B.BAP (By MUN Korean Kitchen)
Tenancy L02 2081 - Highpoint Shopping centre VIC 3032
DRW NO . TITLE
NO . TITLE COVER PAGE
NOTES
PERSPECTIVE VIEW -1 A-01
PERSPECTIVE VIEW -2
SCHEDULE -1
TO SCALE
&
ELEVATION & ELEVATION -A1
DETAIL - MAIN STATION A-02 A-03 A-04
-2
EXISTING PLANS
EXISTING ELEVATIONS & SECTIONS
PROPOSED FLOOR PLAN
PROPOSED REFLECTED CEILING PLAN
PROPOSED
ELECTRICAL PLAN
DETAIL - HANGING MIRROR & SIGHNAGE
DETAIL - BANQUETTE SEAT -1
DETAIL - BANQUETTE SEAT -2
DETAIL - WALLMOUNT HIGH TABLE
DETAIL - SIGNAGE
DETAIL - WALLMOUNT NEON SIGN
DETAIL - CABINET-1
DETAIL - CABINET-2
DETAIL - CABINET-3
DETAIL - MENU BOARDS
DETAIL - WALL LED LETTER SIGNAGES
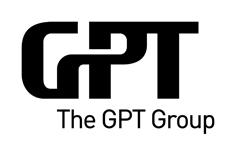
Your design as detailed on the attached plansand specifications has been granted Final Design Approval (FDA) subject to the conditionsoutlined on this approval and noted on the approved stamped drawings.
Approved Drawings
Final Design Approval subject to all notes and stamps on the attached drawings –revise and reissue accordingly for approval. Ensure yourshopfitterretains a copy of these GPT stamped approveddrawings on site at all times.
Services Checklist and Maximum Demand Calculations
Must be submitted for separate approval.
National Construction Code (NCC) and Australian/ New Zealand Standards
The base building shell and associated fit-out works that comprise the leased premises must comply with the National Construction Code (NCC)/ Building Code of Australia (BCA) 2019 including, Australian/ NewZealand Standards and all other statutory/ planning/ authority requirements that apply to the approved fit-out.
Access and Egress Requirements
All tenancies mustcomply with the Disability Discrimination Act (DDA) / Access Premises Standards and all related requirements within the NCC/ BCA 2019 Part D, Australian Standards and Centre specific requirements.
Shopfront
Your shopfront is to comply with the NCC/ BCA 2019 and Section J (where applicable). Shopfront to be self-supporting and not to impose any load on thebase build structure.
All door guides, tracks, lockdowns, trims, covers, mechanisms, access panels need to be recessed and set flush or concealed within surrounding planes.
Shopfront Glazing
Provide a structural integrity diagram and/orcertificate advising the design of your shopfront glazing is in accordance with the NCC/ BCA 2019 and the Australian Standards prior to commencing works on site.
Flooring
All flooring must comply with the NCC/ BCA 2019 and Australian Standards regarding slipcoefficients and fire indices.
Slab/ Wall Chasing
Slab/ wall chasing is not allowed to the lessor’s base building structure without prior express permission and/ or approval from Centre Management.
Recessed Separation Strips
Flush set recessed 3mm flat bar separation strips are required between varying adjacent floor finishes. Raisedcover strips that are typical to some floor finish applications are not acceptable for reasons of trip hazard and aesthetic value.
Expansion Joints
Treatment of joints to suit your floor,wall andceiling finishes and nominalmovement criteria. Refer to details in theCentre specific StyleGuide and the tenancy plans for preferred specification.
Walls
All walls to be clad orfinished including any back of house areas whichcan be seen from the front of houseareas, unless otherwise approved ondrawings. All storeroom walls to be full height.
IntertenancyWalls
Extend IT walls to underside of existing slab and/or roof as per your final approved drawings giving consideration to the Centre’s Fire Engineering Report (FER) where applicable.
Chasing of intertenancy walls to accommodate services or services to be located within the cavity is notpermitted.
Inter-tenancy walls arenon-load bearing.Wall structure to support fixture(s) to be built by your shopfitter.
Ceilings
Ceiling access panels to be located as required by the base building consultants and shall be ‘Trafalgar APC/WW’or equal, flush fitting with the ceiling plane incorporating concealed hinges and Allen key locking.
