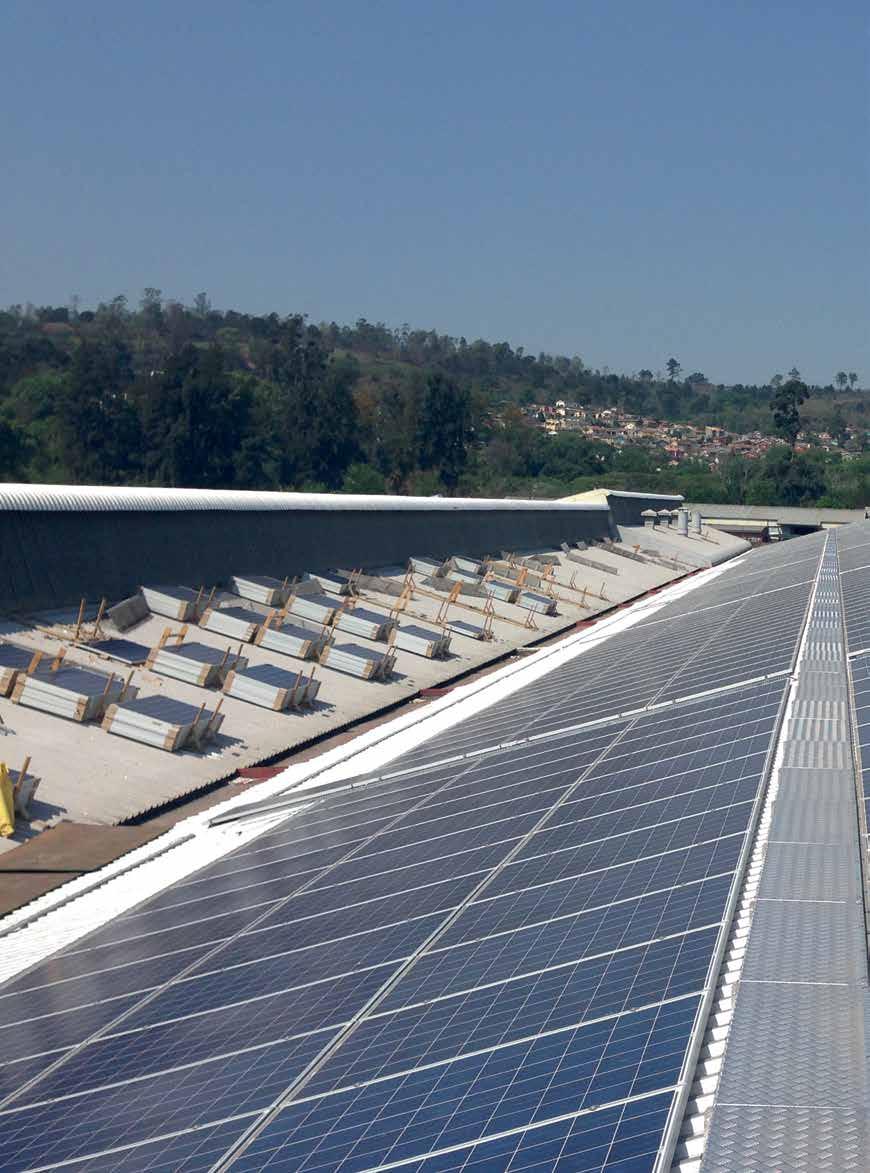
11 minute read
INDUSTRIAL MANUFACTURING GREEN: SUSTAINABILITY IN THE INDUSTRIAL SECTOR We take a look at two light industrial buildings that have recently been awarded green stars
Manufacturing Green: Sustainability in the Industrial Sector
Since the age of the Industrial Revolution, factories have been seen as noisy, dirty, and polluting. Smoke and waste was just an accepted side effect of mass production and mechanised manufacture, and the comfort and health of workers was, historically, barely a consideration. Recently, however, there has been a move to question the status of industrial buildings and their contribution to sustainability. We take a look at two light industrial buildings that have recently been awarded Green Stars.
