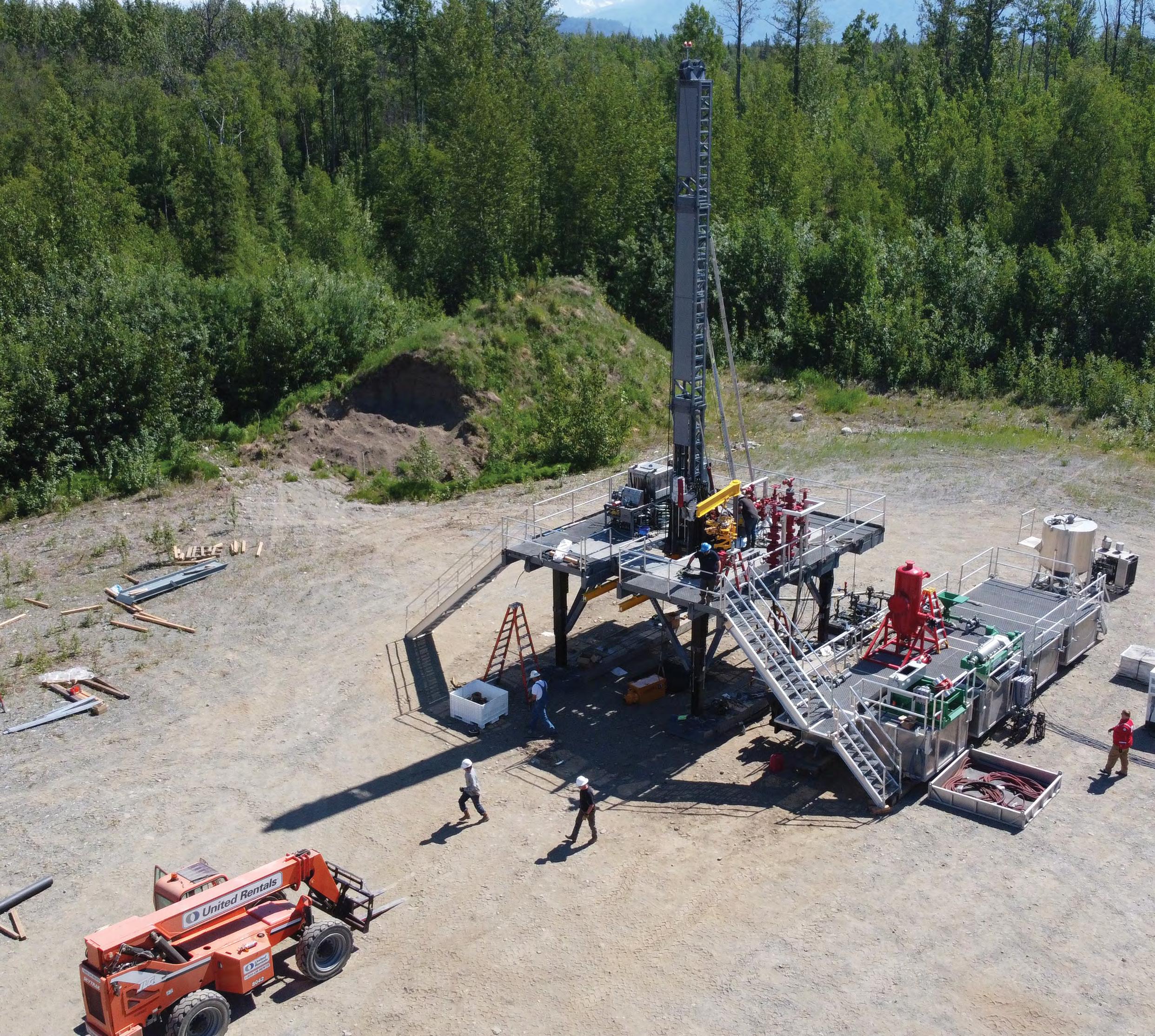
9 minute read
OIL & GAS
Effectual Drilling
Smaller rig promises bigger results
By Scott Rhode
Sometimes, a smaller tool is the right tool for the job. That’s the philosophy behind new technology that Anchorage-based Alaska Drilling and Completions (ADC) is ready to deploy. Co-owners David Ross and Tim Flynn call their novel approach “effectual drilling.” As Flynn, the chief operating officer, defines the term, “We are able to look at how your market is and how we can fit in there to make your market better.” How ADC fits is with a scaled-down rig that promises cost savings and, therefore, more exploration for oil and gas.