Air conditioning register cut outs by shopfitterto lessor nominated locations.
Air registers are to be finished/ colour matched into ceiling surrounds.
Rigid Ductwork
In all tenancies where a ceiling does notform part of the overall design approval, all visible flexible ductwork must be replaced with rigid ductwork by the lessor’s nominated contractorat the lessee’s cost.
Signage and Graphics
Tenancy signage and graphics to be issued for separate approval prior to fabrication unless already approved in attached FDA.
Structural
All structuralitems to be designed and certified by a registered structural engineer.
Lighting and Power
Combined lighting and power heat loadandlighting specifications must meet the ‘GPT Minimum Standards’, the NCC/ BCA 2019 including SectionJ (where applicable) and relevant codes and Australian Standards. Note the allowable maximum illumination power density is 14 watts/ sqm as per the NCC/ BCA 2019 Section J.
Electrical Distribution Board (EDB)
Access to EDBs must complywith the power supplier’s guidelines for access and servicing. The fitout must not contraveneaccess and securityof the EDB. GPT has embedded energy networks in some Centres, if an embedded network is available you can elect to join. This can be confirmed with theCentre Tenancy Delivery Manager (TDM).
Fire Hose Reels and Hydrants
If required,to be located as per the Australian Standards and the NCC/ BCA 2019 Part E.
EmergencyLights and Exit Signs
To be designed and installed to comply with Australian Standards and NCC/ BCA 2019 Section E4. Please note emergency and exit lights must be on a separate circuit and have a test switch.
Electrical Services
Your shopfittermust arrangeall electrical applications with the relevant authority.
Telephone/ Data Services
Your shopfittermust arrangelodgementof the application with the relevant supplier.
Waterproofing of wet areas
Provide waterproof membrane under floor finish in any wet areas/ kitchens/external entry thresholds within the tenancy.
The membrane must return up the walls a minimum of 300mm and turn down into drainage points. Provide epoxy grouting to floortiles.Waterproofing membrane is to be installed under all finishes including vinyl. All relevant certification to be provided.
Water
Water consumption and wastedisposal must be aligned with GPT’s Minimum Standard’s as agreed under the Lease and listed in the Fit Out Guide. Alltapware and sanitaryware designed and specified must be in accordance with our Minimum Standards.
Waste Management
Provide an area within the leased premises that can contain and manage the recycling of waste in a clean and safe manner alignedwith the Centre’s waste streams and recycling program.
SecuritySystem
All security devices and alarms must be concealed. Only dome type securitycameras are permitted. Security system power supply is to be concealed into the surrounding shopfront structure but notthe basebuilding.
Private Certifier/ Building Surveyor
Please contact your Private Certifier/ Building Surveyor for Planning Approvals ie DA, Construction Certificate/ Building Permit.
Site Measure
It is necessary that all information supplied by the Lessor pertinentto the lease deal and the fit outof the premises is checked / inspected /measured and orverified by the Lessee (or duly appointed representative ) on site .
Aluminium Composite Panelling
It is prohibited to use the following aluminium composite panelling (ACP) products in the fitout of your tenancy including in any signage, shopfront, or bulkhead:
A panel that comprises a polyethylene core (meaning a core or lamina that is comprised of 30% or more polyethylene bymass) or lamina bonded to one or more sheets of metal panels including an aluminium composite panel; and Any expanded polystyrene product used in an external insulation and finish (rendered) system. If requested by GPT, you must provide evidence that products used by you do not contravene this prohibition. GPT reserves the rightto require you to remove any such products from the fitout of your premises and to substitute them with other approved products at your cost.
Certification will be required by the Lessor from your providerthat minimum standard material has been installed.