Advertisement
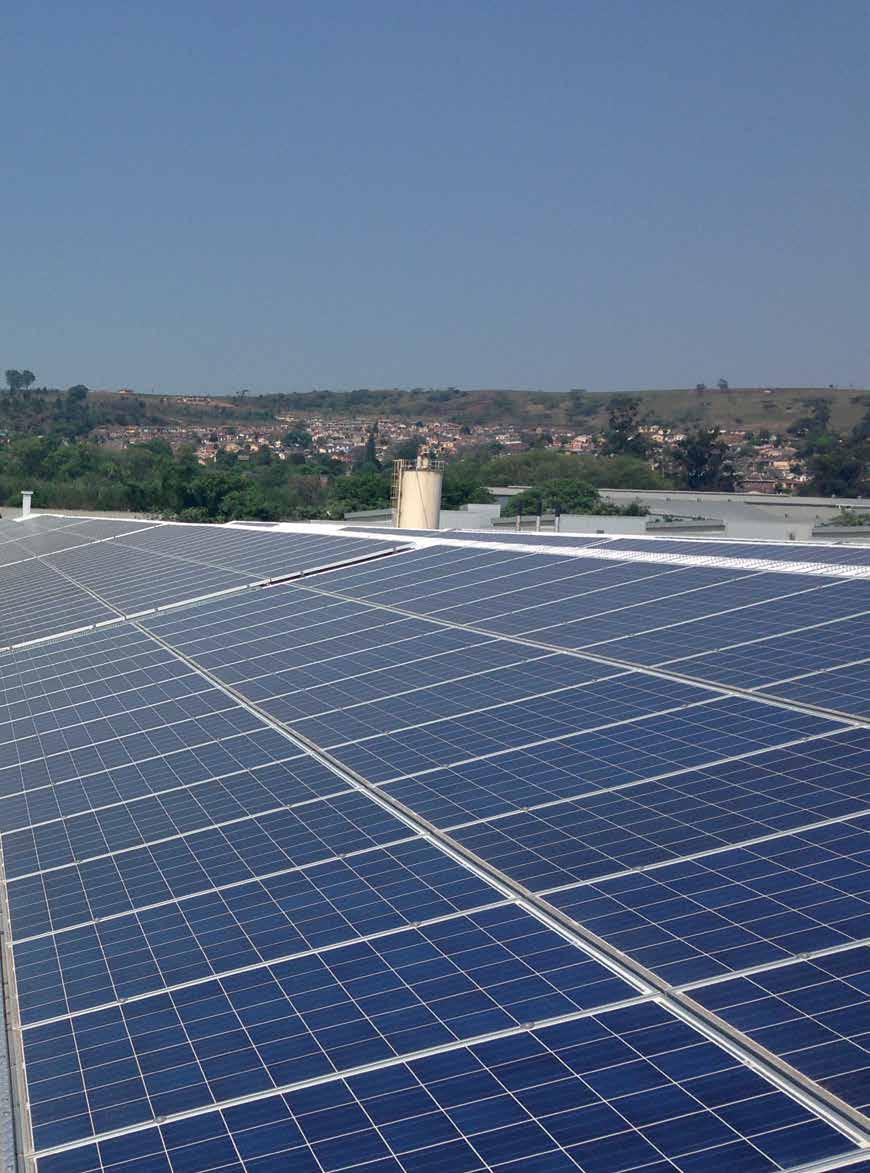
WORDS Melinda Hardisty
European regulations governing work environments and the protection of the natural surroundings are already well advanced. Historically perhaps the conditions weren’t always as healthy, but they certainly prove that industry doesn’t have to be synonymous with pollution and destruction in the modern age. It is encouraging to see local companies rising to the challenge of pursuing more sustainable approaches to manufacturing their products. To that end, the Green Star EBP (Existing Building Performance) tool has been customised to apply to industrial buildings. To date, four South African buildings have successfully achieved Green Star Ratings. The two most recent ratings have been the Equator – The Belt Factory™ in Durban, and Growthpoint’s Serra Building in Germiston, Johannesburg.