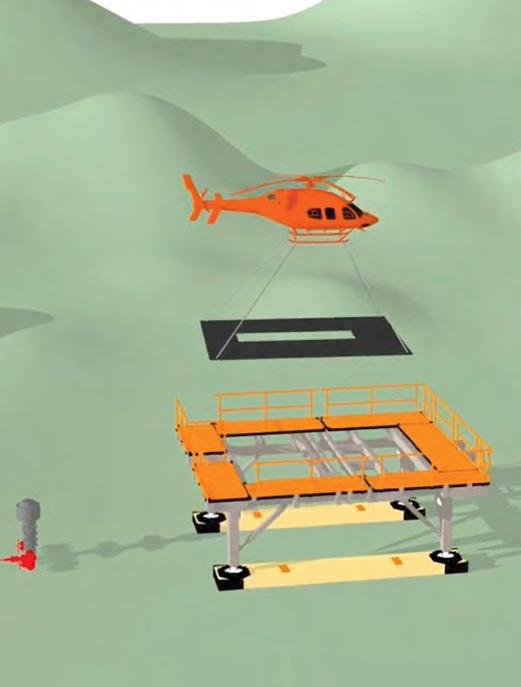
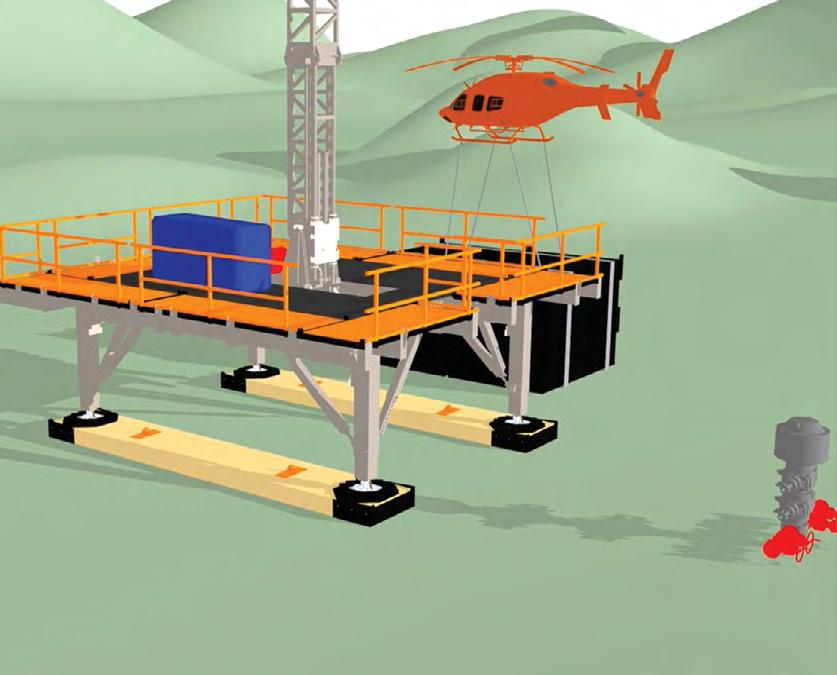
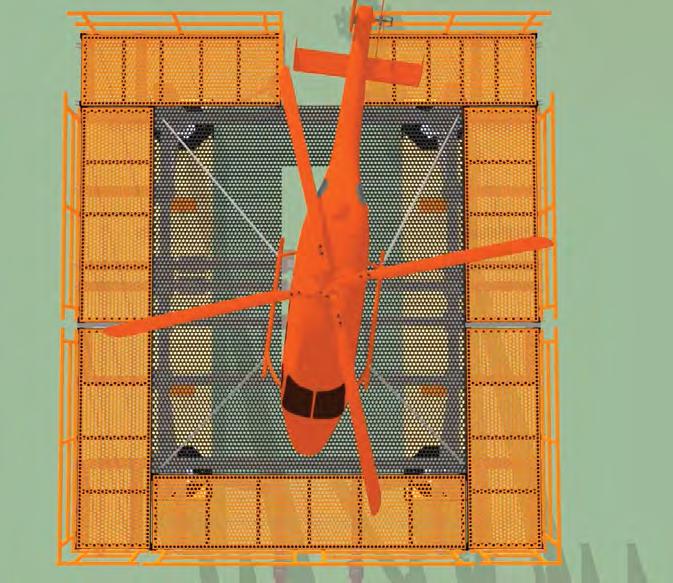
Utilizing relatively smalll pieces allows for the transportation of an entire drill rig and camp in about fifty flights.
Alaska Drilling and Completions
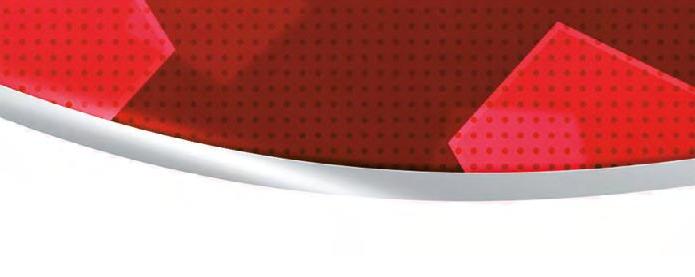
Flynn and Ross both have nearly thirty years of experience as petroleum engineers. Since teaming up to form ADC, they’ve drilled for ConocoPhillips, Repsol, “all major oil lease holders,” says Flynn. The pair have worked in engineering, consulting, and project management, and Ross, ADC’s president, says their all-around service is especially useful for smaller clients who want to monetize a lease.
Over the past decade, Flynn says, they noticed that drilling test wells was getting too expensive. “Usually,” he explains, “the geologists are standing there, right at the end, going ‘We should’ve drilled over there. Can we get a deal on the next one?’ We go, ‘It’s $50 million to go out there again.’ It’s not like it gets any cheaper. In fact, it gets more and more expensive because of the permitting, the logistics… I’ll mention permitting again.”
For an answer, ADC drew inspiration from Australia and New Zealand, where exploration rigs are hauled by helicopter. But instead of using a heavy Sikorsky Skycrane, ADC envisioned equipment that could be transported by more common aircraft—or even overland by all-terrain vehicles. Ross says, “It just kind of came to Tim and my mind because of where we’ve been and the projects we’ve been involved with.” The result is an innovative combination of proven technologies. As Flynn puts it, “It’s not a new movie, it’s a new act in the movie.”
