
10 minute read
3,300-FOOT LIFELINES
Remote runway construction takes grit, group effort
By Amy Newman
Certain things about life in Alaska are absolutes. Bears will emerge from their dens in the spring. Aurora watchers will chase the Northern Lights in winter. And aviation continues to be a literal lifeline to the 82 percent of communities that lie off Alaska’s road system.
“I don’t think it ever hurts to reinforce that aviation is huge for Alaska,” says Angela Smith, aviation group manager for PDC Engineers. “If the planes stop flying in Alaska, it would be a very different world. They play a vital role in most Alaskans’ daily lives that they just don’t even think twice about it.”
With more than 2.4 million square miles of airspace, six times more pilots, and sixteen times the number of aircraft (per capita) than the rest of the United States—huge is an understatement. This vast expanse is served by 700 FAA-regulated airports, 235 of which are rural facilities owned and maintained by the Alaska
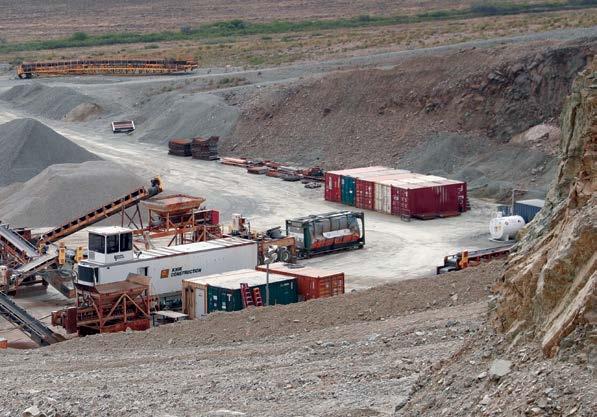
Department of Transportation & Public Facilities (DOT&PF). Comprised of little more than a roughly 3,300-footlong runway, an apron, and a small terminal, rural airports ensure yearround access to residents and tourists and keep communities supplied with goods, equipment, and other everyday essentials.
“In some places, people are relying on those [flights] not just to get out but to get stuff in,” says John Limb, senior associate at Stantec. “The groceries come in on the airplane, the medicine comes in on the airplane, the mail comes in on the airplane.”
For rural airports, smaller doesn’t mean easier when it comes to designing and building facilities. With guidance and input from the FAA and DOT&PF, a team of surveyors and hydrologists; electrical, mechanical, and geotechnical engineers; environmental scientists and consultants; and construction crews with experience working in remote locations collaborate to create a safe, cost-effective, efficient facility that can serve the community long-term.
And they do it while dealing with logistical challenges not found elsewhere.
“We have to get the equipment there, you have to think of material sites and how to find gravel in an area and location and bring it on to the runways and think about how [airport] access roads might interact with the community,” says Ryan Cooper, an environmental scientist with Stantec. “So much of what we see is people just focusing on that miracle mile, the 3,000-feet of the runway, when we also need to think about the whole aspect of what the airport does.”
Designing the Ideal Airstrip
Compared to airports in the Lower 48, even the state’s larger hub airports seem small. But in Alaska, whether an airport is considered a small, rural facility hinges largely on the type of aircraft it can accommodate.
“Most of these communities, when we talk rural [airstrips], are about 3,300foot gravel strips, with a little baby taxiway that connects the runway to the apron, and that’s it,” Limb says. “The aircraft is typically less than 12,500 pounds; that identifies the airport as what we call a small airport.”
Funding for airport projects is limited. In 2020, the DOT received $239 million from the FAA to fund airport improvement programs across the state—which means consultants and designers must figure out how to design a safe, sustainable facility that doesn’t waste taxpayer dollars, Smith says. Sometimes the cost isn’t justified.
“It’s just so doggone expensive to build because it’s [rural Alaska], so hard to get to,” she says. “There are ways to figure it out, but it just takes money, and sometimes it just doesn’t pencil out. And that sounds cold, but sometimes the amount of money to construct the facility and then maintain the facility
Knik Construction operates its own material quarries in Western Alaska to ensure it can supply remote projects with gravel, rock, sand, and other aggregate material.