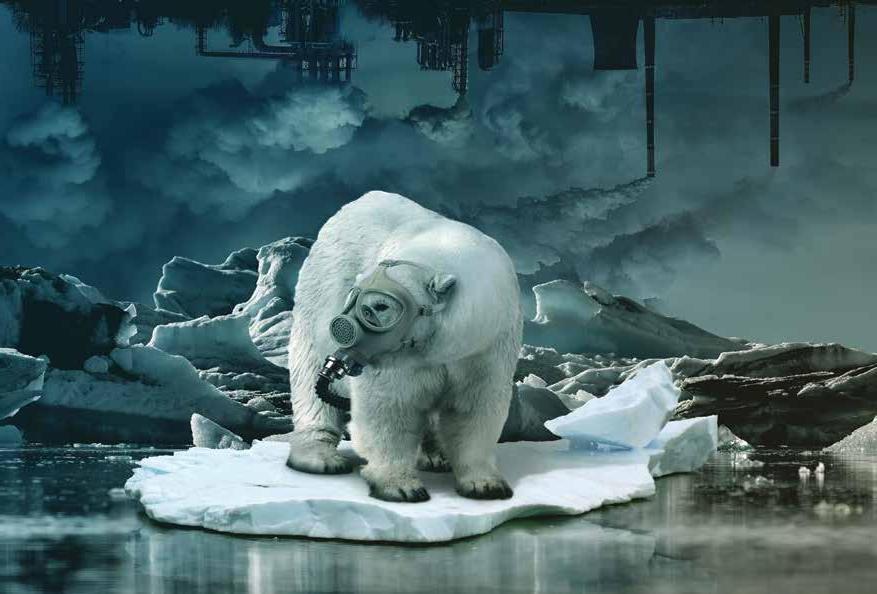
Johan Pretorius
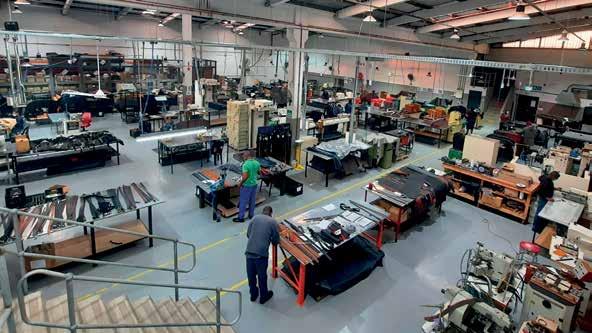
EQUATOR – THE BELT FACTORY™
Project dates:
Completed in June 2018 Green Star rating: 5-Star Green Star Custom Industrial (EBP V1) Location: New Germany, Durban Type of building: Light Industrial (factory, stores, warehouse, offices) Building size: 4 440m² Cost (interventions): R1.3mil
Equator has been manufacturing belts since 2001. By 2009, they were well established in the industry and were authorised to manufacture belts for Levi’s, giving them further credibility. Leon Buhr, founder and director of Equator, explains that the CTFL (Clothing, Textile, Footwear, and Leather) supply chain is one of the least sustainable industries in the world. High consumption of products at low cost leads to economic imbalance and environmental destruction.
Additional glazing and new skylights have been added to allow natural light into the factory space and offices.
Buhr’s passion for sustainability in his business and his life is contagious as he talks about Equator’s sustainability journey. The real impetus for change came when he took a 10-week sabbatical in 2016 to reassess his lifestyle and his business. While making many positive changes in his own life, he also thought about the business he had been building for 15 years and what legacy he would leave. He says: “My daughters (then about 13 and 11) asked me more and more about sustainability and I felt [that] building a business and then not being able to tell your children you did your best to do so in a sustainable (and green) manner would nullify all efforts to lead by example.” He decided that they needed to interrogate every level of the business and manufacturing process and see where they could improve. It could have seemed like an insurmountable problem, but Buhr decided to just take it one bit at a time, fixing small things one by one.
In 2017, the company needed to move to bigger premises and this seemed like the perfect opportunity
Equator - The Belt Factory™ has been transformed in terms of environmental sustainability and human comfort.
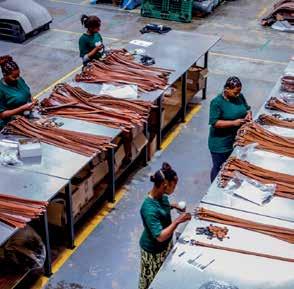
Johan Pretorius
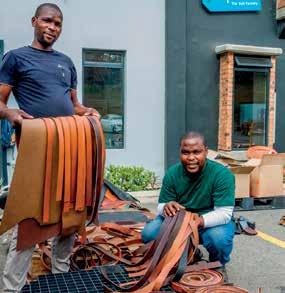
Johan Pretorius
to make drastic changes to their physical space and operations. An old textile mill in New Germany – one of the oldest industrial areas in Durban – was purchased and completely transformed in terms of environmental sustainability and human comfort. These factors were not great priorities in 1967 when the factory was first built.