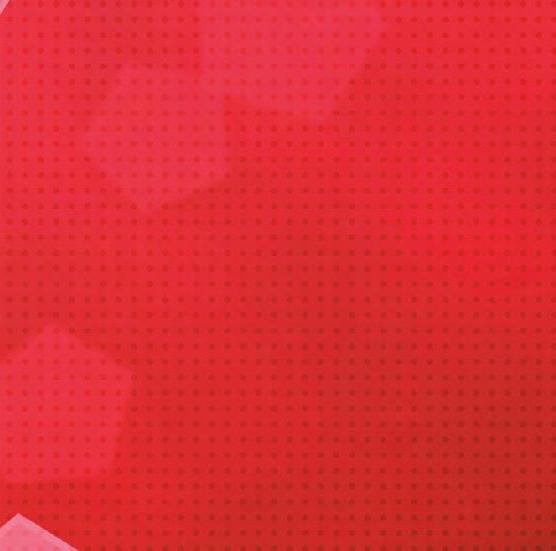
The Problem
The stage was already being set for smaller rigs in Alaska’s oil patch, based on recent trends. According to Ross, “A lot of the reservoirs we’re exploring, up north especially, are much shallower
Innovative, cost eff ective housing with all the comforts of home

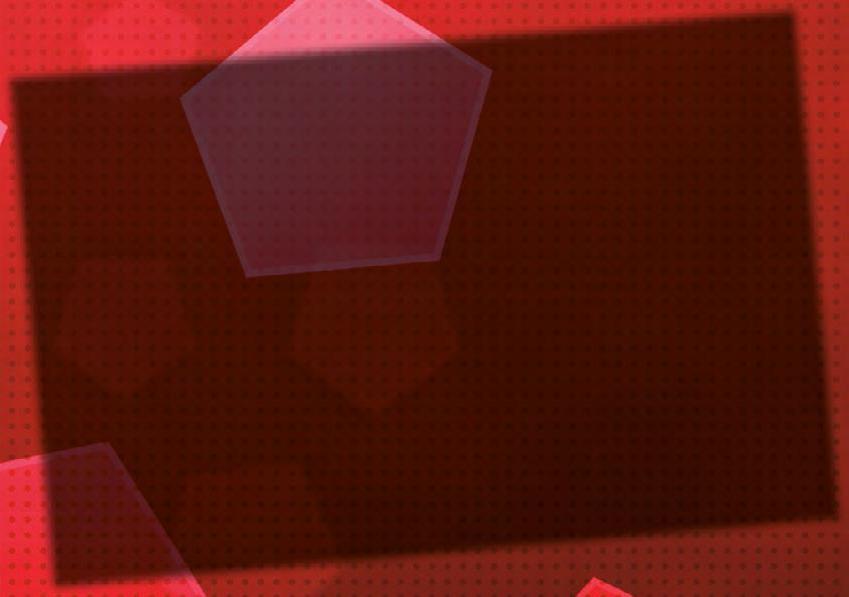
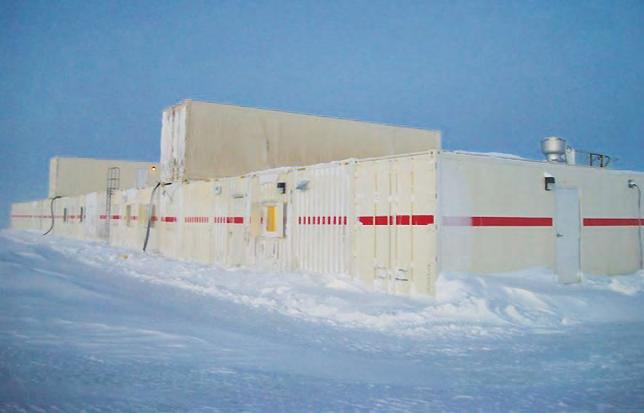
Air Systems Deliver Fresh Air to Each Room!
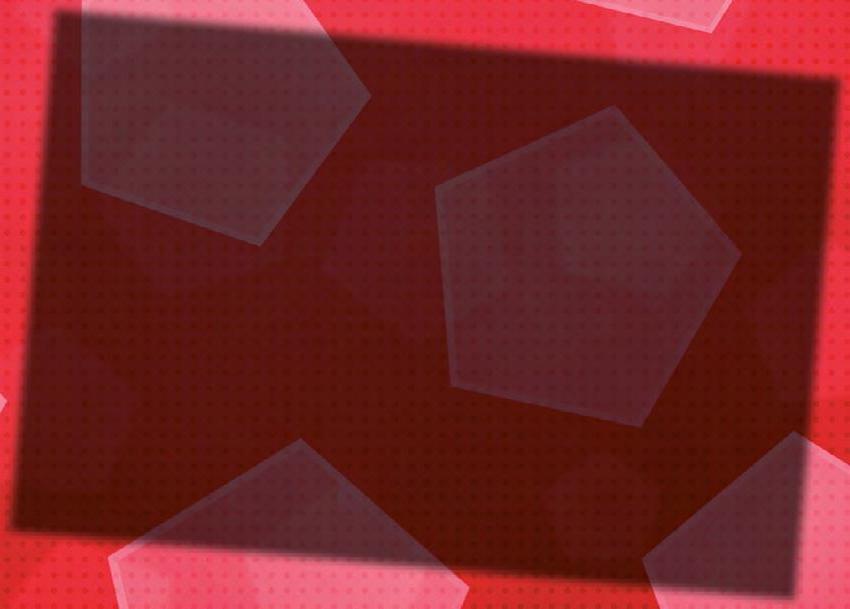
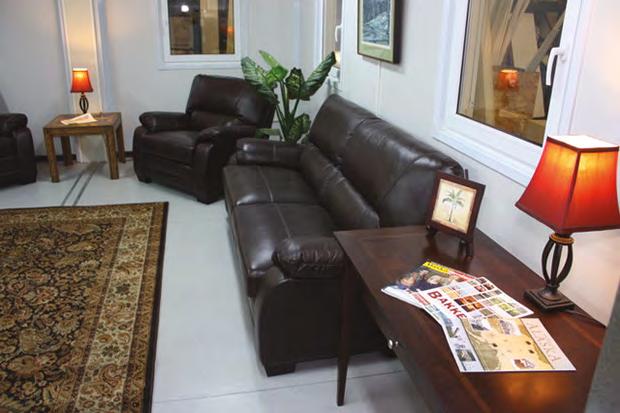
• Arctic tough • Turn-key set up • Rapid mobilization • Custom built • Easy to relocate Let us build your next modular facility
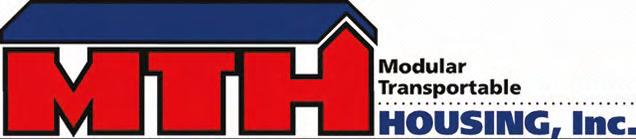
than they used to be back in the Prudhoe Bay days. It did require bigger rigs to do what we were doing, back in the day.”