Knik Construction
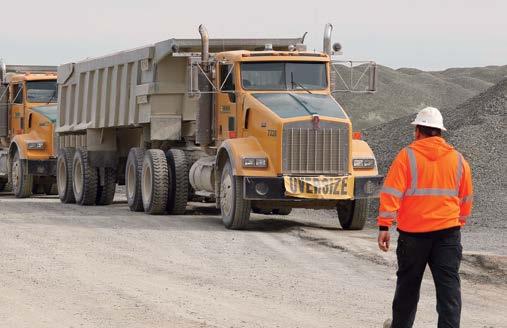
Knik Construction transports gravel and other aggregate materials needed for runway construction via truck and barge to remote project sites throughout Western Alaska.
Knik Construction
for the required length of time doesn’t pencil out.”
The most important aspect of an airport is, obviously, the airstrip. When designing one at a rural community, the priority is determining whether there’s sufficient space to safely orient the runway.
“The minimum recommended runway length is 3,300 feet. It doesn’t have to be 3,300 feet, but most air carriers are going to want more,” Smith says. “Then you’ve got a safety area off each end of it, so you have to plan for at least 5,000 feet or more of length.”
But that space must be in the proper location, or at least in a location that designers can mitigate potential hazards. The runway must be oriented to align with the prevailing wind direction, which is how pilots take off and land, Smith says. And the surrounding terrain, whether mountains, trees, or something else, must be free of obstructions.
The type of aircraft that will use the runway also factors into its design, because it dictates which materials are most appropriate.
“Runways are designed around a strength value, and most of the runways in Western Alaska are gravel runways; they aren’t paved,” explains Dan Hall, president of Knik Construction. “Nome, Bethel, and Kotzebue are bigger hubs, and Alaska Airline planes run in there, so they are all paved. A place like Kasigluk, where a Caravan 207 is hauling people, freight, and mail, is going to have a gravel airfield.”
Just as important as the design of the runway are the supporting pieces that enable it to operate safely.
“There’s more than just surfacing the runway,” Hall says. “Lights, navigational aids, and equipment storage buildings are also usually part of the airport projects.”
Radio communications and some form of weather reporting system, so pilots know the weather conditions before flying in or out, are also necessities, Smith adds.
Logistical Challenges
Every project off Alaska’s road system faces unique challenges that require just as much planning and forethought to overcome as the design and construction of the project itself.
“Our construction in Alaska is completely different than anywhere else in the United States, just based on how big our state is and how little infrastructure is based on roads and access,” Hall says. “It’s more of a logistics project than a construction project.”
Sourcing materials and transporting them to the project site at a reasonable cost is often the biggest hurdle.
“I think the biggest challenge with any rural airport is what gravel materials are available locally and are they good enough to use for a runway,” Hall explains. “It makes costs extremely high if you have to import or bring in all the materials, especially in a Western Alaska scenario, where gravel is hard to find.”
Limb agrees.
“That’s usually the number one problem,” he says. “We have to ask, ‘Where are we going to get the materials from?’ That’s mining materials, finding materials, and being able to ship it to that airport to get the work done. The logistical component of that is just as difficult as doing the work itself.”
In locations with no real gravel sources, like Western Alaska, materials have to be sourced and brought in from other areas, Limb explains. For communities located along a waterway, material and equipment can be shipped
in via barge or shallow-draft landing craft, while hovercraft, helicopters, or even sleds are used for locations unreachable by marine transportation.
Figuring out how to work on the runway while not cutting the community off from the outside world during construction is another challenge. At larger airports, crews shut the runway down and divert aircraft to a taxiway or second runway. Neither of these is an option for a rural airport with a solitary runway and a shortened taxiway.
“The question is, ‘How do you do both?’” Hall says of working on a runway while maintaining flight operations. “There is a disruption as we all know. You can’t rebuild a road without some kind of inconvenience to the public. The goal is to minimize that as much as you can, but it’s not always perfect.”