Buhr says that it was important that their interventions were scientific and measurable, and so they appointed sustainability experts, Andre Harms and Catherine Luyt, of Ecolution Consulting, to manage the Green Star certification on the client’s behalf. With the tag line: “A Place of Craft and a Place of Science”, one wouldn’t expect anything less.
The EBP tool, which has been customised to assess industrial buildings, doesn’t rate the construction or design of a building but rather provides benchmarks to measure the operating performance of a building over time, thus a building needs to be operational for at least a year for its performance to be assessed.
The tool measures performance under eight categories: Management (building management, continuous monitoring, learning resources), Indoor
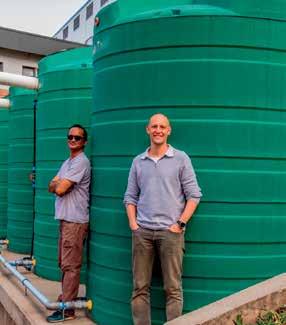
Water tanks storing harvested rainwater for use throughout Equator. Pictured (left) Rajeev Matai (right) and Marc Pozniac.
Johan Pretorius
Environmental Quality (air quality, lighting comfort, thermal comfort, occupant survey, acoustic comfort, daylight views), Energy (energy consumption and peak demands), Water (potable water management), Transport (alternative transportation), Materials (procurement and purchasing, solid waste management), Land Use and Ecology (hardscape, landscape, pest management), and Emissions (refrigerants, legionella prevention, stormwater).
There were no structural or footprint changes made to the existing building, but there was additional (double) glazing and new skylights added to allow natural light into the factory space and offices. A new break room was added for the factory staff that also has plenty of natural light. The office component also gained a new, industrial aesthetic, kitchenette-cumcoffee bar with access to a balcony space. Non-toxic and low VOC paints and finishes were used throughout, and most of the furniture was second hand or up-cycled.
Rainwater harvesting systems were implemented by KZN Water Energy, and low-flow fittings were installed throughout. Treated and purified rainwater is used for washing, drinking, cleaning, and flushing toilets. The interventions are expected to save about 347 600 litres of water a year (when compared to the benchmark of a similar building) and simple payback, at today’s tariffs, is expected within 16 years.
Energy savings were achieved by the use of LEDs and lighting control, high-performance glazing, natural daylighting, hyper-efficient cooling systems, and smart metering, amounting to a combined annual saving of about 285 579kWh (as compared to similar benchmarks). Sarah Robyn Farrell, from transparenCI, who works with Equator on their sustainability communications,
Johan Pretorius
Waste management systems have been implemented that include the reduction, recycling, and composting of manufacturing waste. Pictured (left) Nosipho Zulu, (middle) Thabanie Mngoma and (right) Lungani Manqele.
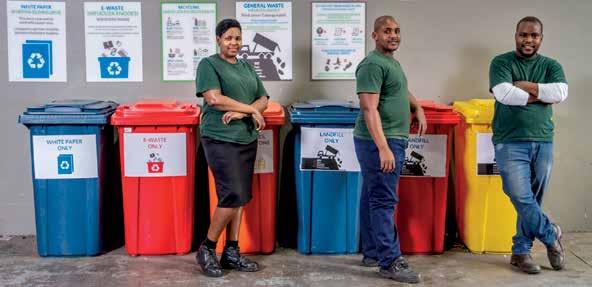
says: “In 2019 the average energy consumed per belt [manufactured] was 0.2 kWh which is the equivalent energy required to make one cup of tea.”
Waste management systems have been implemented that include the reduction, recycling, and composting of waste. Crucial to the successful and sustained implementation of many of these measures is the understanding and buy-in of the staff. Training and vision casting was done at the beginning of the project, and regular refresher discussions are held. The staff was generally enthusiastic and a green committee has been formed. Clear signage, in both English and isiZulu, was installed to clarify and remind people of processes, and the monthly reports on the building performance are shared with all staff so that they understand the impact of the changes they’ve made.