However, Flynn says industry players continued to rely on the rigs they had poured so much capital into. “They’re using development rigs to go out and drill exploration… They have these beautiful, big rigs… they weigh 2 million pounds. Our rig weighs 50,000 pounds.” Ross adds, “It’s extremely expensive, and the risk is getting higher and higher based on the fact that exploration sites are further and further away from any road access.”
When the Alaska economy entered recession in 2014, “We saw the writing on the wall,” says Flynn. He and Ross believed oil companies were spending too much and not getting results, and consequently, “The state was not drilling any more holes.” They agreed something had to change. Flynn asked, “Why are we spending all this massive amount of money to bring this massive rig out there when all you need is a small rig to do it?”
The key to effectual drilling is a rig sized for hard-rock mining. With Ross’ well completion knowledge, additional hardware converts it to a tool that can be used for oil and gas applications. As Ross explains, “It required building a rig to API [American Petroleum Institute] specifications. It required putting together a well control system [and] blowout preventer, in addition to the closed-loop mud system.” ADC is currently applying for patents. As Flynn puts it, “No one had technically done it the way we have done it.”
True, Flynn says, small-scale oil and gas rigs exist, but not the kind they were envisioning. “You go down to West Texas,” he says, “there are smaller, truck-mounted singles that’ll drive around and pull right up to a well and do what you need to do. You can’t heliport that.” Such trucks, he says, weigh 80,000 pounds; to be compatible with the helicopters available, the load must be no more than 5,000 pounds.
The “effectual drilling” rig is made of about fifty pieces, each less than 3,000 pounds. That’s still a lot of assembly,
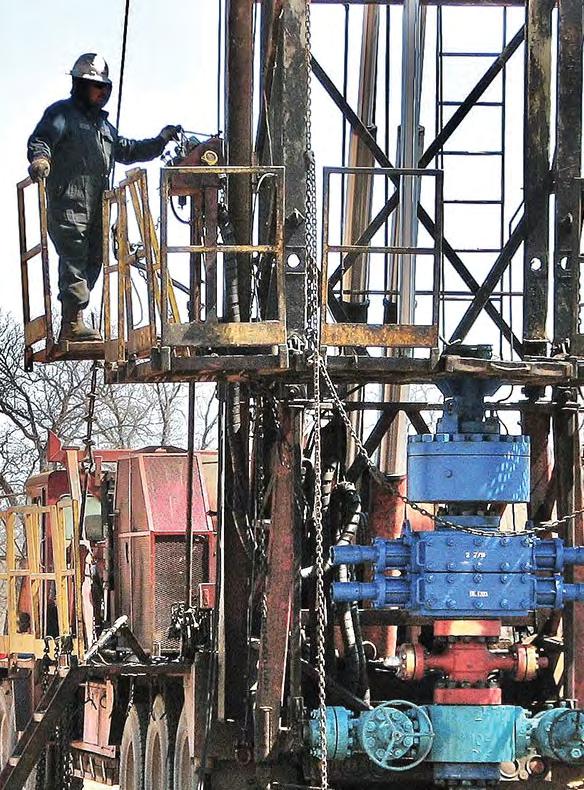
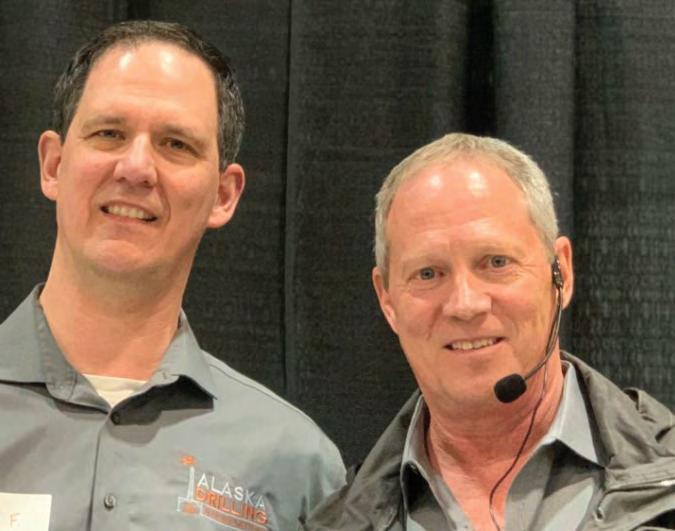
Tim Flynn (L) and David Ross (R) drew on their skill as petroleum engineers to modify a small-scale exploration rig (Below).
