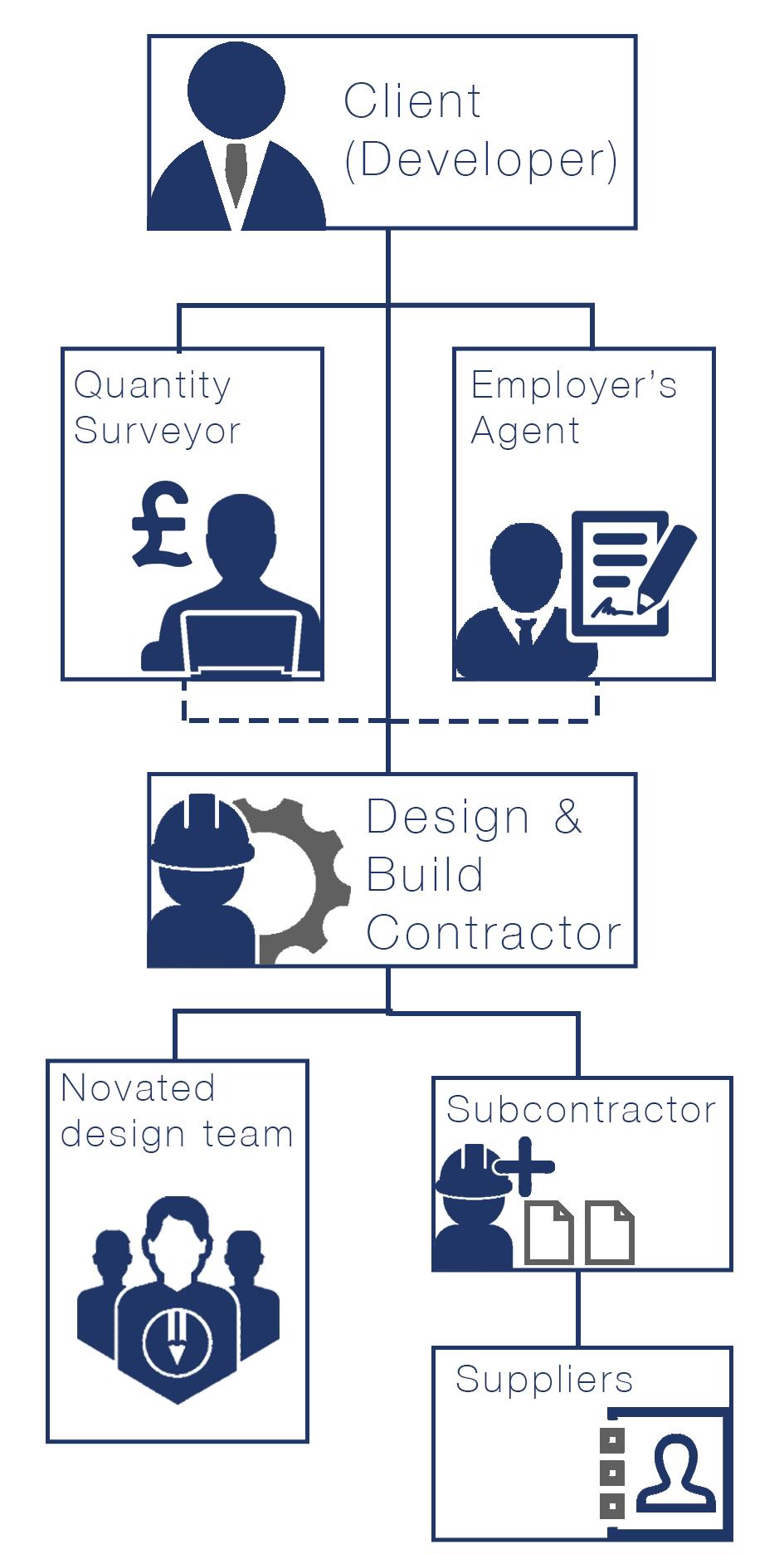
2 minute read
Question 1: Substitution Process
Advise the contractor on the process of changing the Employer’s Requirements in a design & build project.
Employers Requirements, with regards to ‘Design and Build’ procurement (Fig.2), “describes for the contractor the development which the employer wants him to design and build” (Longworth consulting, 2020). This document outlines specifications and details as proposed by the client.
Advertisement
During the formation of this package of information for both client and contractor to review, along with the ‘Value Engineering’ exercise, a change control procedure should be introduced “to ensure that the approved information is not changed without the express permission of the client.” (Designing Buildings, 2020). ‘Value Engineering’ addresses concerns and reduces unnecessary costs whilst improving project efficiency. The process involves:
“
- Identifying the main elements of a product, service or project. - Developing alternative solutions for delivering those functions. - Assessing the alternative solutions. - Allocating costs to the alternative solutions. - Developing in more detail the alternatives with the highest likelihood of success.” (Designing Buildings, 2020) “
Fig.2 Design & Build contractual and functional relationships
It is the job of the employers agent, in house or external, “acting on behalf of the client as the contract administrator for design and build contracts” (Designing Buildings, 2019) to assume the role of a broker between contractor and client, who will then assess the changes. To constitute a change; “there has to be an alteration to the “ requirements set out in the ‘Employer’s
Requirements’ document not simply the work, including any design, undertaken by the contractor” (Chappell and Dunn, 2016, p.420) “ The contractor will therefore have to relay the information from the subcontractor’s QS team to the employer’s agent in order for the client to review the new status (Fig.3). Considering both the window dimensions and the ironmongery finish; the constraints stem from the supplier’s and manufacturer’s capabilities and provisions. This would lead to a mutually agreed review of the ironmongery suppliers, the window manufacturers and the type of window systems.
This would need to be completed before resuming the construction on site so that named suppliers can be verified and new products ordered. Elements to consider are: - Who is requesting the change. “ - The consequences of the change, including health and safety, time, quality, cost (and who will bear the cost). - Proposals for mitigation of any consequences. - The risks associated with the change. - Alternatives to the proposed change. - Time by which the change must be (Designing Buildings, 2020) instructed. “ This ensures that the contractor and the client have been made aware of, approved the changes and understood the risks. If there are any disputes in relation to changes throughout the project timeline, all involved parties can refer to the change control procedure and the signed dates of accepted changes. This could avoid any potential litigation and confusion, resulting in minimal time delays and cost impacts.
Design & Build Contractual/ Functional

Fig.3 Employer agent role in novated Design & Build Procurement