Buhr regards the achievements of the building as only one important step towards sustainability. For the next step, they will be focusing on their materials, responsible sourcing, innovation towards greener raw materials, and improving their packaging and logistics.
BELGOTEX: FORERUNNERS IN INDUSTRIAL GREEN STARS
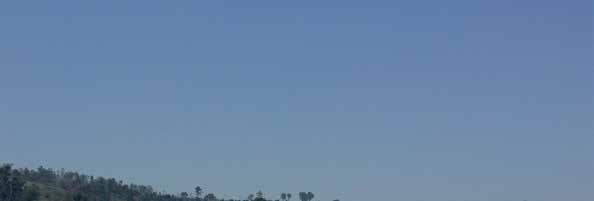
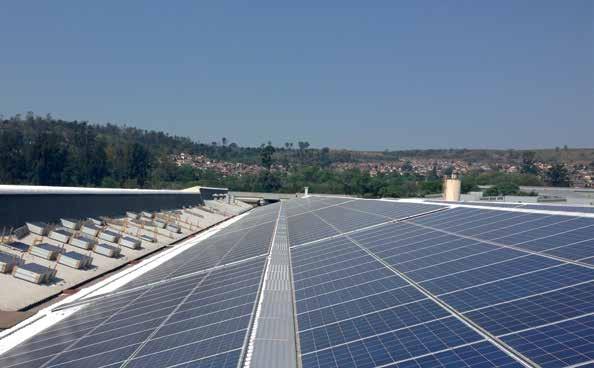
The Belgotex flooring factory in Pietermaritzburg developed the first Custom Industrial EBP Tool. They were awarded a 6-Star rating in 2017. The factory started operations in 1983 and has expanded significantly over the years to produce their current range of carpets and flooring. They have endeavoured to push the boundaries of sustainable manufacturing processes and the production of eco-friendly products since 1991.
The 2017 accreditation recognised the measured operational performance in eight: Management, Indoor Environmental Quality, Energy, Water, Transport, Materials, Land Use & Ecology, and Emissions. Extra credits were awarded for innovative strategies implemented in the manufacturing process.
The company has continued to pursue improved overall sustainability. Energy efficiency is continually being enhanced with new technologies and interventions, both in their operations and their innovative product lines. Their ambition is to invest further in renewable energy, with the groundwork being done over the past two years to obtain a NERSA licence and to reinforce the roofing of a large portion of the factory to support additional solar panels. In 2019, they completed a project linking the factory ablution facilities and cooling towers to a water harvesting dam, further reducing the overall municipal water consumption.
Serra Services
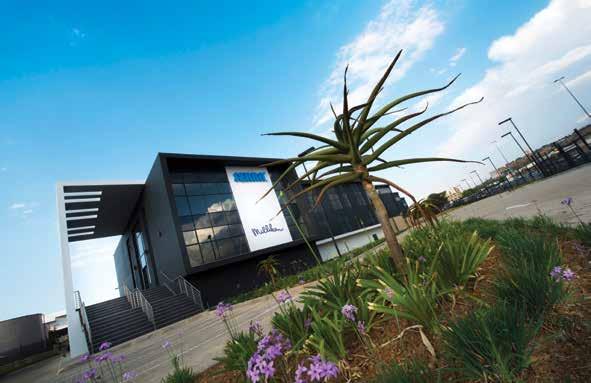
SERRA® PARK, MEADOWBROOK ESTATE
Project dates: March 2019 to February 2020
Green Star rating: 5-Star Green Star Custom Industrial (EBP V1) Location: Meadowbrook, Germiston, Johannesburg Type of building: Light Industrial (manufacturing, offices, warehouse, laundry, showrooms) Building Size: 7 400m²
Serra Park is an example of how industrial buildings are well-suited to being highly efficient. Warehouse roofs are ideally suited for solar panels, efficient lighting and daylighting.