Alaska Drilling and Completions
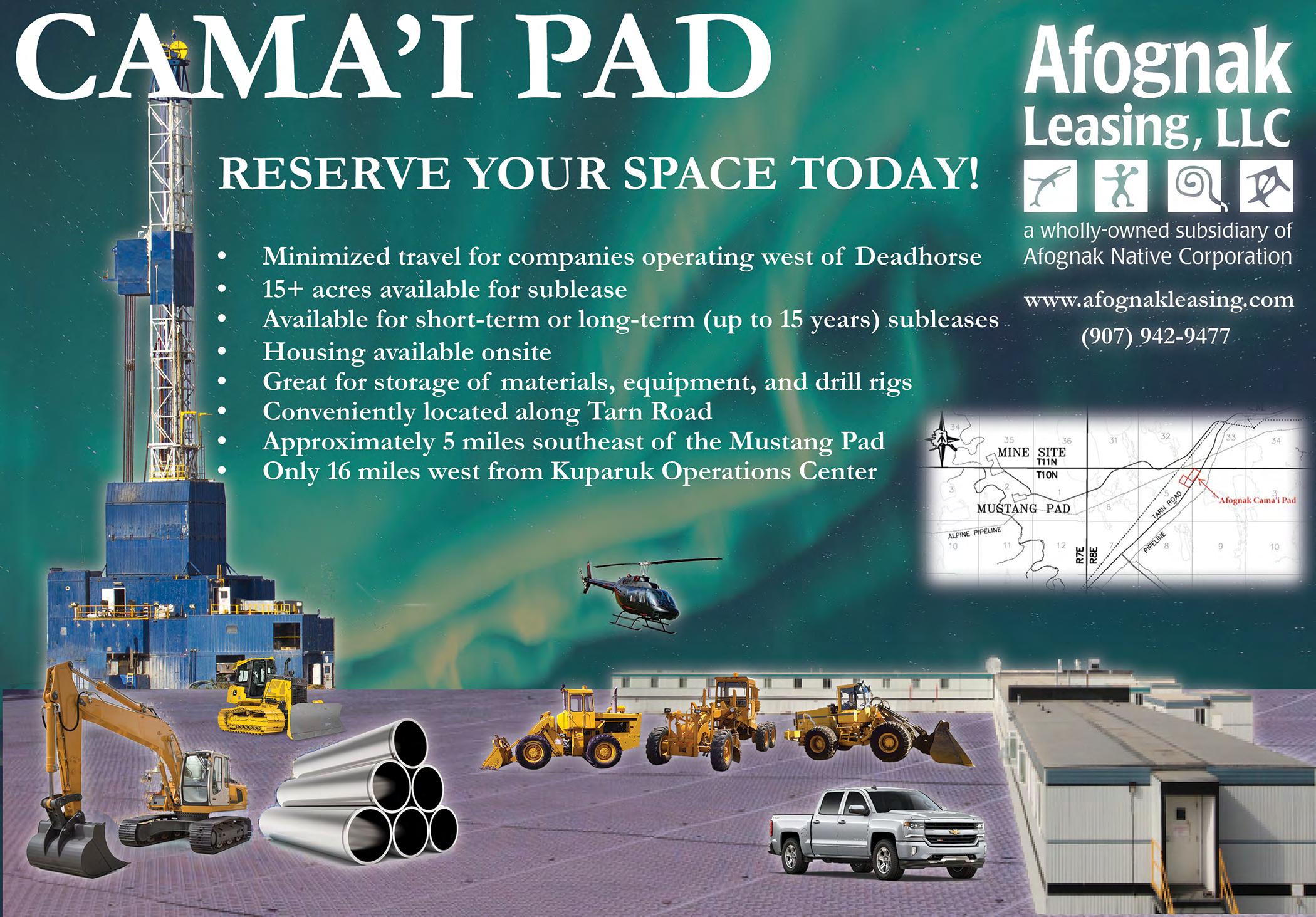
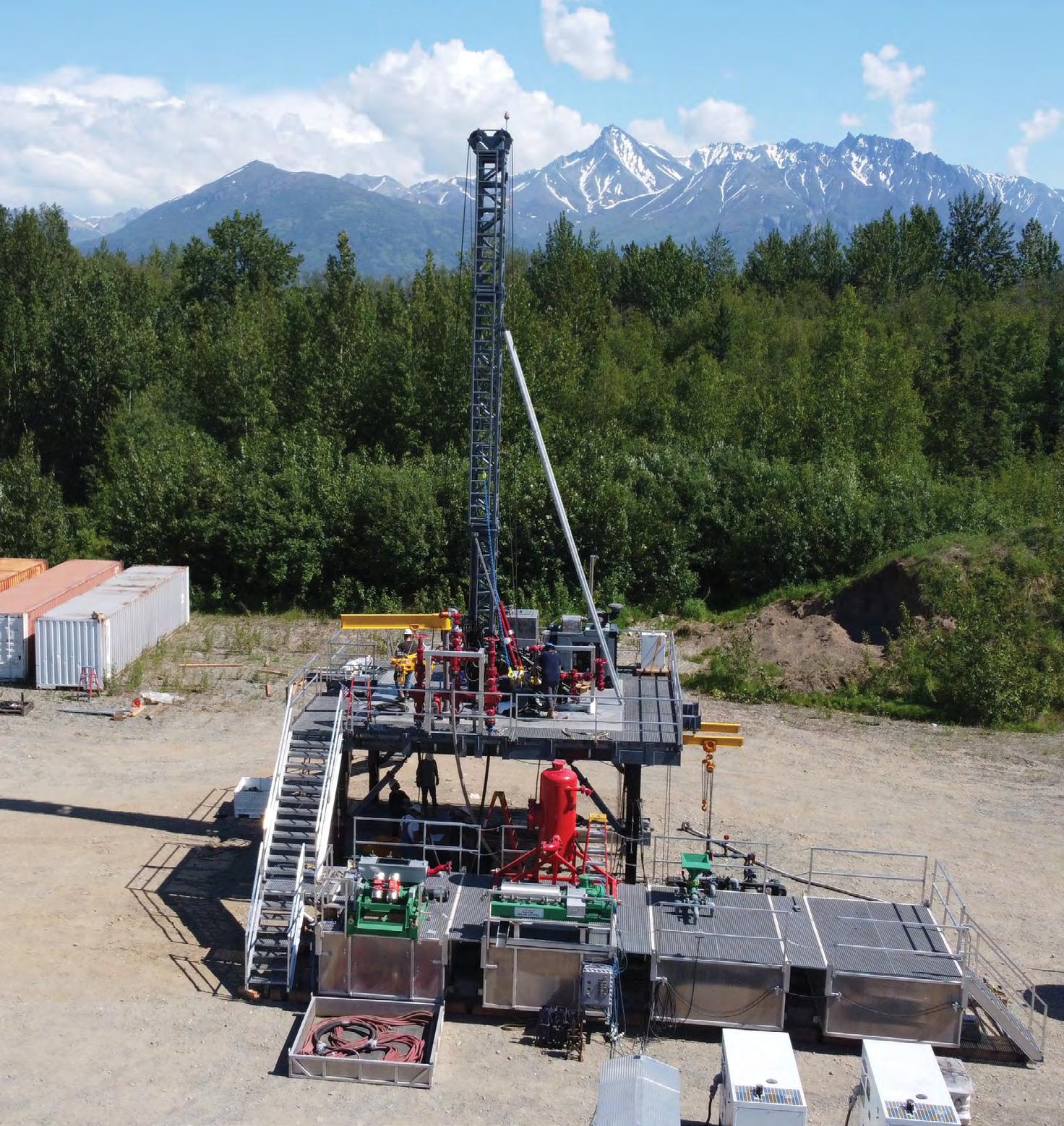
taking three to five days to transport fifty loads, depending on remoteness.
Although helicopters aren’t cheap, Flynn says airlifting is far more affordable than the alternative. “Everybody thinks ‘helicopter’ and it’s that trigger word: ‘Just bring your checkbook,’” he says. “Well, when you decide to build an ice road, you better bring several checkbooks.”
Not that “effectual drilling” is averse to ground transport. If the rig were to be used on the North Slope, for instance, it wouldn’t fly there from its storage yard in Palmer. The trip would take eight, 40foot flatbed trailers. “We’re like a rock band, heading up the road,” Flynn says.
Each of the fifty pieces of the rig can stack on a trailer, which can be pulled over rough terrain by a balloon tired Rolligon truck or a tracked PistenBully. According to Ross, “We have such a lightweight rig that we can actually use these vehicles to pull our equipment out over the tundra, once the tundra opening has occurred,” typically in mid-December.