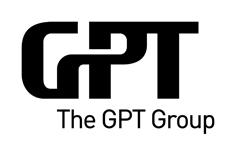
ACCESS AND EGRESS:
● A MINIMUM WIDTH OF 100MM IS REQUIRED THROUGHOUT THE TENANCY WITHIN THE PATH OF TRAVEL TO AN EXIT
● ALL STAIRS ARE TO BE DESIGNED IN ACCORDANCE TO AS 1428 1-2009 THIS WILL INCLUDE BUT NOT LIMITED
TO REQUIRED 1000MM CLEARANCE BETWEEN HANDRAILS OPAQUE RISERS, CONTRAST NOSING S, AND THE HANDRAILS ARE TO TERMINATE 300MM BEYOND THE FINAL RISER AND ROTATE 180 DEGREES TO AS1428 1
DOORS:
● CIRCULATION CLEARANCES ARE REQUIRED TO ALL DOORS WITHIN THE BUILDING INCLUDING THE LIFT
ENSURE ALL DOORWAYS HAVE A MINIMUM CLEAR OPENING OF 850MM, 110MM HINGE SIDE AND 510MM LATCH
SIDE CLEARANCES BASED ON FRONT ON APPROACH TO COMPLY WITH AS 1428 1-2009
● ENSURE ALL ENTRY AND EXIT DOORS TO HAVE HOLD OPEN DEVICE & PEST STRIP TO BOTTOM
● ALL ACCESSIBLE DOORWAYS REQUIRE A MINIMUM LUMINANCE CONTRAST OF 30% PROVIDED BETWEEN
▪ DOOR LEAF AND DOOR JAMB;
▪ DOOR LEAF AND ADJACENT WALL; ARCHITRAVE AND WALL
▪ DOOR LEAF AND ARCHITRAVE; OR
▪ DOOR JAMB AND ADJACENT WALL (AS1428 1 CLAUSE 13 1)
THE MINIMUM WIDTH OF THE AREA OF LUMINANCE CONTRAST SHALL BE 50MM SEE HTTP://WWW DISABILITYACCESSCONSULTANTS COM AU/LUMINANCE-TESTING
● D-TYPE DOOR HANDLES TO VE SPECIFIED FOR DOORS WITH LATCH SETS (AS1428 1 CLAUSE 13 5 2)
● ENSURE ALL DOORS ARE FINISHED FLUSH TO THE WALL
● ALL GLAZING LOCATED WITHIN THE ACCESSIBLE PATH OF THE BUILDING AND CAN BE MISTAKEN FOR AN OPENING FULLY GLAZED PANELS) ARE OT BE INSTALLED WITH DECAL MARKINGS TO AS 1428 1