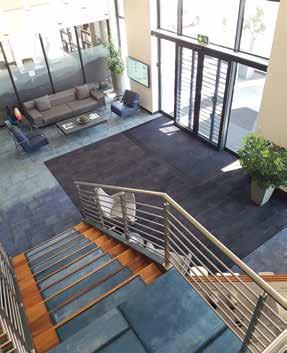
Serra Services

Meanwhile, in Johannesburg, the Serra® Services building owned by Growthpoint Properties has become the first building in Gauteng to have been awarded a 5-Star Green Star rating using the Custom Industrial EBP tool. The success of this project depended on the shared vision and goals of both landlord and tenant. Grahame Cruickshanks, head of sustainability and utilities at Growthpoint, explains that the company’s strategy seeks to create value through sustainability. “All our new office developments should achieve a minimum 4-Star Green Star rating. As part of our dedication to reducing carbon emissions, Growthpoint made a commitment in line with COP-21 to have all
Serra Services
its long-held commercial buildings attain a minimum 4-Star Green Star rating by 2020 year-end and we are progressing well against this target.”
Serra® has been manufacturing and servicing washroom fittings and dispensers for 35 years. Paul Thomaz, group marketing director, says that as a leading hygiene service provider and washroom dispenser manufacturer, “Serra® is duty-bound to highlight health and sustainable environmental practices”. Many years ago, the decision was made to manufacture their products in stainless steel for several reasons, including the material’s sustainability, durability, and low environmental footprint.
Serra Services
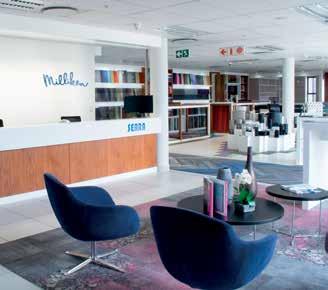
Because the EBP rating grades building and operational performance rather than structure, achieving the targets is largely dependent on the tenant and how they operate in the space. Solid Green Consulting, in collaboration with Sow and Reap, and Imbue Projects, was appointed to advise on the sustainability aspects of the project and to develop a green building guide for the ongoing operation and maintenance of the building.
Francois Retief of Sow and Reap, reiterates the particular importance of the tenant’s buy-in in an industrial building as opposed to offices, where the landlord may have more control over maintenance and cleaning aspects. He also says that industrial buildings are well-suited to being highly efficient. Warehouse roofs are ideally suited for solar panels, efficient lighting and daylighting is often easier to achieve, and intensive water use in processes (like in Serra’s laundry) can make use of non-potable water. 130 photovoltaic panels, with a capacity of 25kWp, were installed on the roof. A further 110 panels are planned for phase 2, and the end goal of 550 panels in total. Three lithium-ion battery banks can provide the offices with 24 hours of uninterrupted power. Andy McKay, director of Greenwave, installed the gridtied solar system and the hybrid battery back-up. He explains that the system can sustain critical equipment during power outages, but also lowers the consumption during peak tariff periods in winter months. This not only saves money but lowers the building’s carbon footprint as well. Errol Taylor, Growthpoint’s head
The EBP rating grades building and operational performance rather than structure, so achieving the targets is largely dependent on the tenant and how they operate in the space.