Mobility is the key selling point. “They want us to put roads down,” Flynn says. “We’re like: We just don’t need
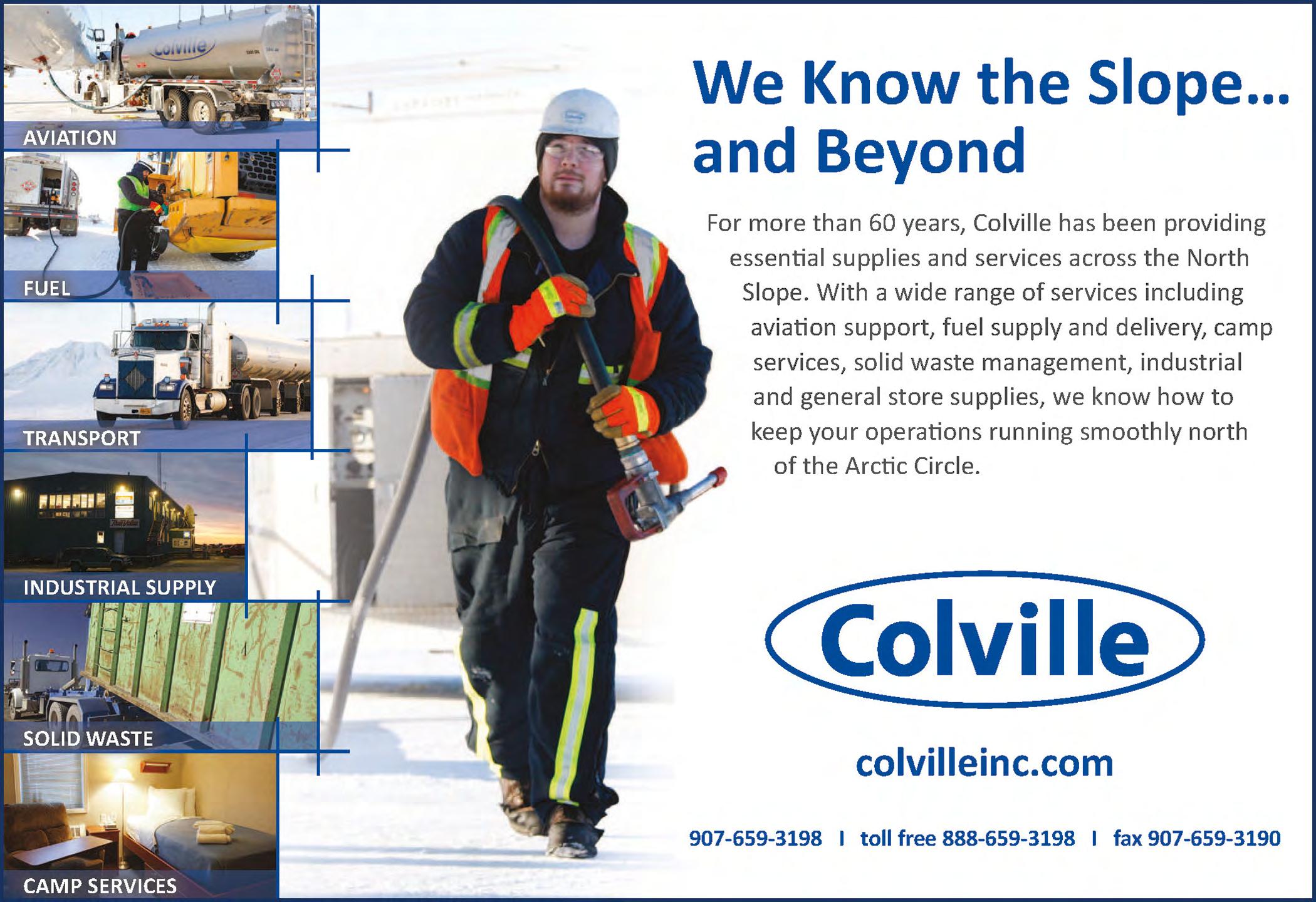
Right-Size Savings
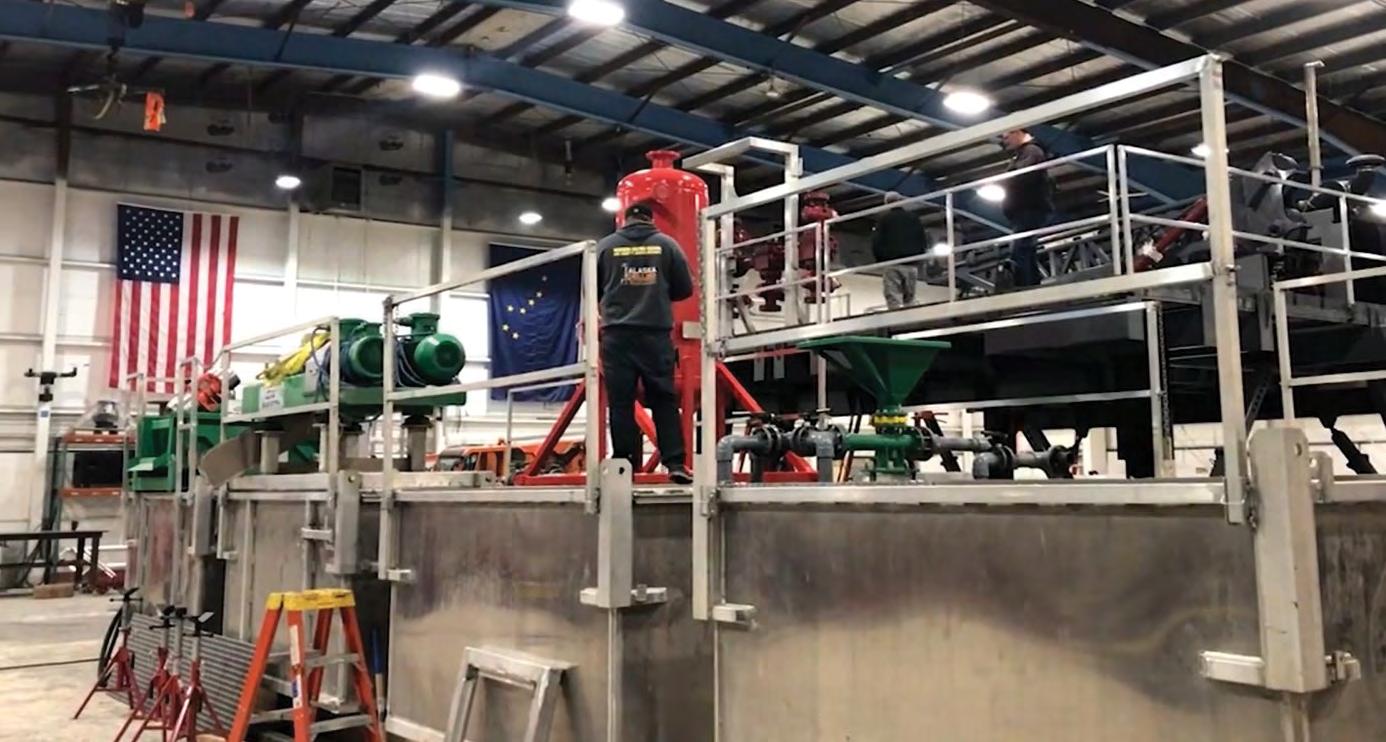
Exactly how much ADC has invested into creating the “effectual drilling” rig, Ross and Flynn would not disclose. All they say is that their method should be “an order of magnitude” cheaper than conventional drilling.
“It’s a lot different than a large rig that sits in a yard and requires many, many people to get it ready to go,” says Flynn. “Ours is much smaller, and requires less men, less diesel burned, less days to move, and we can still drill to 8,000 feet.”
Using current methods, Ross explains, “You’re looking at a support structure of having a roughly 250-man camp. You’re supporting that with numerous support vehicles, trucks with tankers hauling disposable fluids off. You’re burning roughly 6,000 to 7,000, maybe even 10,000 gallons a day of diesel. And that’s on an ice pad that’s roughly 600 by 600 feet.”
Ross and Flynn claim their “effectual drilling” rig can operate on a 100- by 100-foot area, staffed by a crew of twelve to twenty. They might get away with burning less than 2,500 gallons of diesel per day, running heaters in winter. In summer, they believe the rig might sip as little as 100 gallons of fuel daily.
The savings could begin even before the site is set up. According to Ross, “For a snow road operation, we’re looking at about 47 loads to get the entire rig out, and camp, and structure, versus 200, 250 loads minimum.” Further, not being bound to snow roads, Flynn says the rig has another advantage: “Being able to get out in the summer, not having to build a gravel road, and not have to build an ice road, which is not even possible a lot of years down south [in Cook Inlet].”