● DOOR IN A REQUIRED EXIT OR PATHOF TRAVEL TO AND EXIT MUST BE READILY OPENABLE AT ALL TIMES FROM THE SIDE FACING A PERSON SEEKING EGRESS BY A SINGLE HANDED DOWNWARD OR PUSHING ACTION ON A SINGLE DEVICE LOCATED BETWEEN 900 - 1100MM OF THE FLOOR
● FOR DOORS OTHER THAN FIRE DOORS AND SMOKE DOORS WHERE A DOOR CLOSER IS FITTED, THE FORCEREQUIRED AT THE DOOR HANDLE TO OPERATE THE DOOR SHALL NOT EXCEED 20N
● THE DOOR HANDLE AND TELATED HARDWARE SHALL BE OF THE TYPE THAT ALLOWS THE DOOR TO BE UNLOCKED AND OPENED WITH ONE HAND THE HANDLE SHALL BE SUCH THAT THE DAND OF A PERSON WHI CANNOT GRIP WILL NOT SLIP FROM THE HANDLE DURING THE OPERATION OF THE LATCH
● ALL FIRE DOORS TO BE SELF CLOSING OR AUTOMATIC CLOSING IN ACCORDANCE WITH C 3 4 OF THE NCC
MECHANICAL EXHAUST VENTILATION :
● ALL COOKING EQUIPMENT / DISHWASHERS WITH A TOTAL MAXIMUM ELECTRICAL POWER OUTPUT INPUT THAT EXCEEDS 8KW OR A TOTAL GAS INPUT EXCEEDING 29MJ/H MUST HAVE A COMMERCIAL EXHAUST SYSTEM IN ACCORDANCE WITH AUSTRALIAN STRANDARDS 1668 1 PART1 AND PART 2
● EQUIPMENT SCHEDULE TO BE READ IN CONJUNCTION WITH T-A SQUARE DESIGN DRAWING PACKAGE REPORT ANY DISCREPANCIES
● PROCIDE EXHAUST CANOPIES OVER ALL IVER COOKING EQUIPMENTIN ACCORDANCE WITH AS1668 PROVIDE MAKE UP AIR FOR ALL EXHAUST CANOPIES AS PER AS 1668
● EXHAUST CANOPY TO BE PROCIDED TWITH SPRINKLER SYSTEM PROTECTION IN ACCORDANCE WITH CLAUSE 5 6 17 OF AS2118 1-1999
