The lower volume flows more slowly, taking almost three weeks to travel from Prudhoe Bay to Valdez, which used to be a three-day trip. Oil used to arrive at the terminal at 85°F, melting snow off of storage tanks. Alyeska has since added heaters, burning diesel fuel to keep the crude oil above 35°F in winter, or else the mixedin water will freeze.
“The crossover point was really in the 700,000 to 600,000-ish [barrel per day] range, where we started to have to add heat to the line to manage wax and ice risk,” Marchesani explains. “We spent a bunch of time a few years ago taking a really hard look at the design boundaries of operation for the pipeline and how low could we go. With some minor tweaks we figured we could get down below 300,000 [barrels] per
Michelle Egan Chief Communications Officer Alyeska Pipeline Service Company

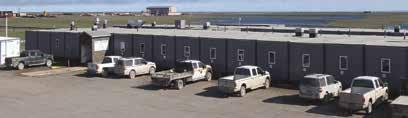
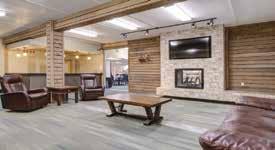
Your Remote Housing Provider
Remote Living Facilities
Competitive Rates
Large Remote Camp Inventory
Turn-key Camp Operations
Quality Gourmet Dining
Rapid Deployment OfficesandOtherRemoteFacilities
Eagle Lodge in Deadhorse
Walk-ins or Contracted Accommodations
Gourmet Dining and Loaded Snack Bar
TelevisionandHigh-SpeedWifi
All Single Occupancy Suites www.afognakleasing.com 907-222-9500
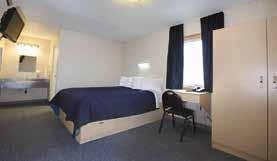
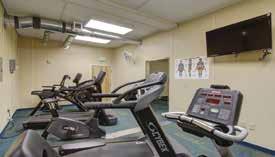
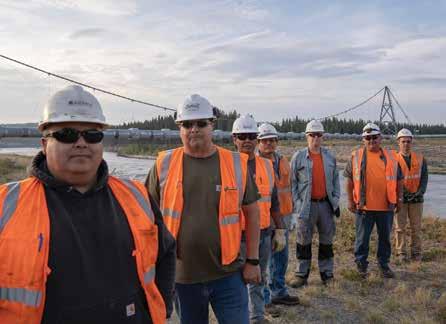
day.” Throughput is still well above that minimum, and projections for the next decade anticipate no significant decline.
While the steel pipe is still the same, equipment along the 800-mile line has been upgraded through the years. In addition to heaters, Alyeska Pipeline replaced jet-turbine pumps with electric drives, and the number of sensors has increased tenfold, aided by wireless connections. Each of the sixtytwo remote gate valves has instruments to monitor temperature, pressure, and flow. “As we continue to grow in understanding every day about the risks associated with the operation, we’ve set up our automation, our pressure protection system, and other safety systems to keep us operating and to keep our folks safe,” Marchesani says.
Declaration of Friendship
This summer, Alyeska Pipeline’s Interim President Danika Yeager and other Alyeska leadership gathered at the Glennallen Response Base for an anniversary luncheon with officials from Ahtna, Incorporated. Nearly onequarter of the pipeline right-of-way crosses Ahtna traditional lands in the Copper River valley, and Ahtna has been among Alyeska’s most important partners, going all the way back to construction and startup.
In July 1974, Alyeska and Ahtna entered a partnership that led to the creation of Ahtna Construction & Primary Products Corporation (AC&PPC). AC&PPC laid the first section of pipe on March 27, 1975, at Tonsina River.
Today, AC&PPC performs work all along the 800 miles of TAPS, from civil construction to pipeline maintenance to emergency preparedness and
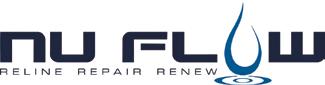
INDUSTRIAL RESIDENTIAL COMMERCIAL
Fix Your Pipes from the Inside - Half the Cost of Pipe Replacement!INDUSTRIAL RESIDENTIAL COMMERCIAL
BEFORE AFTER Fix Your Pipes from the Inside
Half the Cost of Pipe Replacement!