Working overnight provides only a partial workaround, so crews often utilize half-width operations, which allows construction and take-offs and landings to happen on the runway simultaneously. It’s a necessary accommodation to traditional FAA rules regarding runway construction.
“According to FAA rules, when you’re doing work on a runway you have to shut it down,” Limb explains. “That’s not happening here because oftentimes communities don’t have other viable means to get out of the community. You cannot shut them down when you want to redo the airport.”
Half-width operations literally shut down one-half of the runway for the crew to work on it, which allows planes to take off and land from the other half, Limb says. Once construction is completed on one half, the process is repeated on the other.“Most of these communities, when we talk rural [airstrips], are about 3,300-foot gravel strips, with a little baby taxiway that connects the runway to the apron, and that’s it… The aircraft is typically less than 12,500 pounds; that identifies the airport as what we call a small airport.”
John Limb, Senior Associate, Stantec Master Planning
Airports are typically designed as part of a master plan, which Limb says is an environmental function that takes into consideration the socioeconomic impact of the project and how it will
Summer is here. Fly for Work.
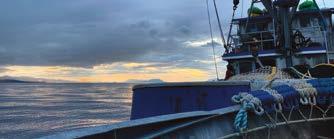
Fly for Play.
Ravn Alaska.
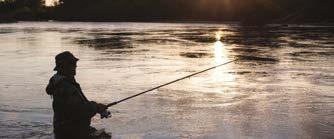
Call 800.866.8394or visit RavnAlaska.com
meet the needs of the community and the surrounding areas.
“There are quite a few different moving parts when we’re designing an airport, as you can imagine,” he says. “We’re often working through our client, which is the Alaska Department of Transportation. The FAA is involved because they’re the funding source; 95 percent of these projects are funded through the airport improvement program.”
Data and input provided by surveyors and hydrologists, geotechnical and electrical engineers, environmental scientists, construction crews, and even the community are all part of the planning and design process.
Provided a project scope is not too large, Smith says “the whole kit and caboodle” of transportation projects—which includes gathering site data, design and permitting, construction sequencing, site prep, and construction—typically takes two to five years.
Construction is often done in phases over seasons, in part because of the practicalities involved in mining materials from local sources.
“In many places, the best material comes from the rivers,” Cooper says. “The best time to do that, because of fish and low water, is during the winter. So oftentimes while it looks like a construction project is just [happening] during the summer, what’s actually happened is that in the fall, that equipment has been staged at the village, and over the winter they work to develop the materials.”
With a limited pool of funds, there’s recently been more focus on maintaining and preserving existing facilities to extend their natural life. This means that the community’s capacity to care for the runways and associated airport facilities factors into the design plan.
“We have to take maintenance and operations into consideration,” Cooper says. “At larger airports they have staff. At these little airports, they often have no full-time staff and they’ve contracted a part-time local person who they’ve given a grader and does some small amount of regrading. So a lot of the design and engineering has to incorporate what’s practical.”
Planning also includes mapping out the most efficient way to deliver equipment and materials to the project site.
“We’ve done some crazy stuff over the years where we’ve had to handle materials five or six times from the material’s source before it gets to the final resting stop at an airport somewhere,” Hall says. “Barging out of Platinum to Kipnuk, then trucking it to the stockpile site. Hauling it to the runway in the winter because you can’t get across the tundra in the summer. There are a lot of factors to consider when planning projects in remote Alaska. We often start years in advance to make sure the puzzle pieces all fit together.”
“Runways are designed around a strength value, and most of the runways in Western Alaska are gravel runways; they aren’t paved. Nome, Bethel, and Kotzebue are bigger hubs, and Alaska Airline planes run in there, so they are all paved. A place like Kasigluk, where a Caravan 207 is hauling people, freight, and mail, is going to have a gravel airfield.”
Dan Hall, President, Knik Construction
Stantec was part of the team that relocated the Noatak Airport due to encroachment of the adjacent river and intrusion of safety areas on the runway.
Stantec