● EXHAUST CANOPY INSTALLATION CERTIFI CATE MUST BE SUPPLIED BY THE EXHAUST CONTRACROR AND SHOULD CERTIFY THAT THE INSLTALLATION OF ANY EXHAUST CANOPIES WITHIN YOUR PREMISEDS MEET ALL REGULATORY REQUIREMENTS AND CODES AND IS SAFE FORE ENERGISING AS REQUIRED UNDER LAW
FLOORS
● ALUMINUM COVING SKIRTING TO COMPLY WITH LOCAL HEALTH REGULATIONS IN ALL FOOD PREPARATION ARES
● R10) NON-SLIP FINISHES TO BE PROVIDED TO ALL FOR PREPARARTION AREAS
● SILICONE SEAL TO ALL JOINTS AND WALL JUNCTIONS
● NON-SLIP FINISHED & TACTILE INDICATORS TO BE PROVIDED TO ALL STEPS AND LANDINGS TO COMPLY WITH AS1428 1-2009
● STAIRS TO HAVE NON -SLIP NOSING, HANDRAIL TO COMPLY WITH AS 1428 1-2009
WALLS:
● ALL FOOD PREPARATION AREAS TO BE IN PARTIAL OR FULLY CONCEALED STAINLESS STEEL SHEET WITH IMPERVIOUS FINISH
● ALL FLOOR JUNCTIONS TO BE FLUSH AND INCLUDE A RECESSED METAL EDGE STRIP ANGLE BETWEEN THE FINISHED DETAILS TO BE PROVIDED TO A SEPERATE APPROVAL
CEILING:
● MINIMUM 2400MM CEILING HEIGHT TO ALL NEW PORTION OF CEILING CHECK WITH ARCHITECT TO CONFIRM ON SITE
WATERPROOFING :
●WATERPROOFING OF WET AREA SHALL COMPLY WITH BCA CLAUSE F 1 7 AND AS3740
-WATER RESISTANT TO A HEIGHT OF NOT LESS THAN 150MM ABOVE THE VESSEL,FOR THE EXTENT OF THE VESSEL WHERE THE VESSEL IS WITHIN 75MM OF A WALL
-WATERPROOF WALL JUNCTIONS WHERE A VESSEL IS FIXED TO A WALL -WATERPROOF TAP AND SPOUT PENETRATIONS WHERE THEY OCCUR IN SURFACES REQUIERD TO BE WATERROOF OR WATER RESISTANT
ACCESSIBLE FACILITIES:
● ENSURE ALL FIXTURES AND HANDRAILS TO COMPLY TO AS 1428 1-2009