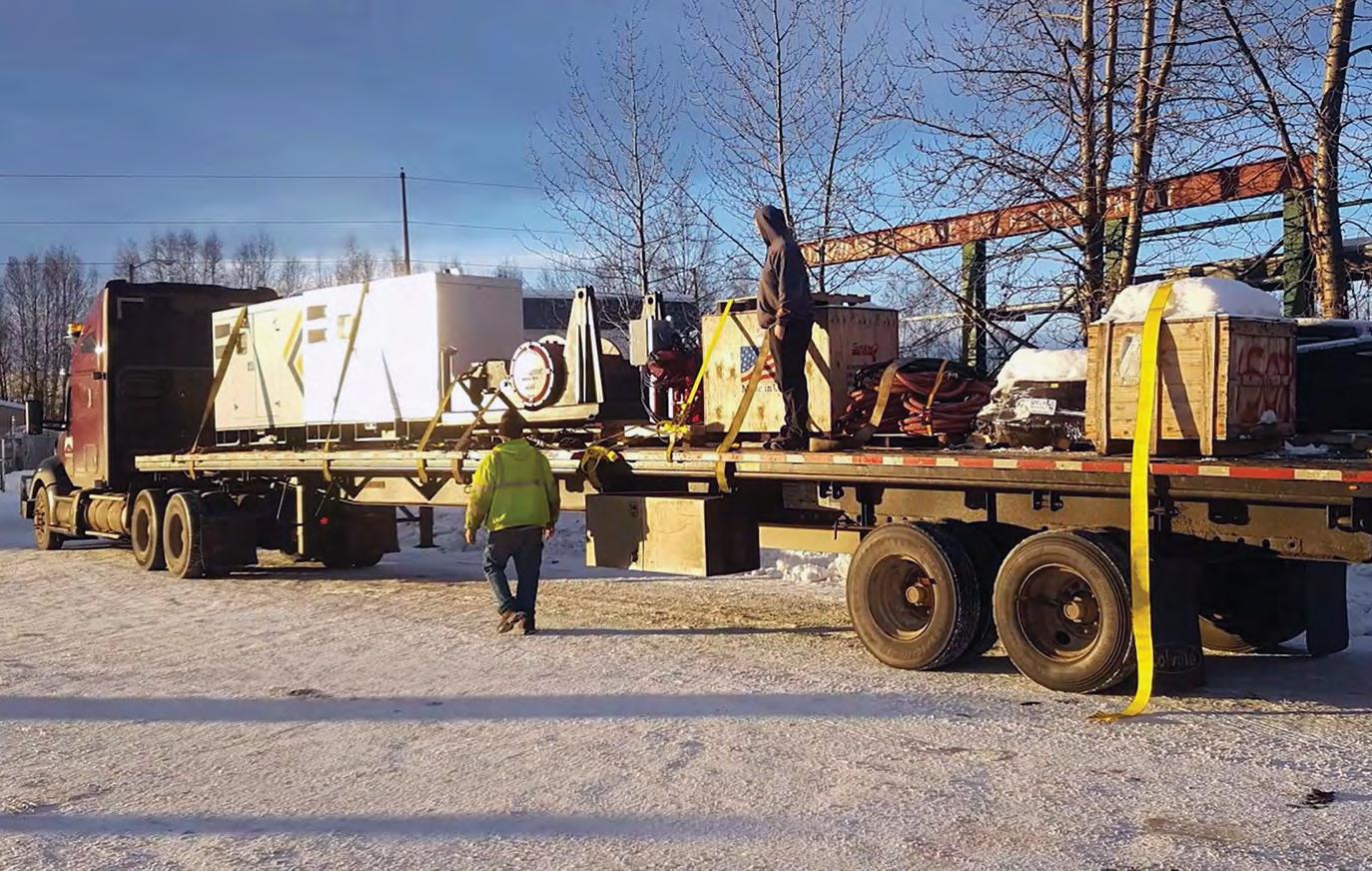
Additional Applications
“Leave no trace” is part of the mission of Alaska Drilling and Completions, as well as a commitment to clean energy. Although their business is mainly geared toward oil and gas, Ross and Flynn envision their rig being used for geothermal prospecting.
“We can set this rig up on the side of a mountain if we had to,” says Ross, and he says the well-control fixtures work as well for hot water and steam as they do for petroleum.
For now, the rig is parked in Palmer, waiting for its first client. ADC unveiled the technology in April and spent the summer testing it. The rig still needs to be winterized before it’s ready for the Slope.
Ross and Flynn don’t see anybody else using their approach, at least not yet. Ross says, “The technology we developed, we feel, has applications throughout the entire state and elsewhere.”
One application, Flynn says, would be Yukon River villages. There are natural gas seeps in Fort Yukon, Galena, and Holy Cross, enough to fuel their electricity needs instead of more expensive diesel. According to Flynn, “effectual drilling” is the key to making that conversion affordable. “Explore for a much smaller amount of money,” he says. “Get down there and see if it’s even viable, versus bringing a big rig and it’s not viable.”
ADC’s co-founders say their goal is to develop Alaska’s resources and create more jobs. But how can that happen when their rig leaves 200odd drillers on the curb? “It’s easily looked at as we are taking away jobs,” Flynn says, “but the reality is we have the potential to create tens to hundreds of more jobs than ever would’ve been possible without this technology.”
ADC hopes new, more affordable technology keeps exploration alive for oil and gas and other resources.
Alaska Drilling and Completions
Tim Flynn, COO, Alaska Drilling & Completions