AFTER BEFORE AFTER
6” Fire Water Supply Line Before and After Epoxy Coated Epoxy Coatings Epoxy Line 300’ of 4” Cast Iron Drain Lines Structural Liners
6” Cast Iron Epoxy Liner Why Replace? Our patented technology creates a new pipe within the original pipe restoring it to a “better than new” condition for a long-term Epoxy Pipe Lined 2" - 10" Cast Iron Drain Lines solution—without digging or tearing up walls, ceilings or floors. 50-year life expectancy. Certified Green Technologies, NSF 61 certified.Bremerton, WA Used in host pipes consisting of copper, clay, concrete metal, iron, clay, concrete, metal, iron, steel, PVC, and fiberglass. Pipe diameter applications range from 1/2” to 12”. Applicable use in the following piping systems, in any infrastructure, in every market sector:
3” Water Main Before & After Epoxy Coated 6” Cast Iron Drain Line Before & After Epoxy Lined
Why Replace? Our patented technology creates a new pipe within the original pipe restoring it to a “better than new” condition for a long-term solution—without digging or tearing up walls, ceilings or fl oors. 50-year life expectancy. Certifi ed Green Technologies, NSF 61 certifi ed. • Potable hot & cold drinking water lines • Potable water distribution mains • Industrial pressure applications • Compressed air systems • Process pipes • Fire suppression sprinkler systems • Hydronic systems (air & water) • Heating and cooling lines • Natural gas & petroleum product lines • Electrical conduit • Collection, Hold & Transfer (CHT) systems in maritime vessels • Storm drains • Rain & roof leaders • Drain & sewer lines • Vertical & vent stacks • Industrial pressure applications • Repair broken pipes
Nu Flow Alaska www.nufl owalaska.com (907)677-2145 fax(907)677-2566 info@nufl owalaska.com Nu Flow AK (Washington state) www.nufl owak.com (425)256-4386 fax(425)749-5669 info@nufl owak.com Nu Flow South Pacifi c www.nufl owsp.com (808)426-7924 fax(808)518-4555 info@nufl owsp.com
Used in host pipes consisting of copper, clay, concrete metal, iron, clay, concrete, metal, iron, steel, PVC, and fi berglass. Pipe diameter applications range from 1/2” to 12”. Applicable use in the following piping systems, in any infrastructure, in every market sector: • Potable hot & cold drinking water lines • Potable water distribution mains • Industrial pressure applications • Compressed air systems • Process pipes • Fire suppression sprinkler systems • Hydronic systems (air & water) • Heating and cooling lines • Natural gas & petroleum product lines • Electrical conduit • Collection, Hold & Transfer (CHT) systems in maritime vessels • Storm drains • Rain & roof leaders • Drain & sewer lines • Vertical & vent stacks • Industrial pressure applications • Repair broken pipes
Nu Flow AK (Washington state) www.nuflowak.com (425)256-4386 info@nuflowak.com Nu Flow South Pacific www.nuflowsp.com (808)426-7924 info@nuflowsp.com
oil spill response. Specialized work has included supporting mainline integrity investigations, high-point vent investigations, and cathodic protection improvements. In 2021, AC&PPC was awarded a new Alyeska contract to perform line-wide survey services.
The significance of Ahtna’s role is honored with a special signing of a renewed declaration of friendship any time there is a major leadership transition at either company. Several generations of Ahtna shareholders have been able to stay in the Ahtna region for careers, receive training or scholarships, and follow in the footsteps of previous generations that decided to work on TAPS.
Pipeline Perspective
In 2022 dollars, the $8 billion construction cost of TAPS equates to just over $39 billion. That’s the same ballpark as the most recent price estimates for building a liquified natural gas pipeline from Prudhoe Bay to Nikiski.
TAPS moved its first billion barrels of crude oil within three years of startup in 1977. At that rate, it would’ve moved 15 billion by this anniversary— except that the early throughput ramped up during the ‘80s. In 1988, the pipeline averaged more than 2 million barrels per day, and the total volume surpassed 18 billion barrels in 2019. However, that year saw throughput dip below half-a-million barrels per day for the first time, and it’s hovered at that level ever since. The last three years have added only half-a-billion barrels to the lifetime total.
Perhaps a more encouraging perspective concerns how much oil remains in reserve on the North Slope. These figures are in the billions, as well.
When the field was discovered, total held reserves in Prudhoe Bay were initially estimated at approximately 2 billion barrels, which itself far exceeded any other oil discoveries to that point. To date, more than 17 billion barrels have already been extracted from Prudhoe Bay and its smaller neighbors, and tens of billions more barrels are known or suspected to remain underground.
Even with 18 billion barrels of production, the US Geological Survey estimates that Alaska may still hold 27 percent of global unexplored reserves. With 75 percent of the exploration portfolio undrilled, significant opportunities for oil and gas development on the North Slope are alive today. In an atmosphere of heightened global tensions, TAPS’ best days may not yet be in the past.
How many more anniversaries are ahead? It has already functioned 50 percent longer than its original thirty-year design lifetime. “It wasn’t really anticipated that TAPS would be operating for forty-five years, but we are, and we’re doing quite well, thank you very much,” says Egan.
Low throughput is not expected to be a serious problem for at least another decade. Marchesani says life-extending upgrades are on the drawing board, but it’s very early in that process. Those systemwide facility upgrades could extend TAPS’ lifespan to nearly a century.
At forty-five years old, TAPS is comfortably middle-aged.
CAMA’I PAD
RESERVE YOUR SPACE TODAY!
• Minimized travel for companies operating west of Deadhorse • 15+ acres available for sublease • Available for short-term or long-term (up to 15 years) subleases • Housing available onsite • Great for storage of materials, equipment, and drill rigs • Conveniently located along Tarn Road • Approximately 5 miles southeast of the Mustang Pad • Only 16 miles west from Kuparuk Operations Center www.afognakleasing.com (907) 222-9500
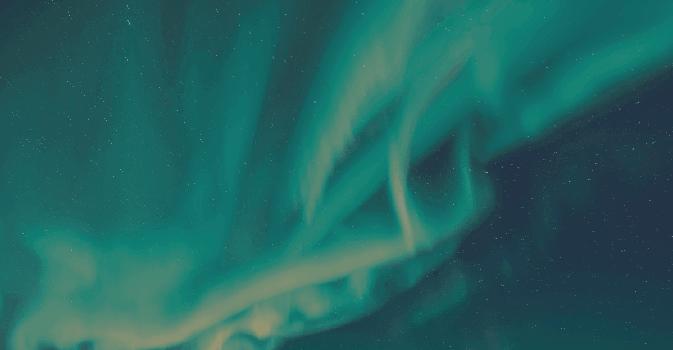

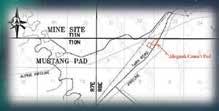
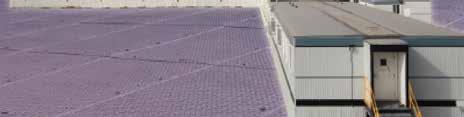