● ENSURE TOILET SEAT HAS A MINIMUM LUMINANCE CONTRAST OF 30% WITH THE BACKGROUND (E G PAN AND FLOOR) AND PROCIDED WITH BACKREST ETC TO COMPLY WITH AS 1428 1-2009
● BRAILLE AND TACTILE SIGNAGE IS REQUIRED TO ALL TOILETS IN ACCORDANCE WITH NCC SPECIFICATION D 3 6 & AS1428 1-2009 ENSURE SIGNAGE IS LOCATED BETWEEN 1200 -1 600 FROM FFL
● STAFF WORKING IN THE RESTAURANT WILL ALWAYS ACCOMPANY DISABLED PATRONS TO THE DOOR AND OPENS FOR THEM IN LIEU OF AS1428 1-2009
FITTING FIXTURES AND EQUIPMENT:
● CONCEAL ALL SERVICE PIPES IN THE FLOOR WALLS CEILING OR PLINTHS OR BRACKETED OFF THE WALLS 25MM OR MORE
● ALL WALL MOUNTED SHELVES ARE TO BE BRACKETED OFF THE WALLS 25MM OR MORE FROM THE WALL
● ENSURE ALL COOKING EQUIPMENTS ARE EASILY MOVABLE, BUTTED AGAINST WALLS OR OTHER EQUIPMENTS, JOINTS SEALED OR SPACED FROM WALLS AND EQUIPMENT BY 150MM MINIMUM
● FIT WHEELS OR CASTORS TO ALL CHEST FREEZERS UPRIGHT REFRIGERATORS, OR LIFT AND PLACE ON ADEQUATE LEGS TO ENABLE EASY CLEANING BELOW
CLEANING EQUIPMENT AND HEMICAL STORAGE :
● CLEANERS SHELVING FOR THE STORAGE CLEANING CHEMICALS AND CLEAING EQUIPMENT LOCATED AT BACK OF HOUSE
EQUIPMENT
● ALL REFRIGERATORS TO BE CAPABLE OF MAINTAINING FOOD BELOW 5°C
● ALL FREEZERS TO BE CAPABLE OF MAINTAINING FOOD BELOW -15°C
● ALL EQUIPMENT USED FOR STORAGE OF HOT FOOD TO BE CAPABLE OF MAINTAINING FOOD ABOVE 60°C
LIGHTING:
● ALL CEILING OR WALL MOUNTED LIGHT FITTINGS ARE TO BE RECESSED OR FLUSH FIXED AND PROVIDED WITH SHATTERPROOF COVERS