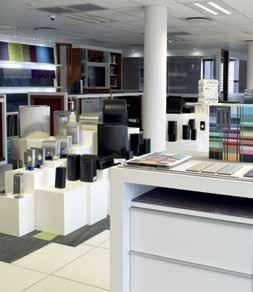
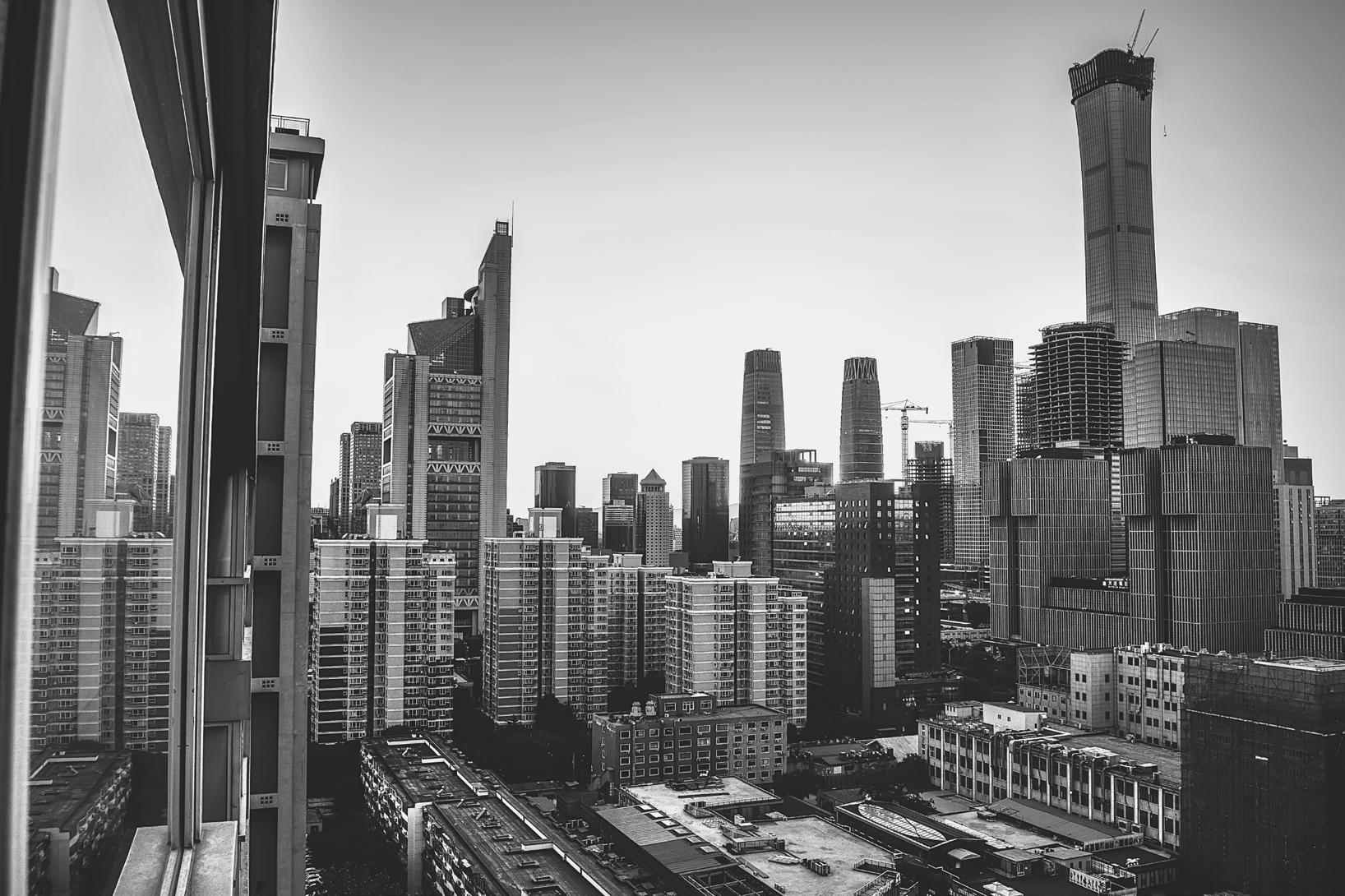
of asset management: Industrial, says that Serra® consumes around 16kWh/sqm/year, as opposed to the benchmark comparison of 106kWh/sqm/year, and the performance is still improving.
Water-saving implementations, and the use of nonpotable water where possible, has enabled the facility to achieve an 88% improvement on similar sized light industrial complexes.
Greenwave also designed, installed, and monitors the Building Management System (BMS) that tracks and controls all the key equipment. This state-of-the-art system is what allows the performance of all the services to be monitored and adjusted as necessary. This, along with regular occupant surveys and other assessments, allows Growthpoint and Serra® to continuously assess the building’s performance and push for further improvements wherever possible.
The teams involved in both of these projects highlight the importance of the education and buyin of the building’s occupants as an important factor in sustained building performance. The key advice for any business looking to embark on their sustainable journey seems to be: Just start!
In the words of Equator’s Leon Buhr: “More and more we realise there is no alternative path for any of us than to make more sustainable decisions each day; in business and personally. That sustainability is not a solar panel here or a Jojo tank there. It is especially not a ‘marketing extra’. It must become deeply embedded in the very foundation of what we think, say, and do.”