● ALL LIGHT FITTING IN COOL ROOM WITH SHATTER PROOF GUARDS
GLAZING
● ALL NEW GLAZING TO BE INSTALLED IN ACCORDANCE WITH AS 1288-2006
● GLAZIER WHO INSTALLED GLASS MUST SUPPLY CERTIFICATION THAT THE INSTALLATION DESIGN AND MATERIALS MEET THE CURRENT AUSTRALIAN STANDARDS, AS1288 AND AS2208
HYDRAULIC:
● ALL PROPOSED GENERAL TUNDISH , GREASY & SEWER WASTE POINTS TO EXISTING WASTE & GREASY WASTE POINTS VIA PRIMING PIPE WHERE POSSIBLE
FIRE SAFETY:
● PORTABLE FIRE EXTINGUISHER TO COMPLY WITH AS 2444-2001
● 2A 40B(E) DRY CHEMICAL PORTABLE FIRE EXTINGUISHER TO BE LOCATED BETWEEN 2M - 20M FROM ELECTRICAL SWITCHBOARDS
● 2A 40B(E) DRY CHEMICAL PORTABLE FIRE EXTINGUISHER TO BE LOCATED BETWEEN 2M - 20M FROM COOKING OLIS AND FATS
● FIRE BLANKET TO BE LOCATED WITHIN KITCHEN AREA TO EXTINGUISH FIRE INVOLVING ANY COOKING OILS AND FATS
● ALL PENETRATIONS THROUGH FIRE RATED MEMBERS TO BE SEALED USING FIRE COLLARS OR FIRE SEAL AS APPROPRIATE IN ACCORDANCE WITH CLAUSE C 3 15
● ELECTRICAL SWITCHBOARD WILL VE IN A SMOKE PROOF NON -COMBUSTIBLE HOUSING
● ALTERATIONS TO THE SPRINKLER SYSTEM ARE TO BE CARRIED OUT IN ACCORDANCE WITH AS 2118 1 BY A REGISTERED FIRE SERVICE CONTRACTOR
● FIRE EXTINGUISHER CERTIFICATE TO BE OBTAINED FROM A FIRE PROTECTION CONTRACTOR
COOL ROOM & FREEZER:
● (IF APPLICABLE) THE COOL ROOM & FREEZER ROOM TO COMPLY WITH CLAUSE G 1 2, BCA 2019 OF THE BUILDING CODE OF AUSTRALIA A COOL ROOM WHICH IS OF SUFFICIENT SIZE FOR A PERSON TO ENTER MUST HAVE:
A DOOR WHICH IS CAPABLE OF BEING OPENED BY HAND FROM INSIDE WITHOUT A KEY
▪ INTERNAL LIGHTING CONTROLLED ONLY BY A SWITCH WHICH IS LOCATED ADJACENT TO THE ENTRANCE
DOORWAY INSIDE THE COOL ROOM FREEZER ROOM
A DOOR REQUIRED BY (a)( ) IN COOLROOM AND FREEZER ROOM MUST HAVE A DOORWAY WITH A CLEAR WIDTH OF NOT LESS THAN 600MM AND A CLEAR HEIGHT NOT LESS THAN 1500MM
▪ AN INDICATOR LAMP POSITIONED OUTSIDE THE COOL ROOM & FREEZER ROOM WHICH IS ILLUMINATED WHEN THE INTERIOR LIGHTS REQUIRED BY a)(ii) ARE SWITCHED ON
▪ AN ALARM THAT IS
- LOCATED OUTSIDE BUT CONTROLLED ONLY FROM WITHIN THE COOL ROOM & FREEZER ROOM
- ABLE TO ACHIEVE SOUND PRESSURE LEVEL OUTSIDE THE COOL ROOM & FREEZER OF 90dB(A)
WHEN MEASURED 3M FROM THE SOUNDING DEVICE
▪ ALL COOL ROOM AND FREEZER INTERNAL FLOOR TO CEILING HEIGHTS TO BE 2 7M UNLESS OTHERWIDE SPECIFIED ON RCP AND RELEVANT SECTIONS ELEVATIONS
▪ BLOWER UNITS TO BE PLACED DIRECTLY ABOVE THE DOORS TO MAXIMISE SHELVING HEIGHTS ALONG ALL PERIMETER WALLS
▪ MECHANICAL VENTILATION IS TO BE IN ACCORDANCE WITH AS 1668 2
PLEASE REPORT ANY DISCREPANCIES WITH DIMENSIONS OR DETAILS TO THE ARCHITECT DRAFTER
NO SUBSTITUTIONS TO ANY FINISHES ARE TO BE MADE WITHOUT PRIOR APPROVAL FROM ARCHITECT / DESIGNER
ALL SIGNAGE AND GRAPHICS ARTWORK TO BE PROVIDED BY CLIENT S GRAPHIC DESIGNER ALL SIGNAGE AND GRAPHICS FEATURED IN DRAWING SET ARE INDICATIVE ONLY
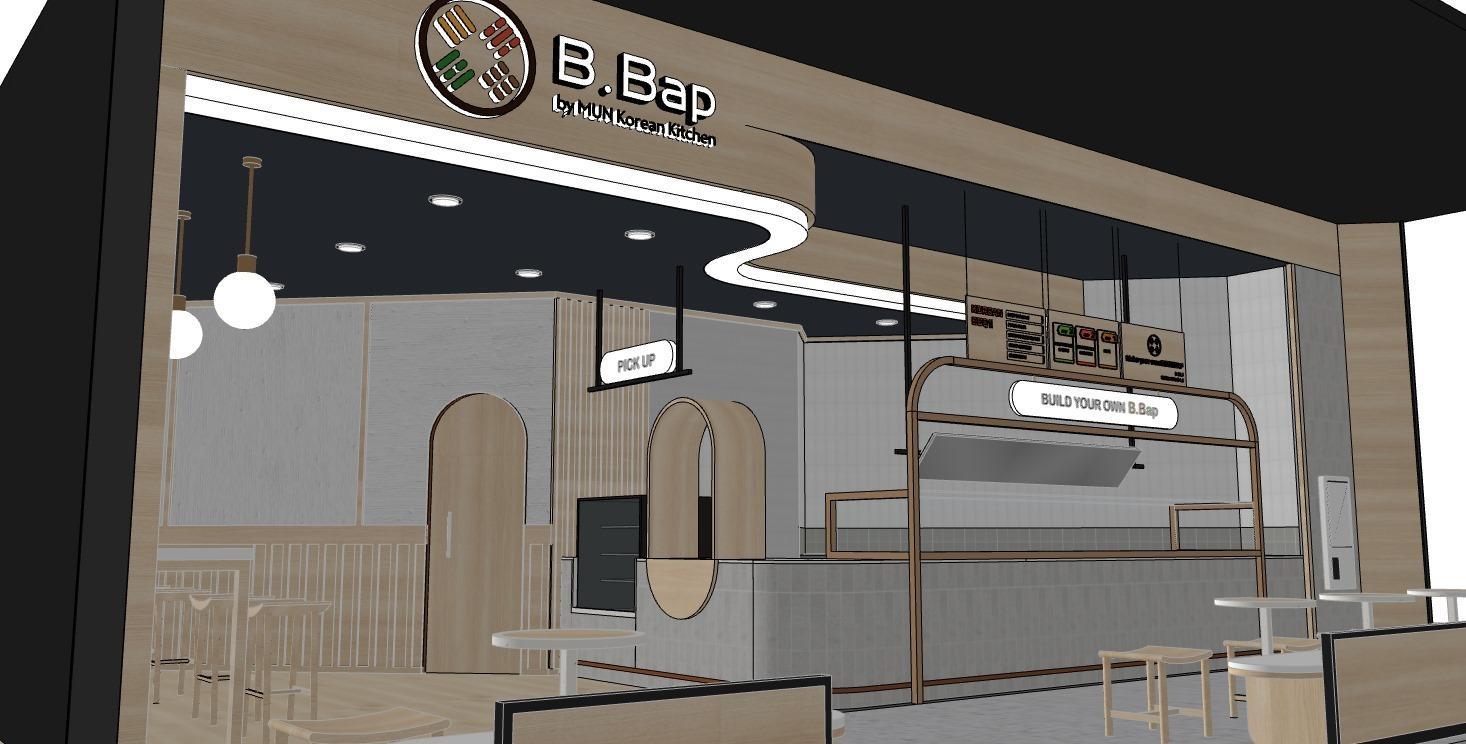
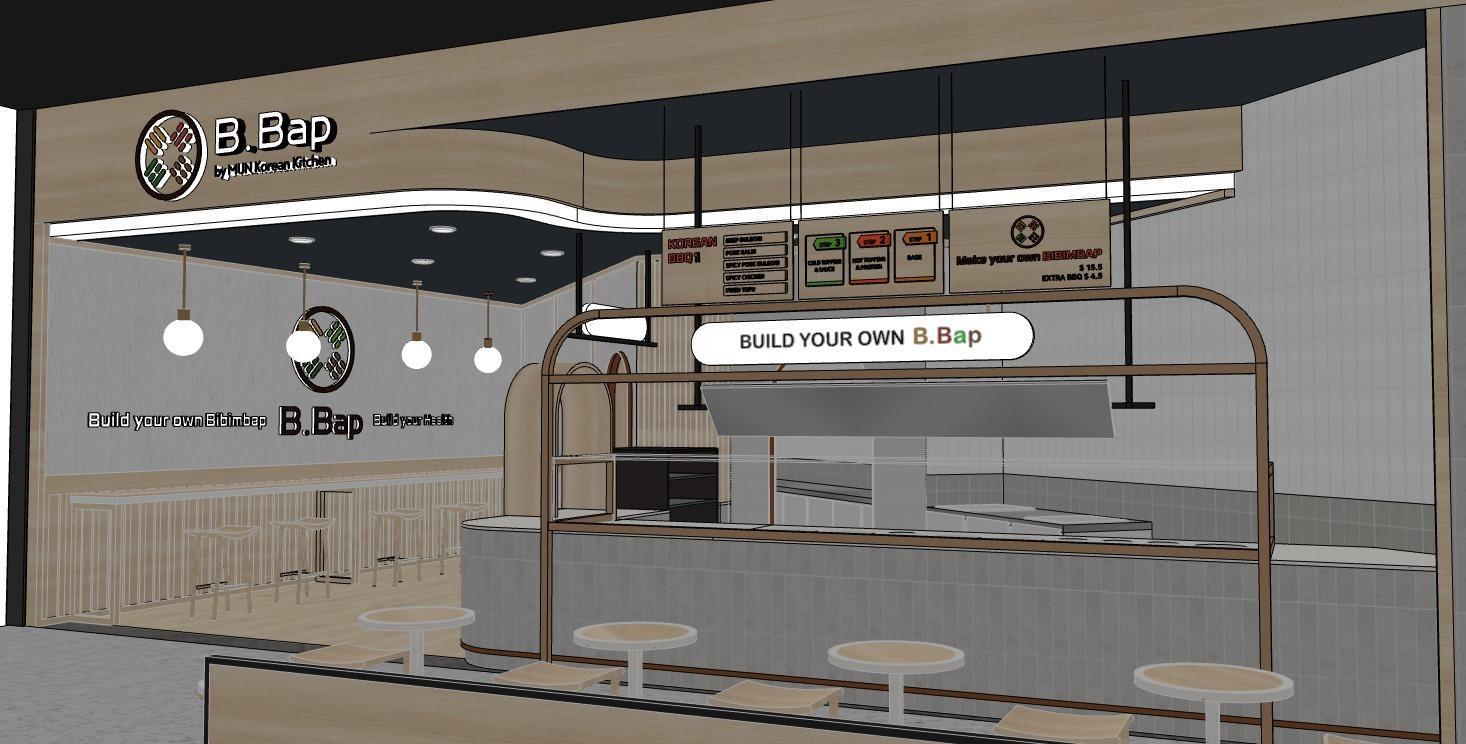
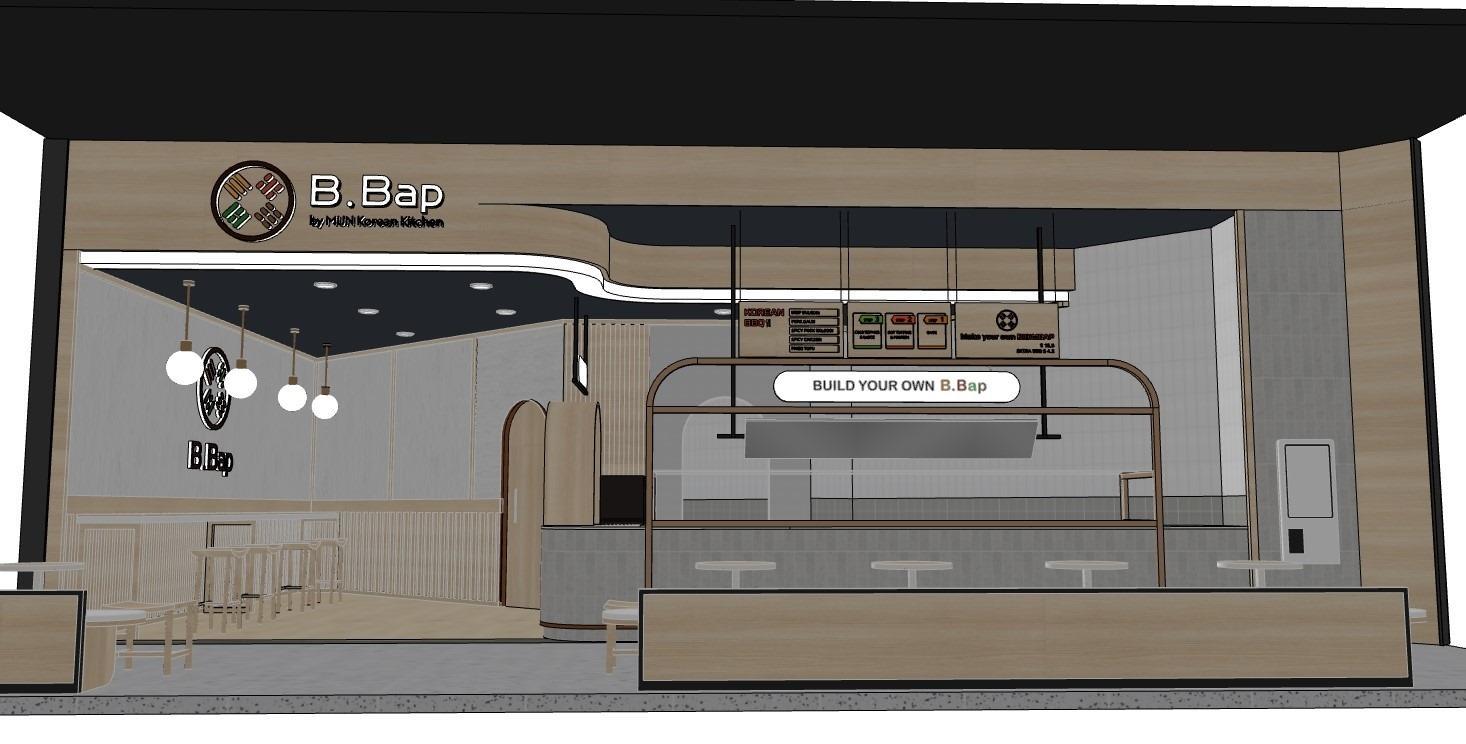